Laser Pas de Deux, Lifts EV Motor Welding Next Level
Combining sealed CO₂ and UV solid-state lasers enables cost-effective hairpin stripping and cleaning with the high quality required for volume EV motor production.
February 12, 2025 by Coherent
EV manufacturers are under increasing pressure to optimize operations and cut costs while improving quality. These efforts are crucial for the necessary expansion in EV market share, especially in the volume markets where there is significant total cost of ownership (TCO) sensitivity, and ICE vehicles are still prevalent.
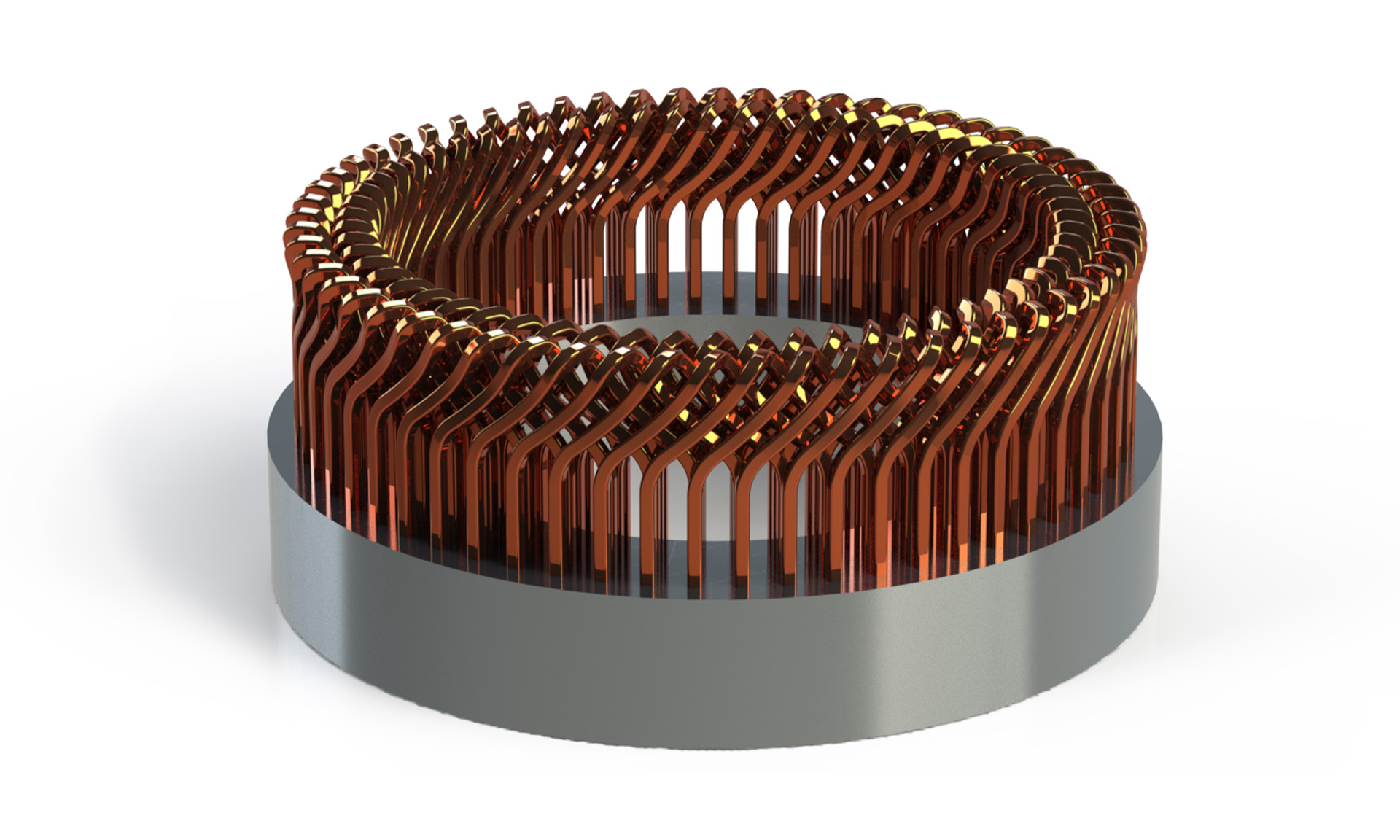
Example of welded hairpins.
For EV engine or motor production, one opportunity lies in optimizing hairpin welding – a process that is critical to motor reliability and performance. Traditional mechanical stripping methods often fall short, leading to process inefficiencies like surface damage, tool wear, and production delays that drive up costs and affect process relaibility.
Laser stripping and cleaning offers a transformative alternative which can overcome the limitations of mechanical stripping while delivering superior results at a lower overall cost. Here we’ll describe an innovative two-step process from Coherent which utilizes CO₂ in combination with UV lasers to produce pristine, weld-ready hairpins. The data presented here demonstrates that this approach offers EV manufacturers a cost-effective way to achieve superior quality welds.
The Hairpin Hurdle
The windings in EV motors are typically formed from individual copper wires. These are bent into a “U” shape (hence the name “hairpin”) and then placed into an assembly. Next, the ends of each adjacent hairpin are welded to their neighbor to electrically connect them and yield a single, continuous winding. Moreover, some alternate designs use a continuous flat wire formed into a wave-like pattern (known as wave winding or S-winding) which is then inserted into the stator slots before being welded.
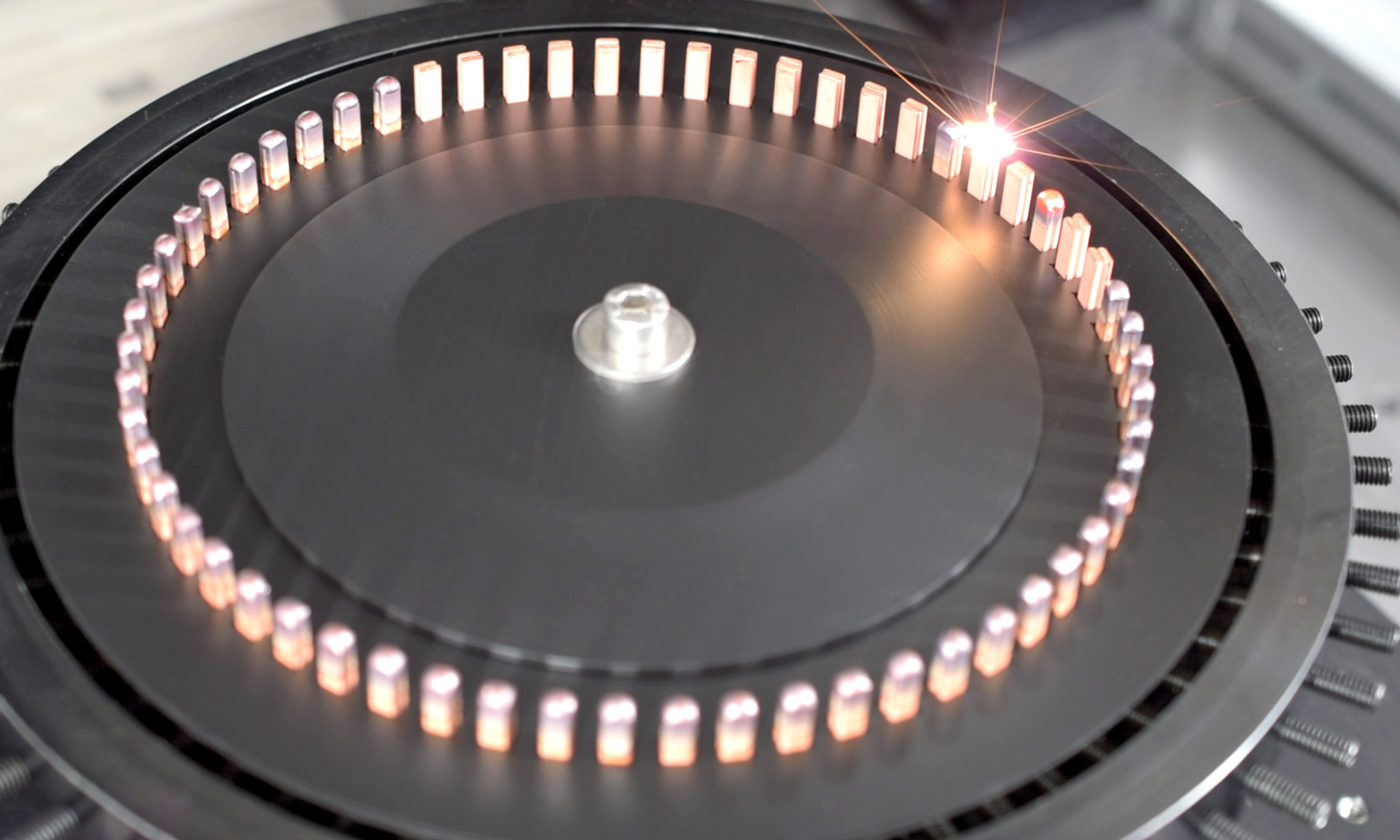
Example of hairpin pairs being laser welded with an ARM fiber laser HIGHmotion 2D scanner from Coherent.
The winding is insulated in all electric motors. In hairpin motors, the insulation needs to be thicker and more robust to accommodate their compact design and the high-voltage requirements typical of electric vehicles.
A small amount of this insulation must be removed from both ends of each hairpin prior to welding. This is critical to ensuring high-quality electrical and mechanical connections.
Traditionally, this task has been primarily performed using mechanical methods, a single step laser process with an IR (1um) pulse lasers has also been used. Mechanical stripping involves using a cutting tool in direct contact with the wire surface to scrape away insulation. While these approaches have been standard for years, it presents significant challenges in the fast-paced world of electric vehicle (EV) production.
For example, the physical contact required for mechanical stripping removes a layer of the copper from the pin leaving a texture surfaces causing gaps and part fit up issues between pins, compromising the integrity and consistency of the welds. Additionally, mechanical tools experience wear leading to process inconsistency, frequent maintenance, unplanned downtime, and potential production interruptions. These issues are compounded by the slower speed of the process, which struggles to keep up with the high-volume demands of EV manufacturing.
2 Step Laser Stripping is a Cut Above
Lasers are used for material removal in a wide range of applications, including insulation stripping. In this context, the benefits of laser processing include:
- Better weld quality: Total insulation removal without any damage to the copper wire ensures a pristine surface for optimum weld quality.
- Reduced maintenance and equipment downtime: The absence of tool wear and the elimination of any possibility of machine jamming provides an uninterrupted production flow.
- Increased throughput: Continuous stripping while the wire is being fed improves production efficiency.
- Enhanced consistency: Without wear or contact, the laser process is stable and reproducible.
It’s easy to see that laser processing can offer process improvements. But the real question is “which is the best laser?” In other words, out of the numerous possible laser sources and implementations that could perform this process, which one provides the best balance of quality, speed, vs cost for high-volume EV motor production applications?
Optimizing the Laser Process
As a leading provider of nearly every type of industrial laser, Coherent is uniquely positioned to objectively investigate this application without any inherent preference for one technology.
In fact, we didn’t find one best laser for hairpin stripping. Instead, our applications engineers developed a two-laser process for achieving optimized coating removal. This approach delivers today to our customers the best pre-weld surface quality in the most cost-effective manner. The primary motivation to investigate the two-laser process was to overcome the issues of single-step laser stripping process.
Single step laser processing is a compromise between the absorption of the coating and underlying copper. The near-1 µm IR wavelength of the fiber laser is not readily absorbed by the coating resulting in heating at the interface and flaking off of the coating into airborne particles. The particles can interfere with the incoming laser beam affecting the cleanliness of the pin and can get trapped in the system resulting in frequent stoppages to clean the equipment. In addition, the penetrated IR beam of the fibre laser will not be able to fully remove the polymer residue from the copper surface. It may melt the surface of the copper wire and expose it the constituents of the insulator polymer such as hydrogen and carbon. This can contaminate the surface, affecting the subsequent weld quality.
The Coherent two-step laser-based hairpin preparation process involves:
- Bulk stripping: The majority of the insulation is rapidly removed using a mid-power CO₂ laser. This type of laser is ideal for high-throughput non-metallic material removal.
- Final Cleaning: A pulsed, low-power, nanosecond, UV solid-state laser is then used to remove any insulation residue. This provides a pristine surface for welding. The short wavelength of UV solid-state lasers excels at high precision materials processing and are particularly effective at removing a wide range of materials including polymers, other organic materials and copper.
For the bulk stripping step, the Coherent J-5-10.6 µm laser proves to be an ideal source. While there are a number of different materials used for hairpin insulation (including polyimide, polyetherimide, polyester, polyesterimide, polyamide, polyether ether ketone, epoxy resins, and various fluoropolymers), all of them strongly absorb the 10.6 µm output wavelength of this laser. And, for all these materials, the absorption is higher at 10.6 µm than at other available CO₂ laser wavelengths we offer, like 9.4 µm and 10.2 µm.
The Coherent J-5-10.6 µm also has desirable practical characteristics. It is a fully sealed, pulsed CO₂ laser that produces an average power of over 400 W meaning it can perform high-throughput stripping. Also, it is a self-contained and compact package that is ideal for integration into automated equipment.
For the final cleaning step, the Avia LX 355-30-60 HE demonstrates just the right combination of output parameters. This is a frequency tripled, diode-pumped, solid-state laser that outputs 30 W of average power at 355 nm. Most importantly, it supports operation at repetition rates of up to 300 kHz, and pulse energies as high as 500 µJ. This enables high-precision ablation at the speed required for this application.
The Avia LX 355-30-60 HE is also designed for easy integration. And the incorporation of Coherent PureUV™ active laser-cleaning engine delivers exceptional lifetime and maintenance-free operation.
Weld Results
The applications lab investigated a number of different processes before arriving at the two-step combination just described. Various lasers, including CO₂, nanosecond pulsed IR fiber lasers, and nanosecond UV lasers were examined singly and in combination. The results of processing insulated hairpins were analyzed in detail and once the most promising sources were identified, the specific process parameters were optimized.
As part of the testing, X-ray photo-electron spectroscopy (XPS) was used to analyze the surface chemistry in order to characterize and quantify contaminants. This is where we discovered that the two-step laser stripping process (CO₂ combined with the UV laser) was the most effective means to remove all residual elements from the copper surface prior to laser welding.

This series of photos compares various removal techniques using CO₂, ns IR fiber (FL), and ns UV solid-state lasers. In the top row of photos, the insulation was polyamide (PA) and in the bottom row the insulation material was polyether ether ketone (PEEK). Even a purely visual examination shows that the CO₂ + UV laser combination appears best in both cases. This was confirmed by actual welding trials.
Of course, the most important metric is the quality of welds obtained after the coating removal process. The next graphic shows a series of X-ray images of welded hairpins. This reveals that the two-step (CO₂ + UV laser) process ultimately yields a superior weld. The two-step CO₂ + UV laser stripping minimizes the weld porosity by eliminating the polymer residue on the surface prior to welding. Polymer residues are known to contain hydrogen, carbon and other organic elements that can enter the molten metal pool in the liquid state then, form porosities during the weld solidification process. Porosities affect the mechanical and electrical performance of the weld.
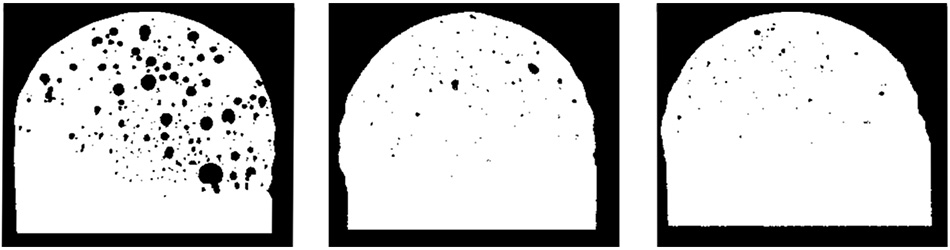
X-ray images of weld beads using the three removal strategies. The CO₂ + UV solid-state laser clearly shows the highest weld quality (lowest porosity content).
Practical Implementation
Coherent stands ready to assist OEMs in implementing this process at whatever level of integration is required. We can provide anything from just laser sources through a complete plug-and-play sub-system that is ready for line integration.
Just as important, Coherent can support in process development. This assistance can be very useful in accelerating the timeline for bringing the process into full production.
Learn more about Coherent CO₂ and nanosecond solid-state lasers.