Laser Pas de Deux,提升电动汽车电机焊接水平
结合密封 CO2 和紫外固态激光器,可实现经济高效的发夹剥离和清洁,以及批量电动汽车电机生产所需的高质量。
2025 年 2 月 12 日,Coherent高意
电动汽车制造商面临着越来越大的压力,要求优化运营并降低成本,同时提高质量。这些努力对于电动汽车市场份额的必要扩大至关重要,特别是在总拥有成本 (TCO) 灵敏度很高且 ICE 汽车仍然普遍存在的数量市场中。
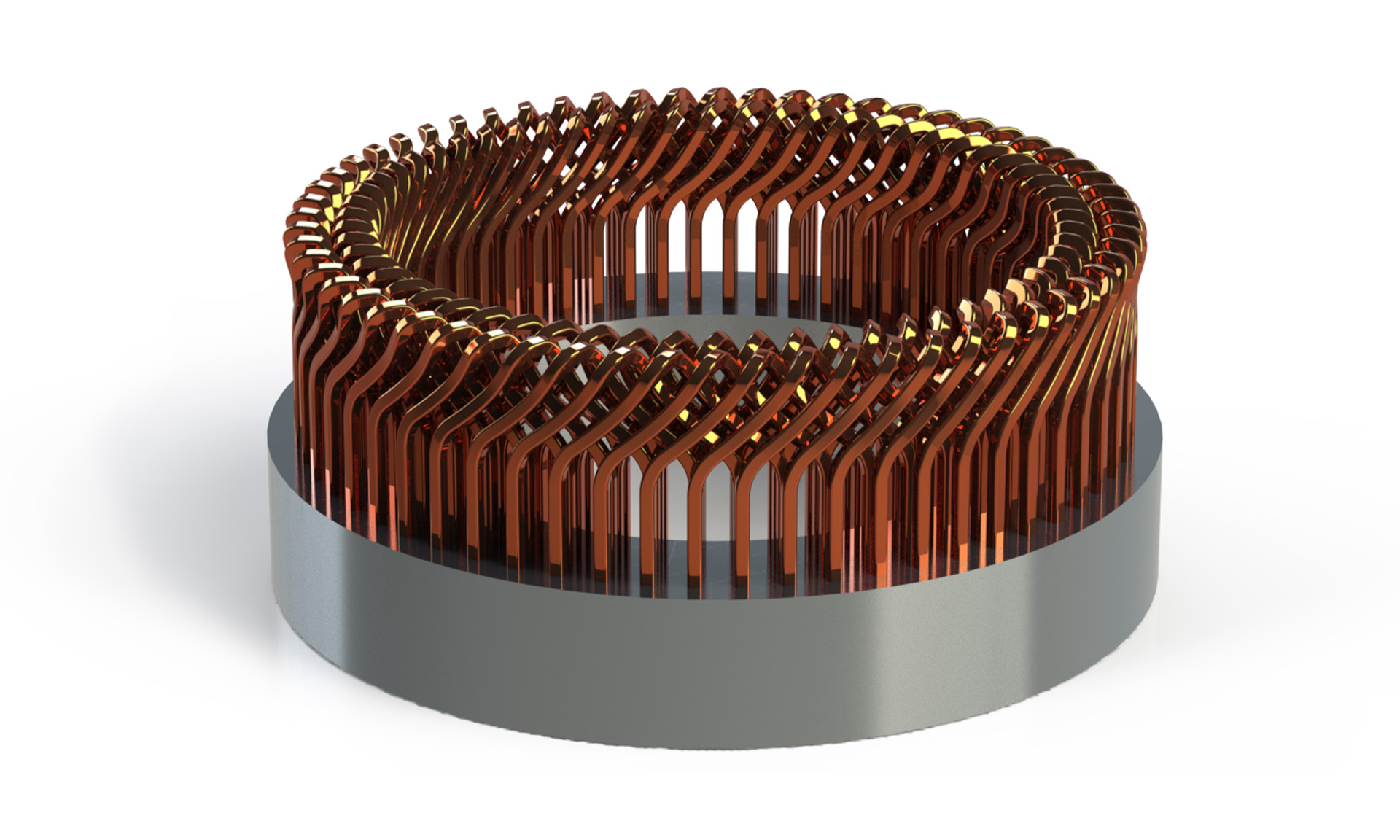
焊接发夹示例。
对于电动汽车发动机或电机生产来说,一个机会在于优化发夹焊接,这一过程对电机的可靠性和性能至关重要。传统的机械剥离方法往往不足,导致表面损坏、工具磨损和生产延迟等工艺效率低下,从而降低成本并影响工艺的可重复性。
激光剥离和清洁提供了一种变革性的替代方案,可以克服机械剥离的局限性,同时以更低的总成本提供卓越的结果。在这里,我们将介绍 Coherent 高意的创新两步工艺,该工艺利用 CO2 与紫外激光器相结合来生产原始的焊接就绪发夹。此处提供的数据表明,这种方法为电动汽车制造商提供了一种经济高效的方法来实现高质量的焊接。
发夹障碍
电动汽车电机中的绕组通常由单独的铜线形成。它们弯曲成“U”形(因此称为“发夹”),然后放入组件中。接下来,将每个相邻发夹的末端焊接到邻居处,以将其电连接并产生单个连续绕组。此外,一些替代设计使用形成波状图案(称为波绕组或 S 绕组)的连续扁平线,然后在焊接之前插入定子槽中。
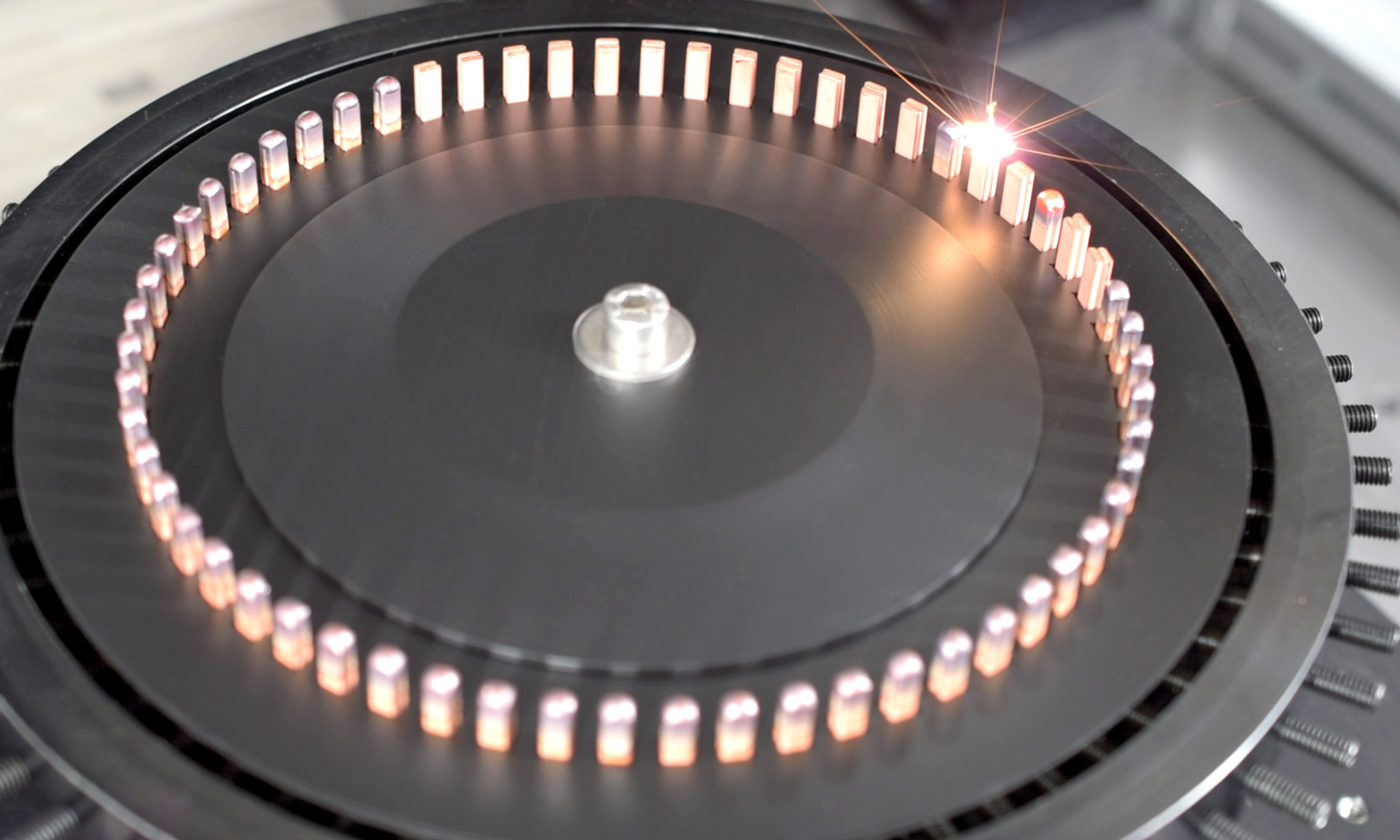
使用相干公司的 ARM 光纤激光器 HIGHmotion 2D 扫描仪激光器焊接的发夹对示例。
绕组在所有电动机中均绝缘。在发夹电机中,绝缘材料需要更厚、更坚固,以适应其紧凑设计和电动汽车典型的高压要求。
在焊接之前,必须从每个发夹的两端去除少量绝缘材料。这对于确保高质量的电气和机械连接至关重要。
传统上,这项任务主要使用机械方法执行,还使用了采用红外 (1um) 脉冲激光器的单步激光工艺。机械剥离涉及使用与线表面直接接触的切割工具来刮掉绝缘层。虽然这些方法多年来一直是标准方法,但它在电动汽车 (EV) 生产的快节奏世界中带来了重大挑战。
例如,机械剥离所需的物理接触会从引脚上去除一层铜,留下纹理表面,导致引脚之间的间隙和零件配合问题,从而损害焊接的完整性和一致性。此外,机械工具的磨损会导致工艺不一致、频繁维护、计划外停机和潜在的生产中断。由于工艺速度较慢,这些问题变得更加复杂,这很难跟上电动汽车制造的大批量需求。
2 步激光剥离在上方切割
激光器用于各种应用中的材料去除,包括绝缘剥离。在这种情况下,激光器加工的好处包括:
- 更好的焊接质量: 完全去除绝缘层而不会损坏铜线,确保了原始表面,以实现最佳的焊接质量。
- 减少维护和设备停机时间: 没有工具磨损和消除机器卡塞的可能性,可实现不间断的生产流程。
- 提高产量: 送丝时连续剥离可提高生产效率。
- 增强一致性: 在没有磨损或接触的情况下,激光器工艺稳定且可重现。
很容易看出,激光器加工可以提供工艺改进。但真正的问题是“哪一种是最好的激光器?”换句话说,在可以执行此过程的众多可能的激光器源和实施中,哪一种能为大批量电动汽车电机生产应用提供质量、速度与成本的最佳平衡?
优化激光工艺
作为几乎所有类型工业激光器的领先提供商,相干公司拥有独特的优势,能够客观地研究这一应用,而无需对一种技术的任何固有偏好。
事实上,我们没有找到用于发夹剥离的最佳激光器。相反,我们的应用工程师开发了双激光器工艺,以实现优化的涂层去除。这种方法如今以最具成本效益的方式为我们的客户提供最佳的焊接前表面质量。研究双激光器工艺的主要动机是克服单步激光器剥离工艺的问题。
单步激光器加工是涂层吸收和底层铜之间的折衷。光纤激光器的近 1 μm 红外波长不容易被涂层吸收,从而导致界面加热,并将涂层剥落成空气颗粒。颗粒可能会干扰进入的激光束,影响引脚的清洁度,并可能卡在系统中,导致频繁停机以清洁设备。 此外,光纤激光器的穿透红外光束将无法完全去除铜表面的聚合物残留物。它可以熔化铜线的表面,并暴露绝缘体聚合物的成分,例如氢和碳。这可能会污染表面,影响后续焊接质量。
Coherent 高意基于激光器的两步发夹制备工艺涉及:
- 散装剥离: 大多数绝缘材料使用中功率 CO2 激光器快速去除。这种类型的激光器非常适合高通量非金属材料去除。
- 最终清洁: 然后使用脉冲、低功耗、纳秒、紫外固态激光器去除任何绝缘残留物。这为焊接提供了原始表面。UV 固态激光器的短波长在高精确材料加工方面表现优异,在去除聚合物、其他有机材料和铜等各种材料方面尤其有效。
对于批量剥离步骤,Coherent J-5-10.6 μm 激光器被证明是理想的光源。虽然用于发夹绝缘的材料有很多(包括聚酰亚胺、聚醚酰亚胺、聚酯、聚酯酰亚胺、聚酰胺、聚醚醚酮、环氧树脂和各种含氟聚合物),但所有这些材料都强烈吸收该激光器的 10.6 μm 输出波长。而且,对于所有这些材料,10.6 μm 时的吸收率高于我们提供的其他可用 CO2 激光器波长,例如 9.4 μm 和 10.2 μm。
Coherent J-5-10.6 μm 还具有理想的实用特性。它是一种完全密封的脉冲 CO2 激光器,平均功率超过 400 W,这意味着它可以执行高通量剥离。此外,它是一个独立紧凑的封装,非常适合集成到自动化设备中。
在最后的清洁步骤中,Avia LX 355-30-60 HE 展示了输出参数的正确组合。这是一种频率三倍、半导体泵浦固态激光器,在 355 nm 波长下输出 30 W 的平均功率。最重要的是,它支持高达 300 kHz 的重复频率和高达 500 μJ 的脉冲能量。这使得能够以这种应用所需的速度进行高精确烧蚀。
Avia LX 355-30-60 HE 还设计用于轻松集成。相干公司 PureUV高意主动激光器清洁引擎的加入提供了卓越的使用寿命和免维护操作。
焊接结果
应用实验室在得出刚才描述的两步组合之前,研究了许多不同的工艺。对包括 CO2、纳秒脉冲红外光纤激光器和纳秒紫外激光器在内的各种激光器进行了单独和组合检测。对处理绝缘发夹的结果进行了详细分析,一旦确定了最有希望的来源,就对特定的工艺参数进行了优化。
作为测试的一部分,使用 X 射线光电子光谱 (XPS) 分析表面化学,以表征和量化污染物。在这里,我们发现两步激光器剥离工艺(CO2 与紫外激光器相结合)是在激光器焊接之前从铜表面去除所有残余元素的最有效方法。

该系列照片比较了使用 CO2、ns IR 光纤 (FL) 和 ns UV 固态激光器的各种去除技术。在照片的顶行中,绝缘材料是聚酰胺 (PA),而在底行中,绝缘材料是聚醚醚酮 (PEEK)。即使是纯粹的目视检查,也表明 CO2 + UV 激光器组合在这两种情况下都表现最佳。这得到了实际焊接试验的证实。
当然,最重要的指标是在涂层去除工艺后获得的焊接质量。下图显示了焊接发夹的一系列 X 射线图像。这表明,两步(CO2 + UV 激光器)工艺最终会产生卓越的焊接效果。两步 CO2 + UV 激光器剥离通过在焊接之前消除表面上的聚合物残留物,最大限度地减少了焊接孔隙率。聚合物残留物已知含有氢、碳和其他有机元素,这些元素可以在液态进入熔融金属池,然后在焊接凝固过程中形成孔隙。孔隙率会影响焊接的机械和电气性能。
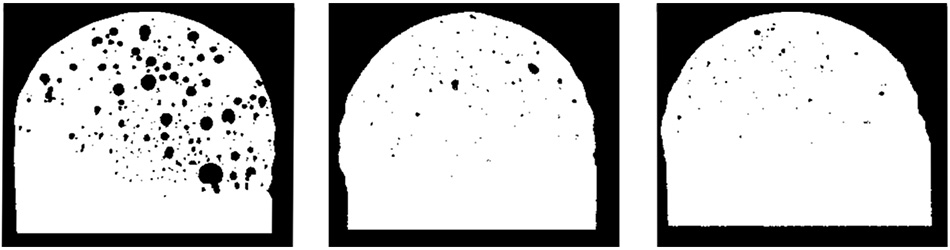
使用三种去除策略的焊缝 X 射线图像。CO2 + UV 固态激光器清楚地显示了最高的焊接质量(孔隙率含量最低)。