2種類のレーザで、EVモーター溶接を次のレベルに引き上げる
シールドCO₂レーザとUV固体レーザを組み合わせることにより、費用対効果の高いヘアピンのストリッピングとクリーニングを、EVモーターの量産に求められる高い品質で行うことができます。
2025年2月12日 Coherent
EV(電気自動車)メーカーは、品質を向上させつつ、業務を最適化してコストを削減する必要にますます迫られています。そうした取り組みは、特に総所有コスト(TCO)に対する感度が高く、ICE車が依然として普及している量販市場において、EVの市場シェアを拡大するために不可欠です。
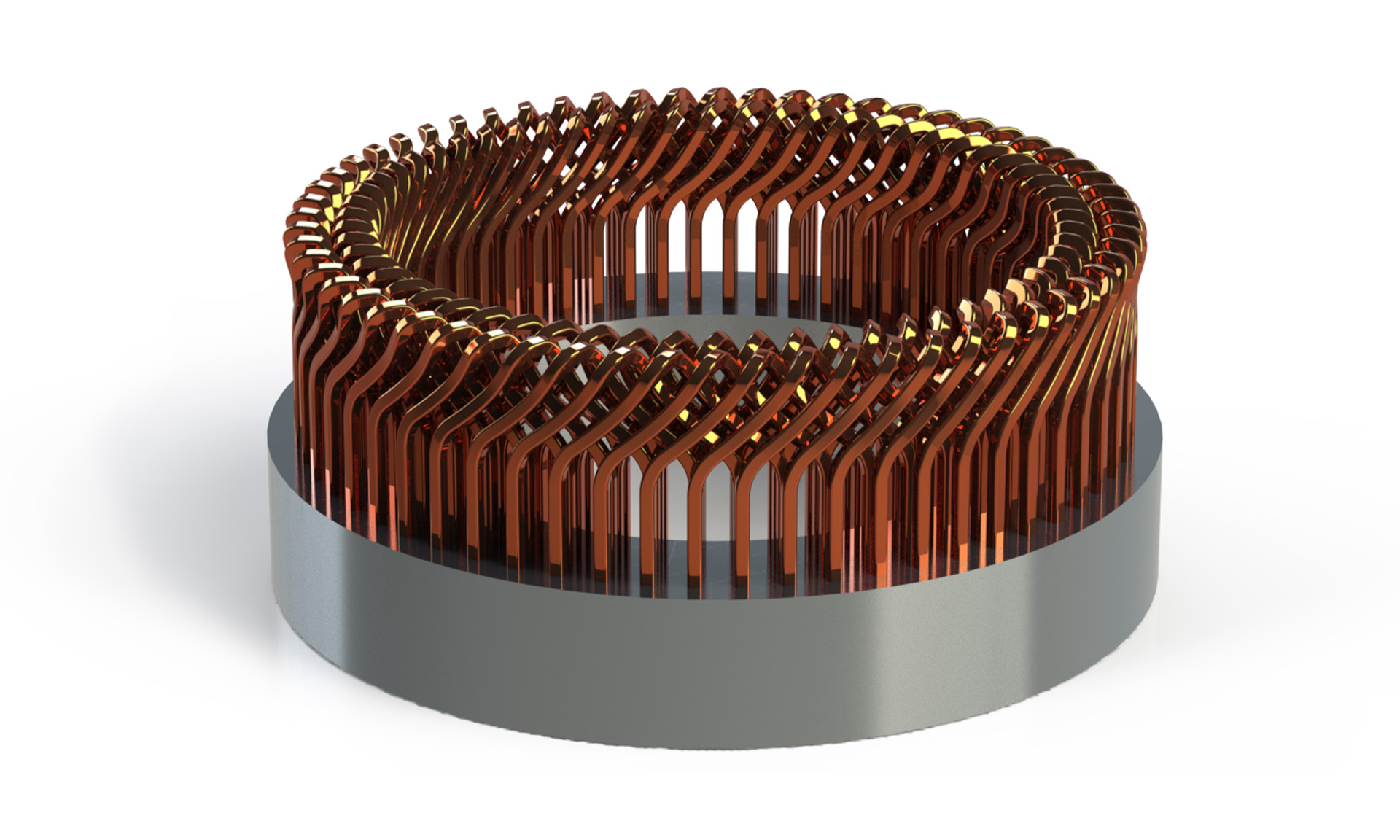
溶接されたヘアピンの例
EVのエンジンやモーターの生産においては、モーターの信頼性と性能にとって重要なプロセスであるヘアピン溶接の最適化に、1つの機会が存在します。従来の機械的なストリッピング(被覆剥離)方法では力不足な場合が多く、それに起因する表面の損傷、工具の摩耗、生産の遅延といったプロセスの非効率性が、コストを押し上げ、プロセスの信頼性に影響を与えます。
レーザによるストリッピングとクリーニングは、機械的なストリッピングの限界を克服できるだけでなく、全体的なコストを抑えつつ優れた結果を達成する、変革的な代替手段です。この記事では、CO₂レーザとUVレーザを組み合わせて活用することによって、溶接に適したきれいな状態のヘアピンを生成する、2工程からなるCoherentの革新的なプロセスについて説明します。本稿に示すデータは、このアプローチによって、卓越した溶接品質を達成する費用対効果の高い方法がEVメーカーに提供されることを実証しています。
ヘアピンの課題
EVモーターの巻線は通常、個別の銅線で構成されます。まず、銅線をU字に曲げて(「ヘアピン」という名称はこれに由来します)、アセンブリに配置します。次に、隣接する各ヘアピンの先端を相互に溶接して電気的に接続し、1本の連続的な巻線にします。さらには、連続的なフラットワイヤを波状のパターン(ウェーブ巻線またはS巻線として知られるものです)に成形して、これを溶接の前にステータースロットに挿入するという、代替設計もあります。
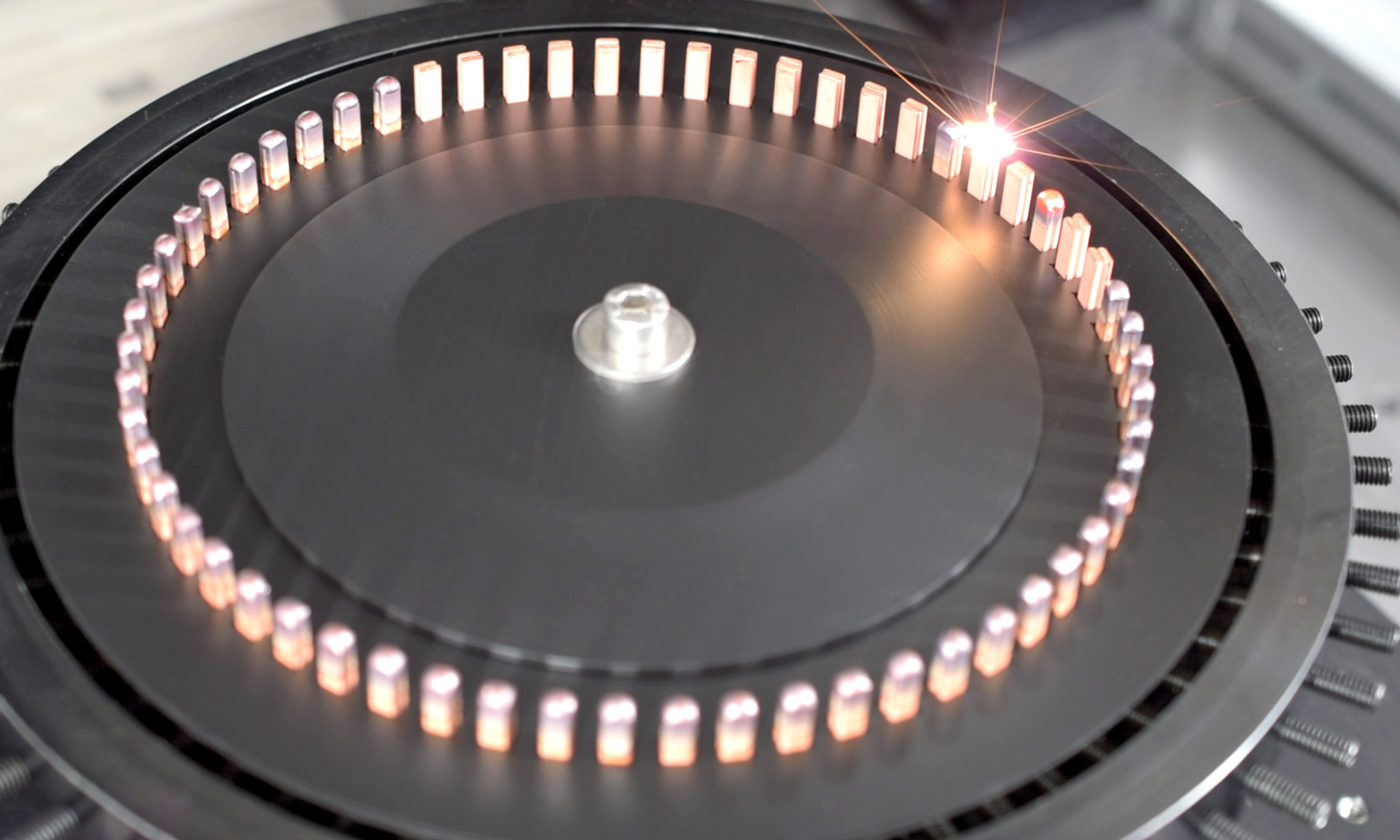
CoherentのARMファイバーレーザ(HIGHmotion 2Dスキャナ装備)で溶接されたヘアピンペアの例
すべての電動モーターにおいて、巻線は絶縁されています。ヘアピンモーターでは、そのコンパクトな設計と、電気自動車に典型的な高電圧要件に対応するために、より厚くて頑丈な絶縁被覆が必要になります。
溶接を行うには、各ヘアピンの両端からこの絶縁被覆を少し除去する必要があります。これは、高品質の電気的および機械的接続を確保するために不可欠な処理です。
従来は、主に機械的な方法でこの処理が行われていましたが、IR(1 um)パルスレーザによるシングルステップのレーザプロセスも使用されています。機械的なストリッピングでは、切断工具をワイヤ表面に直接接触させて、絶縁材を削り取ります。これらの方法は、長年にわたって標準的に用いられてきたものですが、電気自動車(EV)の生産というスピードが求められる分野には、大きな課題を呈します。
例えば、機械的なストリッピングでは物理的な接触が必要であるために、ピンから銅の層が除去されてテクスチャ面が残り、ピンの間に隙間ができて、部品のフィットアップの問題が生じ、溶接の完全性と一貫性が損なわれます。また、機械工具の磨耗は、一貫性のないプロセス、頻繁なメンテナンス、予定外のダウンタイムにつながり、生産の中断を招く可能性もあります。加えて、処理速度が遅くてEV製造の量産需要についていけないという問題があるため、状況はさらに深刻です。
2工程からなるレーザストリッピングで、ワンランク上の品質を実現
レーザは、幅広い種類のアプリケーションにおいて、絶縁材のストリッピングなどの材料除去に使用されています。この用途に対するレーザ処理のメリットとしては、以下のものが挙げられます。
- 接品質の向上:銅線に損傷を与えることなく絶縁材を完全に除去し、望ましい溶接品質につながるきれいな表面を確保します。
- メンテナンスと装置ダウンタイムの低減:工具の摩耗や、機械が詰まる可能性がなくなるため、中断のない生産フローが確保されます。
- スループットの増加:ワイヤを供給しながら連続的にストリッピングが行われるため、生産効率が向上します。
- 一貫性の強化:摩耗や接触がないため、レーザプロセスは安定性と再現性に優れています。
レーザ処理によってプロセスを改善できることは、容易に理解できます。しかし、本当の疑問は、「最良のレーザはどれか」ということです。このプロセスを実行できる可能性のある数多くのレーザ光源と実装方法の中で、EVモーターの量産アプリケーションに対して、品質、速度、コストの優れたバランスを提供するのは、どれなのでしょうか。
レーザプロセスの最適化
Coherent は、ほぼすべての種類の産業用レーザを提供するリーディングカンパニーとして、いずれか1つの技術を潜在的に優先することなく、このアプリケーションを客観的に調査できる比類ない立場にあります。
実際、当社は、ヘアピンストリッピングに最適な単一のレーザを特定したわけではありませんでした。当社のアプリケーションエンジニアが開発したのは、2種類のレーザを使用してコーティング除去の効率化を達成するプロセスです。このアプローチは現在、高い溶接前表面品質を、費用対効果の高い方法でお客様に提供しています。2種類のレーザを使うプロセスを検討する主な動機付けとなったのは、シングルステップのレーザストリッピングプロセスの問題を克服したいという思いでした。
シングルステップのレーザ処理は、コーティングへの吸収とその下の銅への吸収の間の妥協点を探す処理になります。ファイバーレーザの1 µm付近のIR波長は、コーティングに簡単には吸収されないため、照射部分は加熱され、剥がれ落ちたコーティングは微粒子となって大気中に浮遊します。この微粒子は、入射レーザビームに干渉して、ピンの清浄度に影響を与えたり、システムの中に捕捉されて、装置を頻繁に停止して洗浄しなければならない状態を招いたりする恐れがあります。また、ファイバーレーザのIRビームの一部はコーティングを透過してしまうため、ポリマー残渣を銅表面から完全に除去することができません。銅線の表面を溶融して、水素や炭素といった絶縁ポリマーの成分にさらす可能性もあります。そうすると表面が汚染されて、その後の溶接品質に影響が生じる恐れがあります。
Coherent のヘアピン前処理レーザプロセスの2つの工程
- ・バルクストリッピング:中出力のCO₂レーザを使用して、絶縁材の大部分を高速に除去します。このタイプのレーザは、高スループットの非金属材料除去に適しています。
- ・最終クリーニング:続いて、低出力のナノ秒パルスUV固体レーザを使用して、残った絶縁材を除去します。これにより、溶接に適したきれいな表面が得られます。UV固体レーザの短い波長は、高精度材料加工に適しており、ポリマー、その他の有機材料、銅など、幅広い種類の材料の除去に特に効果的です。
バルクストリッピング処理に対しては、Coherent J-5-10.6 µmレーザが理想的な光源であることが実証されています。ヘアピンの絶縁にはさまざまな材料が使用されますが(ポリイミド、ポリエーテルイミド、ポリエステル、ポリエステルイミド、ポリアミド、ポリエーテルエーテルケトン、エポキシ樹脂、各種フッ素樹脂など)、いずれもこのレーザの10.6 µmの出力波長を強く吸収します。また、これらの材料のすべてで、当社が提供する他のCO₂レーザの波長(9.4 µmや10.2 µmなど)よりも10.6 µmの方が、吸収率が高くなります。
Coherent J-5-10.6 µmは、実用上望ましい特性も備えます。完全密閉構造のパルスCO₂レーザで、平均出力は400 Wを超えるため、高スループットのストリッピングが可能です。また、自己完結型のコンパクトなパッケージで提供されており、自動装置への組込みに適しています。
最終クリーニング処理に対しては、Avia LX 355-30-60 HEがまさに適切な組み合わせの出力パラメータを提供します。これは、周波数3倍化LD励起固体レーザで、波長355 nmで平均出力は30 Wです。最も重要な点は、最大300 kHzの繰返周波数での動作と最大500 µJ のパルスエネルギーをサポートしていることです。これにより、高精度のアブレーションをこのアプリケーションに必要な速度で行うことができます。
Avia LX 355-30-60 HEはさらに、簡単に組込めるように設計されています。また、内蔵されているCoherent PureUV™アクティブクリーニングエンジンにより、卓越した寿命と、メンテナンスフリーの動作が実現されています。
溶接結果
当社の応用ラボは、上記の2工程の組み合わせにたどり着くまでに、さまざまなプロセスを検討しました。CO₂レーザ、ナノ秒パルスIR ファイバーレーザ、ナノ秒UVレーザなど、さまざまなレーザを、単体と組合わせの両方で調査しました。絶縁被覆付きヘアピンの処理結果を詳細に分析して、有望な光源を特定した後に、具体的なプロセスパラメータを最適化しました。
試験の一環として、X線光電子分光法(XPS)を使用して表面化学を分析し、汚染物質の特性評価と定量化を行いました。この作業により、2工程からなるレーザストリッピングプロセス(CO₂レーザとUVレーザの組み合わせ)が、レーザ溶接前に銅表面から残留物をすべて除去するための効果的な手段であることを発見しました。

この一連の写真は、CO₂レーザ、ナノ秒IR ファイバーレーザ(FL)、ナノ秒UV固体レーザを使用した除去手法を比較するものです。上列の写真の絶縁材はポリアミド(PA)で、下列はポリエーテルエーテルケトン(PEEK)です。目視だけでも、CO₂+UVレーザの組合わせがどちらの場合に対しても良好であることがわかります。この結果は、実際の溶接試験で確認されています。
当然ながら、最も重要な指標は、コーティング除去後に得られる溶接品質です。以下の図は、溶接後のヘアピンの一連のX線画像を示したものです。2工程(CO₂ + UVレーザ)のプロセスが、最終的に卓越した溶接部を生成することがわかります。CO₂レーザとUVレーザによる2工程のレーザストリッピングは、表面のポリマー残渣を溶接前に除去することにより、溶接部のポロシティ(空孔)を最小限に抑えます。ポリマー残渣には、水素や炭素などの有機物が含まれており、これが液状の金属溶融池に混入すると、溶接部の凝固過程でポロシティが形成されることが知られています。ポロシティは、溶接部の機械的および電気的性能に影響を与えます。
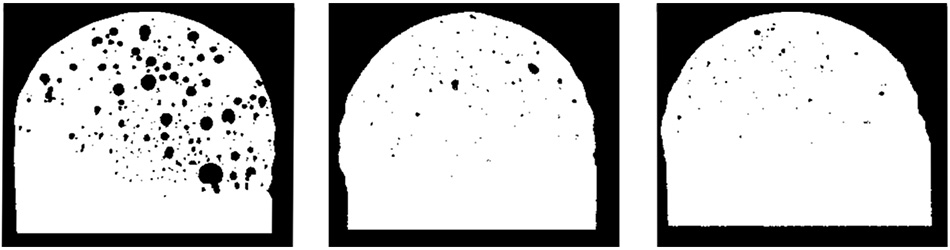
3つの除去手法による溶接ビードのX線画像。CO₂レーザとUV固体レーザを使用する場合に、最も高い溶接品質が得られる(ポロシティ含有率が最も低い)ことが明らかに見てとれます。