Laser Pas de Deux, EV 모터 용접을 한 차원 높이다
밀봉 CO2 및 UV 고체 레이저를 결합하면 EV 모터 대량 생산에 필요한 고품질로 비용 효율적인 헤어핀 스트리핑 및 세척이 가능합니다.
2025년 2월 12일, Coherent
EV 제조업체는 품질을 개선하면서 운영을 최적화하고 비용을 절감해야 한다는 압박을 받고 있습니다. 이러한 노력은 EV 시장 점유율, 특히 상당한 총 소유 비용(TCO) 민감성이 있고 ICE 차량이 여전히 널리 사용되고 있는 볼륨 시장에서 필요한 확장에 매우 중요합니다.
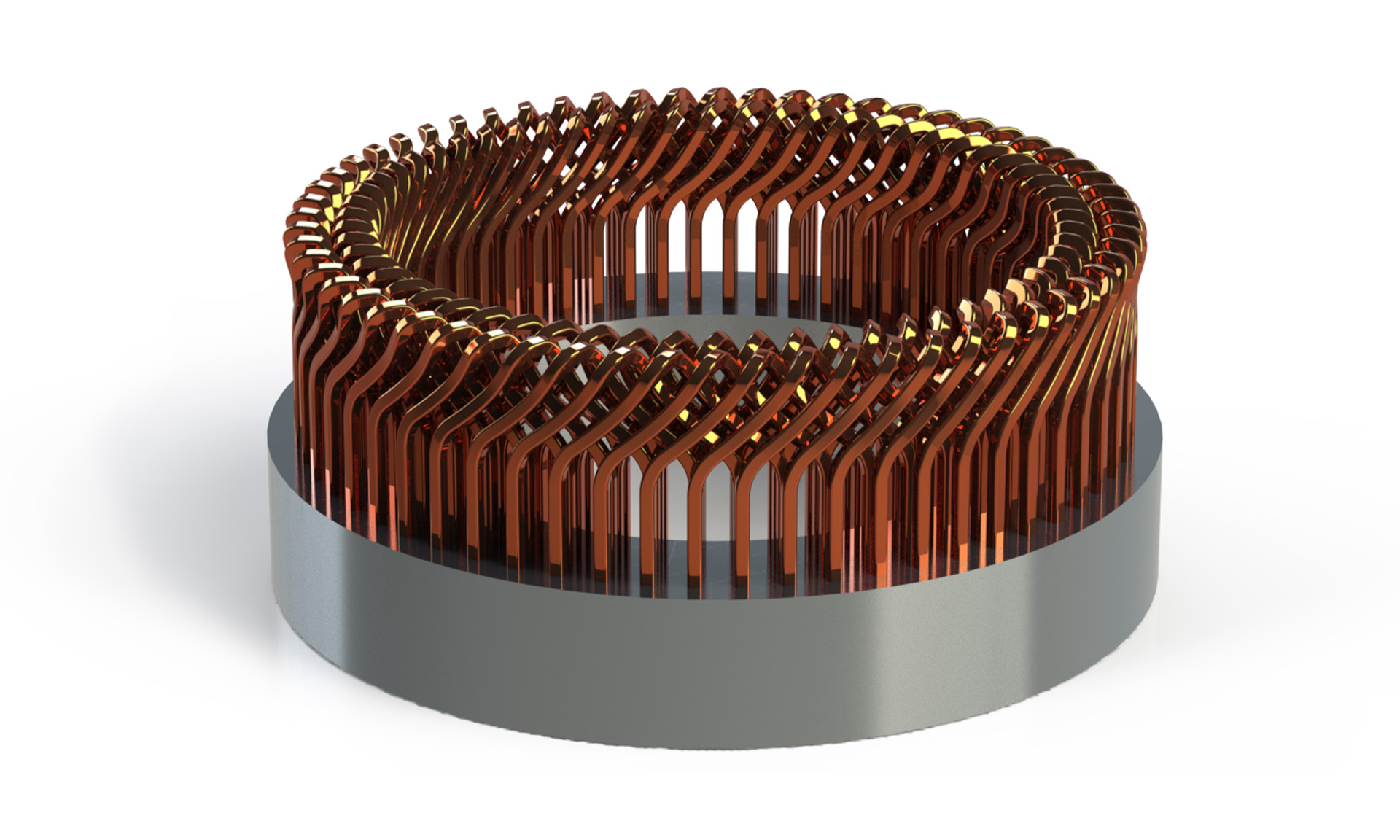
용접 헤어핀의 예.
EV 엔진 또는 모터 생산의 경우, 한 가지 기회는 모터 신뢰성 및 성능에 중요한 공정인 헤어핀 용접을 최적화하는 것입니다. 기존의 기계적 스트리핑 방법은 종종 짧아서 표면 손상, 공구 마모 및 생산 지연과 같은 공정 비효율성을 초래하여 비용을 높이고 공정 신뢰성에 영향을 미칩니다.
레이저 스트리핑 및 세척은 기계적 스트리핑의 한계를 극복하는 동시에 전체 비용을 낮추면서 우수한 결과를 제공할 수 있는 혁신적인 대안을 제공합니다. 여기서는 CO2와 UV 레이저를 함께 사용하여 깨끗한 용접용 헤어핀을 생산하는 Coherent의 혁신적인 2단계 공정을 설명합니다. 여기에 제시된 데이터는 이 접근 방식이 EV 제조업체에게 우수한 품질의 용접을 달성할 수 있는 비용 효율적인 방법을 제공한다는 것을 보여줍니다.
헤어핀 허들
EV 모터의 권선은 일반적으로 개별 구리 와이어로 형성됩니다. 이들은 “U” 모양(따라서 “헤어핀”이라는 이름)으로 구부러진 다음 어셈블리에 배치됩니다. 다음으로 인접한 각 헤어핀의 끝을 이웃에 용접하여 전기적으로 연결하고 단일 연속 권선을 생성합니다. 또한 일부 대체 설계에서는 파도 같은 패턴(파 권선 또는 S 권선이라고 함)으로 형성된 연속 플랫 와이어를 사용한 다음 용접하기 전에 고정자 슬롯에 삽입합니다.
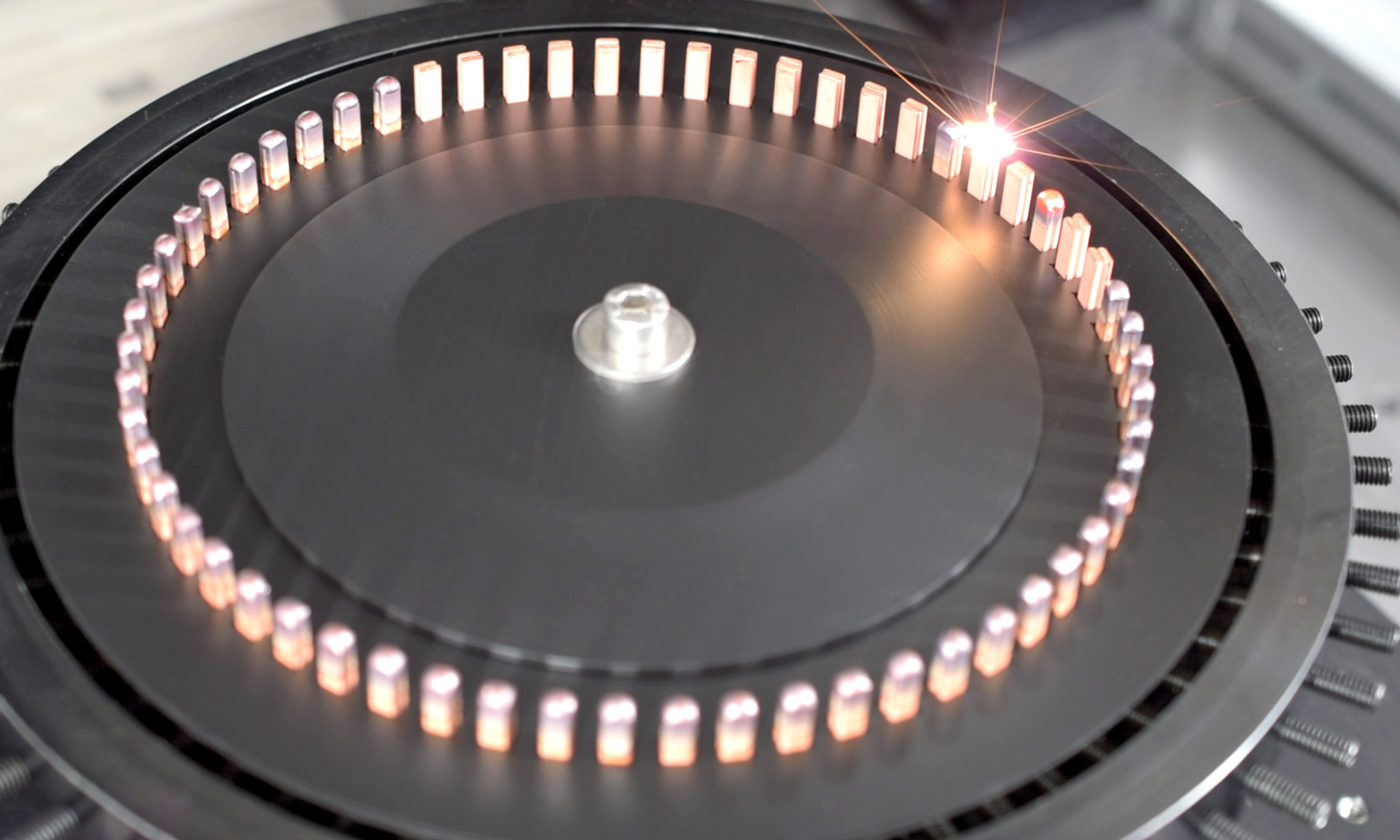
Coherent의 ARM 파이버 레이저 HIGHmotion 2D 스캐너로 레이저 용접되는 헤어핀 쌍의 예.
권선은 모든 전기 모터에서 절연됩니다. 헤어핀 모터의 경우 소형 설계와 전기 자동차의 일반적인 고전압 요구 사항을 수용하려면 절연체가 더 두껍고 견고해야 합니다.
용접하기 전에 각 헤어핀의 양쪽 끝에서 소량의 절연체를 제거해야 합니다. 이는 고품질 전기 및 기계적 연결을 보장하는 데 매우 중요합니다.
전통적으로 이 작업은 주로 기계적 방법을 사용하여 수행되었으며 IR(1um) 펄스 레이저를 사용하는 단일 단계 레이저 공정도 사용되었습니다. 기계적 박리에는 와이어 표면과 직접 접촉하는 절단 도구를 사용하여 절연체를 긁어내는 작업이 포함됩니다. 이러한 접근 방식은 수년 동안 표준이었지만, 빠르게 변화하는 전기 자동차(EV) 생산 세계에서는 상당한 문제를 안고 있습니다.
예를 들어 기계적 박리에 필요한 물리적 접촉은 핀에서 구리 층을 제거하여 텍스처 표면을 남기고 핀 사이에 갭과 부품 맞춤 문제를 일으켜 용접의 무결성과 일관성을 손상시킵니다. 또한 기계적 도구의 마모로 인해 공정 불일치, 빈번한 유지보수, 예기치 않은 가동 중단 및 잠재적인 생산 중단이 발생합니다. 이러한 문제는 공정 속도가 느려서 복합적으로 나타나며, EV 제조의 대량 수요를 따라잡기 어렵습니다.
2단계 레이저 스트리핑은 위 절단입니다.
레이저는 절연 박리를 포함한 광범위한 응용 분야에서 재료 제거에 사용됩니다. 이러한 맥락에서 레이저 가공의 이점은 다음과 같습니다.
- 용접 품질 향상: 구리 와이어의 손상 없이 완전 절연을 제거하면 최적의 용접 품질을 위한 깨끗한 표면이 보장됩니다.
- 유지보수 및 장비 가동 중단 시간 감소: 공구 마모가 없고 기계 걸림 가능성을 제거하면 생산 흐름이 중단되지 않습니다.
- 처리량 증가: 와이어가 공급되는 동안 지속적인 박리는 생산 효율성을 향상시킵니다.
- 향상된 일관성: 마모 또는 접촉 없이 레이저 공정은 안정적이고 재현 가능합니다.
레이저 가공이 공정 개선을 제공할 수 있다는 것을 쉽게 알 수 있습니다. 그러나 실제 문제는 \"최고의 레이저는 무엇입니까?\"입니다. 다시 말해, 이 공정을 수행할 수 있는 수많은 가능한 레이저 소스와 구현 중에서 대량 EV 모터 생산 응용 분야에서 품질, 속도, 비용의 균형을 가장 잘 유지하는 것은 무엇입니까?
레이저 공정 최적화
Coherent는 거의 모든 유형의 산업용 레이저를 제공하는 선도적인 업체로서, 하나의 기술에 대한 고유한 선호도 없이 이 응용 분야를 객관적으로 조사할 수 있는 독보적인 위치에 있습니다.
사실 헤어핀 박리에 가장 적합한 레이저를 찾지 못했습니다. 대신, 당사의 응용 엔지니어는 최적화된 코팅 제거를 달성하기 위해 2레이저 공정을 개발했습니다. 이러한 접근 방식은 오늘날 고객에게 가장 비용 효율적인 방식으로 최상의 사전 용접 표면 품질을 제공합니다. 2레이저 공정을 조사하는 주된 동기는 단일 단계 레이저 박리 공정의 문제를 극복하는 것이었습니다.
단일 단계 레이저 가공은 코팅의 흡수와 기본 구리 사이의 타협입니다. 파이버 레이저의 거의 1μm IR 파장은 코팅에 의해 쉽게 흡수되지 않아 인터페이스에서 가열되고 코팅이 공기 중 입자로 박리됩니다. 입자는 핀의 청결도에 영향을 미치는 유입 레이저 빔을 방해할 수 있으며 시스템에 갇히게 되어 장비를 청소하기 위해 자주 중단될 수 있습니다. 또한 파이버 레이저의 침투된 IR 빔은 구리 표면에서 폴리머 잔류물을 완전히 제거할 수 없습니다. 구리 와이어의 표면을 녹이고 수소 및 탄소와 같은 절연체 폴리머의 성분을 노출시킬 수 있습니다. 이로 인해 표면이 오염되어 후속 용접 품질에 영향을 줄 수 있습니다.
Coherent 2단계 레이저 기반 헤어핀 준비 공정에는 다음이 포함됩니다.
- 벌크 박리: 대부분의 절연체는 미드파워 CO2 레이저를 사용하여 빠르게 제거됩니다. 이 유형의 레이저는 고처리량 비금속 재료 제거에 이상적입니다.
- 최종 세척: 그런 다음 펄스형 저출력 나노초 UV 고체 레이저를 사용하여 절연 잔류물을 제거합니다. 이를 통해 용접을 위한 깨끗한 표면을 제공합니다. UV 고체 레이저의 짧은 파장은 고정정밀도 재료 가공에 탁월하며 폴리머, 기타 유기 재료 및 구리를 포함한 광범위한 재료를 제거하는 데 특히 효과적입니다.
벌크 스트리핑 단계에서 Coherent J-5-10.6μm 레이저가 이상적인 소스임이 입증되었습니다. 헤어핀 절연에 사용되는 다양한 재료(폴리이미드, 폴리에테르이미드, 폴리에스테르, 폴리에스테르이미드, 폴리아미드, 폴리에테르 에테르 케톤, 에폭시 수지 및 다양한 플루오로중합체 포함)가 있지만, 모두 이 레이저의 10.6μm 출력 파장을 강하게 흡수합니다. 그리고 이러한 모든 재료에 대해 흡수는 9.4μm 및 10.2μm와 같이 제공되는 다른 사용 가능한 CO2 레이저 파장보다 10.6μm에서 더 높습니다.
Coherent J-5-10.6μm는 또한 바람직한 실제 특성을 가지고 있습니다. 400W 이상의 평균 출력을 생성하는 완전 밀봉 펄스 CO2 레이저로, 고처리량 스트리핑을 수행할 수 있습니다. 또한 자동화된 장비에 통합하기에 이상적인 독립형 소형 패키지입니다.
최종 세척 단계에서 Avia LX 355-30-60 HE는 출력 매개변수의 올바른 조합만을 보여줍니다. 355nm에서 30W의 평균 출력을 출력하는 주파수 3배, 다이오드 펌프, 고체 레이저입니다. 가장 중요한 점은 최대 300kHz의 반복률과 최대 500μJ의 펄스 에너지에서 작동을 지원하는 것입니다. 이를 통해 이 응용 분야에 필요한 속도로 고정정밀도 절제가 가능합니다.
Avia LX 355-30-60 HE는 간편한 통합을 위해 설계되었습니다. 그리고 Coherent PureUV™ 능동 레이저 세척 엔진의 통합은 탁월한 수명과 유지보수 없는 작동을 제공합니다.
용접 결과
응용 연구실은 방금 설명한 2단계 조합에 도달하기 전에 여러 가지 다른 프로세스를 조사했습니다. CO2, 나노초 펄스 IR 파이버 레이저 및 나노초 UV 레이저를 포함한 다양한 레이저를 단일 및 조합하여 검사했습니다. 절연 헤어핀 가공 결과를 자세히 분석하고 가장 유망한 출처가 식별되면 특정 공정 매개변수를 최적화했습니다.
테스트의 일환으로 X선 광전자 분광학(XPS)을 사용하여 표면 화학을 분석하여 오염 물질을 특성화하고 정량화했습니다. 여기에서 2단계 레이저 박리 공정(UV 레이저와 결합된 CO2)이 레이저 용접 전에 구리 표면에서 모든 잔류 요소를 제거하는 가장 효과적인 수단임을 발견했습니다.

이 일련의 사진은 CO2, ns IR 파이버(FL) 및 ns UV 고체 레이저를 사용하여 다양한 제거 기술을 비교합니다. 사진의 맨 위 행에서 절연체는 폴리아미드(PA)였고 맨 아래 행에서 절연체는 폴리에테르 에테르 케톤(PEEK)이었습니다. 순수한 육안 검사조차도 CO2 + UV 레이저 조합이 두 경우 모두에서 가장 잘 나타난다는 것을 보여줍니다. 이는 실제 용접 시험을 통해 확인되었습니다.
물론 가장 중요한 메트릭은 코팅 제거 공정 후 얻은 용접 품질입니다. 다음 그래픽은 용접된 헤어핀의 일련의 X선 이미지를 보여줍니다. 이를 통해 2단계(CO2 + UV 레이저) 공정이 궁극적으로 우수한 용접을 제공한다는 것을 알 수 있습니다. 2단계 CO2 + UV 레이저 박리는 용접 전에 표면의 폴리머 잔류물을 제거하여 용접 다공성을 최소화합니다. 폴리머 잔류물은 수소, 탄소 및 기타 유기 원소를 포함하는 것으로 알려져 있으며, 이는 액체 상태에서 용융 금속 풀로 들어간 다음 용접 고형화 공정 중에 다공성을 형성할 수 있습니다. 다공성은 용접의 기계적 및 전기적 성능에 영향을 미칩니다.
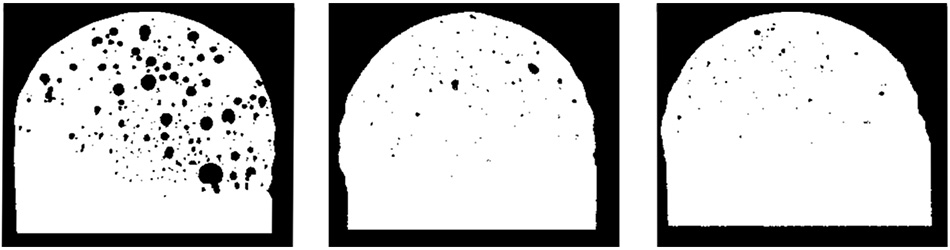
세 가지 제거 전략을 사용한 용접 비드의 X선 이미지. CO2 + UV 고체 레이저는 가장 높은 용접 품질(최저 다공성 함량)을 명확하게 보여줍니다.