CUSTOMER SUCCESS STORY
Teamwork Improves Precision Laser Welding
Tight coordination between the Photon Automation and Coherent applications teams enabled rapid development of an advanced laser welding process.
Photon Automation, Inc. (Greenfield, Indiana, USA) has been designing and developing automated systems for manufacturing since 2000. The company’s ability to consistently deliver solutions that increase productivity and reduce costs has enabled them to build a highly successful business. Today they service customers in diverse areas including energy storage, medical device, consumer products, communications, automotive manufacturing, and aerospace.
Photon Automation currently occupies 250,000 ft² of space, including applications development laboratories, engineering offices, a machine shop and manufacturing space. In addition to designing and building custom automation systems, they also provide applications development services, prototype manufacturing and testing, and design for manufacturability (DFM) consulting. Photon Automation products range from semi-automated, stand-alone tools or fixtures to fully automated production lines.
In 2023 Photon Automation was asked to bid on a welding system for joining busbars to battery terminals for an energy storage application. Their requestor had already worked with another prototyping house on a laser welding system, but they weren’t entirely happy with the results.
In particular, the welding process the end user had was producing a significant amount of spatter. They knew that this spatter typically correlated with weld porosity and poor weld strength. Based on prior positive experiences with Photon Automation, they believed the company would be able to identify the source of the problem and provide the welding technology necessary to eliminate it. And they were confident that Photon Automation could accomplish this all in a timely fashion.
Identifying a Successful Process
Photon Automation began by reaching out to Coherent Labs in Plymouth, Michigan. They asked us to do some testing on the customer-supplied samples using our adjustable ring mode fiber laser (ARM FL) laser. Their prior experience with this laser had shown them that its unique combination of back-reflection immunity, excellent beam quality, and advanced capability for closed-loop power control would enable it to successfully perform this type of difficult weld.
This testing confirmed the capability of the ARM FL, in particular that it provided the spatial and temporal control over how laser power is delivered to eliminate the spatter issue. It also showed that this specific process would require 8 kW of power because of the part thicknesses involved. “We weren’t surprised at the results from the ARM FL,” notes William Huffman, CEO, Photon Automation. “It has proven itself to us in the past as very capable for tackling these kinds of very demanding welding processes.”
Coherent also performed pull tests of the welds to measure their mechanical strength. These confirmed that the ARM fiber laser process delivered the required joint quality. Plus, Photon Automation used their own CT scanner to obtain detailed views of the weld cross sections. This is necessary because a weld that looks cosmetically good from the surface may be still hiding defects underneath. Polished and etched cross-sections may or may not show porosity or cracks that could exist in front of or behind the sample, whereas CT scans show the entire weld in three dimensions.
The CT scans of the ARM laser welds confirmed what Photon Automation had hoped. Namely that weld porosity had been reduced, and that this correlated with a lower concentration of stress risers in the weld. Stress risers are features that cause a concentration of stress in a localized area of a weld joint. These stress concentrations can significantly increase the likelihood of failure, such as cracking or fatigue, under load or vibration.
Photon Automation presented the weld comparisons, including the CT scans, to their customer. While there were multiple factors involved in the customer’s decision making, Photon Automation credits the demonstrated weld quality as the key determining factor in why they won the contract to produce the welding systems.
Coming up to Speed
While the initial applications testing proved that the ARM fiber laser could deliver the required process, Photon Automation understood that there was still quite a bit of work involved in developing a production ready tool around it.
One of the central issues was creating a control system that could take full advantage of the inherent speed capability and other key features of the laser. In particular, the ability of the ARM fiber laser to very rapidly and independently change power in the center and ring beams offers distinct advantages over other lasers that lack this ability. Fully utilizing this capability promised to improve process quality and also deliver a throughput rate that would meet their customer’s needs.
But this challenge played straight into the core competency at Photon Automation. Specifically, this is the ability to combine laser sources, beam delivery systems, motion control, and part handling robotics with the level of precision and control needed to perform the most difficult welding tasks. These are welds that involve factors like high-value materials, high performance joint requirements, or widely dissimilar materials. All of these conditions reduce the process window, necessitating this higher degree of control.
The out-of-the-box control system Photon Automation was presented with at the time had a latency in the 8 ms to 12 ms range. This delay between when the controller initiates a power change and when the laser actually responds to that change caused significant issues when attempting to weld conductors onto lithium-ion battery cells. This was because the scanner was capable of moving the beam on the work surface much faster than the power could be changed in the laser.
Faced with the latency limitations of the existing control hardware, the Photon software team needed to include dwell time within their code to compensate for these indeterminate delays. Photon Automation engineer Michael Dupont knew that a more elegant solution for this impediment would be to use a dedicated signal processor instead of ‘cheating’ the code with artificial delays to compensate for the laggy hardware.
Michael demonstrated his invention to the Photon management team with a wire-wrapped microprocessor-based control board that he put together. This was the start of Photon Automation’s WonderBoard™, a high-speed, dedicated control platform with the sole purpose of providing discrete, independent control of the laser center and ring power in conjunction with spatial position of the laser on the workpiece via custom laser path planning software.
Working in close consultation with Coherent gave Photon Automation access to our in-depth knowledge of the exact workings of the ARM fiber laser. This enabled them to fully optimize the performance of their new controller. Using the WonderBoard™ with the Coherent ARM fiber laser reduced the latency in their overall system (controller, scanner, and laser) down to 2.5 µs – an improvement of nearly 5,000X! The combination of this responsive controller, beam delivery system, and part handling robotics from Photon Automation, plus the Coherent ARM fiber laser, formed the heart of the welding system they delivered.
“We knew before we started this project that the Coherent ARM fiber laser had unique capabilities and offered some big advantages for this kind of demanding welding application,” notes William Huffman, CEO, Photon Automation. “But equally important to the success of this project was the level of cooperation and coordination between our two applications teams. Our technical people are in continual contact and work together very closely. We get an immediate response when we have a question or need a test from the Coherent applications lab. And we’ll help Coherent out, too, because we have different equipment and can perform tests they don’t have direct access to, including the use of Photon’s CT scanning capability. This arrangement allows us to get the absolute best performance possible from the laser, and it gets us to that point very fast. That enables us to keep our customers happy and maintain a competitive edge.”
“Coherent has creative people in their lab who can solve problems. When you combine this with their superior laser technology, you have a partner for mastering the most difficult welding challenges."
— William Huffman, CEO, Photon Automation, Inc.
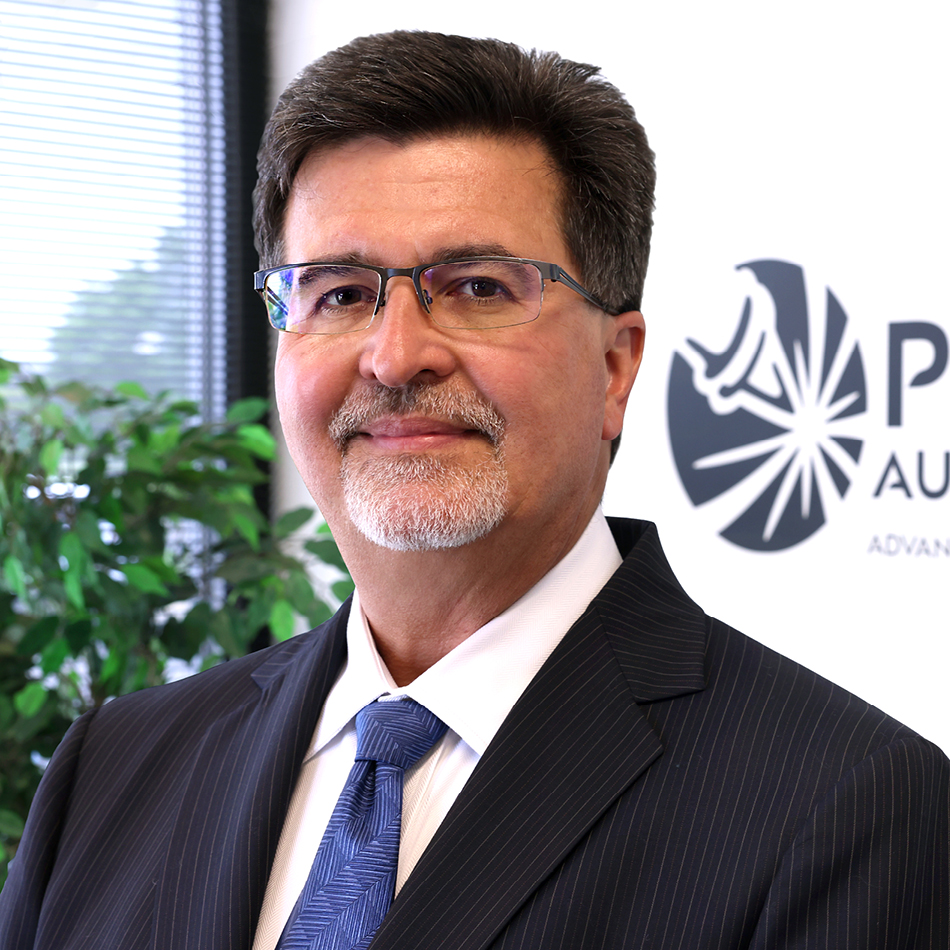
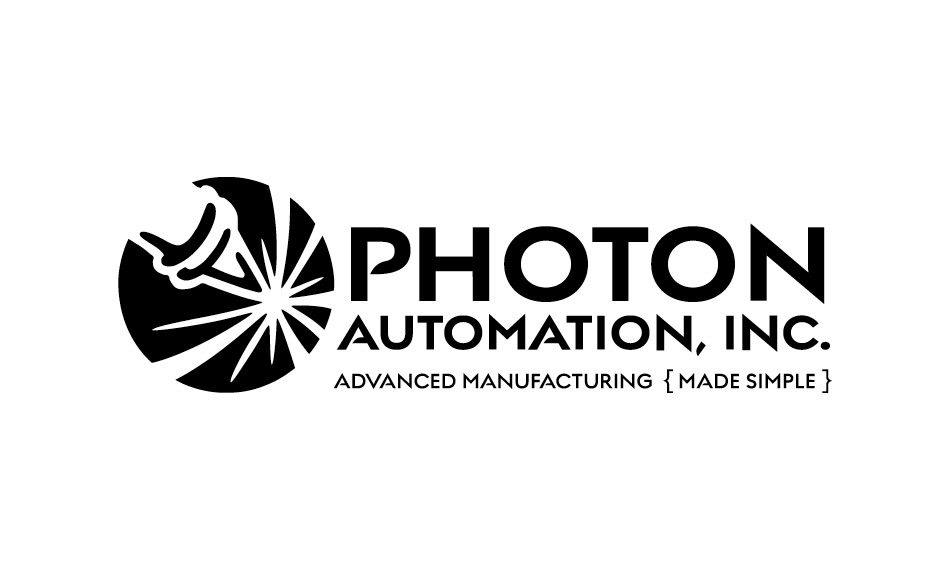

The complete, automated system from Photon Automation for battery welding.
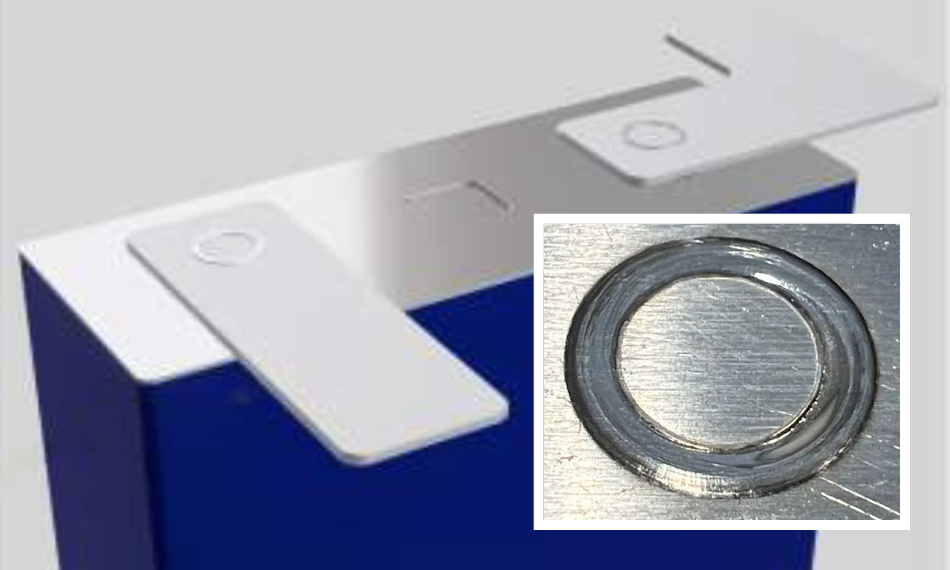
The battery-to-busbar terminal weld involved joining two aluminum parts with high mechanical strength and low electrical resistance.