ERFOLGSGESCHICHTE EINES KUNDEN
Teamarbeit verbessert das Präzisions-Laserschweißen
Eine enge Kooperation zwischen den Teams von Photon Automation und Coherent ermöglichte die schnelle Entwicklung eines hochentwickelten Laserschweißprozesses.
Photon Automation, Inc. (Greenfield, Indiana, USA) konzipiert und entwickelt seit dem Jahr 2000 automatisierte Fertigungssysteme. Die Fähigkeiten des Unternehmens bei der Bereitstellung sowohl produktionssteigernder als auch kostensenkender Lösungen haben es schnell sehr erfolgreich gemacht. Heute verfügt es über einen Kundenstamm in verschiedenen Branchen wie Energiespeicherung, Medizingeräte, Konsumprodukte, Kommunikation, Automobilfertigung und Luft- und Raumfahrt.
Photon Automation vereint auf einer Fläche von rund 23.000 m² verschiedene Anwendungs-Entwicklungslabore, Ingenieurbüros, eine Maschinenwerkstatt und Produktionsanlagen. Neben der Entwicklung und Fertigung kundenspezifischer Automatisierungssysteme bietet das Unternehmen auch Anwendungsentwicklungsdienste, Prototypenfertigung und -tests sowie Beratung zum Thema Design for Manufacturability (DFM) an. Die Produkte von Photon Automation reichen von halbautomatischen, eigenständigen Werkzeugen oder Vorrichtungen bis hin zu vollständig automatisierten Produktionsstraßen.
2023 wurde Photon Automation aufgefordert, ein Gebot für ein Schweißsystem zur Verbindung von Stromschienen mit Batterieklemmen für eine Energiespeicheranwendung abzugeben. Der Anfragesteller hatte bereits mit einem anderen Prototypenhersteller an einem Laserschweißsystem gearbeitet, war aber unzufrieden mit den Ergebnissen.
Insbesondere entstanden durch den Schweißprozess beim Endanwender hohe Mengen an Spritzern. Der Kunde wusste, dass diese Spritzer üblicherweise mit der Porosität der Schweißnaht und geringer Schweißnahtfestigkeit zusammenhingen. Basierend auf früheren positiven Erfahrungen mit Photon Automation war er überzeugt, dass das Unternehmen in der Lage wäre, die Quelle des Problems zu identifizieren und die erforderliche Schweißtechnologie für seine Lösung bereitzustellen. Und er war zuversichtlich, dass Photon Automation all das in kürzester Zeit vollbringen könnte.
Identifizierung eines erfolgreichen Prozesses
Photon Automation begann mit seiner Arbeit, indem es Coherent Labs in Plymouth, Michigan, kontaktierte. Das Unternehmen bat uns, einige Tests an den vom Kunden bereitgestellten Mustern mithilfe unseres Adjustable Ring Mode-Faserlasers (ARM-FL) durchzuführen. Frühere Erfahrungen mit diesem Laser hatten gezeigt, dass seine einzigartige Kombination aus der Vermeidung von Rückreflexionen, hervorragender Strahlqualität und fortschrittlicher Leistungsregelung die erfolgreiche Durchführung dieses schwierigen Schweißvorgangs ermöglichen sollten.
Diese Tests bestätigten die Leistungsfähigkeit des ARM-FL, insbesondere, dass es die räumliche und zeitliche Kontrolle über die Abgabe der Laserleistung ermöglicht, um das Problem der Spritzer zu beseitigen. Es zeigte sich zudem, dass dieser spezifische Prozess aufgrund der Dicke der geschweißten Werkstücke 8 kW Leistung erfordern würde. „Wir waren nicht überrascht von den Ergebnissen des ARM-FL“, sagte William Huffman, CEO, Photon Automation. „Er hat sich für uns bereits in der Vergangenheit als sehr gut geeignet für diese Art herausfordernder Schweißprozesse erwiesen.“
Coherent führte auch Zugversuche an den Schweißnähten durch, um deren mechanische Festigkeit zu messen. Diese bestätigten, dass der ARM-Faserlaser die benötigte Schweißqualität lieferte. Zudem verwendete Photon Automation seinen eigenen CT-Scanner, um detaillierte Querschnitt-Ansichten der Schweißstellen zu erhalten. Das ist notwendig, da selbst eine von außen gut aussehende Schweißnaht in ihrem Inneren Defekte verbergen kann. Polierte und geätzte Querschnitte zeigen nicht in jedem Fall Porosität oder Brüche, die sich vor oder hinter dem Muster verbergen könnten, während CT-Scans die gesamte Schweißnaht in drei Dimensionen offenlegen.
Die CT-Scans der ARM-Laserschweißnähte bestätigten, worauf Photon Automation gehofft hatte. Nämlich, dass die Schweißporosität reduziert wurde und dies mit einer geringeren Konzentration von Belastungszonen einherging. Belastungszonen sind Merkmale, die zu einer Zunahme der Belastung in einem bestimmten Bereich einer Schweißnaht führen. Diese Belastungskonzentrationen können bei hoher Last oder Vibration die Wahrscheinlichkeit eines Bruchs oder einer Materialermüdung signifikant erhöhen.
Photon Automation präsentierte seinem Kunden den Schweißnahtvergleich, einschließlich der CT-Scans. Während die Entscheidung des Kunden verschiedene Dinge berücksichtigte, nennt Photon Automation die demonstrierte Schweißqualität als bestimmenden Faktor dafür, warum das Unternehmen den Vertrag zur Fertigung der Schweißsysteme gewann.
Vom Prototyp zum fertigen System
Während die ersten Anwendungstests bewiesen, dass der ARM-Faserlaser den geforderten Prozess liefern kann, war Photon Automation klar, dass es noch einiges an Arbeit gab, um ein produktionsreifes System zu entwickeln.
Eine der zentralen Herausforderungen war, ein Kontrollsystem zu entwickeln, das so gut wie möglich von der Geschwindigkeit und anderen wichtigen Funktionen des Lasers profitieren konnte. Insbesondere die Fähigkeit des ARM-Faserlasers, sehr schnell und unabhängig die abgegebene Leistung im zentralen Strahl und den Ringstrahlen zu ändern, bot enorme Vorteile gegenüber anderen Lasern, denen diese Fähigkeit fehlt. Eine vollständige Nutzung dieser Fähigkeit versprach eine gesteigerte Prozessqualität und eine Durchsatzrate, die die Bedürfnisse des Kunden erfüllen würde.
Aber diese Herausforderung war wie auf die Kernkompetenzen von Photon Automation zugeschnitten. Insbesondere ist das Unternehmen hervorragend darin, Laserquellen, Strahlführungssysteme, Bewegungssteuerungen und Roboter zur Werkstückführung mit der Präzision und Kontrolle zu kombinieren, die erforderlich sind, um auch die herausforderndsten Schweißaufgaben durchzuführen. Dabei handelt es sich um Schweißnähte, bei denen Faktoren wie hochwertige Materialien, hohe Leistungsanforderungen an die Verbindung oder sehr unterschiedliche Materialien eine Rolle spielen. All diese Bedingungen verkleinern das Prozessfenster, wodurch diese höhere Kontrolle erforderlich wird.
Die fertige Steuerung, die Photon Automation damals vorstellte, hatte eine Latenzzeit im Bereich von 8 ms bis 12 ms. Die Verzögerung zwischen einer Leistungsänderung im Steuermodul und der Reaktion des Lasers auf diese Änderung führte zu großen Problemen bei dem Versuch, Stromleiter an Lithium-Ionen-Batteriezellen zu schweißen. Das lag daran, dass der Scanner den Strahl sehr viel schneller auf der Arbeitsfläche bewegen konnte, als die Ausgangsleistung im Laser geändert werden konnte.
Angesichts der Latenzbeschränkungen in der vorhandenen Steuer-Hardware musste das Software-Team von Photon Automation Wartezeiten in seinen Code integrieren, um diese unvorhersehbaren Verzögerungen zu kompensieren. Ein Ingenieur bei Photon Automation namens Michael Dupont wusste, dass es eleganter wäre, diese Einschränkung mit einem dedizierten Signalprozessor zu lösen, als den Code mit künstlichen Verzögerungen auszustatten, um die hohe Hardware-Latenz zu kompensieren.
Michael stellte dem Management-Team von Photon Automation seine Erfindung vor, eine drahtumwickelte, Mikroprozessor-basierte Steuerplatine, die er entwickelt hatte. Das war der Beginn des WonderBoard™ von Photon Automation, einer dedizierten Hochgeschwindigkeits-Steuerplattform mit dem einzigen Zweck, eine diskrete, unabhängige Steuerung der Center- und Ring-Laserstrahlen im Zusammenspiel mit der räumlichen Position des Lasers auf dem Werkstück über eine eigens entwickelte Laserpfad-Planungssoftware zu ermöglichen.
Die enge Zusammenarbeit mit Coherent gewährte Photon Automation Zugang zu unseren umfangreichen Kenntnissen über die exakte Funktionsweise des ARM-Faserlasers. So konnte das Unternehmen die Leistung seiner neuen Steuerplatine vollständig optimieren. Durch die Verwendung des WonderBoard™ mit dem ARM-Faserlaser von Coherent konnte die Latenz im Gesamtsystem (Steuerplatine, Scanner und Laser) auf 2,5 µs verringert werden – eine Verbesserung um das nahezu 5.000-fache! Die Kombination aus schnell reagierender Steuerplatine, Strahlführungssystem und Robotern zur Werkstückführung von Photon Automation mit dem ARM-Faserlaser von Coherent bildete das Herzstück des an den Kunden gelieferten Schweißsystems.
„Bevor wir mit diesem Projekt begannen, wussten wir bereits, dass der ARM-Faserlaser von Coherent über einzigartige Fähigkeiten verfügte und einige große Vorteile für diese Art herausfordernder Schweißanwendungen bot“, sagte William Huffman, CEO, Photon Automation. „Aber genauso wichtig für den Erfolg des Projekts war die enge Zusammenarbeit und Koordination zwischen unseren beiden Anwendungsteams. Unsere technischen Mitarbeiter waren stets miteinander in Kontakt und haben sehr eng zusammengearbeitet. Wenn wir eine Frage haben oder einen Test benötigen, erhalten wir vom Coherent-Applikationslabor immer sofort eine Antwort. Und wir helfen auch Coherent, da wir über andere Ausrüstung verfügen und Tests durchführen können, zu denen sie keinen direkten Zugang haben, wie beispielsweise mit unserem CT-Scanner. Dieses Arrangement ermöglicht es uns, die absolut bestmögliche Leistung aus dem Laser herauszuholen, und der Weg zu diesem Punkt ist sehr schnell. So können wir unsere Kunden zufriedenstellen und unseren Wettbewerbsvorteil bewahren.“
„Im Labor von Coherent arbeiten kreative Menschen, die Probleme lösen können. In Kombination mit ihrer überragenden Lasertechnologie erhält man dort einen Partner, mit dem man selbst die größten Herausforderungen im Schweißprozess bewältigen kann.“
– William Huffman, CEO, Photon Automation, Inc.
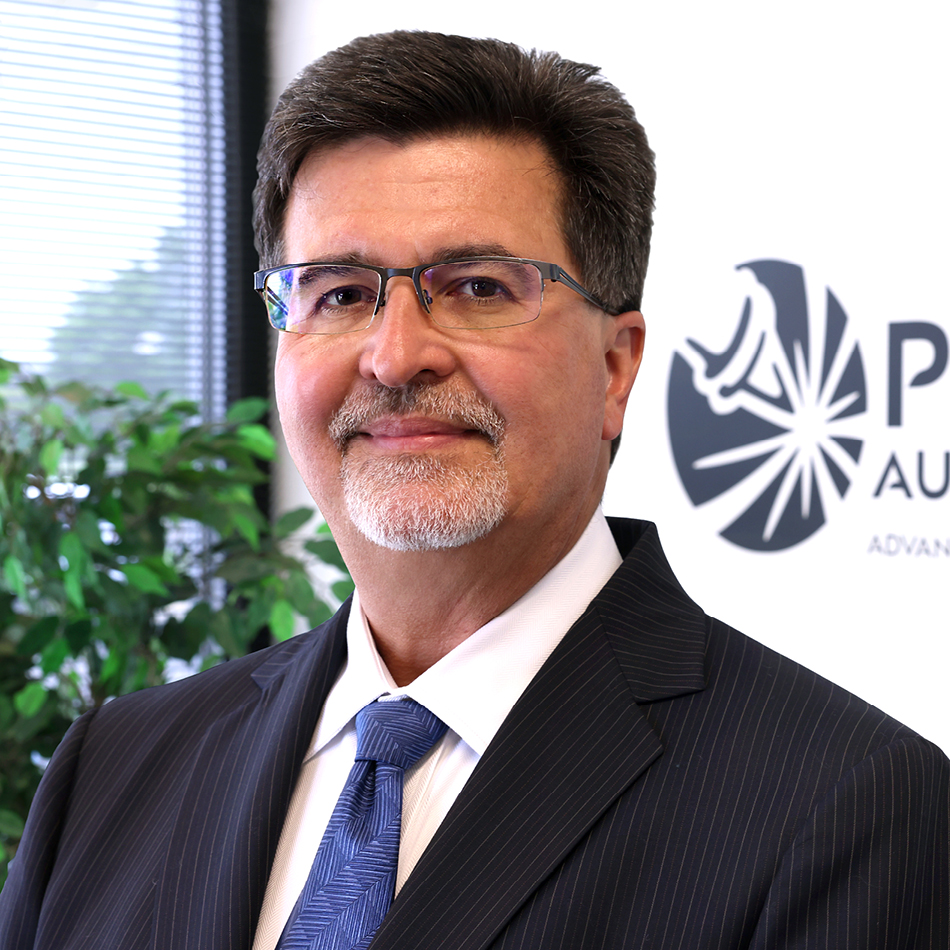
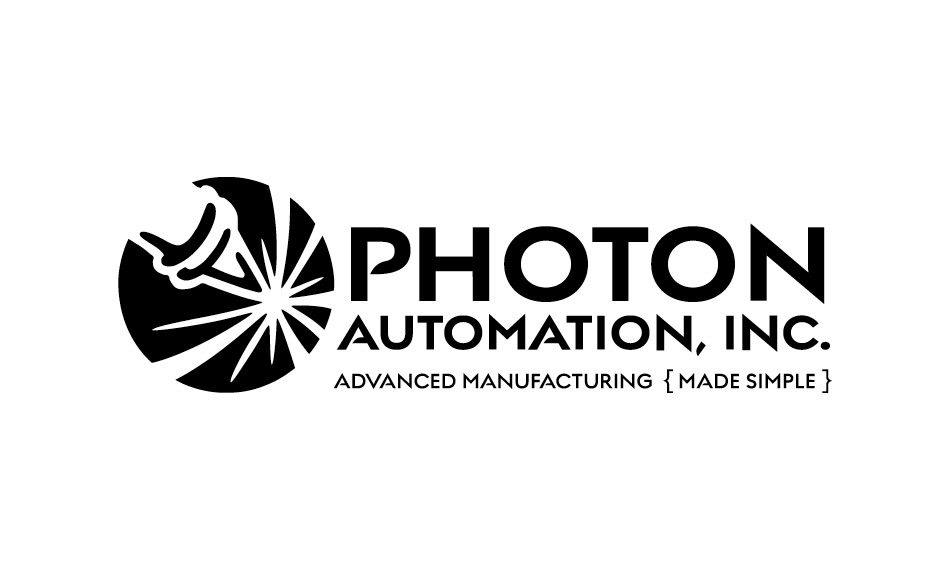

Das vollständige, automatisierte System von Photon Automation zum Batterieschweißen.
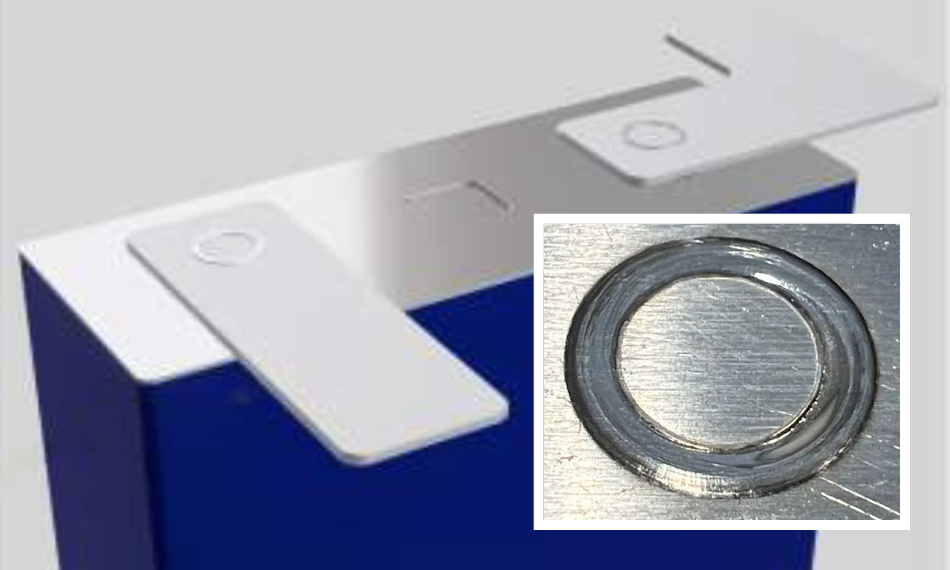
Das Verschweißen von Batterie und Stromschiene umfasste die Verbindung von zwei Aluminiumteilen mit hoher mechanischer Stärke und geringem elektrischem Widerstand.