Lasers in Display Fabrication: Coverglass and Window Cutting
Coherent ultrashort pulse (USP) lasers, together with filamentation technology, cut glass, and sapphire with unmatched results. Combining it with advanced optics enables precise process optimization for specific tasks.
October 4, 2022 by Coherent
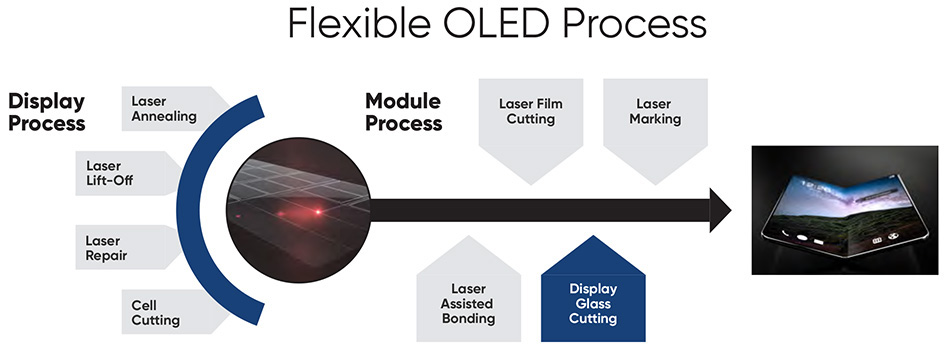
One of the final production steps for phones and other mobile devices is placing a coverglass over the display, and also mounting protective windows over the camera lenses. For cost-effective production, these components must all be rapidly cut out from larger pieces to final shape with high mechanical precision.
Read the other blogs in this series on lasers in display fabrication |
|||
The surface roughness and residual stress created by this cutting are important because these affect the break resistance of the final part. Debris creation is also a factor since this may require extra cleaning steps to remove. Another imperative is to avoid damage to any coatings or other functional layers on the components during cutting.
Ultrashort Pulse (USP) laser cutting based on filamentation satisfies all these requirements. But the specific way that this is implemented depends on the process specifics and production economics. Key factors include the window material and thickness, cut length and shape, and the necessary throughput speed.
USP lasers have glass cutting covered
Most of the coverglass used in mobile devices today is chemically strengthened alkali-aluminosilicate (like Gorilla® Glass), thermally strengthened soda lime glass, or materials similar to these. Coverglass thickness for flexible displays is typically about 0.5 mm. It can be as thin as 30 µm for foldable displays.
To decide how to apply filamentation cutting on parts like these, the first consideration is laser repetition rate. This is because in filamentation cutting, the laser beam is moved over the part surface and each pulse (or pulse burst) produces a single filament – a hole that goes all the way through the glass. The goal is to make a series of essentially evenly spaced perforations in the glass (typically spaced about 50 µm apart). Subsequently, stress is induced at the perforation to transform it into a continuous crack. This will allow the part to be separated. Often, this process uses a Coherent CO2 laser to generate very localized heat stress along the perforation line.
The higher the laser repetition rate, the faster the beam can be moved over the glass surface to make holes at a specific spacing. So, for cutting large parts like display coverglass, the Coherent HyperRapid NXT (repetition rate up to 400 kHz) can work over three times faster than the Rapid LX (repetition rate up to 90 kHz), even though both of these lasers deliver the same energy per pulse. But the HyperRapid NXT is larger and more expensive than the Rapid LX.
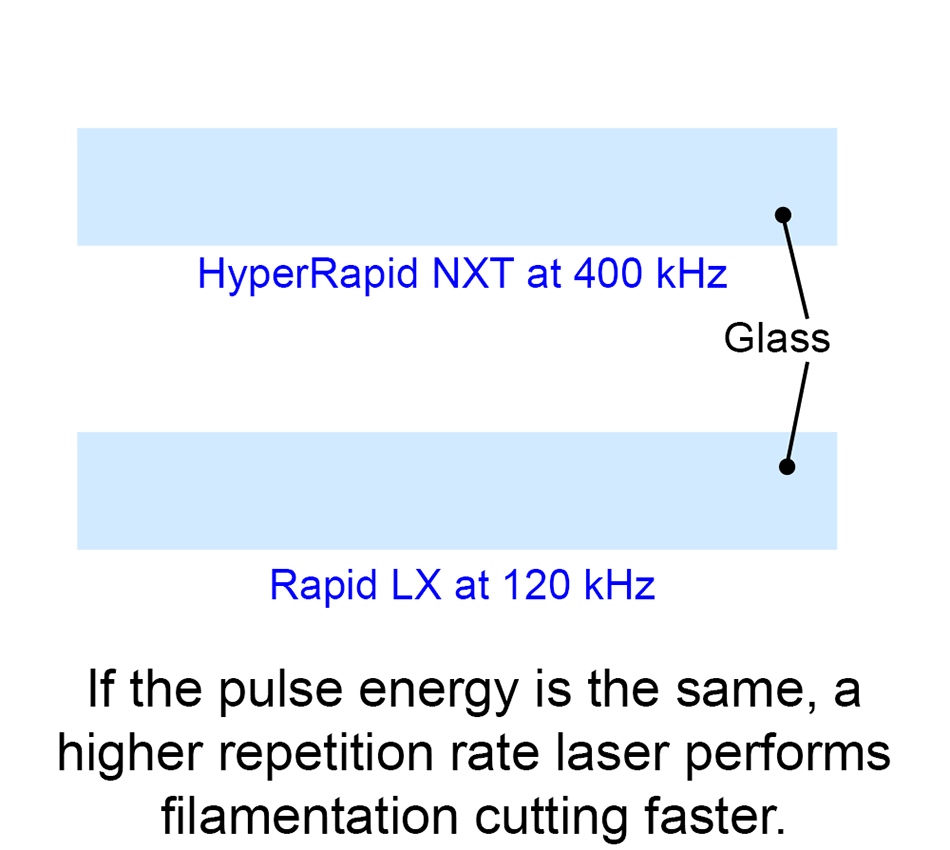
So, if throughput speed is critical, the HyperRapid NXT is the first choice. But there are situations in which the throughput or overall process is limited by stage motion or beam steering. If these make it so that the laser can’t operate at its highest repetition rate, then the HyperRapid NXT can’t deliver its full benefits. In these instances, it’s possible that the Rapid LX can exactly the same quality cuts and throughput.
Sapphire cutting
Small round sapphire windows are used to cover the camera lenses in most cell phones. Sapphire is extremely hard and scratch resistant. It’s also expensive, which is why it’s used so sparingly.
The filamentation process cuts sapphire with no difficulty. But, because the pieces are physically small and round, the Rapid LX – with its lower repetition rate and lower cost – is usually the best choice. To understand why, you need to know something else about how filamentation is actually performed.
For this technique to work, the laser beam must enter essentially perpendicular to the part surface. Because of this, the focusing optics are typically fixed and the workpiece moved with stages. Scanners aren’t used because they would cause the beam to come in at an angle to the surface at some parts of the cut.
Quickly cutting the small circular sapphire windows means that these motors must continually accelerate and decelerate. And the smaller the part, the higher this acceleration gets. Of course, there’s a limit to the acceleration these motors can produce. Generally, they can’t go fast enough to keep up with a laser operating at 400 kHz and produce the desired filament spacing. This means the laser would have to operated at a lower repetition rate. This makes the Rapid LX the optimum choice.
Coherent is focused on cut quality
The beam delivery optics used for filamentation cutting are just as important as the laser source itself. Coherent has developed our own series of focusing optics that are each designed to produce optimum results in different applications.
For example, our “standard” SmartCleave Advanced Classic focusing optics are designed to work with substrates of up to 1.8 mm in thickness. This covers most display applications. But we also have a lens (SmartCleave Advanced LongFi) in which the beam profile has been optimized specifically to enable cutting parts of up to 3 mm in thickness. This will produce different cutting characteristics that are dependent on exact part thickness, so it’s important to understand the tradeoffs involved.
At the other end of the spectrum, we have optics especially for cutting the ultrathin (< 1 mm) glass that is essential to foldable displays. The SmartCleave Advanced Low Damage optics are designed to reduce peak power density within the focus region. This sacrifices the ability to make longer filaments but produces a smaller heat-affected zone and a smoother texture on the entrance side. Minimizing this surface roughness is particularly important for ultrathin glass because it directly impacts bend strength.
It's easy to look at a USP laser manufacturer’s datasheet and simply think that higher power will give faster or better results. But that’s not the case at all. And, even once the best laser is chosen, it must still be focused onto the part in just the right way. Rely on a vendor with years of experience in laser glass cutting and hundreds of actual installations to get the recipe for glass cutting right.
Discover all the Coherent USP lasers.