SmartCleave Cutting: A Clear Winner for Precision Glass Manufacturing
A highly sophisticated glass cutting technique based on ultrashort pulse lasers delivers the results needed for the most demanding applications.
February 10, 2022 by Coherent
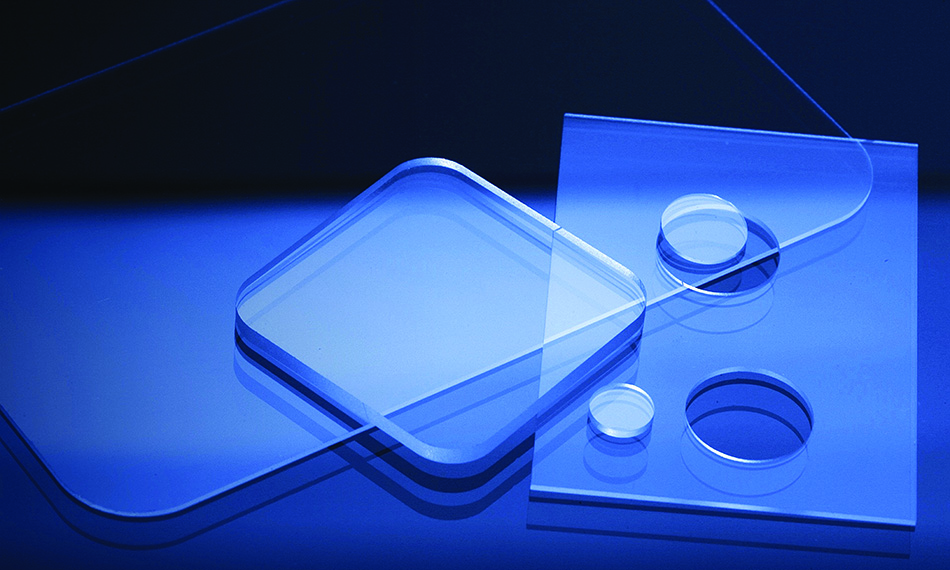
Glass is quite literally all around us, and has been for well over 5,000 years. So, it’s easy to overlook the fact that it’s a unique material, with a very useful combination of physical properties. The most obvious of these, and one of the most valuable, is that it’s transparent.
But, glass is also mechanically strong and relatively scratch resistant. Plus, it doesn’t react with most chemicals – even many strong acids. And, neither liquids nor gases can pass through it. Glass is even biocompatible, which means that sterilized glass can be implanted safely into the human body.
For these reasons, and more, the use of glass has expanded far beyond the architectural and automobile windows we’re all familiar with into increasingly sophisticated products. It’s already widely used in medical devices, life sciences instrumentation, semiconductor tools, and consumer electronics. In the latter, it’s used for display screens in phones, laptops, tablets, and televisions.
The old ways can’t cut it
In many of these high technology applications, there is an ongoing push to make products ever more sophisticated, but also physically smaller and lighter. In terms of the use of glass, this usually translates into a need for thinner pieces, often with curved edges or cutouts. An example of this might be a cellphone display screen that has a cutout for the Home Button.
But, this demand creates a challenge. That’s because traditional glass cutting methods — like good, old-fashioned mechanical cutting with a carbide tool, or waterjet cutting — can’t easily work with really thin pieces of glass, or make these kinds of features – especially tight curves. At least not within the required cost and production time constraints. Even the usual laser glass cutting methods can’t do it cost-effectively at marketing enabling speeds.
Also, these older glass cutting methods produce very small cracks and residual stress in the glass. This makes the glass very much more vulnerable to breakage during subsequent handling and use. Because, oddly, it turns out that when glass breaks, the crack almost always starts at the outer edge, even if the force is applied to it in the center.
Most glass cutting processes also usually create small chips and debris, and a cut edge that isn’t perfectly necessarily perpendicular to the glass surface. Various additional steps, like grinding or polishing the cut surface, may be required because of all this.
For the manufacturer, any additional processing steps required after cutting represent increased production time and cost. Plus, they may have negative environmental impacts if they generate debris that’s hard to dispose of, or require lots of water for cleaning.
SmartCleave speeds precision laser glass cutting
A new cutting method called “filamentation” was developed specifically to meet the growing need for precision, stress-free, debris-free, freeform cutting of thin glass. Filamentation requires an ultrashort pulse (USP) laser because only these can generate the very high peak power this technique relies on.
In filamentation, the USP laser is focused into glass to create a line of microscopic voids (or filaments) which can go several millimeters deep. To make a continuous cut, the laser beam is moved relative to the glass in the desired pattern, and a series of very closely spaced filaments are produced. Depending upon the glass thickness and type, the part will either directly separate along the cut, or can be separated by heating it.
Filamentation enables high-speed cutting of curves and insets (without taper) into glass ranging from 0.05 mm to 10 mm in thickness. And, it even works chemically strengthened glass, which is used extensively in touchscreen displays.
Coherent has developed our own form of filamentation cutting, called SmartCleave. This method specifically utilizes the unique characteristics of our HyperRapid series USP lasers. One of these is the so-called “burst mode” operation, where the laser delivers a rapid-fire series of pulses. This ends up producing a gentler heating profile than a string of pulses having the same total energy, but delivered over a longer time period.
The benefits of SmartCleave are an increase in cutting speed by as much as a factor of two. It also produces holes which are smoother and straighter than other filamentation cutting methods. Additionally, SmartCleave leaves a cut edge which is free of microcracks, chips, and debris. All this improves production throughput and reduces costs by eliminating post-processing steps. And, it yields a mechanically stronger finished glass part.
The use of glass in high technology products is clearly going to continue, because there’s nothing else quite like it. And, SmartCleave cutting enables the production of glass components at the level of precision that these demanding new uses require. Learn more about SmartCleave for cutting glass, sapphire, ceramics, and composite materials.
Related Resources