Lasers in Display Fabrication: Laser Lift-Off
Coherent UVblade systems perform this critical step in the production of the thin, flexible AMOLED displays found in many smartphones, tablets, and other mobile devices.
October 4, 2022 by Coherent
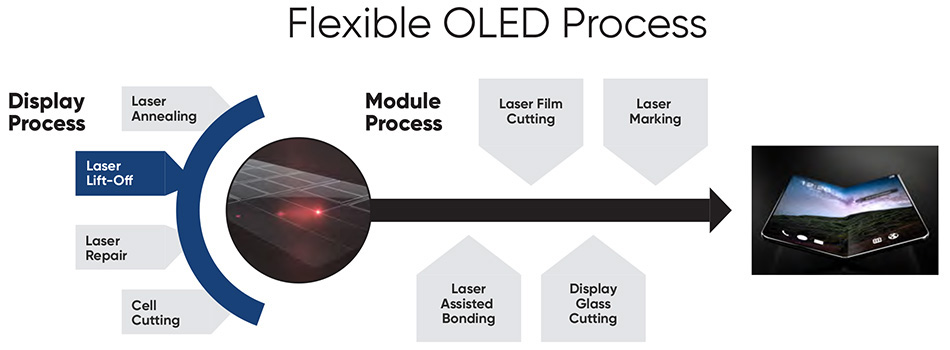
How do lasers help make today’s screens so amazingly thin and light? Because anyone old enough to remember the first TVs appreciates just how far display technology has come from those incredibly bulky picture tubes.
The earliest flat-panel TVs and monitors were all based on liquid crystal displays (LCDs). This technology represented a huge leap forward over the old TV tubes.
But the internal construction of LCDs is actually somewhat complex. The LCD panel itself doesn’t emit light, so they need a backlight, plus a polarizer, and a layer of color filters to make the red, green, and blue pixels. All this limits the ability to miniaturize these devices, and especially to make them more flexible.
Read the other blogs in this series on lasers in display fabrication |
|||
Don’t panic, it’s organic
To get even thinner and more flexible displays, manufacturers developed organic light emitting diode (OLED) technology. Each pixel in an AMOLED display contains three light emitters (red, green, and blue) so it doesn’t need a backlight. As a result, an AMOLED display can be made just a fraction of a millimeter thick. And this is the total thickness, even when you include other layers to add touchscreen functionality and contrast enhancement. Because AMOLED displays can be made so thin, it’s even possible for them to be made flexible or foldable.
But making such thin displays poses a problem for manufacturers. Keep in mind that numerous displays are made at once on a single substrate that’s about 1.5 m x 1.9 m. It would be impractical to process something that size that’s just a fraction of a millimeter thick. Something that large and thin is tricky to handle. Also, it’s critical that the display substrate be very flat – and stay flat – throughout the manufacturing process. Again, that’s hard to do with something large and very thin.
The secret to making thinner displays
To solve this problem, displays are constructed on a thicker and more rigid “mother glass.” The first production step is to bond a thin polymer sheet to this mother glass. This polymer layer will become the bottom of the finished display. Next, silicon is deposited onto this polymer substrate, followed by Excimer Laser Annealing (ELA), then creation of the electronic circuitry, and finally placement of the other display layers.
Near the very end of this process, the display is separated from the mother glass. That’s how you wind up with a razor-thin display.
The displays are nearly finished when they’re separated from the mother glass. At this point, most of the cost has already been built into them. So, scrapping parts at this stage is expensive. This means the separation process must be both precise and gentle.
There are two things that must be avoided in particular. First, the separation process can’t impart any significant mechanical force or stress because the displays are too delicate. Second, the process can’t put much heat into the display since it might damage the electronics.
Excimer lasers bring OLED production into line
The separation process currently in use by major AMOLED display manufacturers is called laser lift-off (LLO). To start LLO, the entire panel is flipped over so that the mother glass is now on top. Then, the light from a high pulse energy, ultraviolet (UV) excimer laser is formed into a long, thin line beam. This line beam is focused through the glass right at the interface between the mother glass and the thin polymer substrate containing the display circuitry.
The beam is rapidly scanned across the entire area of the mother glass. The ultraviolet light passes through the glass but is strongly absorbed by the adhesive joining the mother glass to the polymer, and polymer itself. This heats it all enough to virtually instantly vaporize the adhesive and release the display from the mother glass. But – and this is the really big point – the laser light hardly penetrates at all into the polymer display substrate itself, so it doesn’t cause much heating within the device. The display circuitry is unaffected by the LLO process.
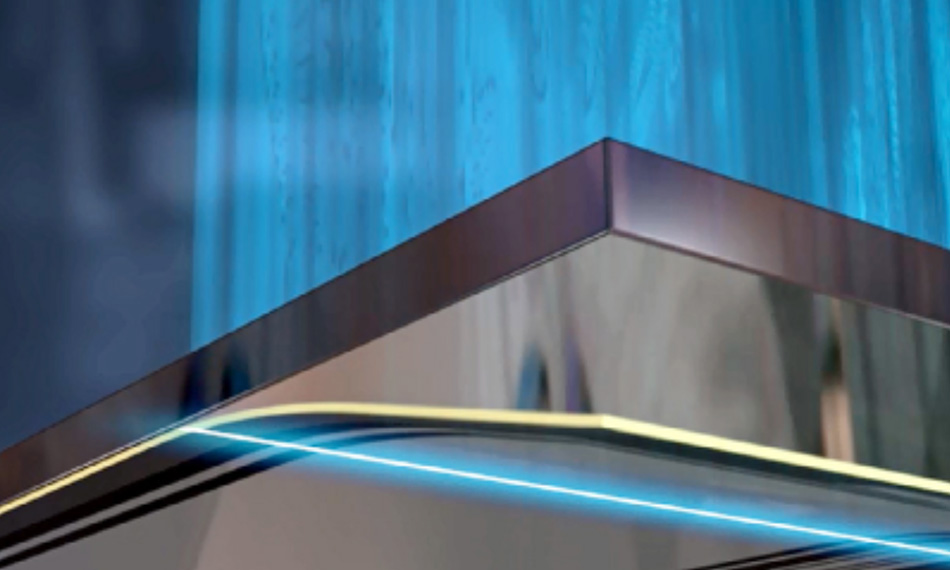
Rapidly scanning the excimer laser line beam enables the delicate display circuitry to be gently separated from the mother glass panel on which it was produced.
Just as with ELA, the excimer laser provides the ideal source for LLO. There are two main reasons for this. First, the excimer laser produces higher pulse energy output in the ultraviolet than available from any other laser type. This UV light is strongly absorbed by the adhesive, and the high laser power produces rapid decomposition of the adhesive. This is what enables LLO to move at the speed required for display production. Speed is important because the major display manufacturers make over one million phones every single day!
Also, the excimer laser beam lends itself to being formed into the long, thin line beam. Plus, it can be converted to have a uniform (flat-top) beam profile, rather than the Gaussian intensity distribution that most lasers produce. The flat-top beam profile allows a much larger process window than a Gaussian beam could provide. It makes production-line LLO less susceptible to slight changes in the exact focus position of the laser, small variations in mother glass dimensions, and is tolerant of some warping of the mother glass.
Coherent LLO systems are used by major display manufacturers worldwide. These combine a highly stable, excimer laser with our unique UVblade optical system which produces the final line beam. We can support all current display sizes, from a single cell to a large substrate. And Coherent UVblade optics are scalable to meet the production requirements of the next generation of both flexible and foldable displays.
Learn more about Coherent Excimer UV Laser Systems.