ホワイトペーパー
組込み型プロセス制御によるレーザ加工の生産性向上
多くの場合、レーザベースの生産加工方法は、スピード、品質、コスト面で他の製造技術に比べて優れています。 しかし、レーザ加工の効果が十分に発揮されるには、加工前から加工後までの工程を、注意深く監視および制御しなければなりません。 この文書では、この種類のプロセス制御を実施するために利用可能な方法と、具体的なツールについて概説しています。
どのような製造プロセスでもばらつきは生まれ、満足のいく結果が得られないことがあります。 レーザ加工では、光学系やビーム伝送系のアライメント、破損、汚れが理由で、または部品ハンドリングや位置合わせのエラーなどが原因となり、レーザ光源そのものに問題が発生することがあります。 また、部品の材料や寸法にばらつきがある場合や、周囲の動作環境が大きく変化した場合にも、レーザ加工の結果に違いが発生することがあります。 そしてもちろん、オペレーターがミスをすることもあります。
プロセス制御の目標は、このような問題をできるだけ早く発見し、可能であれば修正することです。 発見と修正は、理想を言えば不良品が作られる前に、少なくとも不良品が大量に生産される前に行われるべきです。 そして、規格外の製品がお客様に出荷される前に、必ず実施されなければなりません。
当然、プロセス制御は品質向上のために行うものですが、スクラップや再作業を減らし、材料の無駄を最小限に抑えることでコスト削減にもつながります。 そして、あまり目立ちませんが、効果的なプロセス制御によるコスト削減の方法は他にもあります。
その1つは、プロセス制御装置組込みで収集したデータを、機械の稼働率の分析に役立てることです。 この情報は、生産全体の効率向上やレーザシステム自体の早期投資回収のために活用できます。 また、不良品がエンドユーザーに渡った場合の賠償責任や、リコール費用などのコストを削減することも可能です。
そして、プロセス制御とそこから得られるデータは、現在多くの産業で必要とされるコンプライアンスに対応するためにも不可欠なものです。 生産バッチや部品ごとにレーザおよびその他のシステムパラメータの記録をすることは、コンプライアンス基準を満たすためにますます必要とされています。
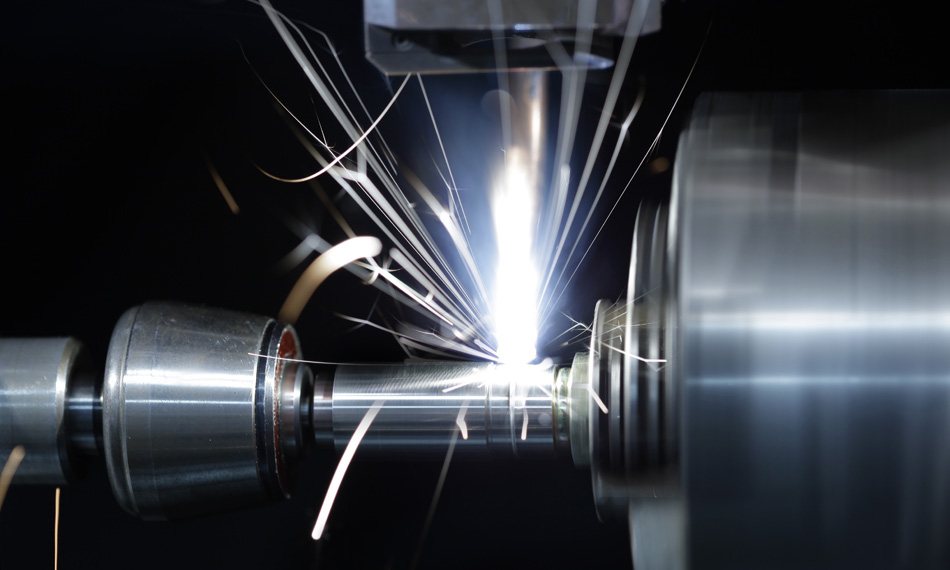
プロセス制御導入のタイミング
プロセス制御は、レーザ加工の各段階で検査やデータ収集を行い、総合的に実施されます。 制御は次の4つの段階に大きく分けられます。
- プリプロセスでの制御
- インプロセスでの監視と制御
- ポストプロセスでの制御
- 定期的なシステム制御
これらの各段階では、プロセス制御装置組込みや導入の詳細に合わせた、さまざまな選択肢が用意されているのが一般的です。 ユーザーは、どの評価方法が必要であるか、あるいは有用であるか、また、どの程度まで品質やスループットに影響を与えるかを決定しなければなりません。 もちろん、それぞれにかかるコストとの天秤にかける必要がありますが、 各段階でどのようなツールがあり、どのような効果が期待できるかを個別に検証してみる価値はあります。
プリプロセスでの制御
木材を扱う大工の間では、「二度測って、一度で切る」という古い格言があります。この心得は、「あとで修正するよりも、間違いが起きないようにする方が良い」という考えを表しています。 そして、生産の現場では、問題の発見は早ければ早いほど良いのです。 そのため、プリプロセスでの測定は、ミスやスクラップ、再作業を減らすために特に効果的な方法です。
レーザ加工でのプリプロセス測定は、まず正しい部品が装着されているかどうかを確認するために行われるのが一般的です。 これは、部品のサイズや形状を調べたり、部品に付けられたバーコードなどや他の識別マークを読み取ったりして行われます。 また、部品の寸法や向きを測定して正確な加工位置を特定することも可能です。 レーザマーキングの場合、この段階で他の製造システムから可変入力データ(シリアル番号、ロット番号、その他の識別情報)を受け取ることもよくあることです。
この種類の測定に最もよく使われる装置組込みは、カメラによるマシンベースのビジョンとパターン認識システムです。 専用の照明アクセサリが付属している場合もあります。
通常、ビジョンシステムは部品があることを確認し、その正確な位置を決定するためにエッジ検出を使用します。 部品に関する特定の特徴や構造を見分けることも可能です。 溶接加工では、溶接の隙間を検出して測定し、部品の適合性を判断することができます。 また、レーザが加工面に正しく集光されるように、集光位置の確認が行われることもあります。
平面だけでなく立体的な形状を持つ部品を加工する場合、ラインスキャンカメラとX軸、Z軸のモーションで形状を検出することもできます。 レーザマーキングが最終的な外面形状に正しく表示されるように「プリディストーション」できるシステムも登場しており、特にマーキング作業では役立つものです。 しかし、この種類のシステムをうまく運用するには、マーキングする部品の形状と向きの正確な測定が必要となります。
インプロセスでの監視と制御
インプロセスでの監視は多くの作業で行われていますが、おそらく、溶接用途で最も重要となるものです。 これは、溶接品質がレーザ動作パラメータに非常に敏感であるためです。 さらに、溶接に隙間や脆弱な箇所があることは、通常、部品に全面的な不具合があるということになるので、ミスは許されません。
溶接の際には測定が必要な項目がいくつかあり、 出力パワーなどのレーザ動作パラメータ、溶接の隙間に対するビーム位置、適切なフォーカスといった項目が含まれます。 金属溶接では、溶け込み深さ、スパッタ、空隙など、さまざまな溶接パラメータを検出することも可能です。 特にポリマー溶接の場合は、溶接部全体の温度と上部のコラプス(つぶれ)高さを測定するのが一般的です。
これらの測定を行うために、かなりの数の装置組込みが開発されています。 最も広く利用されていると思われる技術として、高速度カメラと光コンピュータトモグラフィ(OCT)測定があります。 また、後方反射レーザ光や溶接加工で発生する光の測定も、非常に有効なプローブとなります。 加えて、音響の監視は材料内の溶接プロセスの状態を高感度で検出することができますし、 パイロメーターによるレーザ出力制御やサーマルイメージングも頻繁に利用されています。
ポストプロセスでの制御
通常、ポストプロセスでの制御操作の主な目的は2つです。 一つめは、加工方法が正しく実施され、部品が仕様の範囲内であることを確認することです。 二つめは、ISOなどの規格に準拠した結果の記録です。 記録には、レーザやその他のシステムパラメータ、完成部品の寸法が含まれることがあります。
金属溶接の場合、特に亀裂の発生を検出するために、加工時と同様の技術を冷却時に使用する場合があります。 この場合もまた、サーモグラフィや音響探知などの手段が含まれることがあります。 そして、溶接の全体的な形状とアライメントの評価のため、ビジョンで確認される可能性もあります。 人工知能(AI)をはじめとする機械学習は、部品の品質だけでなく外観までもを評価するビジョンシステムで、採用が進んでいます。 このため、より完全な自動化が可能となり、オペレーターへの依存や主観がより少ない加工を行うことができるようになっています。
定期的なシステム制御
定期的なシステム制御は、システムがアクティブに使用されている間に行われる操作のことです。 特定の操作とは無関係にシステムの健全性を測定し、必要な調整を行うために実施されます。 また、この操作では、設備総合効率(OEE)に関わるデータの収集ができます。
レーザシステムの場合、定期的に評価しなければならないビームパラメータがいくつかあります。 出力、ビーム品質(M²およびホットスポットや小規模な強度変化の特定)、ビームアライメント、焦点位置などがそのようなパラメータに含まれます。 この時点で、光学系のアライメントやビーム経路内のオプティクスの汚れも確認できます。 このような測定は、システムの適切な運用のために大切であるだけでなく、システム間のばらつきを最小限に抑える(つまり、生産の安定性を高める)ためにも重要です。
統合ソフトウェアでプロセス制御が容易に
これまで、ユーザーはたびたび、サードパーティ製のプロセス制御装置組込みをレーザシステムに追加してきました。 そのため、これらのアクセサリとの光学的、機械的、電子的、ソフトウェア的な統合が複雑化していました。 また、システムがうまく機能しない場合、サプライヤー間での「責任のなすりあい」がしばしば起こりました。 しかし今は、レーザシステムのプロバイダーがこれらの機能をすべて統合し、単一のターンキーシステムとして提供することが一般的になってきています。
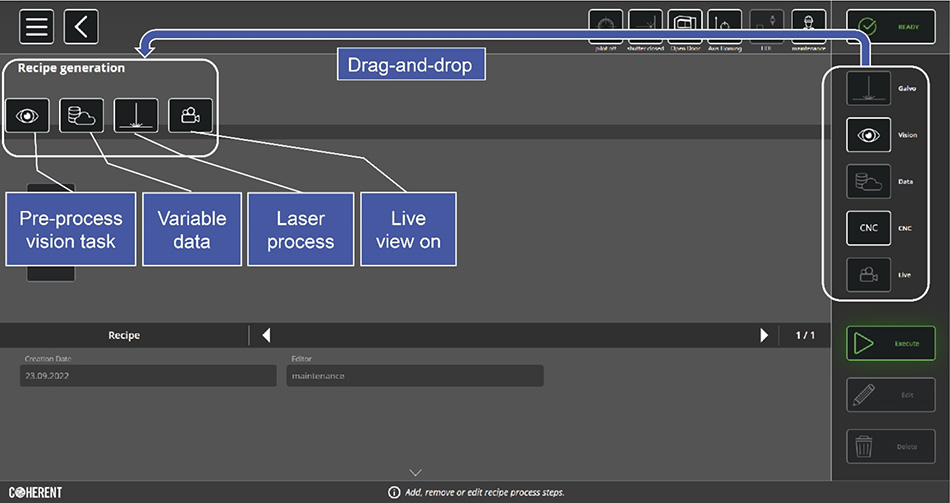
図1:Coherent Laser FrameWorkでは、検査、プロセス制御、加工の各種作業をタイムライン上にドラッグすることでジョブを作成します。
たとえば、Coherentは、自社のレーザ溶接機、切断機、マーキング機の多くに、前述のすべての機能を備えたプロセス制御装置組込みを用意しています。 Coherent Laser FrameWorkは、これらのすべてのツールを統合し、使用を簡素化する統一されたソフトウェアプラットフォームとマシンインターフェースを提供します。 ビジョンを使ってのプリプロセス検査、溶接のインプロセス監視、ポストプロセスのビーム診断など、さまざまなプロセス制御タスクが、レーザパラメータおよび部品ハンドリング操作とともにジョブセットアップ時に指定可能です。 図は、Laser FrameWorkの簡単なドラッグ・アンド・ドロップ機能を使って、加工方法レシピにタスクを追加している様子を示しています。
次の図は、具体的なタスク(ここでは金属溶接加工)にこの機能がどのように応用できるかを示したものです。 まず、PartVision(カメラ式アクセサリ)が部品のバーコードを読み取って正しい部品であることを確認し、適切な加工方法レシピを機械に読み込みます。 次に、ビジョンシステムで溶接を行う部品の特徴を識別します。
溶接加工自体は、SmartSense+を使って監視します。 このシステムは、光学検出器と音響センサーを内蔵し、後方反射レーザ光に加え、加工で放出される光をキャプチャします。 溶接プロセスの状態を継続的に評価し、問題や不具合を即座に発見することができるシステムです。
PartVisionはポストプロセスの部品検査に使用されます。 その後、システムはすべての加工パラメータとその他の関連情報を保存します。
最後に、ジョブの合間にBeamInspectを使用して、レーザビームの状態や調子を評価します。 BeamInspectは精密な自動測定を行い、加工結果に影響を及ぼす、すべてのビームパラメータを計算する、統合型レーザビーム診断ツールです。
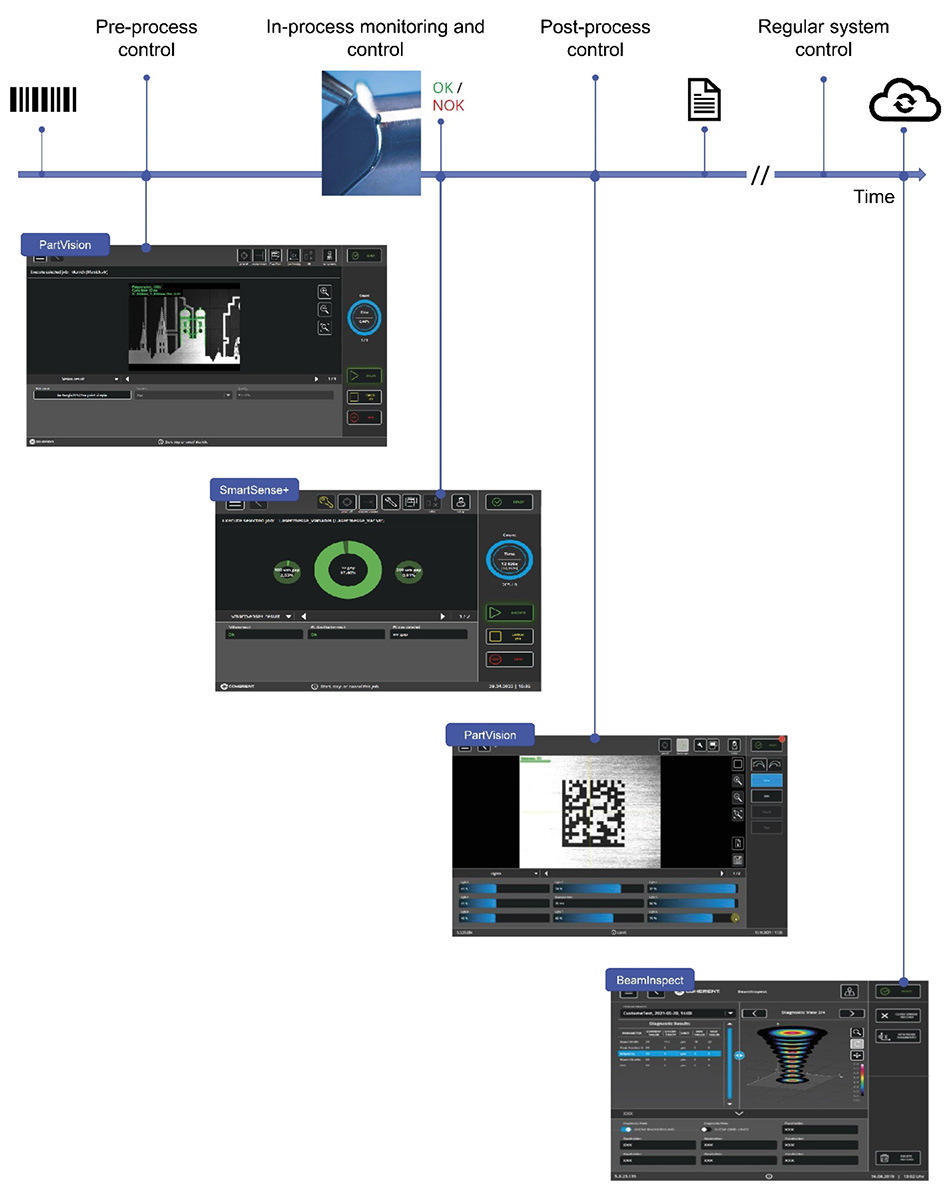
図2:各段階での検査、プロセス制御タスクを組込んだLaser FrameWorkを使用して指定した、レーザ溶接タスクの例です。
まとめ
高速化、高精度化、歩留まり向上というレーザ加工への継続的な需要は、製造の各段階でのプロセス制御を必要とします。 しかし、高度に複雑化する可能性があり、メーカーがうまく導入することが難しいのです。 Laser FrameWorkのような統一されたソフトウェアインターフェースをもつ統合システムなら、簡素化が可能です。 さらに、セットアップ、トレーニング、メンテナンスが単一ソースで完結するため、シンプルで安心な使い勝手を提供します。 これらはすべて、レーザ加工のメリットをより多くのユーザーにもたらすものです。