白皮书
使用嵌入式工艺控制提高激光系统生产效率
与其他制造技术相比,在许多情况下,基于激光的生产工艺具有速度、质量和成本优势。 但是,要充分发挥激光工艺的优势,需要在加工之前、期间和之后进行仔细的监测和控制。 本文档回顾了一些可用于实施此类工艺控制的方法和特定工具。
任何类型的制造工艺都会发生变化,因此有时会产生不令人满意的结果。 对于激光工艺,由于光学器件和光束传输系统的对准、损坏或污染问题,以及零件处理和定位错误等原因,激光源本身可能会出现问题。 当零件材料成分或尺寸不一致,或者周围工作环境发生重大变化时,激光加工结果也会有所不同。 当然,操作员错误总是会出现的。
工艺控制的目标是尽早识别并尽可能纠正任何此类问题。 理想情况下,工艺控制应该在制造出任何不良零件之前进行,或者至少在生产出许多不良零件之前进行。 并且,应该始终在不合规格的产品运送给客户之前进行工艺控制。
显然,工艺控制是用于提高质量,但它也可以减少报废和返工,并最大限度减少材料浪费,从而节省资金。 此外,还有其他一些不太明显的方法,可以通过有效的工艺控制来降低成本。
其中一个方法是使用工艺控制仪器收集的数据来帮助分析机器利用率。 然后此信息可以用来提高整体生产效率,并为激光系统本身更快实现投资回报。 这个方法还有一个好处,那就是如果不良产品到达最终用户手中,可以降低与可能的法律责任追究或召回成本相关的成本。
最后,工艺控制以及从中获得的数据对于满足目前许多行业中的合规性要求至关重要。 为了满足合规性标准,越来越需要记录生产批次甚至每个零件的激光器和其他系统参数。
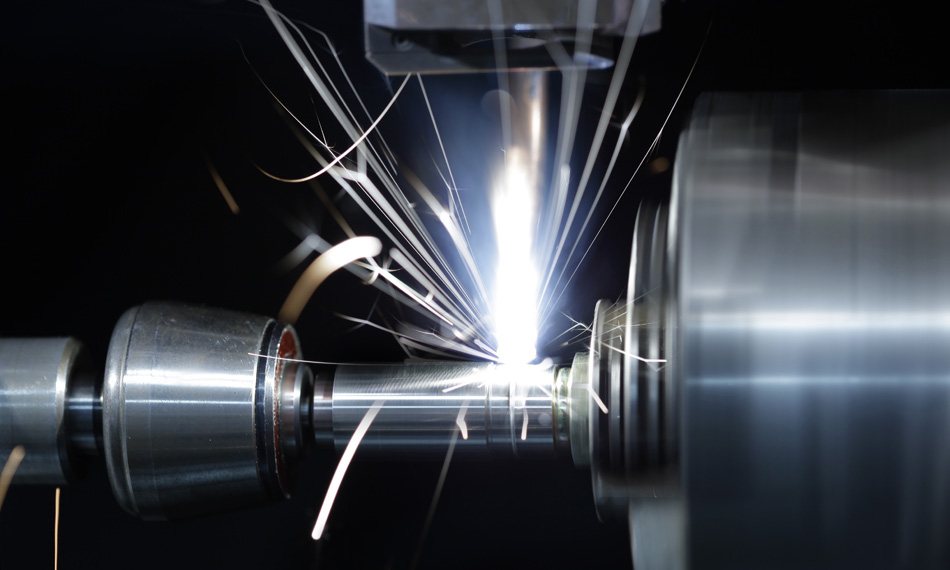
何时实施工艺控制
全面实施的工艺控制方案涉及激光工艺每个阶段的监测和数据收集。 这可以分为四个大类:
- 加工前控制
- 加工中监测和控制
- 加工后控制
- 周期性系统控制
在以上每个阶段中,工艺控制仪器和实施细节方面通常都有多种选项。 用户必须决定哪些测量是必要的或有用的,以及它们将在多大程度上影响质量和产量。 当然,这必须权衡每一项的成本。 有必要单独检查上述各个阶段,以查看可用的工具以及它们可能带来的好处。
加工前控制
木匠们之中流传着一句老话:“量两次再动手。”这个规矩表达的意思就是,预防错误发生比修复错误好。 在生产中越早发现问题越好。 因此,进行加工前测量是一种特别有效的方法,可以减少错误、废品和返工。
对于激光工艺,通常首先使用加工前测量来验证是否已加载正确的零件。 这可以通过检查零件尺寸/形状,或通过读取零件上的条形码或其他识别标记来完成。 此外,还可以测量零件尺寸和方向,并确定加工的精确位置。 在激光打标流程中,系统通常在此阶段从其他制造系统接收可变输入数据(序列号、批号和其他识别信息)。
用于此类测量的最常见仪器是基于摄像头的视觉和图案识别系统。 此系统可能配有专门的照明配件。
通常,视觉系统将使用边缘检测来验证零件是否存在并确定其精确位置。 它还可以识别零件上的某些特定特征或结构。 对于焊接工艺,可以检测和测量焊缝间隙以确定零件配合。 还可以执行焦点位置检查,以确保激光将正确地聚焦在工作表面上。
要加工具有 3D 几何形状(不是简单平面)的零件,可以使用能够在 x 轴和 z 轴上运动的线扫描摄像机来完成形状检测。 这对于打标操作特别有用,因为一些系统现在可以“预扭曲”激光标记,使其在最终轮廓表面上看起来正确。 但此类系统要想成功运行,就需要准确测量待打标零件的形状和方向。
加工中监测和控制
加工中监控可以用于许多任务,但可能对焊接应用最为关键。 这是因为焊接质量对激光操作参数非常敏感。 此外,焊缝中的间隙或薄弱点通常表示零件完全报废,因此几乎没有出错的余地。
焊接过程中需要测量几个方面。 其中包括激光操作参数(如输出功率),以及相对于焊缝间隙和适当焦点的光束位置。 在金属焊接中,还可以检测各种焊接参数,如熔深、飞溅和空隙。 特别是对于聚合物焊接,通常测量整个焊缝沿线的温度和顶部的塌陷高度。
相当多的仪器已经开发出来,用于执行所有这些测量。 高速摄像机和光学计算机断层扫描 (OCT) 测量可能是使用最广泛的技术。 测量背反射激光和焊接工艺本身发出的光也是非常有用的探测方法。 此外,声学监测可以灵敏地检测材料内焊接过程的状态。 基于高温计的激光功率控制和热成像也经常使用。
加工后控制
加工后控制操作通常有两个主要目标。 首先是验证工艺是否得到了正确执行,以及零件是否符合规格。 其次是根据 ISO 和其他标准记录结果。 这可能涉及记录激光和其他系统参数,以及成品零件的测量值。
金属焊接的冷却阶段,可以采用与加工过程中使用的同一系列技术,尤其是检测是否形成任何裂纹。 同样,这可能包括热成像和声学检测等手段。 视觉检测可用于评估整体焊缝几何形状和对准。 人工智能 (AI) 和其他机器学习越来越多地与视觉系统配合使用,以评估零件质量甚至外观美观度。 这样工艺就可以进一步实现完全自动化,并减少对操作员的依赖性和经验影响。
周期性系统控制
周期性系统控制是指在系统使用期间执行的操作。 这些操作旨在衡量系统的健康状况,而无需依靠特定操作,并进行必要的调整。 这也可以说成是用于收集整体设备效率 (OEE) 相关数据的点。
对于激光系统,应定期评估几个与光束相关的参数。 这些包括功率、光束质量(M² 以及任何热点或小规模强度变化的识别)、光束对准和焦点位置。 此时还可以识别光束路径内任何光学器件的光学校准和污染。 这些类型的测量对于系统的正常运行以及最大限度减小系统间差异(从而提高生产一致性)非常重要。
集成软件简化工艺控制
过去,用户经常在他们的激光系统中添加第三方工艺控制仪器。 这会导致这些配件的光学、机械、电子和软件集成变得复杂。 当系统无法正常工作时,这通常会导致供应商之间“相互指责”。 但现在激光系统供应商越来越普遍地集成所有这些功能,并将其作为单个完整系统提供。
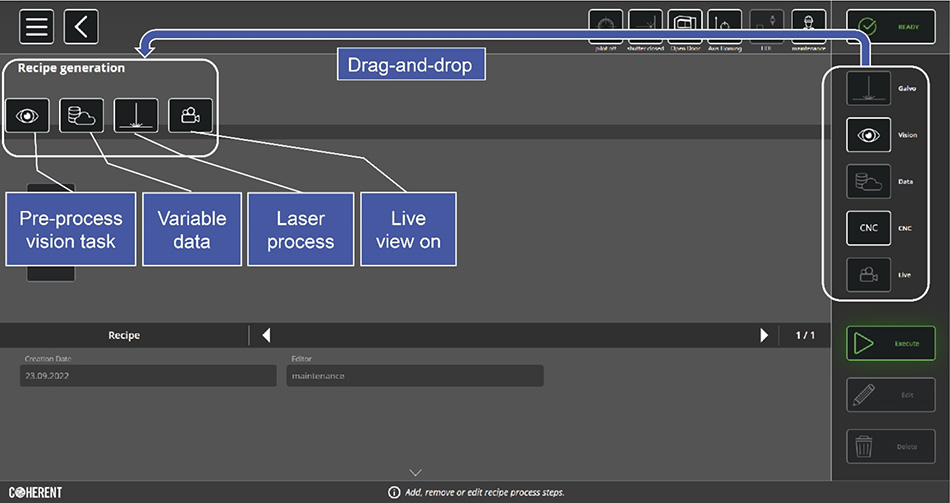
图 1:在 Coherent Laser FrameWork 中,可以通过将各种检查、工艺控制和处理任务拖到时间线上来创建作业。
例如,Coherent 为其许多激光焊接、切割和打标机器提供了可用于刚刚描述的所有功能的工艺控制仪器。 Coherent Laser FrameWork 提供了一个统一的软件平台和机器界面,集成并简化了所有这些工具的使用。 各种工艺控制任务,如使用视觉的加工前检查、焊接过程中的监控和加工后光束诊断,可以在作业设置期间与激光参数和零件处理操作一起指定。 该图显示了如何使用 Laser FrameWork 中的简单拖放功能将这些添加到工艺配方中。
下图显示了如何将此功能用于特定任务 – 在本示例中为金属焊接工艺。 首先,PartVision(一种基于摄像头的附件)读取零件条形码以验证是否提供了正确的零件,并将正确的工艺配方加载到机器中。 接下来,视觉系统识别要进行焊接的零件的特征。
焊接工艺本身使用 SmartSense+ 进行监控。 该系统结合了光学检测器和声学传感器,能够捕获后向反射的激光以及工艺本身发出的光。 它持续评估焊接工艺状态,并立即识别任何问题或缺陷。
PartVision 用于加工完成后的零件检查。 然后所有工艺参数和其他相关信息都由系统存储。
最后,不执行作业时,BeamInspect 用于评估激光束的状态和运行状况。 BeamInspect 是一种集成式激光束诊断工具,可对影响工艺结果的所有光束参数执行精确的自动测量和计算。
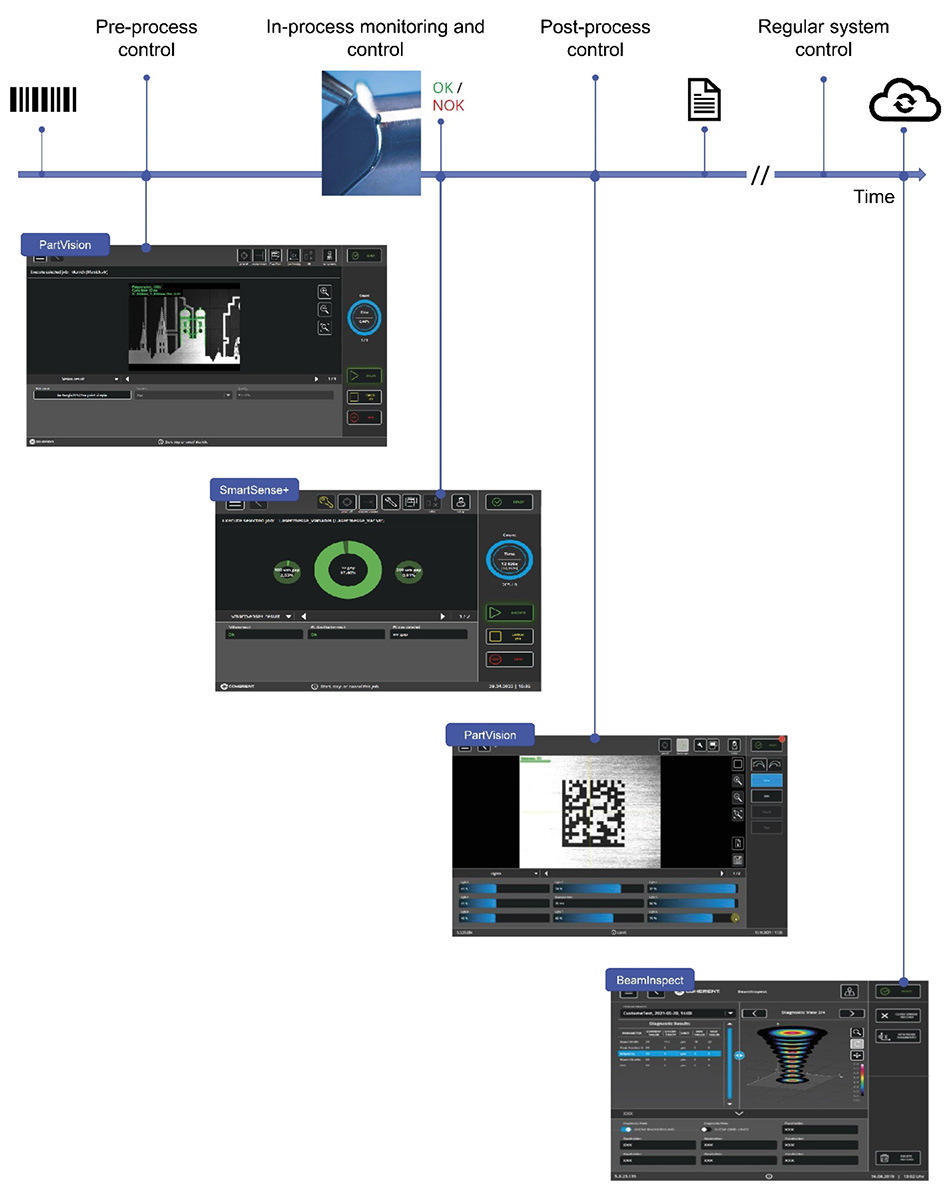
图 2:使用 Laser FrameWork 指定的激光焊接任务示例,该示例包括每个阶段的监测和工艺控制任务。
结论
为了满足对激光工艺更快工作速度、更高精度和更高产量的持续需求,必须要在生产的每个阶段进行工艺控制。 但这会造成复杂度显著提高,导致制造商难以成功实施。 具有统一软件界面的集成系统,如 Laser FrameWork,可以简化此项工作。 此外,它们为用户提供了简单和安心的方式,因为他们可以通过单个来源进行设置、培训和维护。 这样一来,就有更多的用户能够享受到激光加工的好处。