WHITEPAPER
VERBESSERN SIE DIE PRODUKTIVITÄT VON LASERSYSTEMEN MIT INTEGRIERTER PROZESSKONTROLLE
Laserbasierte Produktionsprozesse bieten in vielen Fällen Geschwindigkeits-, Qualitäts- und Kostenvorteile gegenüber anderen Fertigungstechnologien. Um die Vorteile eines Laserprozesses voll ausschöpfen zu können, bedarf es jedoch einer sorgfältigen Überwachung und Kontrolle – vor, während und nach der Durchführung des Prozesses. Dieses Dokument gibt einen Überblick über einige der Methoden und spezifischen Werkzeuge, die für die Implementierung dieser Art der Prozesskontrolle zur Verfügung stehen.
Jede Art von Herstellungsprozess unterliegt Schwankungen und führt daher manchmal zu unbefriedigenden Ergebnissen. Bei einem Laserprozess können Probleme mit der Laserquelle selbst, mit der Ausrichtung, Beschädigung oder Verschmutzung der Optik und des Strahlführungssystems, mit Fehlern bei der Handhabung und Positionierung der Teile und vielem mehr auftreten. Die Ergebnisse des Laserprozesses können auch variieren, wenn die Materialzusammensetzung oder die Abmessungen der Teile nicht übereinstimmen oder wenn sich die Betriebsumgebung erheblich ändert. Und natürlich gibt es immer Bedienungsfehler.
Das Ziel der Prozesskontrolle ist es, diese Probleme so früh wie möglich zu erkennen und möglicherweise zu korrigieren. Im Idealfall sollte dies geschehen, bevor schlechte Teile hergestellt werden, oder zumindest bevor sehr viele davon produziert werden. Und es sollte immer geschehen, bevor ein Produkt, das nicht der Spezifikation entspricht, an den Kunden ausgeliefert wird.
Natürlich dient die Prozesskontrolle der Qualitätsverbesserung, aber sie spart auch Geld, indem sie den Ausschuss und die Nacharbeit reduziert und die Materialverschwendung minimiert. Darüber hinaus gibt es noch andere, weniger offensichtliche Möglichkeiten, mit denen eine effektive Prozesskontrolle die Kosten senkt.
Eine davon ist die Verwendung von Daten, die von Sensoren zur Prozesskontrolle gesammelt werden, um die Maschinenauslastung zu analysieren. Diese Informationen können dann genutzt werden, um die Gesamteffizienz der Produktion zu verbessern und eine schnellere Kapitalrendite für das Lasersystem selbst zu erzielen. Ein weiterer Vorteil ist die Senkung der Kosten, die durch mögliche Haftungs- oder Rückrufkosten entstehen, wenn ein fehlerhaftes Produkt den Endverbraucher erreicht.
Schließlich können die Prozesskontrolle und die daraus abgeleiteten Daten für die Erfüllung der in vielen Branchen geltenden Compliance-Anforderungen von entscheidender Bedeutung sein. Die Einhaltung von Normen erfordert zunehmend die Aufzeichnung von Laser- und anderen Systemparametern für Produktionschargen oder sogar für jedes einzelne Teil.
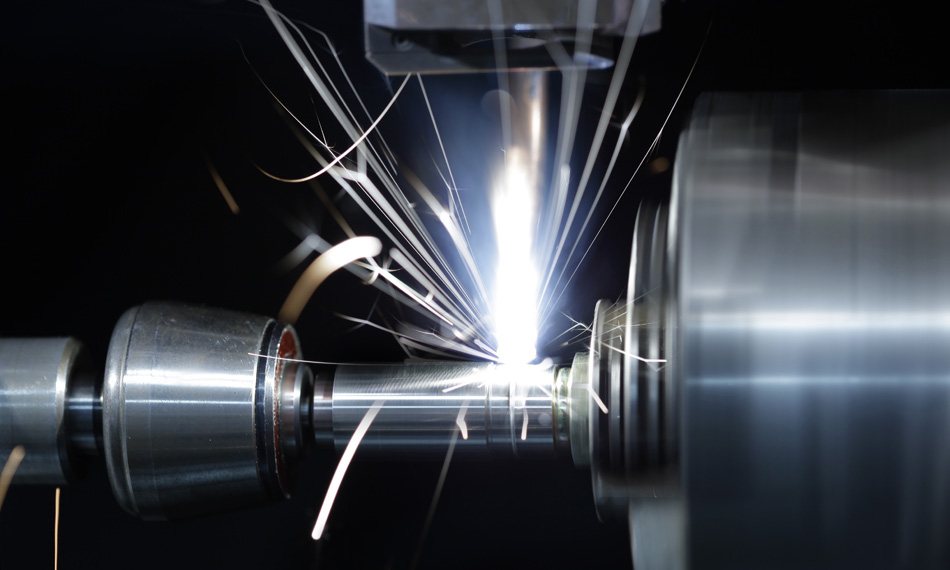
Wann ist eine Prozesskontrolle erforderlich?
Eine umfassend angelegte Prozesskontrolle beinhaltet Inspektionen und Datenerfassung in jeder Phase des Laserprozesses. Diese kann in vier große Bereiche unterteilt werden:
- Kontrolle vor dem Prozess
- Überwachung und Steuerung während des Prozesses
- Kontrolle nach dem Prozess
- Regelmäßige Systemkontrolle
In jeder dieser Phasen gibt es in der Regel eine Vielzahl von Optionen in Bezug auf die Prozesssteuerungsinstrumente und die Besonderheiten der Implementierung. Der Anwender muss entscheiden, welche Messungen notwendig oder nützlich sind und inwieweit sie Qualität und Durchsatz beeinträchtigen. Dies muss natürlich gegen die Kosten der einzelnen Produkte abgewogen werden. Es lohnt sich, jede dieser Phasen einzeln zu untersuchen, um herauszufinden, welche Tools zur Verfügung stehen und welche Vorteile sie möglicherweise bringen.
Kontrolle vor dem Prozess
Holzarbeiter haben ein altes Sprichwort: „Zweimal messen, einmal schneiden.“ Hinter dieser Redensart steht die Idee, dass es besser ist, einen Fehler zu vermeiden, als ihn später zu beheben. Je früher die Probleme in der Produktion erkannt werden, desto besser. Daher ist die Durchführung von vorbereitenden Checks ein besonders effektiver Weg, um Fehler, Ausschuss und Nacharbeit zu reduzieren.
Bei Laserprozessen werden Checks vor der Verarbeitung in der Regel zuerst durchgeführt, um zu überprüfen, ob die richtigen Teile geladen wurden. Dies kann durch die Prüfung der Größe/Form des Teils oder durch das Lesen eines Barcodes oder einer anderen Identifikationsbeschriftung auf dem Teil geschehen. Außerdem können die Dimensionen und die Ausrichtung der Teile gemessen und die genaue Position für die Bearbeitung bestimmt werden. Bei der Laserbeschriftung ist es außerdem üblich, dass das System in dieser Phase variable Eingangsdaten (Seriennummer, Chargennummer und andere Identifikationsdaten) von anderen Fertigungssystemen erhält.
Am häufigsten werden für diese Art von Überprüfungen kamerabasierte Bildverarbeitungs- und Mustererkennungssysteme eingesetzt. Dies kann durch spezielles Beleuchtungszubehör ergänzt werden.
Normalerweise verwendet ein Bildverarbeitungssystem die Kantenerkennung, um das Vorhandensein des Teils zu bestätigen und seine genaue Position zu bestimmen. Es kann auch bestimmte Merkmale oder Strukturen auf dem Teil identifizieren. Bei Schweißprozessen kann der Schweißspalt erkannt und gemessen werden, um die Passgenauigkeit der Teile zu bestimmen. Es kann auch eine Überprüfung der Fokusposition durchgeführt werden, um sicherzustellen, dass der Laser richtig auf die Arbeitsfläche fokussiert wird.
Um Teile mit einer 3D-Geometrie (nicht nur flach) zu bearbeiten, kann die Formerkennung mit einer Zeilenkamera zusammen mit einer Bewegung in der x- und z-Achse erfolgen. Dies ist besonders nützlich für Beschriftungsvorgänge, da einige Systeme jetzt eine Laserbeschriftung „vorverzerren“ können, so dass sie auf der endgültigen konturierten Oberfläche korrekt erscheint. Der erfolgreiche Einsatz dieser Art von System erfordert jedoch eine genaue Messung der Form und Ausrichtung des zu beschrifteten Teils.
Überwachung und Steuerung während des Prozesses
Die prozessbegleitende Überwachung wird für viele Aufgaben eingesetzt, ist aber wahrscheinlich bei Schweißanwendungen am wichtigsten. Der Grund dafür ist, dass die Qualität der Schweißnaht sehr stark von den Betriebsparametern des Lasers abhängt. Darüber hinaus stellen Spalte oder Schwachstellen in einer Schweißnaht in der Regel einen totalen Verlust des Teils dar, so dass es kaum Raum für Fehler gibt.
Beim Schweißen müssen mehrere Dinge gemessen werden. Dazu gehören die Betriebsparameter des Lasers, wie z. B. die Ausgangsleistung, sowie die Position des Strahls relativ zum Schweißspalt und der richtige Fokus. Beim Metallschweißen kann eine Vielzahl von Schweißparametern wie Eindringtiefe, Spritzer und Hohlräume ebenfalls erfasst werden. Insbesondere beim Polymerschweißen werden in der Regel die Temperatur entlang der gesamten Schweißnaht und die Kollapshöhe des Oberteils gemessen.
Für die Durchführung all dieser Messungen wurde eine ganze Reihe von Instrumenten entwickelt. Hochgeschwindigkeitskameras und optische Computertomographie (OCT) sind wahrscheinlich die am häufigsten verwendeten Techniken. Sowohl die Messung des zurückreflektierten Laserlichts als auch das vom Schweißprozess selbst emittierte Licht sind ebenfalls sehr nützliche Indikatoren. Darüber hinaus kann die akustische Überwachung ein feinfühliges Mittel sein, um den Zustand des Schweißprozesses im Material zu erkennen. Auch Pyrometer-basierte Laserleistungskontrolle und Wärmebildtechnik werden häufig eingesetzt.
Kontrolle nach dem Prozess
Es gibt in der Regel zwei Hauptziele bei der Kontrolle nach dem Prozess. Zunächst wird geprüft, ob der Prozess korrekt durchgeführt wurde und ob das Teil innerhalb der Spezifikationen liegt. Die zweite Aufgabe ist die Protokollierung der Ergebnisse in Übereinstimmung mit ISO- und anderen Normen. Dies kann die Aufzeichnung von Laser- und anderen Systemparametern sowie von Messungen des fertigen Teils beinhalten.
Beim Schweißen von Metallen können während der Abkühlphase die gleichen Techniken wie bei der Verarbeitung eingesetzt werden, insbesondere um die Bildung von Rissen zu erkennen. Auch hier können unter anderem Thermografie und akustische Erkennung zum Einsatz kommen. Die Bildverarbeitung kann verwendet werden, um die gesamte Schweißnahtgeometrie und -ausrichtung zu beurteilen. Künstliche Intelligenz (KI) und andere maschinelle Lernverfahren werden zunehmend in Bildverarbeitungssystemen eingesetzt, um die Qualität der Teile und sogar das Aussehen zu beurteilen. Dadurch kann ein Prozess stärker automatisiert werden und ist weniger bedienerabhängig und subjektiv.
Regelmäßige Systemkontrolle
Die periodische Systemkontrolle bezieht sich auf Vorgänge, die zwischen den aktiven Nutzungszeiten des Systems durchgeführt werden. Diese dienen dazu, den Zustand des Systems unabhängig von einem bestimmten Vorgang zu beurteilen und gegebenenfalls Anpassungen vorzunehmen. Dies ist auch der Punkt, an dem Daten zur Gesamtanlageneffizienz (OEE) gesammelt werden können.
Bei einem Lasersystem sollten mehrere strahlenbezogene Parameter regelmäßig bewertet werden. Dazu gehören Leistung, Strahlqualität (M² und die Identifizierung von Hotspots oder kleinen Intensitätsschwankungen), Strahlausrichtung und Fokusposition. Auch die optische Ausrichtung und die Verschmutzung von Optiken im Strahlengang kann an dieser Stelle festgestellt werden. Diese Arten von Messungen sind wichtig für den ordnungsgemäßen Betrieb des Systems und auch für die Minimierung von System-zu-System-Schwankungen (und damit die Verbesserung der Produktionskonsistenz).
Integrierte Software vereinfacht die Prozesskontrolle
In der Vergangenheit haben Anwender ihre Lasersysteme oft mit Instrumenten zur Prozesssteuerung von Drittanbietern ergänzt. Dies erschwerte die optische, mechanische, elektronische und softwaretechnische Integration dieses Zubehörs. Und es führte oft zu „Schuldzuweisungen“ unter den Lieferanten, wenn das System nicht richtig funktionierte. Heute ist es jedoch zunehmend üblich, dass der Lasersystemanbieter all diese Funktionen integriert und ein einziges, schlüsselfertiges System liefert.
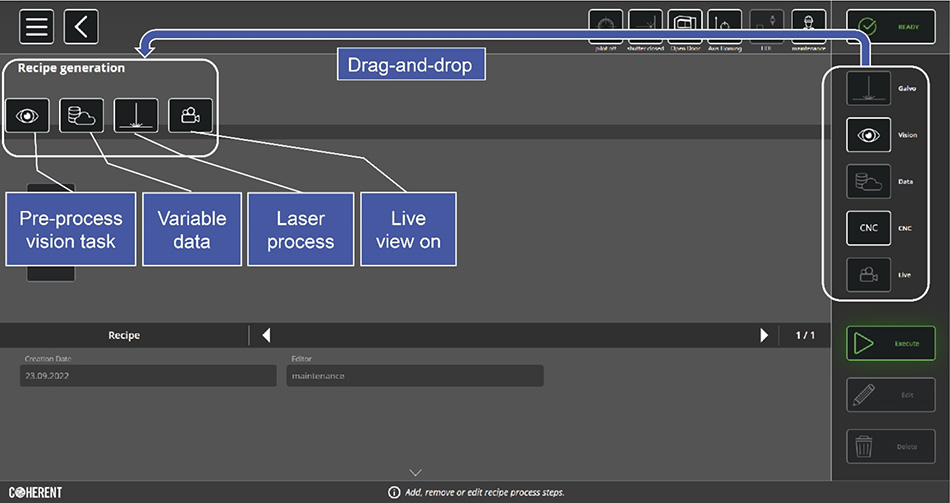
Abbildung 1: In Coherent Laser FrameWork wird ein Auftrag erstellt, indem verschiedene Inspektions-, Prozesskontroll- und Verarbeitungsaufgaben auf die Zeitleiste gezogen werden.
Coherent bietet zum Beispiel Prozesskontrollinstrumente für alle gerade beschriebenen Funktionen für viele seiner Laserschweiß-, Schneid- und Beschriftungsmaschinen an. Coherent Laser FrameWork bietet eine einheitliche Softwareplattform und Maschinenschnittstelle, die all diese Funktionen integriert und vereinfacht. Verschiedene Aufgaben der Prozesskontrolle – wie die Inspektion vor dem Prozess mit Hilfe von Bildverarbeitungsverfahren, die Überwachung des Schweißens während des Prozesses und die Strahlendiagnose nach dem Prozess – können zusammen mit den Laserparametern und der Teilehandhabung während der Auftragseinrichtung festgelegt werden. Die Grafik zeigt, wie diese mit Hilfe der einfachen Drag-and-Drop-Funktion von Laser FrameWork zum Prozessrezept hinzugefügt werden.
Die nächste Grafik zeigt, wie diese Funktionalität für eine bestimmte Aufgabe – in diesem Fall ein Metallschweißverfahren – eingesetzt werden könnte. Zunächst liest PartVision (ein kamerabasiertes Zubehör) den Barcode eines Teils, um zu überprüfen, ob das richtige Teil vorgelegt wurde, und lädt die richtige Prozessrezeptur in die Maschine. Als nächstes identifiziert das Bildverarbeitungssystem ein Merkmal auf dem Teil, das geschweißt werden soll.
Der Schweißprozess selbst wird mit SmartSense+ überwacht. Dieses System umfasst optische Detektoren und akustische Sensoren. Es erfasst rückreflektiertes Laserlicht sowie das vom Prozess selbst emittierte Licht. Es bewertet kontinuierlich den Status des Schweißprozesses und identifiziert sofort alle Probleme oder Fehler.
PartVision wird für die Nachbearbeitung der Teileinspektion verwendet. Dann werden alle Prozessparameter und andere relevante Informationen vom System gespeichert.
Schließlich wird BeamInspect zwischen den Aufträgen verwendet, um den Zustand und die Gesundheit des Laserstrahls zu beurteilen. BeamInspect ist ein Instrument zur Laserstrahldiagnose, das präzise, automatische Messungen und Berechnungen aller Strahlparameter durchführt, die sich auf die Prozessergebnisse auswirken.
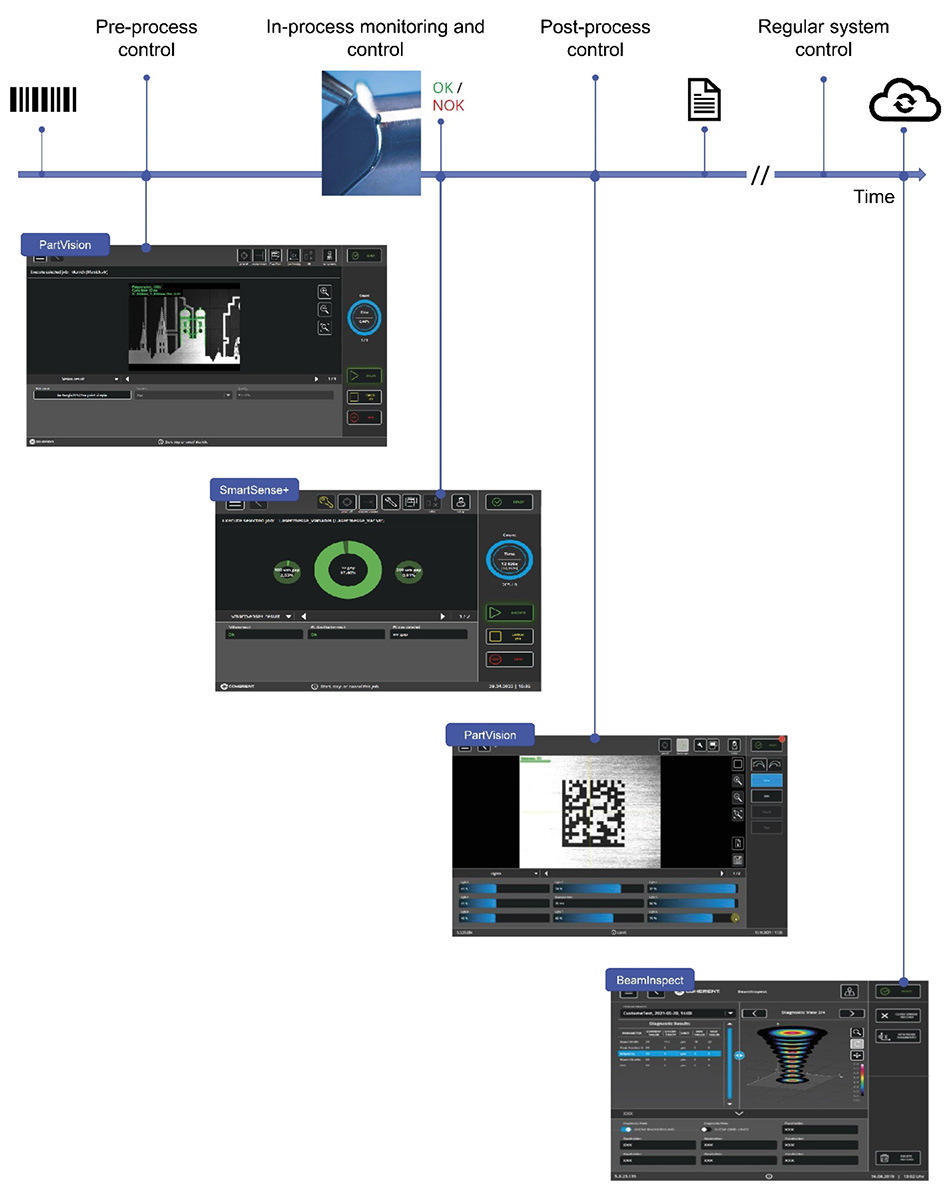
Abbildung 2: Beispiel einer mit Laser FrameWork spezifizierten Laserschweiß- und -markieraufgabe, die in jeder Phase Inspektions- und Prozesskontrollaufgaben beinhaltet.
Schlussfolgerung
Die ständige Forderung nach schnelleren, präziseren und ertragreicheren Laserprozessen erfordert eine Prozesskontrolle in jeder Phase der Produktion. Dies kann jedoch zu einem hohen Maß an Komplexität führen, so dass es für Hersteller schwierig ist, sie erfolgreich umzusetzen. Integrierte Systeme mit einer einheitlichen Softwareschnittstelle, wie Laser FrameWork, können dies vereinfachen. Außerdem bieten sie dem Anwender die Einfachheit und Sicherheit, dass er sich bei der Einrichtung, Schulung und Wartung an eine einzige Stelle wenden kann. All dies macht die Vorteile der Laserbearbeitung einem breiteren Anwenderkreis zugänglich.