時代に左右されないmicroLED生産ソリューション
エキシマレーザベースのレーザ誘起前方転写(LIFT)は、現在だけではなく、将来においても実用的な大量転写プロセスです。
2024年7月23日、Coherent

microLEDは、他のパネルタイプよりも輝度、効率、寿命の点で優れているため、次世代ディスプレイ技術の最前線に立っています。実際、microLEDの利点は非常に多く、高度なスマートウォッチから広範なAR/VR体験に至るまで、革新的な応用が期待されています。
しかしながら、ディスプレイ業界は大きな挫折に直面しました。大手テクノロジー企業のAppleが、長年にわたる多額の投資(2014年以降、推定30億米ドル以上)の末、野心的なmicroLEDプロジェクトを断念したのです。Appleは、この決定の理由を公式に発表していません。
Apple以外のディスプレイ業界の関係者は、Appleが既存のOLEDディスプレイと比較して、価格競争力の高いmicroLEDディスプレイを開発できなかったのではないかと推測しています。Appleは、最先端の生産技術を活用していなかったために歩留まりと生産高が向上しなかった可能性があります。この問題を解決する鍵となるのが、大量生産の重要な工程である「大量転写」プロセスの手法です。
ここでは、高度な大量転写技術の重要な役割について説明し、Appleを窮地に追い込んだ可能性のある生産上の問題を、エキシマレーザベースの手法でどのように克服できるかを見ていきます。この手法が、経済性と将来性を備えたmicroLED生産ソリューションをどのように提供するかを確認します。
「大量転写」とは一体何か?
大量転写プロセスについては、過去の投稿で詳しく説明しています。簡単に言うと、microLEDの生産は、赤、緑、青のLEDを個々の基板に実装することから始まります。これらの基板は、最後の段階で、最終的なディスプレイ回路基板に転写する必要があります。ディスプレイ回路基板でこれらの基板は3つの各グループ(赤、緑、青)に配置され、ディスプレイの各ピクセルが形成されます。
場合によっては、LEDはまず元の基板から「一時的なキャリア」に転写され、そこで接着剤で固定されます。その後、ディスプレイパネルに転写されます。他のメーカーは、中間工程を挟むことなく、LEDを元の基板からディスプレイパネルに直接転写します。
いずれの方法でも、大量転写を難しくしている要因がいくつかあります。第一に、LEDはミクロン単位の位置精度で配置する必要があります。第二に、膨大な数のLEDを転写する必要があるため、プロセスを高速化する必要があります。たとえば、わずか500×500ピクセルのディスプレイであっても、750,000個(500×500×3)ものLEDを個々に転写する必要があるのです。第三に、このプロセスは、歩留まりを最大化し、広範囲の修理を避けるために、信頼性が高くなければなりません。
また、microLED技術が発展するにつれて、LED自体の大きさも小さくなっていくことに留意する必要があります。現在、LEDのサイズは約50×50 µmですが、最終的には10×10 µmか、それよりさらに小さくなると予測されています。LEDは小さくなればなるほど、損傷させずに転写し、必要な精度で配置することが難しくなります。
レーザがmicroLEDに革命をもたらす
レーザ誘起前方転写(LIFT)では、現在のLEDのダイサイズ(約20 µm×20 µm)でも、将来のより小型のダイサイズ(10 µm×10 µm)でも、実用的かつ経済的な方法で大量転写を行うことができます。LIFTでは、エキシマレーザのパルスが透過性のある一時的なキャリアの裏側から入射します。光がGaNバッファ層に吸収されると、GaN層は蒸発します。こうしてLEDダイは、極めて近い距離に配置されたディスプレイ基板に転写されます。最終的なボンディング工程によって、LEDは機械的にも電気的にもパネル基板に接続されます。
microLEDディスプレイの生産において、エキシマLIFTは、他の大量転写の方法と比べて非常に多くの利点があります。特に重要な利点の一つは、配置精度が高いことです。LIFTでは、1 µm以下の配置精度を達成できます。これは、小型の高解像度ディスプレイを生産する際に必須の精度です。このレベルの精度があれば、各microLEDが完璧に整列されることが保証され、ディスプレイの品質を損なうピクセル不良のリスクも低減されます。
また、LIFTは圧倒的な効率性と速度を誇ります。数百万個のmicroLEDを迅速かつ確実に転写できるため、大幅な生産時間の短縮とコスト削減を実現できます。これは、ディスプレイメーカーが品質を損なうことなく、生産を拡大しようとしている場合に特に有利です。
さらに、レーザベースの大量転写は、さまざまなサイズの基板やmicroLEDに適応できるため、柔軟性があります。小型のウェアラブルデバイスから大型の超高解像度テレビまで、各種のmicroLEDアプリケーションの需要が増加している中、この汎用性は極めて重要となります。
また、当社のLIFTソリューションは将来を見据えて設計されています。microLED市場が発展し、より小型でピクセルピッチの狭いLEDが利用されるようになっても、エキシマLIFTシステムは迅速に適応できます。これは、設備を大規模に一新したり、ダウンタイムを発生させたりすることなく行えるため、メーカーは競争市場で優位性を維持することができます。こうした適応性とCoherentの研究開発に対する継続的な取り組みによって、当社のソリューションは、ディスプレイの将来にとって極めて重要な技術として位置づけられています。
実際に使用した結果
Coherentのアプリケーションエンジニアは、現在生産されているデバイスよりもサイズと厚さが大幅に小さいmicroLEDダイにLIFTを適用するために、最近、パラメータの一部を定量化するテストを実施しました。具体的には、5 µm×5 µm×3 µm(厚さ)のmicroLEDを対象とするLIFTの配置精度を、ギャップ距離(microLEDを保持する一時的なキャリアからターゲット基板までの距離)の関数としてテストしました。大量生産環境で非常に狭いギャップ距離(50 µm以下)を確実に維持することは難しいため、このデータは有用です。したがって、LIFTは、LEDダイが小さい場合であっても、これより広いギャップにおいて、迅速かつ確実に、そして大規模に機能する必要があります。
実験の設定では、Coherent UVtransferを使用して、4インチのGaNドナーウェハにあるmicroLEDを直径100mmの石英のターゲットウェハに転写しました。配置精度(x方向とy方向)は、ダイを自動的に識別し、各ダイの中心位置を特定できる顕微鏡とマシンビジョンシステムを使って測定されました。それぞれのギャップ距離で、979個のmicroLEDが転写されました。
次のグラフは、979個すべてのmicroLEDの配置精度(理想位置からのオフセット)を示しています。ギャップは50 µm、ダイ間のピッチは90 µmです。このデータを要約すると、microLEDの99.7%(3σ)が、ターゲット位置から0.66 µm(x)、0.56 µm以内に配置されています。
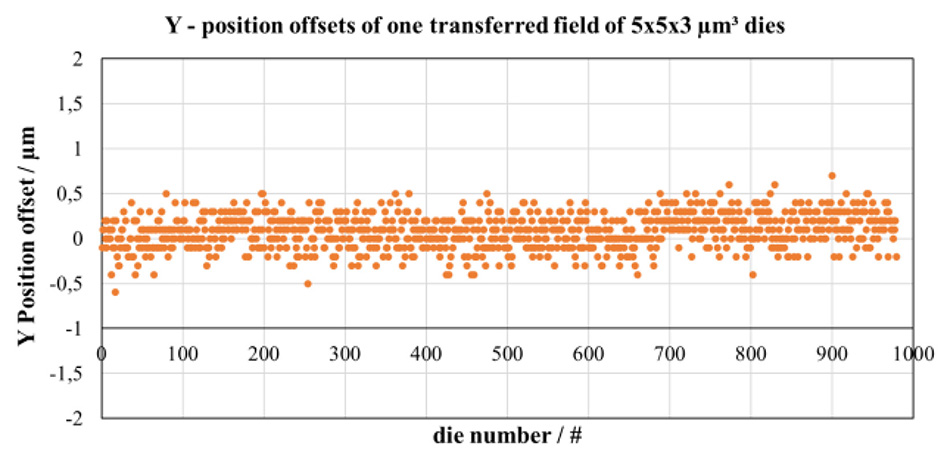
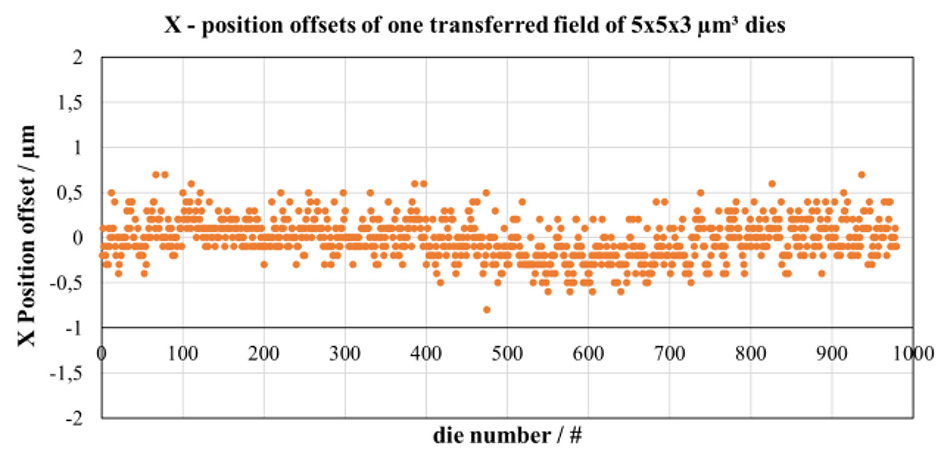
979個のmicroLED(各サイズは5×5×3 μm³)のLIFTの位置オフセット。ギャップを50 µm、ダイ間のピッチを90 µmとして転写。
次のグラフは、配置精度がギャップ距離に応じてどのように変化するかを示しています。ギャップ距離が80 µmまでにおいては、サブミクロンの配置精度が維持されました。これらの数値から、LIFTは、小型のmicroLEDに対して完全に実用性があることがわかります。
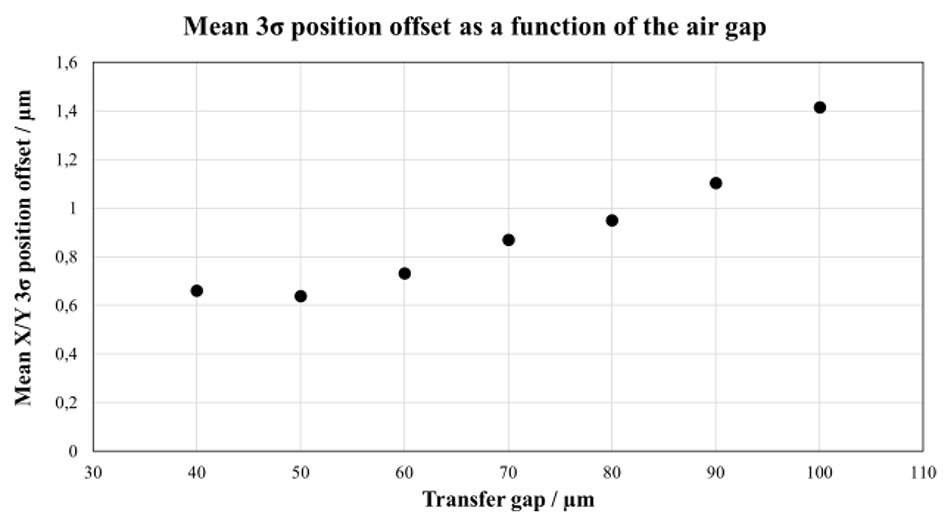
平均3σ位置オフセット偏差(x方向とy方向の3σ値の平均)。979個のmicroLED(寸法:5×5×3 μm³)のLIFTにおける、転写ギャップ距離の関数として表されます。
microLEDディスプレイは画期的な視聴体験を実現しますが、その商業化は大量生産の問題によって阻まれ、最も技術に精通したメーカーでさえもその意欲を失っていました。エキシマレーザベースのLIFTは、生産上の一つの大きなハードルを克服し、他の大量転写技術では解決できなかった問題を解決しています。最小サイズのLEDでも精密かつ高速に転写することができ、そのベースとなるレーザは、要求が厳しい他のディスプレイ生産プロセスでも、24時間365日の動作信頼性を実証しています。さらに、LIFTの適応性により、進化し続けるmicroLEDへの適合性が確保されます。こうしたことから、LIFTはディスプレイメーカーが将来にわたって利用できるソリューションであり、この技術の商業化への道を開くものとなっています。
LIFTについて詳しくはこちら。