CUSTOMER SUCCESS STORY
BRINGING LASER CLADDING TO INDONESIA
A Coherent high-power diode laser system has enabled Laser Indonesia to become one of the first in their country to offer on-site cladding services.
Tommy Suriady loves lasers. That’s why he started his laser job shop in Bandung, Indonesia, in 2014. Today, Laser Indonesia has over 30 employees in two cities and offers laser cutting, welding, marking, and cladding services to businesses throughout Southeast Asia. They support customers in oil & gas, power, mining, construction, electronics manufacturing, machine tools, and more. And Suriady still believes in lasers so strongly that he doesn’t offer any non-laser processes (other than traditional welding methods that are combined with lasers).
But Laser Indonesia didn’t add laser cladding to their portfolio until 2022. In fact, before then the process was virtually unknown in Indonesia.
GETTING STARTED IN CLADDING
While Suriady had heard of laser cladding from Coherent many years before, his journey into laser cladding really began in 2019. That’s when Coherent, through our Malaysia/Singapore office, offered to integrate a cladding system for him. He needed this assistance since, despite his experience with a myriad of laser processing technologies, he lacked any detailed expertise in cladding. Also, the capital cost for a laser cladding system represented a significant expense and risk to a company the size of Laser Indonesia. He wanted to make sure he got it right the first time.
Suriady already owned industrial lasers from several of the major manufacturers in the world, so before accepting the offer he sought their guidance. He relates, “Many of these companies are not even into cladding yet, while some others wanted me to buy expensive systems with complicated zoom optics and lots of other options. They’re good lasers, but at the time I wanted something fundamental. First of all, I couldn’t afford anything more. And second, there’s a big learning curve. I wanted a simple system that I could get running quickly and use to start generating some income. Plus, I needed a system robust enough to survive any mistakes we were going to make with it. Coherent was the only company who seemed to be capable and, most importantly, willing to put together a cladding laser that fit my budget and then provide the support I needed to bring it on-line.”
THE CLADDING LEARNING CURVE
Laser Indonesia took delivery of a Coherent HighLight DL4000HPS in December, 2020. This is a compact, 4 kW, fiber-coupled diode laser system with integrated chiller. Coherent also equipped the laser with focusing optics that produce a 3 mm diameter beam on the work surface and a gas-delivered powder delivery head.
Laser Indonesia spent virtually all the next year learning how to use it and get optimum results. Suriady says, “The substantial support I got from the Coherent team during this time was absolutely essential to our success. Coherent provided equipment support, as well as an immense amount of laser cladding know-how. They had a multinational support team consisting of engineers from Singapore, Malaysia, Vietnam, and Germany. Despite the COVID lockdowns, this group managed to get the system up, running, and cladding.” Suriady relates that he also performed many customer demonstrations and trials to refine his techniques while convincing prospects about the process.
CLADDING IN THE FIELD
By 2022, Laser Indonesia was ready to take laser cladding on the road. Literally. Because all of their work is performed on-site at customer locations. This is necessary since most of the equipment Laser Indonesia clads is too big, heavy, or expensive to bring back to their own shop.
Typical cladding jobs include resurfacing steam turbine blades in power plants, restoring bearing surfaces on shafts in industrial machinery, and refacing large rollers in paper mills. The gas-delivered powder nozzle (which forces the powder towards the work surface under pressure) enables the system to perform cladding in any orientation – even upside down. This capability provides the operational flexibility to clad just about any part or piece of equipment without having to move or reposition it. Suriady reports that this is a critical feature for their work.
Inconel 625 is often their material of choice as the cladding powder, mainly due to the types of industry that Laser Indonesia serves. “Inconel 625 tends to deliver a clad layer that is compatible and at least as strong as the original material,” states Suriady. “Plus, it’s very corrosion and chemical-resistant. We used it on one of our first jobs to clad the inside of a tank that processes chlorine-based precursors for a PVC manufacturer. The results impressed our customer so much that after one year of use they’ve already asked us to do more.”
The Coherent laser is usually mounted on a variety of Kuka robot arms, depending on the requirements of the task. Laser Indonesia typically sends a four-man crew on a job. This is enough manpower to load and unload the laser system from their custom-made truck and roll it to the work site.
During a job one worker operates the laser, one controls the robot, and another serves as safety officer, viewing and recording the whole operation. Suriady himself usually acts as process designer together with the engineering team on site. Every job needs its own novel approach; no two jobs are the same.
In addition to delivering high-quality cladding results, Suriady cites the laser’s ease-of-operation, compact size, robustness, and reliability as outstanding features for him. “We travel great distances to remote locations to each job and the laser often gets bounced around on the trip. Plus, the operating environments are almost always high temperature and high humidity,” he notes. “The Coherent laser is portable and robust enough for us to transport, quick to set up, and has been very reliable under all conditions. It also has an integrated, self-contained chiller, so the cooling system isn’t dependent on the local water quality, which isn’t always so great.”
“Nobody in Indonesia had even heard of laser cladding before we started, so I took a giant risk,” continues Suriady. “But so far everyone we’ve served has been so impressed with the results. It is addictive, you know? It’s obviously cheaper than part replacement, and our customers immediately saw they were saving a tremendous amount of time by recladding worn parts. Then after a while, they realized they were also saving big bucks. And they are ecstatic! Laser cladding delivers better results than any other method. I’m already getting repeat orders, and the reliability and flexibility of the Coherent laser give me confidence to grow our cladding business further.”
“I saw an opportunity for laser cladding in Indonesia, but I didn’t know how to get started. Coherent listened to my needs, helped me build a system, and supported me through getting it running successfully."
— Tommy Suriady, President, PT Laser Indonesia
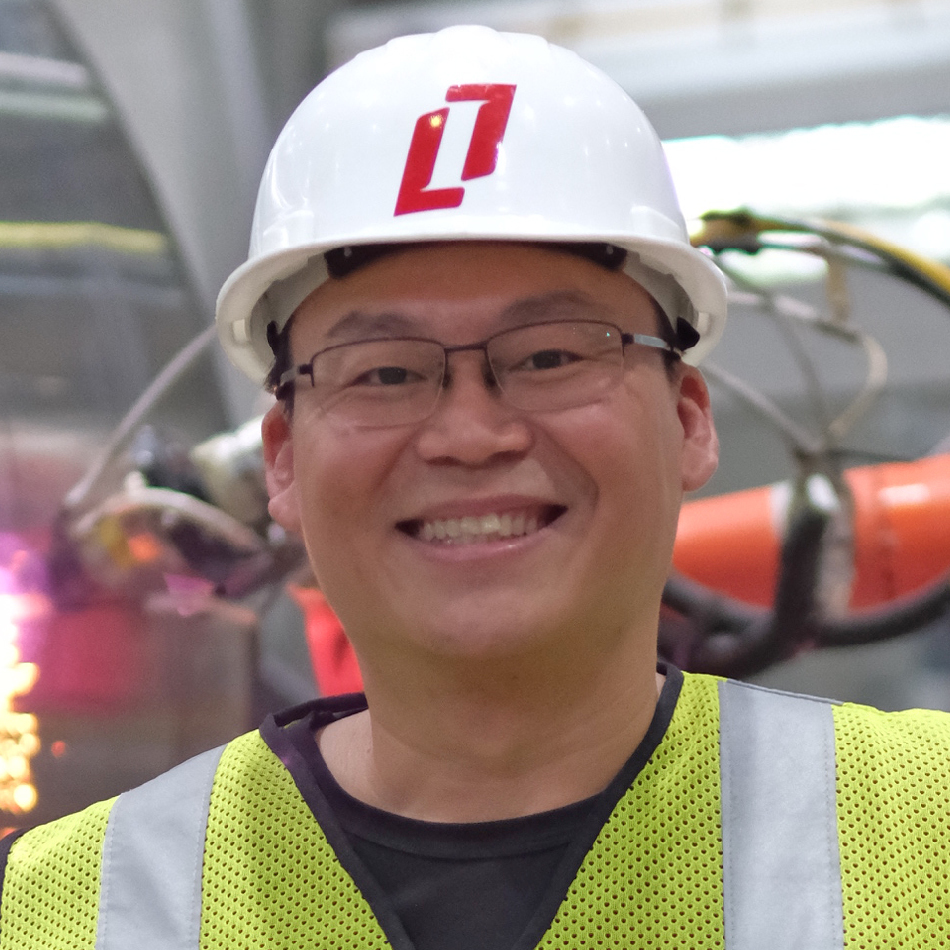
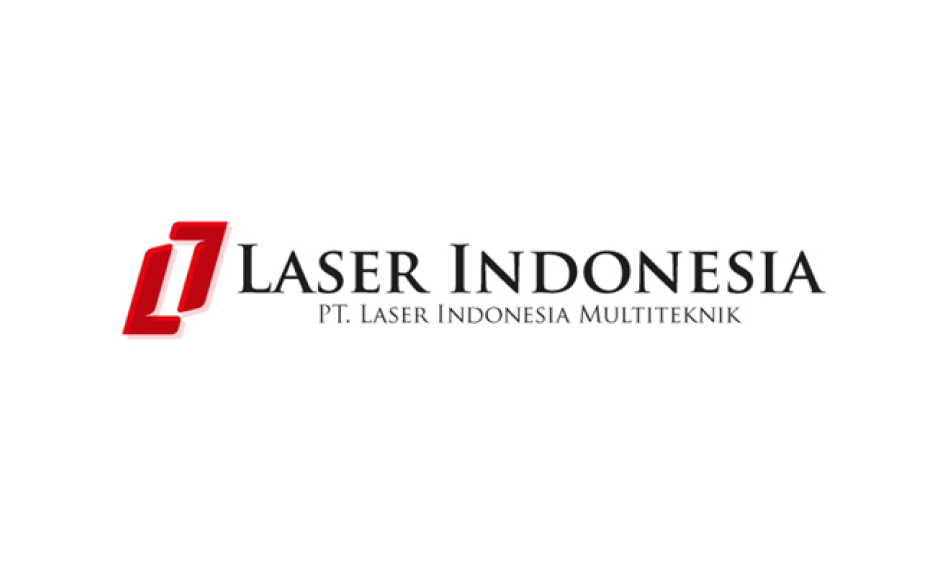
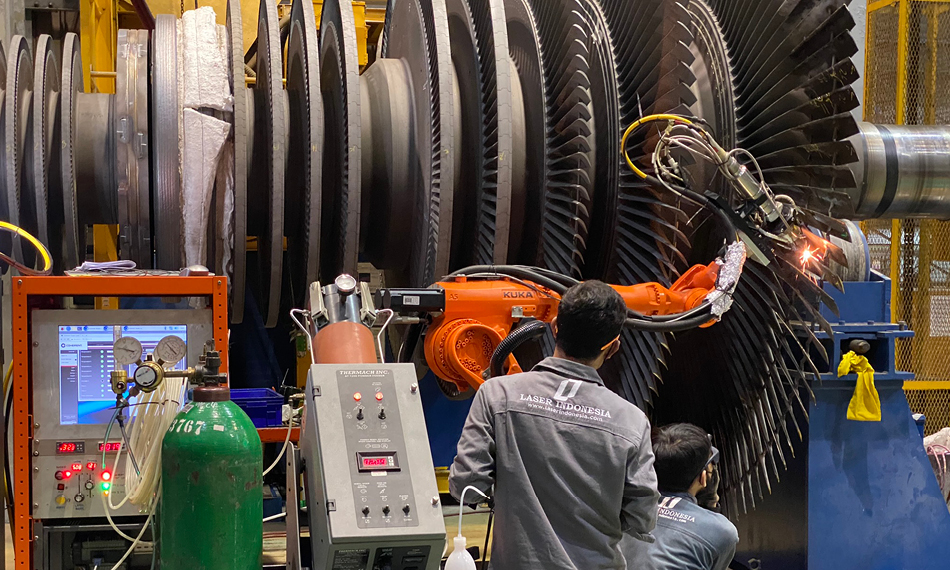
Figure 1. Restoring the leading-edge surface of turbine blades with cladding. Cladding is much quicker and less costly than removing and replacing worn blades or repairing them using traditional welding or thermal spray methods.
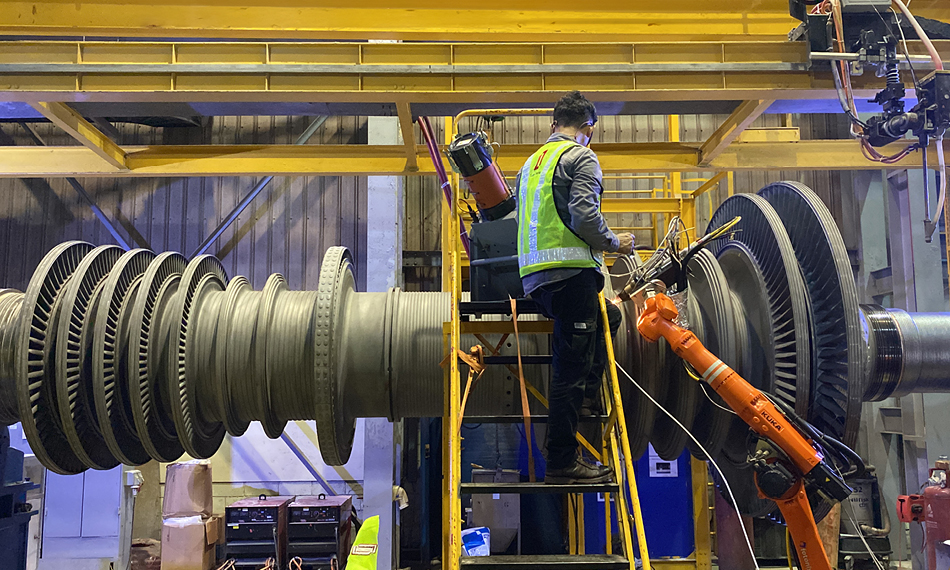
Figure 2. Bearing surfaces on large machines can be quickly resurfaced at the customer site with laser cladding.
Figure 3. The entire cladding system is compact and easy-to-use, which enables Laser Indonesia to transport it and operate it at remote locations.