Enhancing IR Coating Durability
The Coherent diamond over-coat enables high-performance IR thin films with exceptional durability.
December 18, 2023 by Coherent
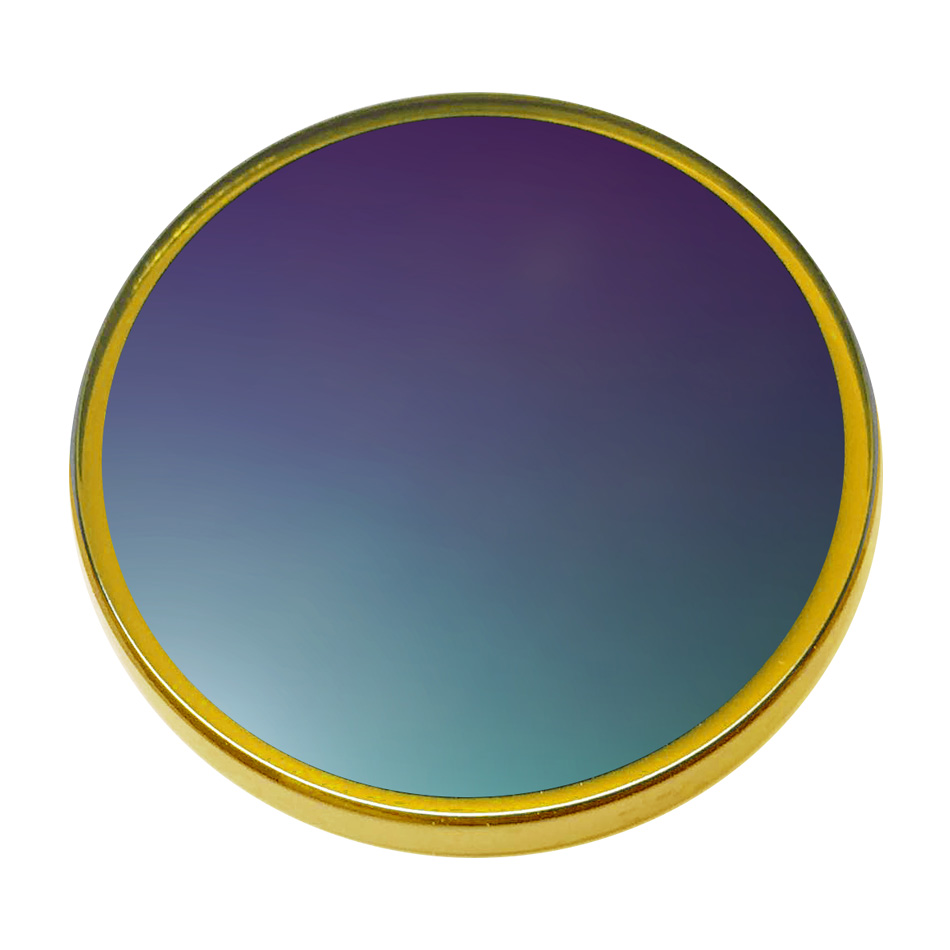
From eyeglasses to precision laser lenses, the vast majority of optical components made have some sort of performance-enhancing thin film coating on their surface(s). These might serve to reduce distracting reflections on eyeglasses, improve the power delivered by an industrial laser system, or selectively pass certain wavelengths in a flow cytometer to enable cell identification. Coatings can also make an optical surface more mechanically durable and easier to clean.
How do coatings work?
Thin film coatings work by using interference effects between light waves. This is the same phenomenon that makes colors appear in soap bubbles and oil slicks, even though the soap or oil itself is colorless.
The drawing illustrates the basics of how interference works. Without a coating, a glass surface reflects about 4% of the incident light. This means that only 92% of the light makes it through a window or glass lens (since there are two surface – a front and back). This light loss lowers the throughput or efficiency of an optical system. And in something like a camera lens which contains multiple individual components, it can also reduce image contrast.
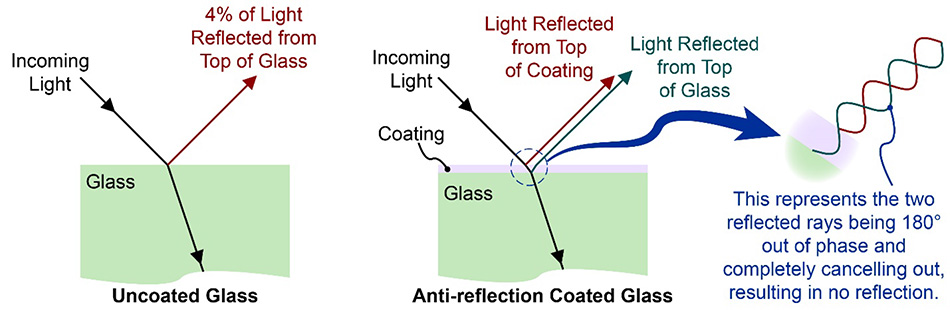
Normally, each surface of a glass optic reflects about 4% of visible light back. If a thin coating is applied to the surface, it creates a second reflection. By manipulating coating thickness and refractive index, a variety of effects can be achieved, including eliminating the reflection almost entirely.
Placing a coating on the optical surface introduces a second reflection – one from the top of the coating, and another at the coating/glass interface. Those two rays will be exactly out of phase (as shown in the drawing) if the coating thickness is one-quarter the of the light wavelength. If the two waves are also the same amplitude (which depends on the refractive indices of the materials), then they will destructively interfere entirely. This means there is no reflection at all – at least at that specific angle and wavelength. This is an anti-reflection (AR) coating.
Coatings often contain numerous layers of two or more different materials. These are arranged to produce a wide variety of effects, all of which exploit the basic mechanism of light wave interference just presented. Most coatings can be categorized as follows:
Coating Function |
Explanation |
Antireflection (AR) |
Used to suppress unwanted surface reflections. Can operate at a single wavelength, or over a range of wavelengths. |
High reflection (HR) |
Mirror coatings increase the reflectivity of a surface. Can operate at a single wavelength, or over a range of wavelengths. |
Partial reflection |
Beamsplitters transmit some of the input light and reflect the rest. They are often used at nonzero angles of incidence. |
Short wave pass/long wave pass |
These pass shorter wavelengths and transmit longer wavelengths, or vice-versa. They are often used at nonzero angles of incidence. |
Bandpass |
These filters pass a range of wavelengths around a central value and reject everything else. |
Polarization |
These separate incident light into orthogonally polarized components, typically transmitting one and reflecting the other. |
Sometimes coatings perform functions other than just modifying optical characteristics. For example, transparent conductive coatings are used extensively in touchscreens to provide electronic functionality. Hydrophobic and oleophobic coatings, which repel water and oils respectively, are also frequently applied to touchscreens. Diamond-like carbon (DLC), sapphire thin films, and other materials are employed to enhance mechanical durability of optics.
How are coatings made?
Fabricating coatings requires the ability to deposit multiple thin layers – typically from about 100 nanometers to a few microns in thickness – of a dielectric or metal on to the target material. For almost all coatings, it is critical to maintain precise control over the thickness of each layer, as well as its refractive index. The uniformity of these properties across the entire component is also important.
Ideally, the manufacturer can also control the mechanical characteristics of the layers, such as the amount of tensile or compressive stress in each layer. This is necessary to yield a final product which is both durable and adheres well to the substrate.
The most commonly used coating methods are various forms of physical vapor deposition (PVD) or chemical vapor deposition (CVD). For example, one of the oldest and most widely used PVD techniques is evaporative coating. Here, the optics are placed into a high vacuum chamber. The coating material is heated either resistively or by electron beam bombardment until it vaporizes. This vapor fills the vacuum chamber and recondenses on the optical surfaces to form the coating layer.
Each coating technology has its own specific capabilities, advantages, and disadvantages. Coherent employs virtually every major method available in order to deliver optimum results for each use case. The chart compares some of their key characteristics.
Method |
Evaporation |
Evaporation with Ion Assisted Deposition |
Ion Beam Sputtering |
Magnetron Sputtering |
|
Wavelength Range |
<266 nm |
+ |
– |
O |
– |
266 nm – 5 µm |
+ |
+ |
+ |
+ |
|
>5 µm |
+ |
– |
O |
– |
|
Cost |
+ |
O |
O |
+ |
|
Mechanical & Environmental Durability |
– |
O |
+ |
O |
|
Scatter & Absorption |
– |
O |
+ |
O |
|
Laser Damage |
+ |
+ |
+ |
+ |
|
Deposition Precision |
– |
O |
+ |
O |
Coating at Coherent – Range, Quality, and Volume
Consistently producing high-quality optical coatings, especially in large volumes, requires quite a bit more than just the deposition chambers themselves. It starts with coating design. This means determining the combination of materials and layer thicknesses that will deliver the desired optical performance, as well as meet any other requirements for mechanical durability, laser damage threshold, cost, or other characteristics.
Then, an array of process monitoring instrumentation and metrology equipment is typically employed to control and measure layer properties during deposition itself. These ensure that the coating design is faithfully reproduced on the optics. A variety of metrology instruments are used to measure the optical and mechanical properties of finished products.
Coherent is a vertically integrated optics manufacturer which puts us in a unique position to deliver high-quality optical coatings in virtually any volume. We manufacture substrate materials, fabricate components, design and produce coatings, and even make assemblies – all in-house. And we have deep knowledge and experience in every one of these areas.
Coherent also has the test equipment to verify every aspect of component performance. In fact, we have quality assurance (QA) at each step of production and perform 100% inspection of every optic we make.
All this enables us to control our entire process – from raw materials to finished goods – to guarantee every optical and mechanical specification for our products, and more. And it means we offer a secure supply chain to minimize risk and uncertainty for our customers. Plus, the range and quantity of production equipment at Coherent allows us to make just about any type of coating and scale in volume as needed.
It's Good to Make Hard Coatings
Our extensive capabilities, especially in terms of materials, also put us in the lead in terms of developing new coatings. One standout example of this is our unique diamond over-coat (DOC) which is primarily intended for infrared optics.
Infrared optics are used in a wide range of applications, including consumer electronics, medical devices, industrial laser systems, and military and aerospace imagers. The optical performance demands in all these areas is increasing continually. Many of these uses also require durability and reliability – in particular, the ability to repeatedly clean the surface of an optic without damaging the coating.
In the past, users had to choose between traditional coatings, which deliver high performance but might not be highly durable, or diamond-like carbon (DLC) coatings that offer great durability, but not cutting-edge performance. Specifically, DLC anti-reflection coatings are typically single-layer designs that only partially improve optical transmission and are limited to certain substrate materials, such as germanium and silicon.
The DOC eliminates that tradeoff and delivers both the outstanding optical performance of a traditional evaporative coating and the unmatched durability of a CVD diamond film. To fabricate the DOC, we utilize a custom-designed coating system that combines both evaporative methods and CVD in a single process.
While the fabrication of our DOC requires specialized equipment, much of our technology actually lies in the coating design. Specifically, this design must match the high refractive index and high mechanical stress of the diamond-like carbon film with the underlying PVD materials.
The DOC has numerous applications, and a great example of the coating’s robustness is in industrial laser processing – specifically high-speed, high-volume drilling of holes (called vias) in printed circuit boards. A window protects the laser-focusing optics and gets spattered by debris from the drilling process. The use of a diamond-coated protective window increases the time between cleanings. It also allows aggressive cleaning to remove copper and other particulate while still maintaining its optical properties substantially extending its lifetime and reducing the cost and downtime for a replacement window.
A further use case is on the final lens surface in an optically-based glucose measuring system. Here, the final optic is in contact with the patient or sample, and therefore may require periodic cleaning. Again, the DOC would allow this optic to be cleaned without damage.
The DOC represents a breakthrough in coating technology. But it’s just one of the many types of coatings Coherent can produce. Learn more about our coating capabilities.