AN IN-DEPTH LOOK AT 3D SENSING
Coherent is a leading provider of advanced illumination solutions for 3D sensing applications.
May 22, 2024 by Coherent
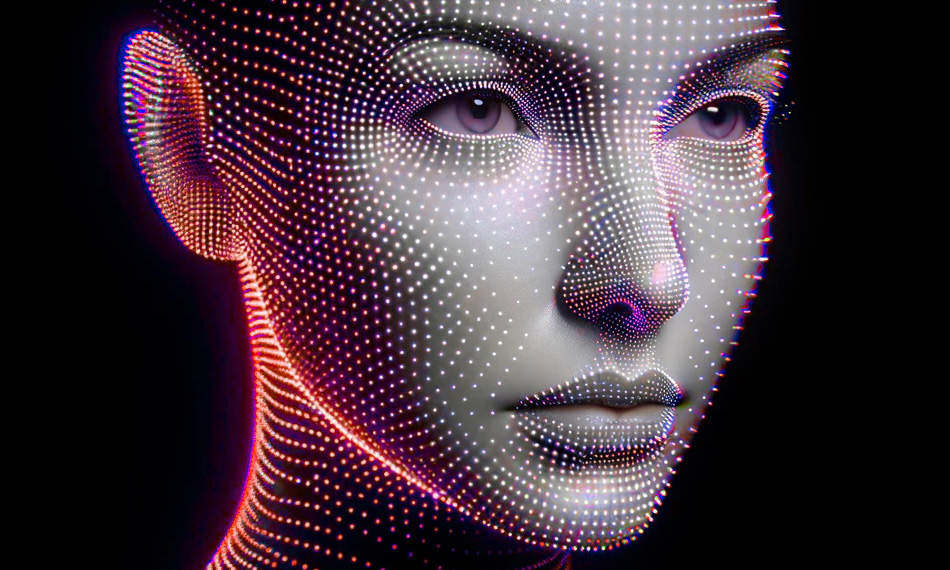
The world is three dimensional. That statement is so obvious that most of us never question how we perceive it. But, in fact, each of our eyes captures a flat image – just like a camera. And it’s only in our brains that the magic of forming a 3D perception from those two flat images occurs.
Today, we increasingly ask digital systems to interact with the 3D world – whether it’s to interpret gestural controls, perform facial recognition, or automatically pilot a vehicle. To accomplish these tasks, we need to give them at least some of our ability to perceive depth.
Depth Sensing
There are two basic approaches used for 3D (depth) sensing in digital imaging: triangulation and time-of-flight (ToF) measurements. Sometimes these techniques are even combined.
Triangulation is based on geometry. One form of triangulation – binocular vision – is the way that human 3D (stereoscopic) vision operates. We have two eyes separated horizontally. This means that each eye sees the world from a slightly different angle. This difference in perspective creates a parallax, meaning a shift in the position of an object relative to the background depending on which eye you’re looking with. Our brains then use this parallax information to sense the depth (distance) of objects in our field of view and create our single, unified, 3D perception of the world.
But stereo vision can be dependent on lighting conditions and requires distinct textured surfaces. These make it difficult to reliably implement. Instead, computer vision systems use another form of triangulation that relies on “structured light.” This is just a fancy name for projecting a pattern (like a series of lines or numerous spots of light) onto an object and analyzing the distortion of this pattern from a slightly different angle. This takes much less processing power than recreating true binocular vision, and it enables a computer to rapidly calculate depth information and reconstruct a 3D scene.
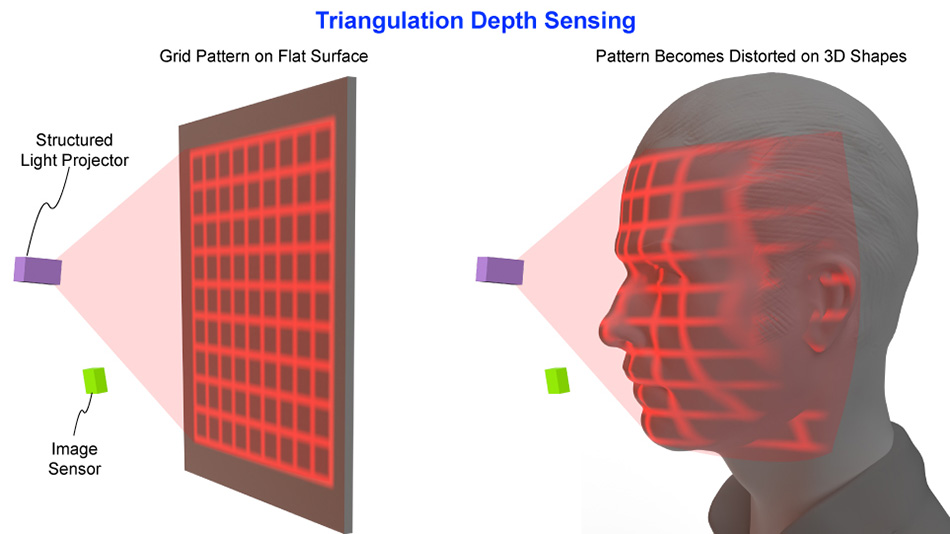
In one form of triangulation depth sensing a structured light pattern is projected onto the scene, and an imaging system analyzes the distortion of this pattern to derive depth information for the illuminated area.
Triangulation methods excel in high-resolution mapping of surfaces. They work best over shorter distances, making them very useful for tasks like facial recognition.
Time-of-Flight imaging (ToF) comes in two different forms. In “direct Time-of-Flight" (dToF) the scene is illuminated with pulses of light, and the system measures the time it takes for the reflected light pulses to return. Since the speed of light is known, this return time can be directly converted into distance. If this calculation is performed independently for each pixel in an image, then a depth value at each point in the scene can be derived.
The second form of ToF is "indirect Time-of-Flight" (iToF). Here, the illumination is a continuous, modulated signal. The system measures the phase shift of this modulation in the returned light. This provides the data used to calculate object distances.
ToF technology shines in its ability to measure over larger areas and distances quickly. This makes it ideal for tasks like room scanning in virtual reality headsets or obstacle detection for robot navigation.
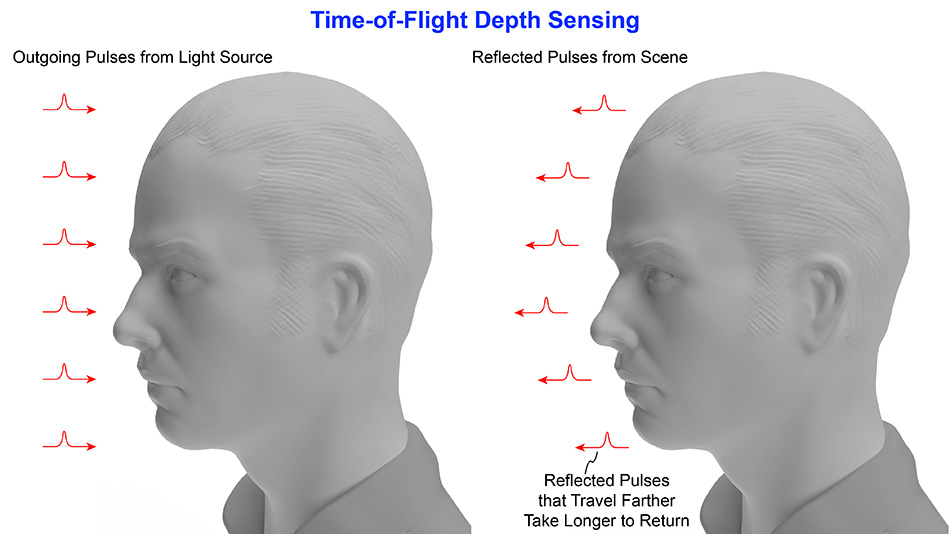
Direct Time-of-Flight sensing measures the round-trip travel time of light pulses and converts the time intervals into distance measurements.
3D Sensing Light Source Requirements
The characteristics of the light source are crucial in determining the effectiveness and accuracy of both triangulation and ToF 3D sensing methods. Each application has unique illumination requirements, although they also have certain common needs.
Triangulation benefits from a coherent light source. This provides greater flexibility in terms of the patterns that can be created. It also enables them to form higher-resolution structured patterns and to maintain pattern integrity over longer distances.
A triangulation light source also needs to have stable beam-pointing characteristics. Any fluctuations in these can lead to inaccurate depth measurements.
ToF systems require a light source capable of emitting either short, precise pulses of light (dToF) or continuous output that can be modulated at high frequencies (iToF). The precision in pulse timing and modulation frequency with short rise and fall times is paramount for accurate distance measurement.
ToF systems, especially those using flood illumination to cover large areas or long distances, generally require higher output powers than triangulation systems. This ensures that the return light will have sufficient intensity to be detected, and that the system will function well with high levels of ambient light.
As output power scales up, the need for power efficiency (the ratio of optical output power to input electrical power) becomes more important. Efficiency becomes particularly relevant for portable (battery operated) devices.
Lasers for Better Depth Sensing
Diode lasers provide a better match to these requirements (for both triangulation and TOF sensing) than any other light source. Light emitting diodes (LEDs) have been deployed in the past for some 3D sensing uses because they’re readily available and relatively low cost. But, as the demands on 3D sensing system performance and efficiency increase, LEDs can’t really measure up.
One reason is that diode lasers offer a unique combination of narrow spectral output, coherence, and brightness. Together, these make them ideally suited for creating precise, high-contrast, stable structured light patterns.
The narrow spectral output of lasers also makes it much easier to filter out ambient light in the detection system. This improves performance for all types of sensing systems in bright sunlight or other well-lit scenes.
The higher brightness of diode lasers further boosts the power of the returned signal. Especially for TOF applications, this translates into shorter shutter times, higher frame rates, and improved ability to see objects which aren’t highly reflective, and, again, improved performance in brightly lit scenes. LEDs, with their lower intensity, struggle to achieve the same level of detail and depth resolution.
Additionally, diode lasers boast a significant advantage over LEDs in terms of power consumption and size. Their ability to emit a strong signal from a small form factor makes them ideal for compact, battery-operated devices.
Finally, diode lasers can be switched or modulated at much faster rates than LEDs. This rapid modulation allows for advanced ToF techniques which can deliver improved accuracy.
Coherent Shines in 3D Sensing
Coherent is the world leader in illumination sources for 3D sensing – we’ve shipped over 2 billion units! Our portfolio includes lasers, optics, and complete illumination modules.
Our sources comprise vertical cavity surface emitting lasers (VCSELs), VCSEL arrays, and edge-emitting diode lasers (EELs).
In particular, VCSEL arrays – typically with output at 940 nm – have become the dominant light source for 3D sensing today. There are several reasons for this. One is that the light exits a VCSEL from the top of the device, rather than from the side like in an EEL. This makes it easier to integrate them on a circuit board with other components. Also, VCSELs cost less than EELs at the power levels used in 3D sensing. As a result, EELs are typically only employed at longer wavelengths (>1200 nm) where VCSELs with good performance are not yet available. The key advantage of these longer wavelengths is more robust performance in bright sunlight (they allow virtually all sunlight to be filtered out) and enhanced eye safety (10X higher power levels are possible compared near-IR wavelengths).
Coherent has a mature platform for VCSEL and EEL fabrication based on 6-inch GaAs wafers. This has enabled us to become the volume leader in this technology and to consistently deliver devices with outstanding reliability and performance.
Light sources for 3D sensing are usually configured as either flood illuminators or pattern projectors. Flood illuminators provide homogeneous light coverage over a specific angle. They are used in applications like facial recognition and gesture detection where uniform light distribution over the entire field of view is key to measurement accuracy.
Pattern projectors are actually used for both triangulation and ToF systems. Combining light patterns with ToF measurements improves signal-to-noise ratio and reduces multipath-induced measurement errors. These are inaccuracies that occur when the light bounces off more than one surface before reaching the sensor.
In each case, optics are used to shape and transform the laser output to meet the exact requirements of the application. Producing a flood illuminator can usually be accomplished with relatively simple, low-cost, molded plastic lenses. But the demands for structured light sources are more stringent.
Coherent meets the needs for structured light illumination with diffractive optical elements (DOEs) and meta-optics. The latter utilize nanostructures – physical features that are smaller than the wavelength of the light – to alter its propagation properties. This can include changing the beam shape, divergence angle, and intensity distribution, as well as splitting the beam to create structured light patterns.
One great thing about Coherent meta-optics is that they can combine multiple optical functions – like beam collimation and splitting – into a single compact element. Doing this reduces the size and complexity of the optical system and also improves the overall performance of the 3D sensing module.
Another key differentiator for Coherent is our ability to engineer and vertically integrate an entire illumination module solution. This integration ensures that the light source, optics, driver IC and packaging are all optimized to work seamlessly together, providing our customers with a reliable, high-performance, yet cost-effective product that is ready for mass deployment in the most demanding applications.
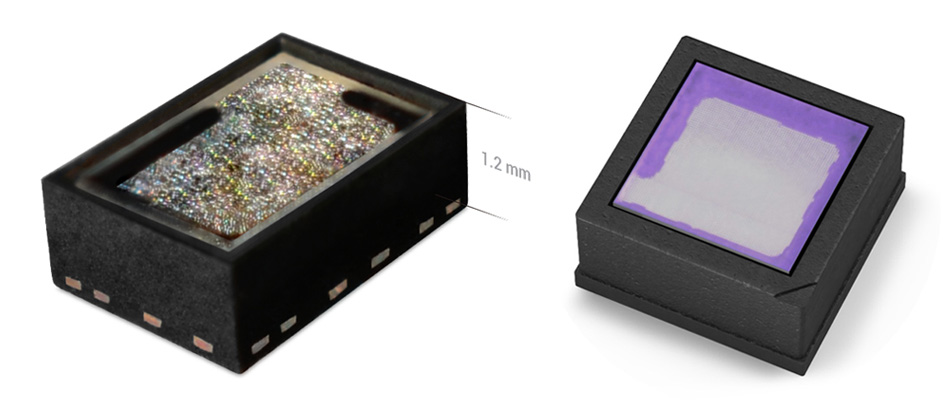
Coherent manufactures flood illumination and dot projection modules.
For example, our illumination modules for 3D sensing are engineered to minimize electronic parasitics (unwanted capacitance, inductance, or resistance). This is essential for delivering the nanosecond pulse width and sub-nanosecond rise/fall times on which high-accuracy ToF sensors depend. Additionally, we emphasize the importance of eye safety, integrating features that monitor the integrity of the device and the output power to ensure that light output always stays within established safe levels under all circumstances. This is imperative for consumer devices.
When you put it all together, Coherent provides more than just superior components: You get a team who understands the intricacies of 3D sensing technology and can deliver a complete, integrated solution that enhances device performance and ensures user safety. By partnering with us, you can rely on our legacy of excellence and our continuing development of photonic innovations.
Learn more about Coherent products for 3D sensing.