PCBデパネリングとは?
PCBデパネリングとは、同時製造に使用された大きなパネルから個々のプリント回路基板(PCB)を取り外すプロセスを指します。PCBは通常、効率化のために複数の基板を含むパネルで製造されるため、この工程はPCB製造において非常に重要なステップです。製造工程が完了した後、これらの個々の基板は、目的のエレクトロニクス機器に使用するために分離(デパネリング)する必要があります。
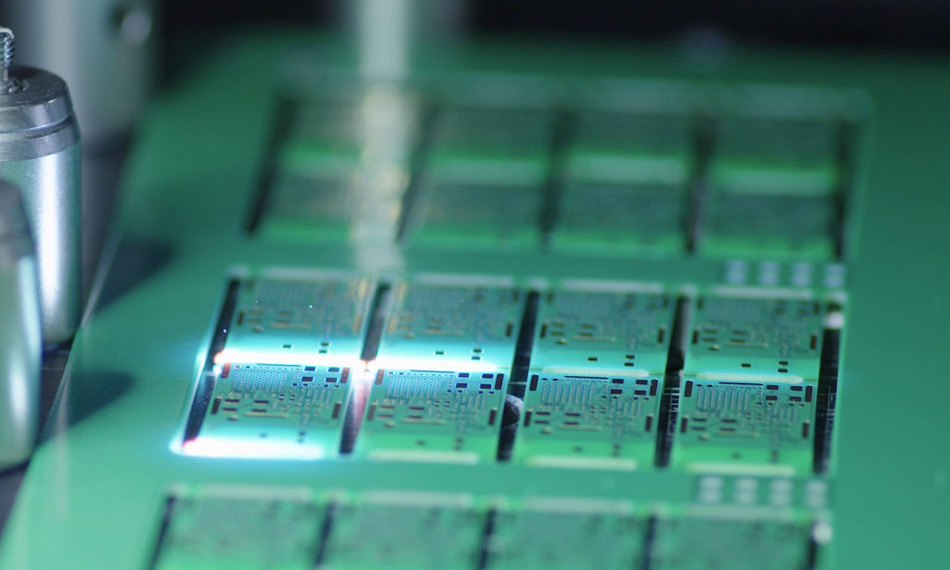
PCBの材料、厚さ、構成が技術的に変化したことで、従来の機械的な切断やデパネリング(パネル剥離)の方法からレーザベースの加工方法への移行が進んでいます。しかし、PCBデパネリング用レーザがすべて同じように作られているわけではありません。切断の特性と品質、特に熱影響部(HAZ)の点では、さまざまなレーザによって大きな違いがあります。これは、PCB上に回路をどの程度密に配置できるかを決定するため、加工方法の利用率に影響します。また、回路の機能や、防水やEMIシールドのような下流工程にも影響を与える可能性があります。このドキュメントでは、Coherentで開発された新しいナノ秒レーザと関連する切断加工方法についてご紹介します。これは、現在入手可能な他の製品に比べ、HAZを大幅に低減したレーザPCBデパネリングを実現するものです。
レーザによるデパネリングのニーズの進化
ほんの数例を挙げると、スマートフォン、各種ウェアラブル機器、VR機器、車載用センサー、ホームオートメーション機器など、小型化されたエレクトロニクス機器の継続的な市場成長は、高密度で高性能なプリント基板のニーズに直結しています。これらのデバイスは、旧世代のマイクロエレクトロニクスよりも物理的に小型で複雑であるだけでなく、消費者からは、よりエネルギー効率が高く(バッテリーの寿命が長く)、より安価であることが求められています。
PCB技術の面では、これがいくつかのトレンドを牽引してきました。その中には、より薄い従来の基板の使用、フレックス回路の広範な実装、より厚い導電層、低κ誘電体の利用拡大(後者は特に5G技術向け)などがあります。コストを考慮すると、加工方法利用率の向上も必要になります。具体的には、歩留まりを向上させるために、パネル上の基板同士を近づけることです。
デパネリングに関しては、このようなことから、カーフ幅をますます狭くし、切断工程の寸法精度を高める必要があります。また、PCBの機能エリアと切断部の物理的な距離が近いということは、機械的なストレスや熱によるものであれ、切断工程が周囲の材料や回路に影響を及ぼしてはならないということです。その後の洗浄工程が必要となるようなゴミの発生を最小限に抑えることも必要条件です。
これらの制約があるため、ルーター、のこぎり、型抜き、パンチング、スコアリング、ピザ切断など、従来の機械的なPCBデパネリング方法は実用的でなく、費用対効果も低くなっています。このため、切断速度の低下は通常避けられないものの、先に述べた事実上すべての分野で大きなメリットをもたらすレーザ切断への移行が進んでいます。
レーザ切断を理解する
レーザデパネリングは、もちろん以前から使われていました。ただし、さまざまなレーザベース技術を理解し、区別することが重要です。当初の実装では、遠赤外線を放出するCO2レーザを利用していました。この技術ではバルク材を加熱して切断するため、HAZが大きくなります。また、紫外線の波長が短いのに比べ、この長い波長はスポットサイズを小さく集光できないため、カーフ幅が大きくなります。
10年以上前、LD励起固体レーザ(DPSS)、ナノ秒パルス幅、周波数3倍レーザが、PCBのデパネリングに有効な光源として登場しました。紫外線(355 nm)出力と十分なパルスエネルギーにより、比較的「低温」のアブレーション加工方法による材料除去が実現します。つまり、CO2レーザよりもHAZがはるかに小さく(それでも目立ちますが)、破片や再キャスト材の発生が大幅に少ないレーザです。市販されている光源のパルスエネルギーと繰り返し周波数は、CO2レーザほどではありませんが、経済的に実行可能な送り速度での切断を可能にします。この技術の主な利点を表にまとめました。
利点 |
説明 |
機械的精度 |
切断は、狭いカーフ幅とともに、非常に高い寸法精度と精密さで行われます。これにより、PCB上のニアアクティブフィーチャをカットする能力が向上します。 |
ストレスフリー |
切断プロセス自体は振動や摩擦がなく、PCBに機械的変形や剥離を生じさせたり、残留応力をもたらすことはありません。これにより、切断工程で後から故障メカニズムが導入されるのを防ぐことができます。 |
低いHAZ |
UVレーザアブレーション加工方法は本質的に「低温」であるため、基板のバルク変化を防ぎ、回路ショートにつながる可能性のある回路トレースの溶融を回避できます。このプロセスでは破片の発生が最小限に抑えられるため、その後の洗浄工程が不要になり、またその後の回路故障の可能性も最小限に抑えられます。組み立てた基板のデパネリングも可能です。 |
オペレーションの柔軟性 |
レーザビームは、コンピューター制御で動く慣性のないツールで、その出力を急速に変化させることができます。これにより、いくつかの利点が得られます。第一に、事実上どんな形状でも切断できるため、PCB設計者は従来の切断方法によるフォームファクターの制限から解放されます。次に、切断パターンをソフトウェア制御で変更できるため、生産における迅速な切り替えが可能になり、小ロット生産もコスト効率よく行えます。最後に、レーザの出力を変化させることで、1つのツールで切断できるだけでなく、さまざまな作業を行うことができます。これにはマーキングや彫刻、金属アブレーションなどが含まれます。 |
材質に依存しない |
紫外線はほとんどすべてのPCB材料に強く吸収されます。これにより、従来の銅張りのフレックスラミネート、フレックス材料(より厚い導電層を組み込んだものまで)、さまざまな低κ誘電体を含む、事実上すべてのPCB構造と互換性のある加工方法となります。 |
表1. UVレーザによるPCB切断の主な特徴と利点
CoherentのAVIA LXとレーザデパネリングの最新技術
レーザデパネリングが多くの利点をもたらすことは明らかですが、PCBメーカーは、冒頭で述べたような市場原理がもたらすサイズ、材料、コストに関するこれまで以上に厳しい課題に対応するため、すでにこの技術を限界まで押し進めています。特に、ナノ秒パルス幅のUV LD励起固体レーザで、HAZと加工屑の形成をさらに低減し、切断品質を向上させることは、活発な開発分野となっています。
この取り組みを支援するために、Coherentのアプリケーション研究では、ナノ秒パルス幅、高パルスエネルギー、UV LD励起固体レーザ(AVIA LX)を使用して、さまざまなPCB材料や組み合わさった材料を切断した場合の結果と加工余地を調査しました。Coherentのチームは、この研究に基づき、新しいPCB切断方法を開発しました。この方法は、HAZの減少、切断エッジの品質向上、カーフ幅の減少、生産スループットの向上を実現することがすでに実証されています。
この技術の重要な要素の1つは、加工面に照射されるレーザパルスのタイミングと空間的位置を、熱の蓄積を避けるように制御する独自の方法です。このアプローチでは熱損傷がないため、厚い材料(1 mm以上)を切断する際に、大幅に高いパルスエネルギーを持つレーザを使用することができます。
高いパルスエネルギーの利点は、厚い材料の切断に使用される従来の方式を採用する必要がなくなることです。具体的には、横方向にずらした一連のスクライブで「V溝」を作ります。「V溝」の形状は、高アスペクト比のカットを行う際に、ビームが材料に深く食い込むのを避けるために必要です。これでは出力が低下し、アブレーション効率が低下します。しかし、AVIA LXとこの新しいパルスタイミングアプローチを組み合わせることで、400 μJという高いパルスエネルギーを利用して、 同じラインに沿って繰り返しスクライブすることができます(横方向の変位、すなわち「V溝」はありません)。その結果、切断速度が向上し、カーフ幅が大幅に減少します。
パルスエネルギーが高いほど、加工面におけるレーザ焦点の許容範囲も広がります。具体的には、低いパルスエネルギーレーザを使用する場合、材料が貫通したらビームの焦点を移動させ、最小集光スポットサイズを切断が発生する深さで常に正確に維持する必要があります。これは、材料のアブレーションしきい値を超えるのに十分なレーザフルエンスを得るために必要です。しかし、実際にこれを行うには、物理的にプリント基板を上にずらす必要があり、プロセスが遅くなるか、3軸スキャナ(フォーカス機能を持つもの)を採用する必要があり、装置のコストと複雑さが増します。
AVIA LXはパルスエネルギーが高いため、プリント基板の中間にレーザを集光して切断することができます。これは、レーザの焦点が完全に合っていなくても、アブレーションに十分なレーザフルエンスがあるからです。その利点は、切断の高速化とシステムの複雑性の軽減です。
改善の例を以下の写真に示します。この例は、この用途用に現在市販されているタイプのUV LD励起固体レーザを使用した場合と、AVIA LXとこの新しいアプローチで同じ素材を加工した場合の、銅トレースのある厚さ1.6 mmのプリント基板のカットを比較したものです。この技術で加工された基板は、切り口がきれいになり、銅トレースの切り口が大幅に改善されています。
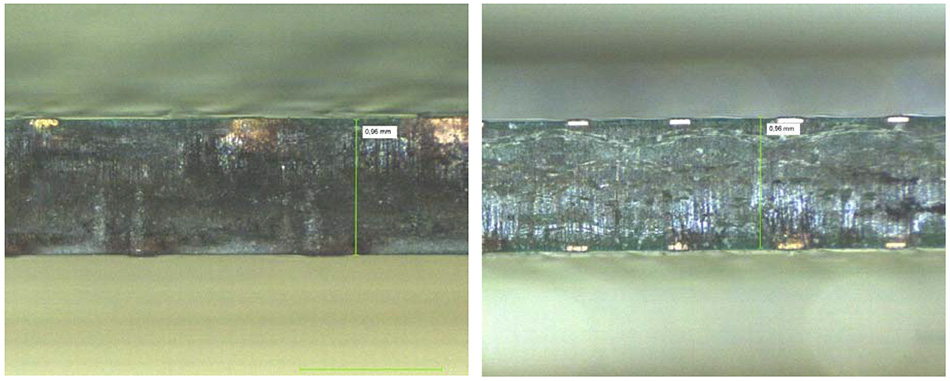
図1. (左)他社製UV LD励起固体レーザ、(右)Coherentの新たな切断工程を採用している高パルスエネルギーUV LD励起固体レーザ(AVIA LX)で切断した1.6 mm厚プリント基板の断面。後者の方がエッジの品質が良く、銅トレースのカットがよりきれいになります。
次の一連の画像は、Coherentの方法を利用することでカーフ幅が減少したことを示しています。
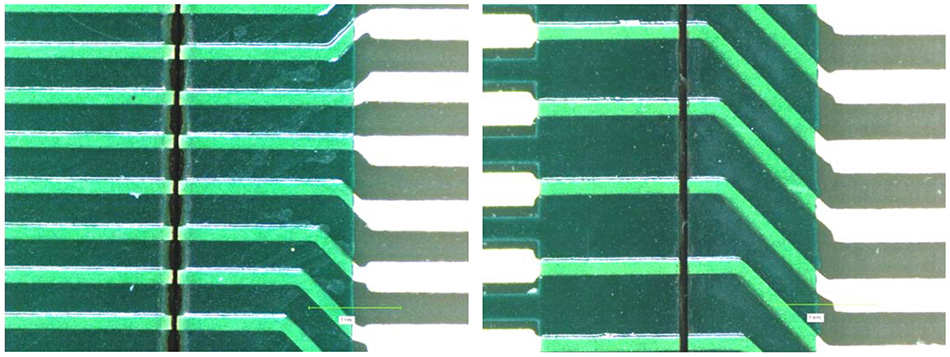
図2. (左)他社製UV LD励起固体レーザ、(右)高パルスエネルギーUV LD励起固体レーザ(AVIA LX)を使用して切断された0.95 mm厚プリント基板の上面図。右の方がカーフ幅が狭く一貫しています。
次の写真は、AVIA LXが多層PCB(グラスファイバー層を含む)の切断において、切り屑を最小限に抑え、トレンチ幅を狭くし、HAZを大幅に減少させたことを示しています。
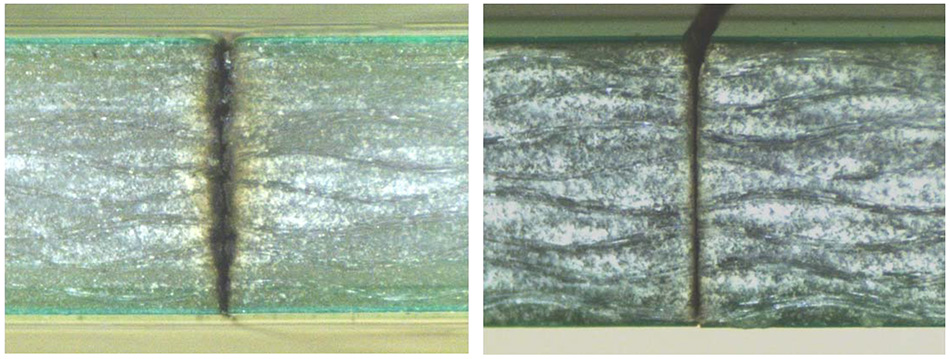
図3. 1.6 mm厚の多層プリント基板(グラスファイバー層あり)を、(左)他社製UV LD励起固体レーザ、(右)高パルスエネルギーUV LD励起固体レーザ(AVIA LX)を用いてCoherentの新方式で切断した断面。これにより、トレンチチャネルが狭くなり、HAZが小さくなります。
従来、ポリイミドやEMIシールド金属箔のレーザ切断では、HAZが広いため切断ラインで剥離が発生していました。この場合、材料にダメージを与えないよう、パルスエネルギーを低くする必要があります。しかし、同じパルシングアプローチを用いた場合、熱蓄積をなくし、HAZとカーフ幅の減少という同じ利点をもたらします。その結果、下流の生産工程でより高い収率を達成できるようになり、生産コストが削減されます。
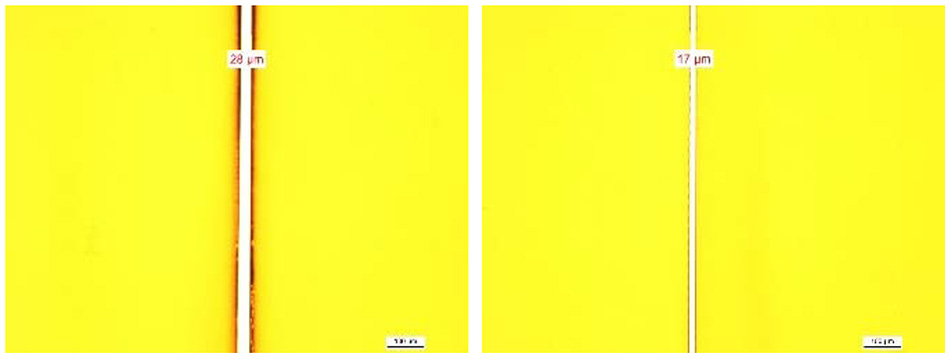
図4. 厚さ100 μm のポリイミド金属箔の上面図。左側は競合他社のUV LD励起固体レーザを使用して得られた切断結果で、広い切断溝とかなりの熱影響ゾーンがあります。右の切断結果はAvia LX UV LD励起固体レーザで達成されました。これにより、トレンチチャネルが狭くなり、HAZが小さくなります。
最後に、Coherentのパルス法で可能な、フレックスPCBを処理する際のより低いパルスエネルギーでのHAZの低減とスループットの向上を、次の写真に示します。
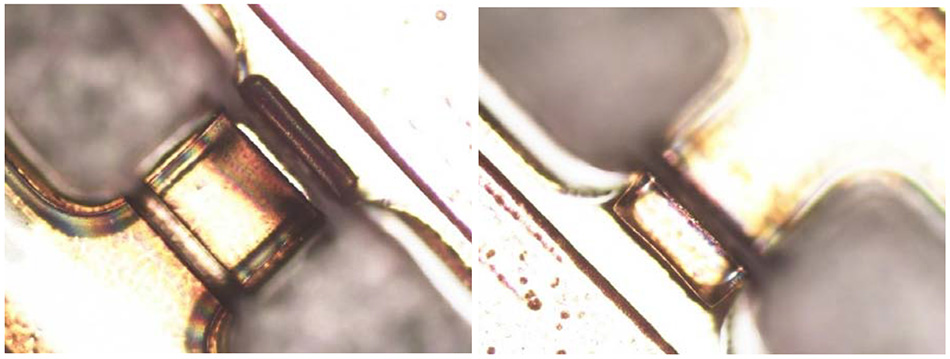
図5. (左)他社製UV LD励起固体レーザと(右)高パルスエネルギーUV LD励起固体レーザ(AVIA LX)で切断した0.13 mm厚FPCBの上面図。この結果、HAZははるかに小さくなり、高い切断速度(11 mm/秒に対して13 mm/秒)でこれを達成することができました。
実用的な高パルスエネルギーUV LD励起固体レーザ
従来の厚いPCB材料の場合、Coherentパルス制御法を実際に実施するには、従来市販されていたものよりも高いパルスエネルギーを持つUV LD励起固体レーザ光源が必要です。このニーズに応えるため、Coherentは、最大500 μJのパルスエネルギーを生成できる20W(355 nm)、固体、ナノ秒パルス幅レーザのAVIA LXを開発しました。
Coherent AVIA LXの詳細をご覧ください。