Was ist PCB-Depaneling?
Beim PCB-Depaneling handelt es sich um den Prozess des Entfernens einzelner Leiterplatten (PCBs) aus einem größeren Panel, das für die gleichzeitige Fertigung verwendet wurde. Dieser Prozess ist ein wichtiger Schritt bei der Leiterplattenherstellung, da Leiterplatten aus Effizienzgründen typischerweise in einem Panel mit mehreren Platinen hergestellt werden. Nachdem der Fertigungsprozess abgeschlossen wurde, müssen diese einzelnen Platinen voneinander getrennt werden, um in den jeweiligen elektronischen Geräten verwendet werden zu können.
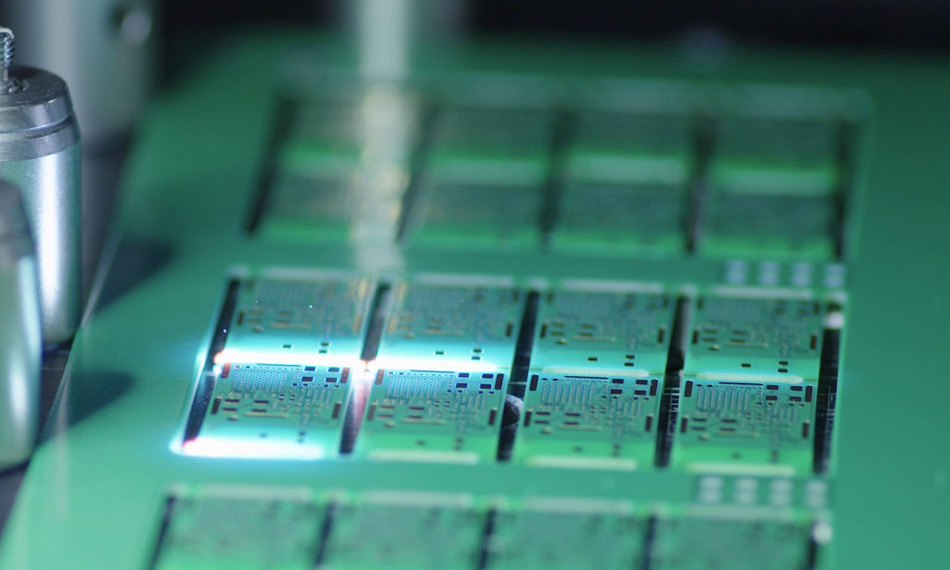
Technologische Veränderungen bei den Materialien, der Dicke und der Zusammensetzung von Leiterplatten führen zu einer Abkehr vom herkömmlichen mechanischen Schneid- und Depaneling-Verfahren hin zu laserbasierten Verfahren. Aber nicht alle Laser zum PCB-Depaneling sind gleich. Es gibt erhebliche Unterschiede zwischen den verschiedenen Lasern in Bezug auf die Schneideigenschaften und die Qualität, insbesondere im Hinblick auf die Wärmeeinflusszone (WEZ). Dies wiederum wirkt sich auf die Prozessauslastung aus, da diese bestimmt, wie eng die Schaltungen auf einer Leiterplatte platziert werden können. Auch kann dies eine Auswirkung auf die Funktionalität der Schaltungen und nachgelagerte Prozesse wie Wasserdichtigkeit oder EMI-Abschirmung haben. In diesem Dokument werden ein neuer Nanosekundenlaser und ein dazugehöriges Schneidverfahren vorgestellt, das bei Coherent entwickelt wurde. Dieses ermöglicht das Depaneling per Laser mit einer wesentlich geringeren Wärmeeinflusszone im Vergleich zu anderen derzeit erhältlichen Produkten. .
Der wachsende Bedarf an laserbasiertem Depaneling
Das anhaltende Marktwachstum von miniaturisierten elektronischen Geräten, darunter Smartphones, verschiedene Wearables, VR-Geräte, Kfz-Sensoren und Hausautomatisierungsgeräte, um nur einige Beispiele zu nennen, führt direkt zu einem Bedarf an dichteren und leistungsfähigeren Leiterplatten. Diese Geräte sind nicht nur physisch kleiner und komplexer als die vorherige Generation der Mikroelektronik, es gibt auch eine Nachfrage der Verbraucher, sie energieeffizienter (für eine längere Batterielebensdauer) und billiger zu machen.
Im Bereich der Leiterplattentechnologie hat dies zu mehreren Trends geführt. Dazu gehören die Verwendung dünnerer herkömmlicher Leiterplatten, die großflächige Einführung flexibler Schaltungen, dickere leitende Schichten und die verstärkte Verwendung von Dielektrika mit niedrigem κ-Wert (letzteres insbesondere für die 5G-Technologie). Auch aus Kostengründen ist eine bessere Prozessauslastung erforderlich. Konkret bedeutet dies, dass die Leiterplatten auf einer Platine näher beieinander liegen und ein höherer Ertrag besteht.
Für das Depaneling erfordert dies zunehmend schmalere Schnittspaltbreiten und eine höhere Maßgenauigkeit beim Schneidprozess. Die räumliche Nähe des Schnitts zu den Funktionsbereichen der Leiterplatte bedeutet auch, dass der Schneidprozess das umgebende Material oder die Schaltkreise nicht beeinträchtigen darf, weder durch mechanische Belastung noch durch Hitze. Ein weiteres Erfordernis ist die minimale Produktion von Rückständen, die einen nachfolgenden Reinigungsschritt erforderlich machen könnten.
Aufgrund all dieser Einschränkungen sind herkömmliche mechanische Verfahren zum Depaneling, wie z. B. Fräsen, Sägen, Stanzen, Ritzen, in Stücke schneiden usw., weniger praktikabel und kostengünstig. Dies führt zu einer Hinwendung zum Laserschneiden, das in praktisch jedem der genannten Bereiche erhebliche Vorteile bietet, allerdings in der Regel auf Kosten einer geringeren Schneidgeschwindigkeit.
Das Scheiden mit Laser verstehen
Das laserbasierte Depaneling wird natürlich schon seit einiger Zeit eingesetzt. Es ist jedoch wichtig, die verschiedenen laserbasierten Technologien zu verstehen und voneinander zu unterscheiden. Ursprünglich wurden CO2-Laser verwendet, die im fernen Infrarot emittieren. Bei dieser Technologie wird das Grundmaterial erhitzt, was zu einer erheblichen Wärmeeinflusszone führt. Außerdem kann diese lange Wellenlänge im Vergleich zu kürzeren UV-Wellenlängen nicht auf eine so kleine Spotgröße fokussiert werden, was zu einer größeren Schnittfugenbreite führt.
Vor über einem Jahrzehnt entwickelte sich der diodengepumpte Festkörperlaser (DPSS) mit Nanosekunden-Pulsbreite und frequenzverdreifachter Lasertechnik zu einer brauchbaren Quelle für das Leiterplatten-Depaneling. Dieser Laser bietet ultraviolette Strahlung (355 nm) mit ausreichender Pulsenergie, um die Materialentfernung durch einen relativ „kalten“ Abtragungsprozess zu ermöglichen. Das heißt, mit einer viel kleineren (aber immer noch spürbaren) Wärmeeinflusszone als beim CO2-Laser und mit einer wesentlich geringeren Produktion von Abfall und Nachgussmaterial. Die Pulsenergie und die Wiederholrate der handelsüblichen Quellen ermöglichen das Schneiden mit wirtschaftlich vertretbaren Vorschubgeschwindigkeiten, wenn auch nicht so schnell wie der CO2-Laser. Die Hauptvorteile dieser Technologie sind in der Tabelle zusammengefasst.
Vorteil |
Erläuterung |
Mechanische Präzision |
Das Schneiden erfolgt mit sehr hoher Maßgenauigkeit und Präzision sowie einer schmalen Schnittfugenbreite. Dies verbessert die Fähigkeit, nahezu aktive Elemente auf der Leiterplatte auszuschneiden. |
Stressfrei |
Der Schneidprozess selbst ist vibrations- und reibungsfrei und vermeidet eine mechanische Verformung oder Delaminierung der Leiterplatte sowie Eigenspannungen. Dadurch wird die Einführung nachträglicher Fehlermechanismen durch den Schneidprozess vermieden. |
Niedrige HAZ |
Die inhärente „kalte“ Beschaffenheit des UV-Laserabtragsverfahrens verhindert Veränderungen am Substrat und vermeidet das Schmelzen von Leiterbahnen, was zu einem Kurzschluss führen könnte. Durch die minimale Verschmutzung des Prozesses entfällt die Notwendigkeit nachfolgender Reinigungsschritte, was wiederum die Möglichkeit eines späteren Stromkreislaufdefekts minimiert. Das Verfahren ermöglicht sogar die Trennung von montierten Platten. |
Operative Flexibilität |
Der Laserstrahl ist ein trägheitsloses Werkzeug, das sich computergesteuert bewegt und dessen Leistung schnell variiert werden kann. Dies bietet mehrere Vorteile. Erstens kann praktisch jede beliebige Form geschnitten werden. Somit sind Leiterplattendesigner von den Beschränkungen des Formfaktors befreit, die durch herkömmliche Schneidmethoden auferlegt werden. Außerdem können die Schneidmuster softwaregesteuert variiert werden, was eine schnelle Umstellung der Produktion ermöglicht und auch die Herstellung von Kleinserien kostengünstig macht. Schließlich ermöglicht die unterschiedliche Laserleistung, dass ein einziges Werkzeug neben dem reinen Schneiden noch viele andere Vorgänge ausführen kann. Dazu können Beschriftungen/Gravuren und Metallabtragungen gehören. |
Materialunabhängig |
Ultraviolettes Licht wird von fast allen Materialien einer Leiterplatte stark absorbiert. Dadurch ist der Prozess mit praktisch jeder Leiterplattenkonstruktion kompatibel, einschließlich herkömmlicher kupferkaschierter Flexlaminate, Flexmaterialien (sogar solchen mit dickeren leitfähigen Schichten) und verschiedenen Low-κ-Dielektrika. |
Tabelle 1. Hauptmerkmale und Vorteile des UV-Laser-basierten Leiterplattenschneidens
AVIA LX und der neueste Fortschritt im laserbasierten Depaneling von Coherent
Obwohl das laserbasierte Depaneling zweifellos zahlreiche Vorteile bietet, stoßen Leiterplattenhersteller bereits jetzt an die Grenzen dieser Technologie bei Ihren Bestrebungen die immer strengeren Größen-, Material- und Kostenanforderungen zu erfüllen, die sich aus den eingangs erwähnten Marktkräften ergeben. Insbesondere die Erzielung einer weiteren Reduzierung der Wärmeeinflusszone und der Trümmerbildung sowie die Verbesserung der Schnittqualität mit UV-DPSS-Lasern mit Nanosekunden-Pulsbreite sind ein aktiver Entwicklungsbereich.
Um diese Bemühungen zu unterstützen, hat die Anwendungsforschung bei Coherent die Ergebnisse und den Prozessraum der Verwendung eines UV-DPSS-Lasers mit Nanosekunden-Pulsbreite und hoher Pulsenergie (AVIA LX) zum Schneiden einer Vielzahl von Leiterplattenmaterialien und Materialkombinationen untersucht. Basierend auf dieser Arbeit entwickelte das Team bei Coherent eine neue Methode zum Schneiden von Leiterplatten, die bereits nachweislich eine geringere Wärmeeinflusszone, eine höhere Schneidkantenqualität, eine geringere Schnittfugenbreite und einen höheren Produktionsdurchsatz liefert.
Ein Schlüsselelement dieser Technik ist eine proprietäre Methode zur Steuerung des Timings und der räumlichen Positionierung der an die Arbeitsoberfläche abgegebenen Laserpulse, sodass ein Wärmestau vermieden wird. Da bei diesem Ansatz keine thermischen Schäden auftreten, ist es möglich, beim Schneiden dickerer Materialien (1 mm und mehr) einen Laser mit wesentlich höherer Pulsenergie zu verwenden.
Der Vorteil einer höheren Pulsenergie besteht darin, dass die herkömmliche Methode zum Schneiden dickerer Materialien nicht mehr verwendet werden muss. Konkret geht es dabei um die Herstellung einer Reihe seitlich versetzter Anreißer, um eine „V-Nut“ zu erzeugen. Die „V-Nut“-Geometrie ist erforderlich, um ein Abschneiden des Strahls zu vermeiden, wenn er bei einem Schnitt mit hohem Seitenverhältnis weiter in das Material eindringt. Dies würde seine Leistung verringern und somit die Abtragseffizienz einschränken. Allerdings kann der AVIA LX in Verbindung mit diesem neuartigen Puls-Timing-Ansatz Pulsenergien von bis zu ~400 μJ nutzen, um wiederholt entlang derselben Linie zu ritzen (keine seitliche Verschiebung oder „V-Nut“). Das Ergebnis ist ein schnelleres Schneiden und eine deutlich reduzierte Schnittfugenbreite.
Eine höhere Pulsenergie erhöht auch die Laserfokustoleranz auf der Arbeitsoberfläche. Insbesondere bei der Verwendung eines Lasers mit niedrigerer Pulsenergie ist es notwendig, den Fokus des Strahls beim Eindringen in das Material zu verschieben, damit die minimale Fokuspunktgröße immer genau in der Tiefe beibehalten wird, in der der Schnitt erfolgt. Dies ist notwendig, um eine ausreichende Laserfluenz zu erreichen, um über die Materialabtragungsschwelle zu gelangen. In der Praxis erfordert dies jedoch entweder eine physische Verschiebung der Leiterplatte nach oben, was den Prozess verlangsamt, oder den Einsatz eines dreiachsigen Scanners (einer mit Fokussierfunktion), was die Kosten und die Komplexität der Ausrüstung erhöht.
Die höhere Pulsenergie des AVIA LX ermöglicht es, den Laser einfach auf einen Punkt in der Mitte der Leiterplatte zu fokussieren und den Schnitt durchzuführen. Der Grund dafür ist, dass die Laserfluenz für die Abtragung auch weit außerhalb des perfekten Fokus des Lasers ausreicht. Der Vorteil ist ein schnelleres Schneiden und eine geringere Systemkomplexität.
Ein Beispiel für die Verbesserungen sind die folgenden Fotos, die Schnitte in eine 1,6 mm dicke Leiterplatte mit Kupferbahnen zeigen. Diese wurden mit dem derzeit für diese Anwendung kommerziell erhältlichen UV-DPSS-Lasertyp durchgeführt und stehen im Vergleich zu demselben Material, das mit dem AVIA LX und diesem neuen Ansatz bearbeitet wurde. Die mit dieser Technik bearbeitete Leiterplatte weist eine sauberere Schnittkante und eine deutliche Verbesserung der Schnittkanten der Kupferbahnen auf.
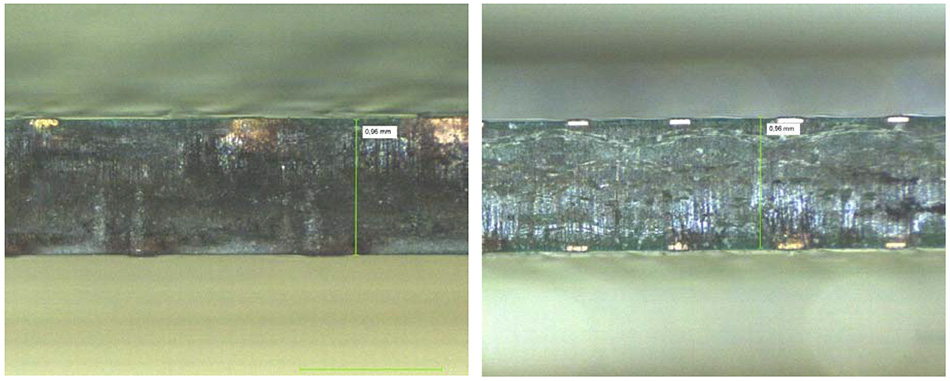
Abbildung 1. Querschnitte einer 1,6 mm dicken Leiterplatte, geschnitten mit (links) einem UV-DPSS-Laser eines Wettbewerbers und (rechts) einem UV-DPSS-Laser mit hoher Pulsenergie (AVIA LX), der das neue Schneidverfahren von Coherent verwendet. Letzteres sorgt für eine bessere Kantenqualität und einen saubereren Schnitt der Kupferbahnen.
Die nächste Reihe von Bildern zeigt die Verringerung der Schnittfugenbreite, die durch den Einsatz des Verfahrens von Coherent erreicht wurde.
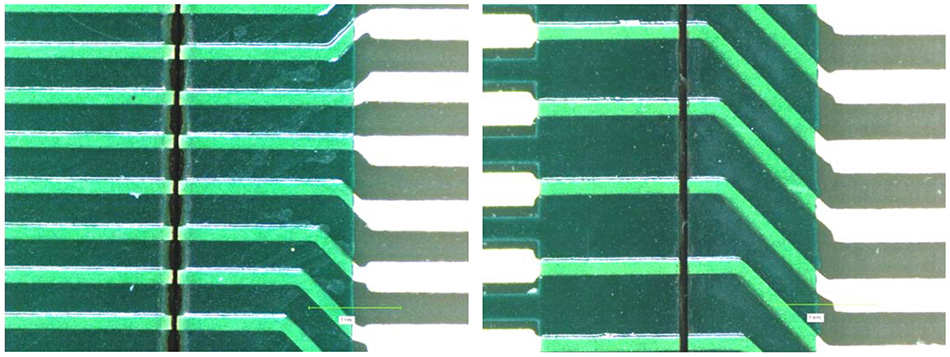
Abbildung 2. Draufsicht auf eine 0,95 mm dicke Leiterplatte, die mit einem UV-DPSS-Laser eines Wettbewerbers (links) und einem UV-DPSS-Laser mit hoher Pulsenergie (AVIA LX) geschnitten wurde, der einen schmaleren und gleichmäßigeren Schnittspalt erzeugt.
Die nächste Reihe von Fotos zeigt, wie der AVIA LX das Schneiden von mehrlagigen Leiterplatten (mit Glasfaserlagen) mit minimalen Ablagerungen, geringer Schnittbreite und erheblich reduzierter Wärmeeinflusszone ermöglicht.
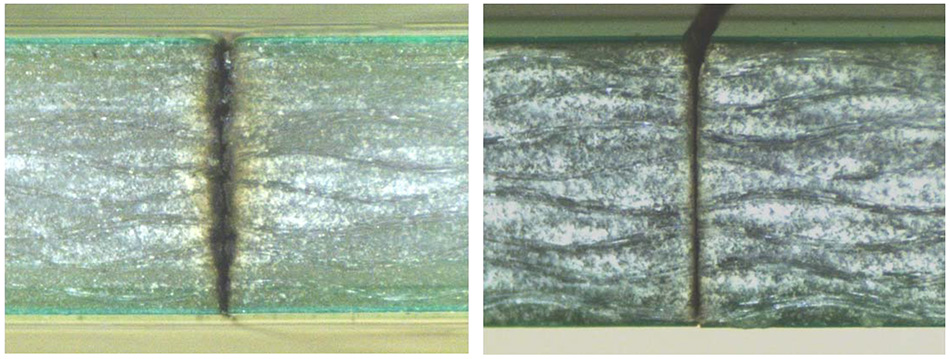
Abbildung 3. Querschnitte einer 1,6 mm dicken, mehrlagigen Leiterplatte (mit Glasfaserschichten), geschnitten mit einem (links) UV-DPSS-Laser eines Wettbewerbers und (rechts) einem UV-DPSS-Laser mit hoher Pulsenergie (AVIA LX) mit dem neuen Verfahren von Coherent. Dies führt zu einem engeren Schneidkanal und einer kleineren Wärmeeinflusszone.
In der Vergangenheit kam es beim Laserschneiden von Polyimid- und EMI-Abschirmfolien aufgrund der breiten Wärmeeinflusszone zu einer gewissen Delamination an der Schneidlinie. In diesem Fall ist es notwendig, eine niedrigere Pulsenergie zu verwenden, um eine Beschädigung des Materials zu vermeiden. Es wird jedoch derselbe pulsierende Ansatz verwendet, um den Wärmestau zu beseitigen und die gleichen Vorteile einer reduzierten Wärmeeinflusszone und Schnittspaltbreite zu erzielen. Dies wiederum senkt die Produktionskosten, da die nachgelagerten Produktionsprozesse eine höhere Ausbeute erzielen können.
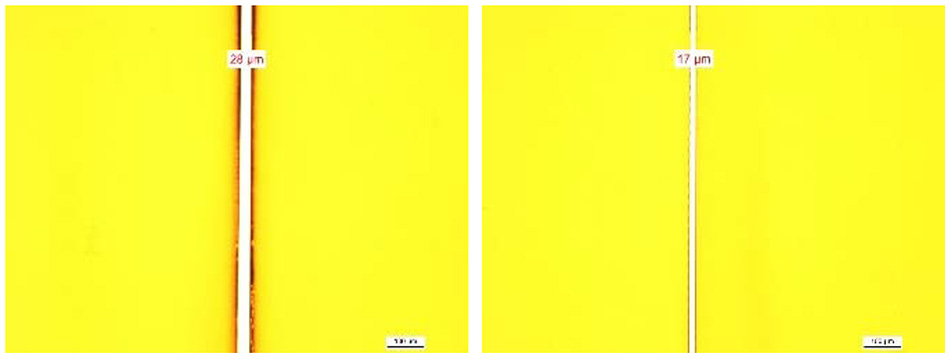
Abbildung 4. Die Draufsicht auf eine 100 μm dicke Polyimidfolie zeigt links ein Schnittergebnis, das mit einem UV-DPSS-Laser eines Wettbewerbers erzielt wurde, der eine breite Schnittfuge und eine beträchtliche Wärmeeinflusszone aufweist. Das Schnittergebnis auf der rechten Seite wurde mit dem Avia LX UV DPSS-Laser erzielt. Dies führt zu einem engeren Grabenkanal und einer kleineren Wärmeeinflusszone.
Die nächsten Fotos zeigen die geringere Wärmeeinflusszone und den höheren Durchsatz, die mit dem Pulsverfahren von Coherent möglich sind, jedoch mit geringerer Pulsenergie bei der Bearbeitung einer flexiblen Leiterplatte.
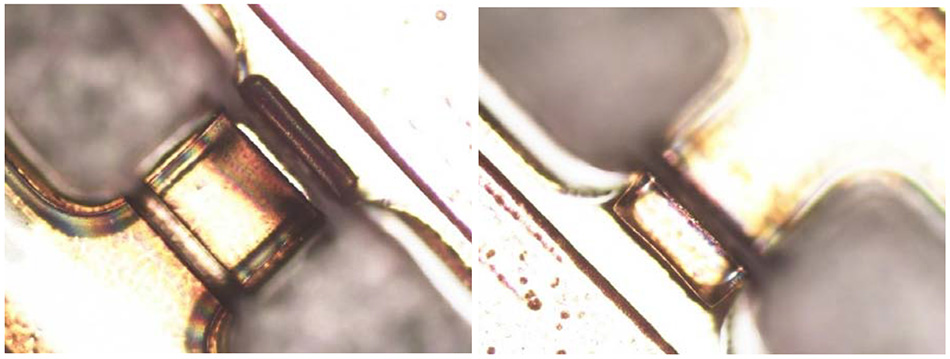
Abbildung 5. Draufsicht auf 0,13 mm dicke FPCBs, die mit einem (links) UV-DPSS-Laser eines Wettbewerbers und (rechts) einem UV-DPSS-Laser mit hoher Pulsenergie (AVIA LX) geschnitten wurden. Dies führte zu einer viel kleineren Wärmeeinflusszone und dies bei einer höheren Schneidgeschwindigkeit (13 mm/s im Vergleich zu 11 mm/s).
Praktische UV-DPSS-Laser mit hoher Pulsenergie
Für herkömmliche dicke Leiterplattenmaterialien erfordert die praktische Umsetzung der Pulssteuerungsmethode von Coherent eine UV-DPSS-Laserquelle mit höherer Pulsenergie als bisher auf dem Markt erhältlich. Um diesen Bedarf zu decken, hat Coherent den AVIA LX entwickelt, einen Festkörperlaser mit 20 W (bei 355 nm) und Nanosekunden-Pulsbreite, der eine Pulsenergie von bis zu 500 μJ erzeugen kann.
Erfahren Sie mehr über den Coherent AVIA LX.