什么是 PCB 板切割?
PCB 板切割是指从用于同步制造的较大面板上移除单个印刷电路板 (PCB) 的工艺。此工艺是 PCB 制造中的关键步骤,因为为了提高效率,PCB 通常在包含多块板的面板中生产。在制造过程完成后,这些单独的电路板需要进行分离或切割,以用于其预期用途的电子设备。
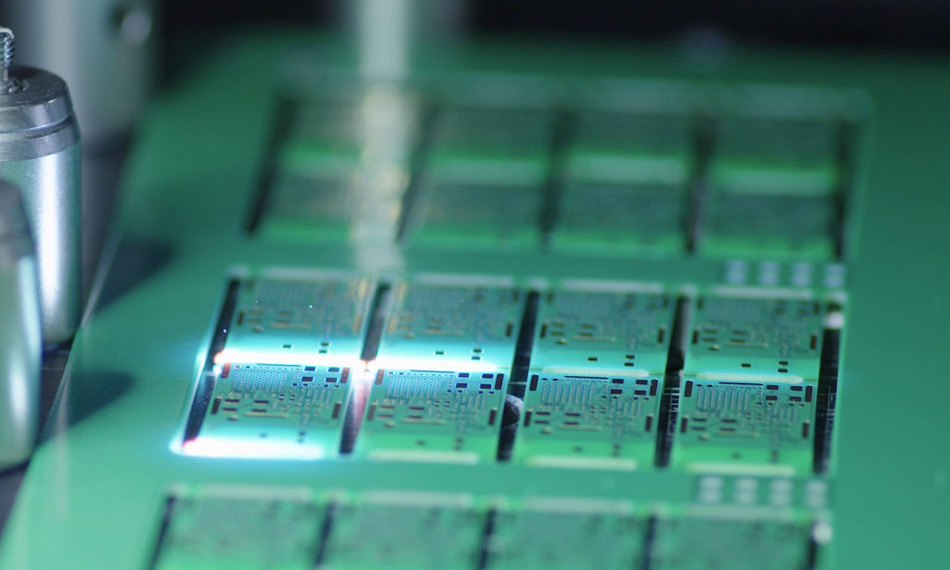
PCB 的材料、厚度和成分正在经历技术变革,促使人们从传统的机械切割和板切割方法转向基于激光的工艺。但并非所有用于 PCB 板切割的激光器都是一样的。各种激光器在切割特性和质量方面存在明显差异,特别是在热影响区 (HAZ) 方面。这反过来又会影响工艺利用率,因为它决定了 PCB 上的电路间距,并且还会影响电路功能和下游工艺,例如防水或 EMI 屏蔽。本文档介绍了 Coherent 高意开发的新型纳秒激光器和相关切割工艺,与其他现有产品相比,该激光器能够显著减小激光 PCB 板切割过程中产生的热影响区 (HAZ)。
不断变化的激光板切割需求
智能手机、各种可穿戴设备、VR 设备、汽车传感器和家庭自动化设备等小型电子设备市场持续不断地增长,直接引发了对密度更高、性能更强的 PCB 的需求。比起上一代微电子设备,这些设备不仅尺寸更小、结构更复杂,而且还需要具有更高的能效(以延长电池寿命)和更低廉的价格以满足消费者的需求。
这在 PCB 技术领域掀起了多种浪潮,其中包括使用更薄的传统电路板、大规模应用柔性电路、增加导电层厚度以及增加低介电常数物质的应用(后者尤其适用于 5G 技术)。改进工艺利用率还有控制成本方面的考虑。具体来说就是,面板上的电路板间距会更小,以提升产能。
对板切割而言,所有这些都需要不断降低的切口宽度并提高尺寸精度。要缩短切割位置与 PCB 功能区域的距离,还要求切割过程不能对周围的材料或电路产生影响,无论是机械应力影响还是发热影响。另外还要求尽量减少碎片的产生,这可能需要后续的清洁步骤。
在这些要求的限制下,刨槽机、锯、模切、冲孔、刻画和披萨切等传统机械 PCB 板切割方法的实用性和成本效益大大降低。这推动了激光切割的发展,前文提到的几乎每个领域都因采用激光切割获得了巨大的好处,尽管切割速度通常有所降低。
了解激光切割
激光板切割技术投入使用已有一段时间,但了解和区分各种基于激光的技术非常重要。最早投入使用的是二氧化碳激光器,此激光器可以发射远红外激光。这种技术通过加热疏松材料来实现切割,过程中会产生明显的热影响区。此外,与波长较短的紫外线相比,这种激光的波长更长,聚焦的光斑尺寸无法做到紫外线光斑那样小,这意味着切口宽度会更大。
十多年前,二极管泵浦固态 (DPSS) 纳秒脉冲宽度三倍频激光器开始出现,为 PCB 板切割提供了实用的激光源。这种激光器可以提供具有足够脉冲能量的紫外线 (355 nm) 输出,从而通过相对较“冷”的烧蚀工艺来去除材料。也就是说,相比于 CO2 激光器,这种激光器的热影响区要小得多(但仍然很明显),并且碎片和重铸材料的产生量也大大减少。市售光源的脉冲能量和重复频率能够实现以经济实用的进给速度进行切割,尽管速度比起二氧化碳激光器还是慢一些。下表总结了该技术的主要优点。
优点 |
解释 |
机械精度 |
切割的尺寸精度非常高,并且切口宽度很窄。这增强了在 PCB 上切割近活动特征的能力。 |
无应力 |
切割工艺本身不会产生振动和摩擦,不会造成 PCB 的机械变形或分层,也不会引入残余应力。这样,切割工艺就不会引入后续故障。 |
HAZ 低 |
紫外激光烧蚀工艺固有的“冷”特性可防止基板发生大幅变化,并避免可能导致短路的电路迹线熔化。该工艺产生的碎片非常少,因此无需后续清洁步骤,并且同时还可极大地减少发生后续电路故障的可能。该工艺甚至可以对组装好的板进行切割。 |
操作灵活性 |
激光束是一种依靠计算机控制移动的无惯性工具,其功率可以快速变化。这带来了几项优势。首先,激光束几乎可以切割出任何形状,使 PCB 设计人员摆脱了使用传统切割方法需要考虑的形状因素限制。其次,可以通过软件控制切割图案,实现灵活敏捷的生产过程,并使短期制造具有成本效益。最后,由于激光功率可变,因此使用单个工具就可以执行除了切割之外的其他各种操作,包括打标/雕刻和金属烧蚀。 |
不依赖于特定材料 |
几乎所有 PCB 材料都会大幅吸收紫外线。因此该工艺几乎能兼容所有 PCB 结构,包括传统的覆铜柔性层压板、柔性材料(甚至包含较厚导电层的材料)和各种低介电常数物质。 |
表 1:基于紫外激光的 PCB 切割的主要特点和优势
AVIA LX 和 Coherent 高意激光板切割技术的最新进展
虽然激光板切割技术明显具有众多优势,但 PCB 制造商已经充分发挥了这项技术的潜力,以满足开头部分中市场提出的日益严格的尺寸、材料和成本挑战。特别指出,进一步减小热影响区并减少碎片形成,以及提高纳秒脉冲宽度 UV DPSS 激光器的切割质量,是当前热门的发展领域。
为了帮助实现这一目标,Coherent 高意的应用研究探索了使用纳秒脉冲宽度、高脉冲能量、UV DPSS 激光器 (AVIA LX) 切割各种 PCB 材料和材料组合的结果和工艺空间。基于这项工作,Coherent 高意团队开发了一种新的 PCB 切割方法,该方法已被证实可以减小热影响区、提高切割边缘质量、减小切口宽度并提高生产量。
该技术的一个关键要素是一种专有方法,用于控制传送到工作表面的激光脉冲的时间和空间定位,同时避免产生热积聚。由于这种方法不存在热损伤,因此在切割较厚的材料(1 mm 及以上)时可以使用具有更高脉冲能量的激光。
使用更高脉冲能量的优点在于无需采用那些用于切割较厚材料的传统方案。具体来说,就是进行反复横向划线来获得“V 形槽”。在进行高纵横比切割时,“V 形槽”几何形状可以确保光束穿透材料,避免中途被阻断。这会降低其功率,从而限制烧蚀效率。然而,将 AVIA LX 与这种新颖的脉冲定时方法相结合,就可以利用高达约 400 μJ 的脉冲能量沿着同一条线重复划线(无横向位移或“V 形槽”)。这样,切割速度会更快并且切口宽度显著减小。
较高的脉冲能量还增加了工作表面的激光聚焦公差。具体来说,当使用较低脉冲能量的激光器时,需要在穿透材料时移动光束的焦点,以便随着切割的进行,能够始终精确地在切口深度上保证较小的聚焦光斑尺寸。为了获得足够的激光通量以便超过材料烧蚀阈值,这样做是必要的。然而,实际执行此操作需要移动 PCB,这会减慢流程,或者使用三轴扫描仪(具有聚焦功能),这会增加设备成本和复杂性。
AVIA LX 的脉冲能量较高,可以将激光简单地聚焦在 PCB 中间的一点上并进行切割。这是因为即使激光没有充分聚焦,其能量密度也足以对材料进行烧蚀。这样做的好处是切割速度更快,并降低了系统复杂性。
下面的照片中采用两种方式对带有铜迹线的 1.6 mm 厚 PCB 进行切割,一种方式是采用可用于此应用的商用 UV DPSS 激光器类型,另一种方式则采用 AVIA LX 和上述新方法,通过比较二者的结果展示了改进效果。结果显示,采用这种技术处理的电路板具有更干净的切割边缘,并且铜迹线的切割边缘得到了显著改善。
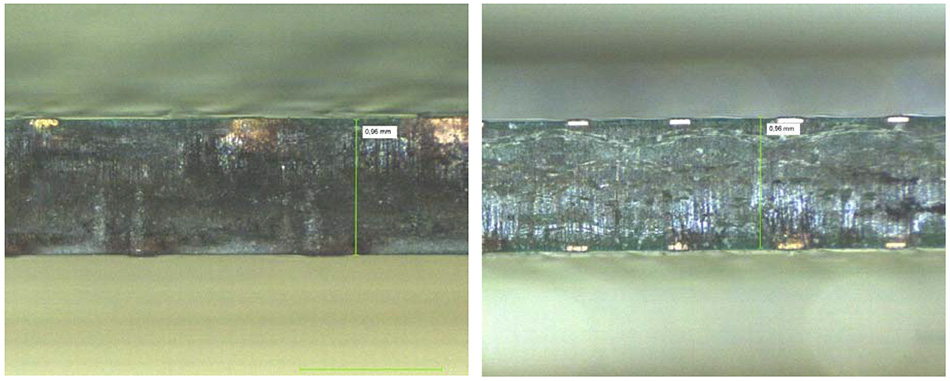
图 1:切割 1.6 mm 厚 PCB 得到的横截面,左侧为使用竞争对手的 UV DPSS 激光器的效果,右侧为使用具有全新 Coherent 高意切割工艺的高脉冲能量 UV DPSS 激光器 (AVIA LX) 的效果。后者的边缘质量更好,铜迹线切割效果更干净。
下一组图像展示了利用 Coherent 高意方法实现更小的切口宽度。
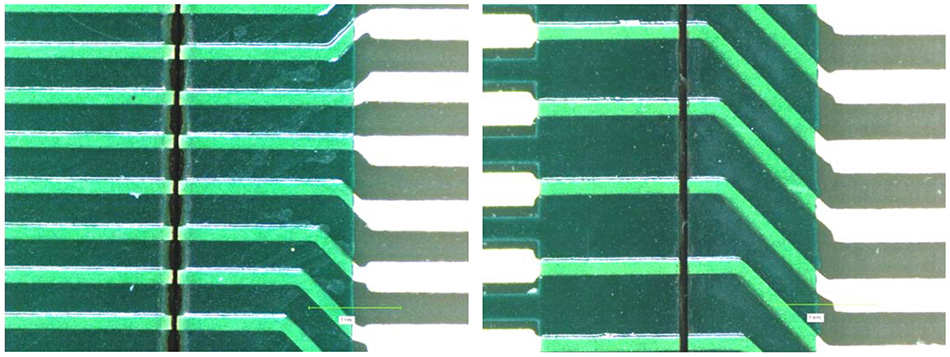
图 2:切割 0.95 mm 厚 PCB 的俯视图,左侧为使用竞争对手的 UV DPSS 激光器的效果,右侧为使用高脉冲能量 UV DPSS 激光器 (AVIA LX) 的效果,后者的切口更窄并且更加均匀一致。
下一组照片展示了 AVIA LX 如何能够在切割多层 PCB(带玻璃纤维层)时,大幅减少碎片、缩短沟槽宽度并显著减小热影响区。
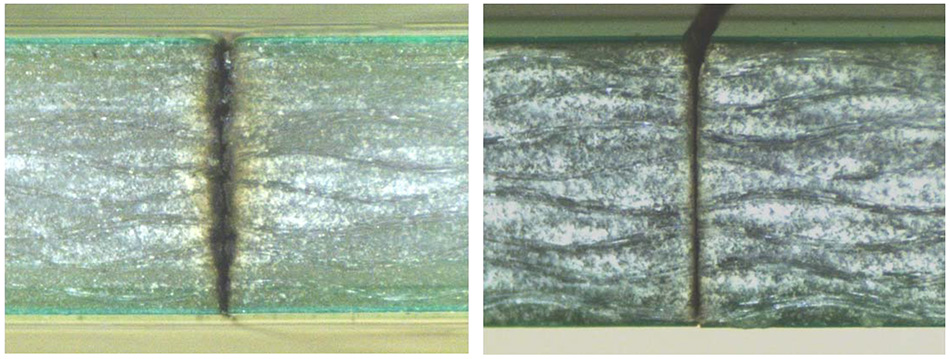
图 3:切割 1.6 mm 厚多层 PCB(带玻璃纤维层)得到的横截面,左侧为使用竞争对手的 UV DPSS 激光器的效果,右侧为使用具有全新 Coherent 高意方法的高脉冲能量 UV DPSS 激光器 (AVIA LX) 的效果,其沟槽通道更窄并且热影响区更小。
过去,对聚酰亚胺和 EMI 屏蔽箔进行激光切割时,由于热影响区较宽,在切割线处会产生一些分层。在这种情况下,有必要使用较低的脉冲能量以避免损坏材料。但是,使用上述脉冲方法可以在消除热积聚的同时减小热影响区和切口宽度。这样反过来还可以提升下游生产工艺的产能,从而降低生产成本。
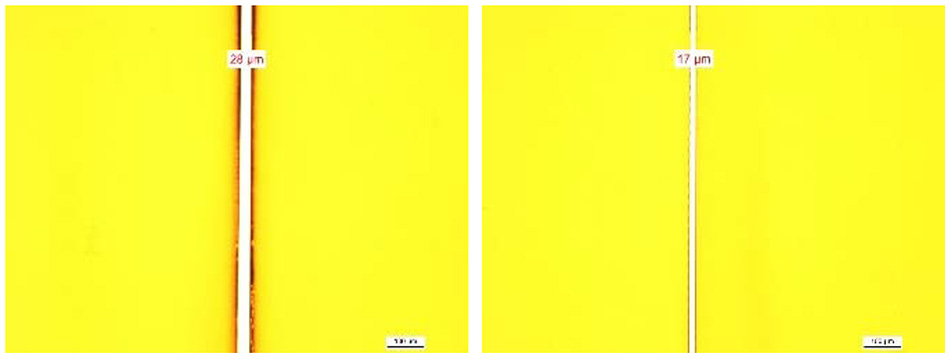
图 4: 100 μm 厚的聚酰亚胺箔的俯视图,左侧显示了使用竞争对手的 UV DPSS 激光器实现的切割结果,具有较宽的切口和较大的热影响区。右侧显示了使用 Avia LX UV DPSS 激光器实现的切割效果,其沟槽通道更窄并且热影响区更小。
最后一组照片展示了使用 Coherent 高意脉冲方法可以减小热影响区并提高生产量,但在处理柔性 PCB 时脉冲能量较低。
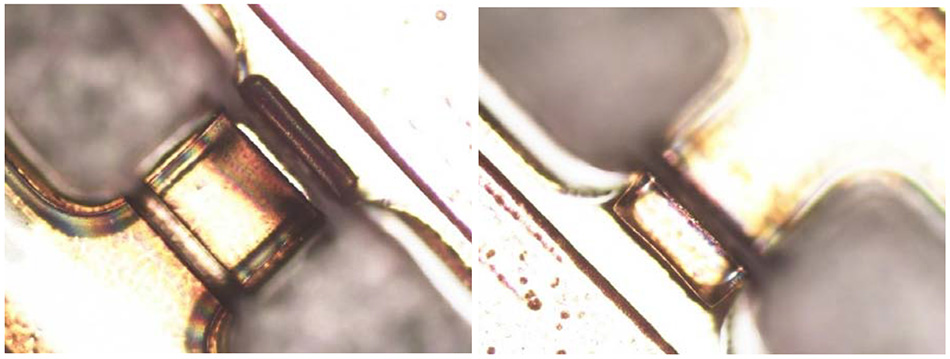
图 5. 切割 0.13 mm 厚 FPCB 的俯视图,左侧为使用竞争对手的 UV DPSS 激光器的效果,右侧为使用高脉冲能量 UV DPSS 激光器 (AVIA LX) 的效果,其热影响区更小,同时切割速度更高(13 mm/秒,前者为 11 mm/秒)。
实用的高脉冲能量 DPSS 紫外激光器
在实际生产中,要对传统的厚 PCB 材料实施 Coherent 高意脉冲控制方法,所采用的 UV DPSS 激光源需要比以往的市售产品具有更高的脉冲能量。为了满足这一需求,Coherent 高意开发了 AVIA LX,这是一款 20 W(355 nm)固态纳秒脉宽激光器,可产生高达 500 μJ 的脉冲能量。
详细了解 Coherent AVIA LX。