WHITE PAPER
A Medical Device Challenge: Welding Thin Wires of Dissimilar Metals
Overview
Stainless steel or nitinol are popular materials in medical devices. Application experts from Coherent have developed a process to safely weld thin wires made of such difficult-to-weld materials. This process can even be undertaken without destroying any plastic coating
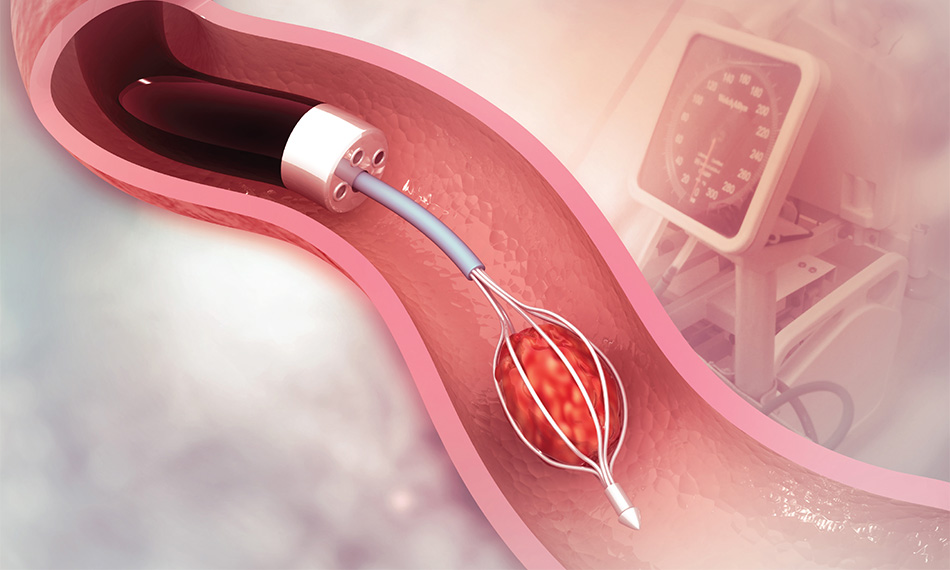
Micro-welding for medical devices
Laser welding is widely used in manufacturing medical devices like implants or endoscopic devices, often to join delicate parts. This becomes challenging if the joining partners are very thin wires made of difficult-to-weld materials. Typical materials are stainless steel, nitinol, or titanium because they are biocompatible, corrosion resistant, and easily sterilized. The challenge becomes even more difficult if a connection of dissimilar materials is intended. The laser is the preferred (if not the only) tool for this task. Welding such materials must not compromise their desirable physical properties, e.g., memory properties of nitinol.
When joining thin wires, a zero gap is required; they must be placed precisely against each other, since no filler is used and even a small gap can be too large for a reliable connection. Accordingly, the laser beam has to be precisely focused, too. While the first problem is solved with a fixture, the latter task requires the alignment of the laser focus position by means of an automated vision system.
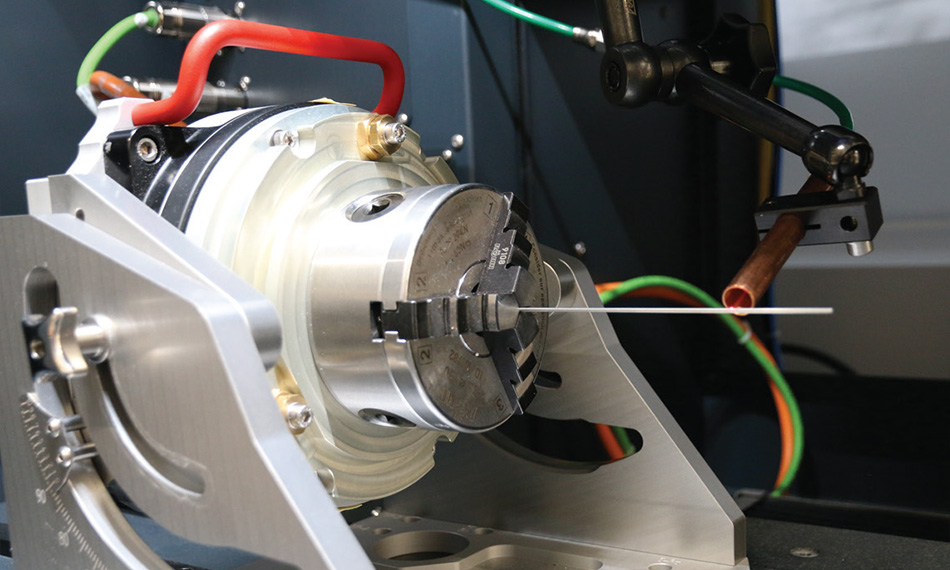
Figure 1: Setup for wire welding: The welding partners are fixed on a tube. Process gas is introduced through an 8 mm brass tube.
Welding with the ExactWeld 430
Welding thin wires with diameters as small as 25 µm (0.001”) requires a precise application of energy into the welding spot. The small pulse energy must be delivered in a controlled and reproducible way. The duration and temporal shape of such a laser pulse plays a crucial role.
The ExactWeld 430 machine from Coherent is a turnkey solution for precision laser welding that meets all these requirements. The workstation contains an integrated fiber laser source (Coherent StarFiber). Typical laser configurations for the ExactWeld range between 100 W and 600 W of output power. With a reproducible pulse modulation width, millijoule-energy laser pulses can be created. The laser beam is delivered by a galvoscanner or a fixed welding optics system. The workstation also includes a system for the control and supply of process gases. Just as important, the Class 1 laser housing complies with the latest ergonomic guidelines.
The vision system and illumination play a crucial role when processing parts with such tiny dimensions. When correctly optimized, the vision system enables automated processing, which means, for example, that a weld gap control stops the welding process if the gap is too large.
The wires are placed on a designated fixture before machining. This fixture is essential to keep the wires precisely in place during the welding process. The workstation is available with several options for the robotic part clamping of the fixtures. It supports up to four degrees of freedom (x, y, z, and rotation). User-friendly software controls the system, which also has factory automation capabilities (Industry 4.0/Internet-of-things ready) to enhance the quality, yields, and throughput of small metal part welding. All processed parts can be recorded for traceability: data may include a part number, time stamp, and certain images.
"When correctly optimized, the vision system enables automated processing, which means, for example, that a weld gap control stops the welding process if the gap is too large."
Laser welding of 25 µm nitinol and stainless-steel wires
In a recent study in the Coherent application labs, the ExactWeld 430 was used to join thin wires made of nitinol and stainless steel. Several material combinations were chosen:
1) nitinol/nitinol
2) stainless steel 316L/stainless steel 316L
3) stainless steel 316L/nitinol
The two different wires were fixed as coils on a liner, which was protected by a PTFE sleeve. A critical goal was to join the wires without damaging the PTFE sleeve. The diameters of the welding partners were equal; wires were tested with d = 25.4 µm as well as some larger diameters. The task was successfully accomplished without cutting through the PTFE sleeve in all cases.
Some key process details were as follows. The laser used a 2x beam expander with a focal length of 100 mm. The working distance was 0.5 mm with a theoretical spot diameter of 12.5 µm. For the diameter of 25.4 µm, the laser power for welding varied from 30 W to 50 W, depending on the material combination. The pulse duration was adjusted to between 0.035 and 0.05 ms, resulting in pulse energies between 1 mJ for welding and 2.5 mJ for cutting off the protruding wire. Argon was used as process gas for all the experiments with a flow of 15 l/min, a brass tube diameter of 8 mm, and a BAK 4 nozzle at a distance of 1.4 mm (see figure 2).
For welding thicker wires the pulse duration was increased while the actual laser power was kept at the same level as it was for welding thin wires. After welding the wires, the obstructing wire ends were cut off with a series of stronger pulses.
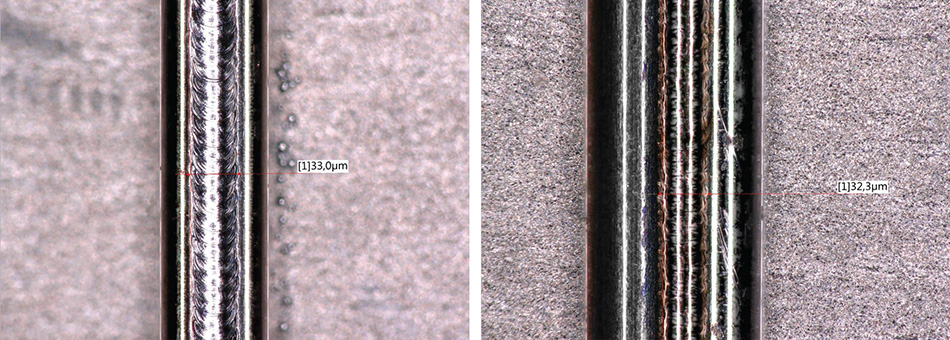
Figure 2: Welding of nitinol to nitinol (left) and nitinol to stainless steel welding (right).
Study results
The application trial showed that a 100 Watt StarFiber laser is sufficiently powerful to weld different wire combinations. The process window is fairly narrow for all types. It is smaller than 10 W in peak power and less than 10 µs in pulse duration. Higher values cut the wires while lower values do not connect them. The pulse shape that was used helped to make the process stable. It is essential that the wires touch and that the gaps cannot be bridged. Cutting the wires also carries the risk of welding the wire ends to the next wire. Therefore, positioning is critical.
Peak-Power [W] | Pulse Duration [ms] | Repetition Rate [Hz] | Speed [mm/min] | Remarks |
30 | 0.035 | 30 | 20 | Welding |
40 | 0.05 | 30 | - | Cutting |
Turnkey optimized solutions
The ExactWeld workstations are factory customized by applications experts from Coherent according to the desired applications. This customization includes not only the lasers, process control, and automated handling systems but also special fixtures, if necessary. Customers thus gain tremendous value from the collective knowledge and experience of the application engineers.
In this way, ExactWeld can be optimized for a wide variety of weld types and geometries. For contact welding, minimum welding spots with diameters down to 10 µm can be realized. For seam welding, small seam geometries can be achieved at high welding speeds. Free-form welding can also be programed. Thanks to the rotary stage, seal welding can be performed with no porosities and crack-free seams to provide for leakproof welding. For all systems, worldwide local service and spare parts supply are always readily available.
"Customers thus gain tremendous value from the collective knowledge and experience of the application engineers."
"Recent practical improvements in terms of reliability, performance, and ease of use, promise to make it more economically attractive as well."
Coherent is a vertically integrated manufacturer unmatched in our ability to also offer superior products at several different levels of integration. For example, the new ExactWeld 430 combines the industry-leading ExactSeries workstation platform, already proven in many applications, with a state-of-the-art Coherent StarFiber 100 to 600 laser sub-system. For traceability, every part can be logged with part and process details.
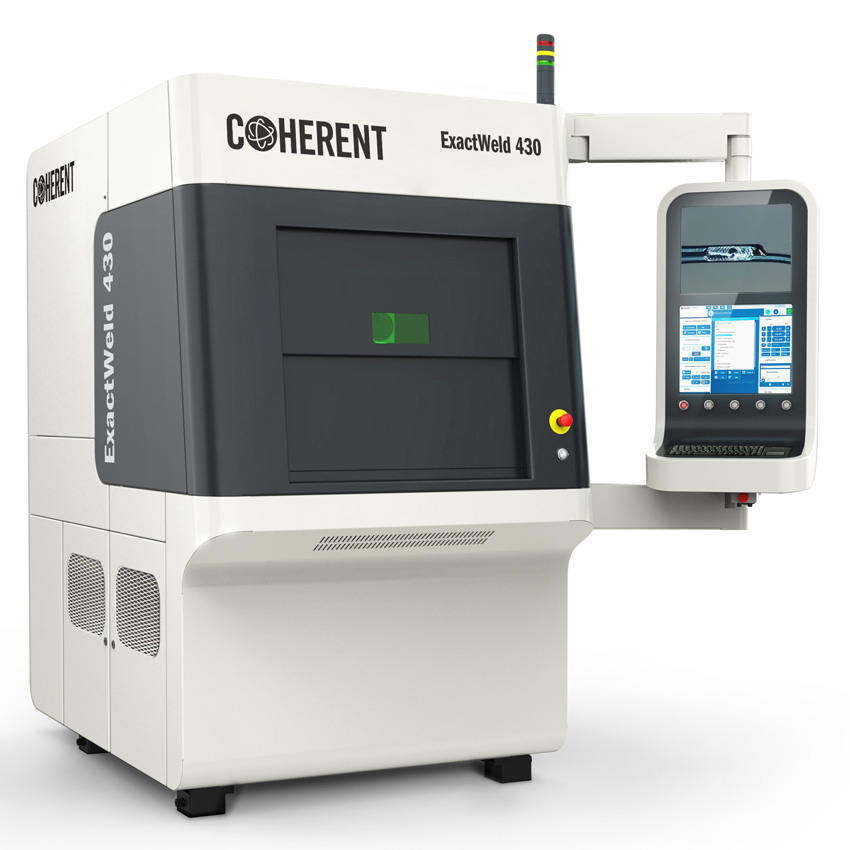
Figure 3: The ExactWeld 430 from Coherent is a class 1 laser device for automated welding tasks.
Summary
In conclusion, one of the most challenging welding applications in medical device manufacturing – the welding of wires as thin as 25.4 µm (0.001”) from nitinol and stainless steel – has been successfully accomplished. A special material such as nitinol requires a small process window; the pulse power, duration, and temporal shape must be generated reliably and repeatably. The small dimensions also demand precise positioning of the workpiece and the focused laser. The Coherent ExactWeld 430 has already established itself in a variety of other demanding welding applications in the medical device industry. It is now proved able to deliver the best solution for this difficult wire welding task. Recent practical improvements in terms of reliability, performance, and ease of use, promise to make it more economically attractive as well.