ホワイトペーパー
医療機器の課題 : 異種金属の細いワイヤーの溶接
概要
ステンレスやニチノールは、医療機器によく使われている材料です。 Coherentのアプリケーションエキスパートは、このような溶接が難しい材料で作られた細いワイヤーを安全に溶接するプロセスを開発しました。 このプロセスは、プラスチックコーティングに損傷を与えることなく実行することができます
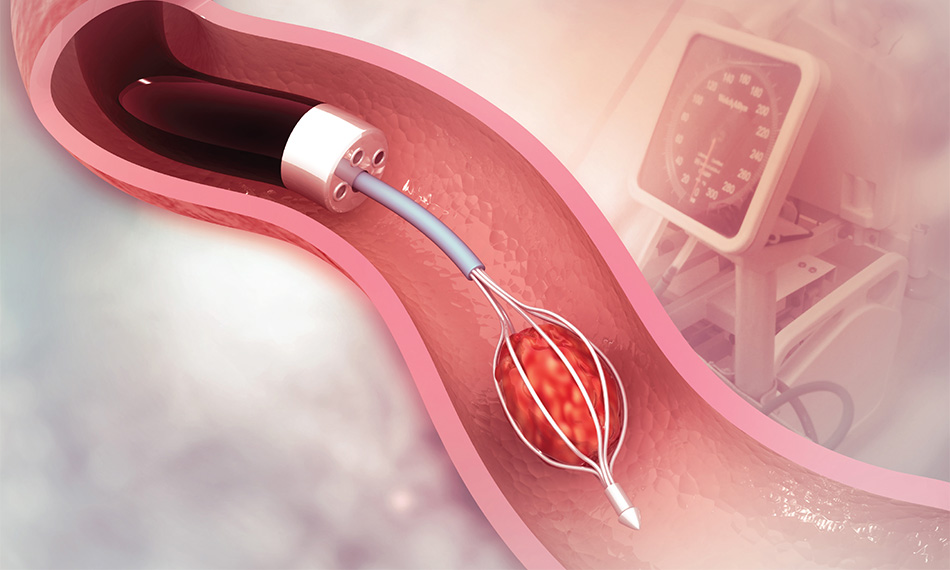
医療機器のマイクロ溶接
レーザ溶接は、インプラントや内視鏡装置などの医療機器の製造に広く使用されており、多くの場合、繊細な部品の接合に使用されます。 課題となるのは、接合相手が溶接の難しい材料で作られた非常に細いワイヤーである場合です。 典型的な材料は、生体適合性や耐食性があって容易に滅菌できる、ステンレス、ニチノール、またはチタンです。 さらに難しい課題となるのは、異種材料を接合しようとする場合です。 レーザは(唯一ではないにしても)この作業に適したツールです。 そのような材料を溶接する際、望ましい物理的特性(例 : ニチノールの形状記憶特性)を損なってはなりません。
細いワイヤー同士を接合する場合、ゼロギャップが求められます。フィラーを使用しない場合、小さなギャップであっても信頼性の高い接合をするためには大きすぎる可能性があるため、ワイヤーを互いに正確に配置する必要があります。 したがって、レーザビームも正確に焦点を合わせる必要があります。 最初の問題は治具で解決されますが、後者の作業では自動化ビジョンシステムによるレーザ焦点位置のアライメントが必要になります。
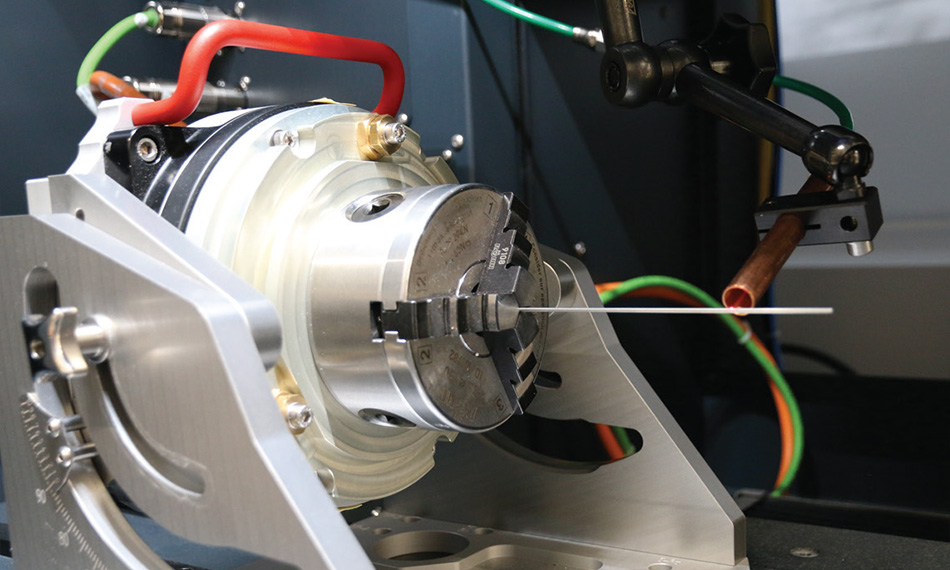
図1 : ワイヤー溶接の構成 : 溶接の対象はチューブに固定します。 プロセスガスは、8 mmの真ちゅう製チューブから導入されます。
ExactWeld 430による溶接
直径25 µm(0.001インチ)の細いワイヤー同士を溶接するには、溶接スポットにエネルギーを正確に加えることが必要です。 小さなパルスエネルギーは、制御され再現できる方法で供給しなければなりません。 このようなレーザパルスの幅と時間的形状は重要な役割を果たします。
CoherentのExactWeld 430は、これらすべての要件を満たす、高精度レーザ溶接のターンキーソリューションです。 ワークステーションには、内蔵のファイバーレーザ光源(Coherent StarFiber)が含まれています。 ExactWeldの典型的なレーザ構成の場合、出力の範囲は100 Wから600 Wです。 再現性のあるパルス変調幅で、mJレベルのエネルギーを持つレーザパルスを生成できます。 レーザビームは、ガルボスキャナーまたは固定溶接オプティクスシステムにより照射されます。 ワークステーションには、プロセスガスの制御と供給のためのシステムも含まれています。 また重要なこととして、クラス1のレーザハウジングは最新の人間工学的ガイドラインに準拠しています。
小さな寸法の部品を加工する場合、ビジョンシステムと照明が重要な役割を果たします。 適切に最適化すると、ビジョンシステムによるプロセス自動化が可能になります。たとえば、ギャップが大きすぎる場合、溶接ギャップの制御により溶接プロセスが停止します。
ワイヤーは加工前に指定の治具にセットされます。 この治具は、溶接プロセス中にワイヤーを正確に所定の位置に保つために不可欠です。 ワークステーションには、治具のロボット式部品クランプのオプションが幾つかあります。 最大4つの自由度(x、y、z、回転)をサポートします。 ユーザーフレンドリーなソフトウェアがシステムを制御します。このシステムには工場オートメーション機能(インダストリ4.0およびIoTに対応)が搭載されており、小型金属部品溶接の品質、歩留まり、スループットが向上します。 処理された部品はすべて、トレーサビリティのために記録することができます。 データには、部品番号、タイムスタンプ、特定の画像を含めることもできます。
「適切に最適化すると、ビジョンシステムによるプロセス自動化が可能になります。たとえば、ギャップが大きすぎる場合、溶接ギャップの制御により溶接プロセスが停止します。」
25 μmのニチノールワイヤーとステンレスワイヤーのレーザ溶接
Coherentアプリケーションラボの最近の研究では、ExactWeld 430を使用して、ニチノールとステンレスでできた細いワイヤーの接合が行われました。 以下の複数の材料の組み合わせが選ばれました。
1)ニチノール / ニチノール
2)ステンレス316L/ ステンレス316L
3)ステンレス316L/ ニチノール
PTFEスリーブで保護されているライナー上に、2種類のワイヤーがコイルとして固定されました。 重要な目標は、PTFEスリーブを損傷せずにワイヤーを接合することでした。 溶接材料の直径は互いに同じで、d = 25.4 μmのワイヤーと、幾つかのより大きな直径のワイヤーでテストされました。 すべてのケースでPTFEスリーブを切断することなく、作業は正常に完了しました。
プロセスの主な詳細は次の通りです。 レーザは、焦点距離100 mmの2倍ビームエキスパンダーを使用しました。作動距離は0.5 mmで、理論上のスポットサイズは12.5 µmでした。 直径25.4 μmの場合、溶接用のレーザ出力は、材料の組み合わせに応じて30 Wから50 Wの間で変化しました。 パルス幅は0.035~0.05 msに調整され、パルスエネルギーは溶接の場合は1 mJ、突き出たワイヤーを切断する場合は2.5 mJになりました。 すべての実験でアルゴンがプロセスガスとして使用され、流量は15 L/ 分、真ちゅう管の直径は8 mm、BAK 4ノズルの距離は1.4 mmでした(図2参照)。
より太いワイヤーを溶接する場合には、実際のレーザ出力は細いワイヤーを溶接する場合と同じレベルを維持したまま、パルス幅が長くされました。 ワイヤーを溶接した後、邪魔になるワイヤーの端部がより強い連続パルスで切断されました。
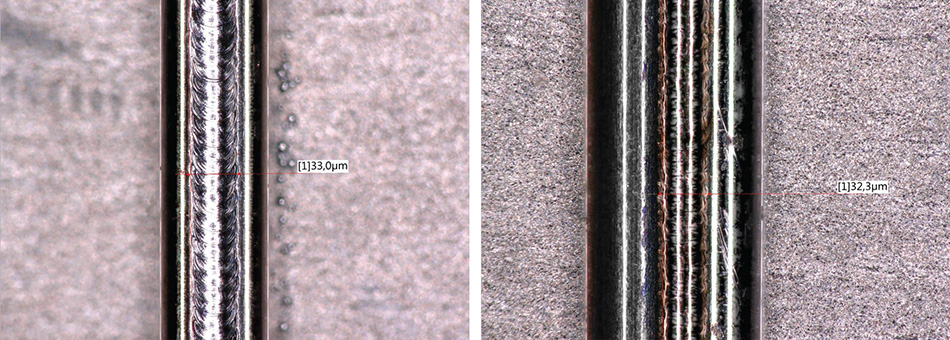
図 2: ニチノールとニチノールの溶接(左)、ニチノールとステンレスの溶接(右)。
研究結果
このアプリケーショントライアルでは、100 WのStarFiberレーザに、さまざまなワイヤーの組み合わせを溶接するのに十分な出力があることが示されました。 プロセスウィンドウは、すべてのタイプでかなり狭くなります。 ピークパワーは10 W未満で、パルス幅は10 µs未満です。 値を大きくするとワイヤーが切断されてしまい、値を小さくするとワイヤーは接続されません。 使用されたパルス形状は、プロセスを安定させるのに役立ちました。 ワイヤーが接触し、ギャップが埋まらないことが不可欠です。 ワイヤーが切断されると、ワイヤーの端部が次のワイヤーに溶接される危険もあります。 そのため、位置合わせが非常に重要です。
ピークパワー[W] | パルス幅(ms) | 繰返周波数(Hz) | 速度[mm/分] | 備考 |
30 | 0.035 | 30 | 20 | 溶接 |
40 | 0.05 | 30 | - | 切断 |
ターンキー最適化ソリューション
ExactWeldワークステーションは、Coherentのアプリケーションエキスパートにより、用途に合わせて工場でカスタマイズされます。 このカスタマイズには、レーザ、プロセス制御、自動処理システムだけでなく、必要に応じて特殊な治具も含まれます。 お客様はアプリケーションエンジニアに蓄積された知識と経験から大きな価値を得ることができます。
このようにして、ExactWeldはさまざまな溶接の種類や形状に最適化できます。 接触溶接の場合、直径が最小10 µmまでの溶接スポットを実現できます。 シーム溶接の場合、高い溶接速度で小さなシーム形状を実現できます。 自由度の高い溶接もプログラミングできます。 回転ステージのおかげで、穴や亀裂のないシール溶接ができ、漏れのない溶接が実現します。 すべてのシステムにおいて、世界各地でのサービスおよびスペア部品の供給がいつでも利用できます。
「お客様はアプリケーションエンジニアに蓄積された知識と経験から大きな価値を得ることができます。」
「信頼性、パフォーマンス、使いやすさに関する最近の実際的な改善により、経済的にもさらに魅力的な製品になる見込みです。」
Coherentは、さまざまな統合レベルで優れた製品を提供する能力においても、比類のない垂直統合型メーカーです。 たとえば、新製品のExactWeld 430は、多くのアプリケーションですでに実力が証明されていて業界をリードしているExactSeriesワークステーションプラットフォームと、最新のCoherent StarFiber 100~600レーザサブシステムを組み合わせたものです。 トレーサビリティ用に、部品とプロセスの詳細をすべての部品に記録することができます。
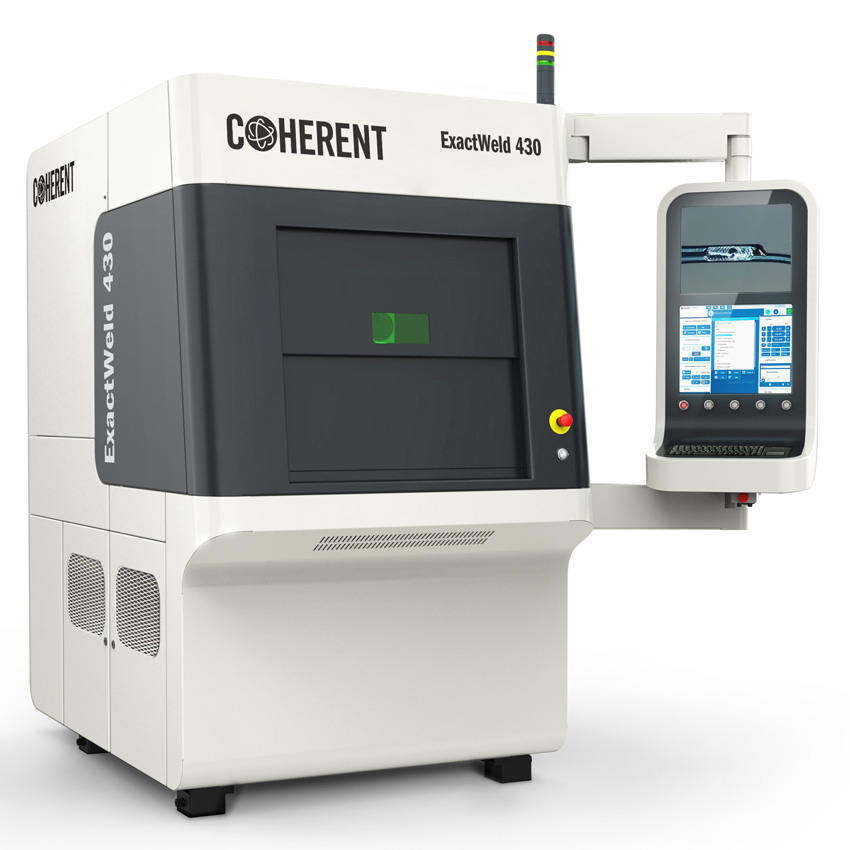
図 3: CoherentのExactWeld 430は、自動溶接作業用のクラス1レーザ装置です。
概要
結論として、医療機器製造における最も困難な溶接用途の1つである、細さ25.4 µm(0.001インチ)のニチノール製ワイヤーとステンレス製ワイヤーの溶接に成功しました。 ニチノールなどの特殊な材料では、プロセスウィンドウを小さくする必要があり、パルス出力、持続時間、時間形状を確実かつ再現性を持たせて生成する必要があります。 サイズが小さい場合、ワークピースの位置が正確で、レーザの焦点が絞られている必要もあります。 Coherent ExactWeld 430は、医療機器業界での要求の厳しいさまざまな溶接用途において、すでにその地位が確立されています。 今では、この難しいワイヤー溶接作業に最適なソリューションを提供できることが証明されています。 信頼性、パフォーマンス、使いやすさに関する最近の実際的な改善により、経済的にもさらに魅力的な製品になる見込みです。