CUSTOMER SUCCESS STORY
Semi-Automated System Improves Medical Device Welding
The Challenge
Microtech Welding fabricates medical devices, instruments and implants, which often involves welding of thin (<1 mm) metal parts. The traditional welding method for joining metal components is gas tungsten arc welding (GTAW); the drawback of this method is that it heats up the parts, which are typically delicate or contain heat sensitive components, such as springs. Furthermore, GTAW produces a relatively large weld seam, and can also discolor the material, both of which necessitate time consuming and costly rework to remedy. Microtech Welding needed a high quality welding method that produces a minimal heat affected zone, and which could be implemented in a cost effective manner with their relatively limited production batch sizes (usually in the 20 to 30 range).
The Solution
The Coherent Select Manual Welder system employs a solid-state laser, which produces substantially less heat input into the part than GTAW. This eliminates the pre-heating often required for GTAW, as well as a post welding annealing cycle, to minimize or correct for thermally induced stress or warpage in a welded device. Laser beam welding also avoids discoloration, and produces a small, straight and consistent weld seam that is cosmetically attractive, and doesn’t need to be subsequently ground down. To use the Select Manual Welder, the operator can weld manually by holding the workpiece by hand and move it under the laser beam. This way, even complex contours can be easily laser welded which otherwise would require a sophisticated and expensive motion control system. Alternately the operator can choose to set up a semi-automated mode if the workpiece size and shape allows this option.
The Result
Use of the Coherent Manual Welder at Microtech Welding has increased their throughput, and the company now runs multiple systems in production. The laser beam welder has also improved weld quality over GTAW, and reduced the need for post weld finishing. Plus, laser beam welding makes it easier to weld dissimilar alloys of a single material together than GTAW. The ability of the system to “learn” a weld path also makes it easy to consistently repeat a process, and is particularly valuable to Microtech Welding, since it speeds production of small batches without requiring the time or expense necessary to implement full automation.
“The Select Manual Welder delivers just the right level of automation for our type of production. Using it, we develop our process, save the settings, make a fixture, and then just repeatedly run the program. It has simplified and sped our manufacturing, and also delivers superior results."
— Mike Zehner, Production Manager Microtech Welding Corp.
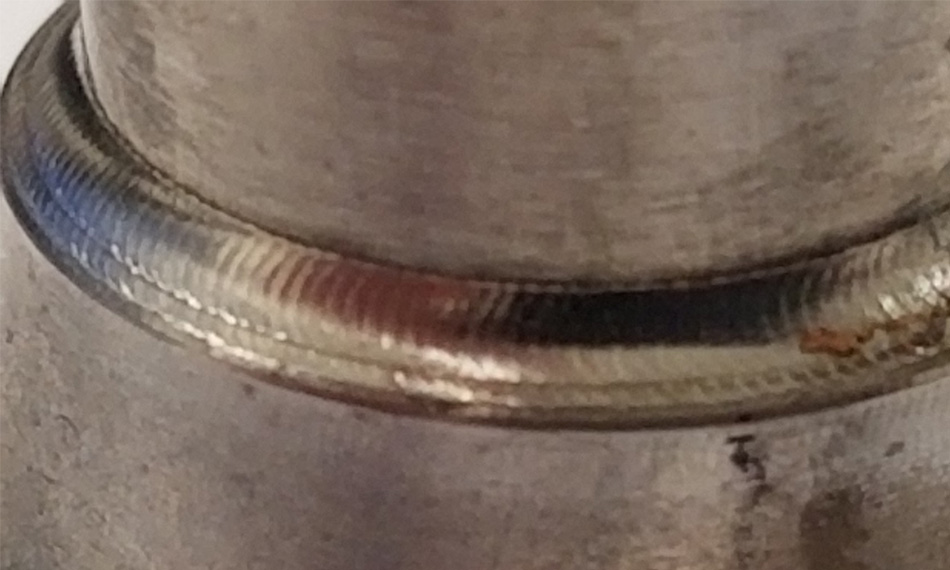