CUSTOMER SUCCESS STORY
Reliable High-Power CO₂ Lasers Improve Lamp Manufacturing
A 1 kW Coherent DC Series laser delivers the combination of performance, reliability, and cost needed for this industrial process, and Coherent support makes the job easier for the integrator.
With over 100 years of welding experience, machine tool builder Arnold Ravensburg (Ravensburg, Germany) is expert in the technology. They were early adopters of laser welding and have been building their own systems since 1985.
Because of their outstanding expertise, especially with CO₂ lasers, companies throughout the world seek out Arnold Ravensburg to solve some of their most difficult welding challenges. They understand that the company will develop a custom solution – often incorporating the laser, beam delivery system, fixturing, and part handling robotics – rather than force a “one size fits all approach” to customers’ unique problems.
Lamp Sealing Application
In 2023, a major manufacturer of lighting products approached Arnold Ravensburg to provide a system for sealing discharge arc lamps. Specifically, the cylindrical quartz glass bulb envelope must be melted to form a seal with the internal ceramic structures that support the anode and cathode. This seal must be continuous and hermetic and extend around the entire circumference of the bulb. This is necessary to retain the high-pressure gas mixture it will be filled with in a subsequent step. This seal must last the entire lifetime of the bulb.
The process requires melting the glass at two places around the entire circumference of the bulb so that it forms a hermetic seal with the ceramic component inside. This will enable the bulb to retain its gas fill over its lifetime.
Originally, the lighting manufacturer performed this sealing process with a flame. However, over the past 10 years, they had migrated to laser processing. They found laser sealing more repeatable and the use of a temperature sensing pyrometer system enabled them to better regulate the process for improved consistency and yields.
Unfortunately, they experienced quality and delivery problems with their original laser system supplier. They were looking for a new vendor who could provide a faster, more consistent process and deliver on time.
The lighting manufacturer already had a history with Arnold Ravensburg, making it natural for them to approach the company with this project. Especially since the only practical source for this application is a CO₂ laser and Arnold Ravensburg is particularly expert with this technology.
The CO₂ laser is required because the bulb envelope material is transparent in the visible and near infrared. This means it can’t be readily processed with shorter wavelength lasers – their light will simply pass right through the material, rather than be absorbed to heat it up.
Choosing a Laser
While this application obviously required a CO₂ laser, Arnold Ravensburg first had to determine process specifics. They found that the optimum method was to continuously rotate the bulb while applying the laser energy at the desired spot. This rapidly heats the bulb. The material temperature is continuously monitored by a non-contact pyrometer, and when it reaches the correct value, the laser is turned off. The bulb continues to rotate and the molten glass flows to make the seal.
Arnold Ravensburg engineers realized they couldn’t perform both seals simultaneously due to potential differences in process parameters. Thus, the two seals are produced sequentially. The rate-limiting factor is how fast the bulb material flows, resulting in each weld taking about three minutes to perform.
The process requires about 800 W of laser power. Arnold Ravensburg chose the Coherent DC 010 as the source for this application. This is the 1 kW model from our DC Series of high-power, sealed, slab discharge CO₂ lasers that extends up to 8 kW.
“Several factors led us to use the DC 010,” notes Hansjörg Klotz, Sales Director at Arnold Ravensburg. “Our end users appreciate that the sealed, slab discharge design offers much greater reliability than the fast flow construction used in other multi-kilowatt CO₂ lasers. It also delivers lower operating costs, better reliability, a longer lifetime, and a long maintenance interval. Plus, being sealed, these lasers avoid any issues with contamination entering the laser, which is always a concern in industrial environments. Finally, the DC Series output power remains constant throughout the laser’s lifetime, ensuring excellent process consistency.”
Partnering for Success
From the perspective of a machine builder like Arnold Ravensburg, Klotz cites ease of integration as a significant advantage. “We’ve used Coherent DC Series lasers many times before, and building a system around them is very straightforward. They offer a true industrial interface, fitting seamlessly into a Fieldbus environment. Many of our customers use Profibus protocol, especially in Germany where Siemens controllers are almost universal, and the DC Series supports that directly.”
“Another factor is Coherent itself,” reports Klotz. “We consider Coherent a partner, and it’s always easy to get the support and information we need from them. For example, we sometimes need detailed data on the beam characteristics of a particular laser for optical calculations, and Coherent never hesitates to provide that.”
“Also, our experience is that there’s excellent unit-to-unit consistency in Coherent lasers. So, once we’ve designed optics, we can construct systems knowing that there won’t be any significant individual adjustment required. The same applies to beam stability; it doesn’t change after installation. This matches our own design philosophy very well. Arnold Ravensburg beam delivery systems are designed so that no optical realignment is necessary if a mirror is replaced. But, of course, this requires that the laser pointing itself remains stable.”
“These are workhorse lasers needing only annual service,” says Klotz. “We can install them without worrying about performance issues or failures in the field. Using the Coherent DC Series laser in our systems eliminates headaches for us and our customers. And that keeps them coming back to us for more.”
“The combination of output stability and consistency, together with high operational reliability, makes the Coherent DC Series CO₂ lasers ideal for integrators, line builders, and end users alike."
– Hansjörg Klotz, Sales Director, Arnold Ravensburg
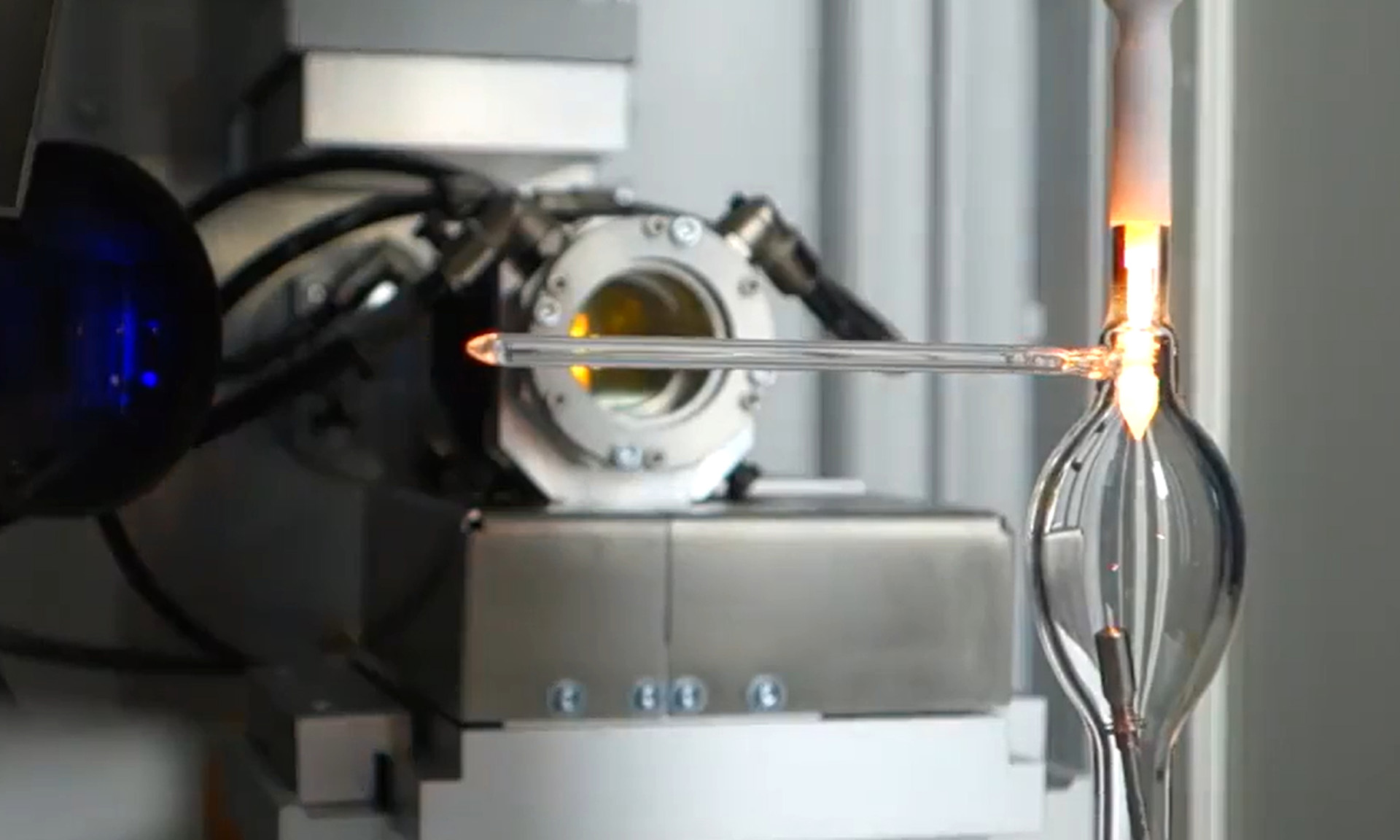
Figure 1. The laser melting system for glass bulbs from Arnold Ravensburg is melting the glass at two places to hermetically seal the bulp.
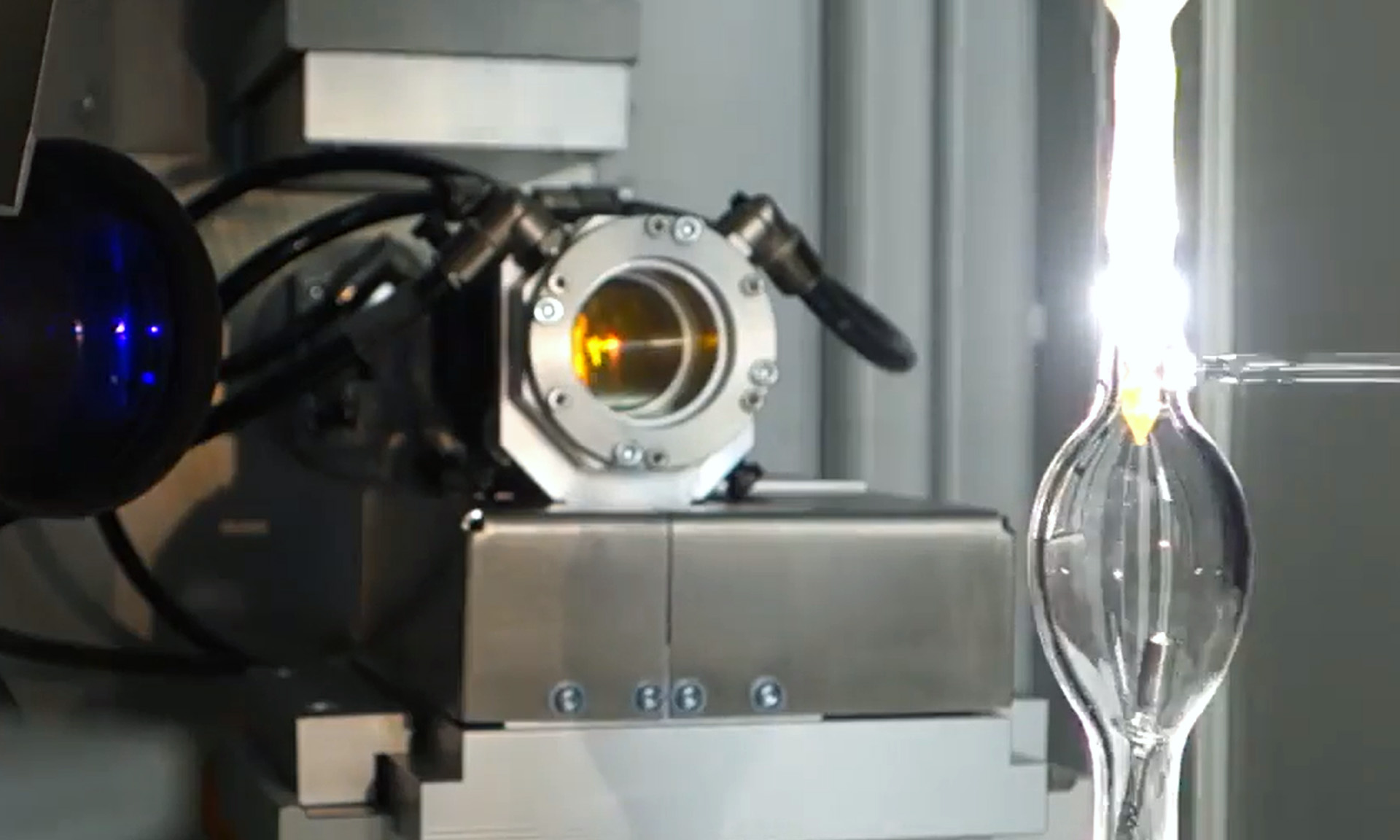
Figure 2: The bulp is continuously rotating while the laser energy is applied at the desired spot with a Coherent DC 010 laser
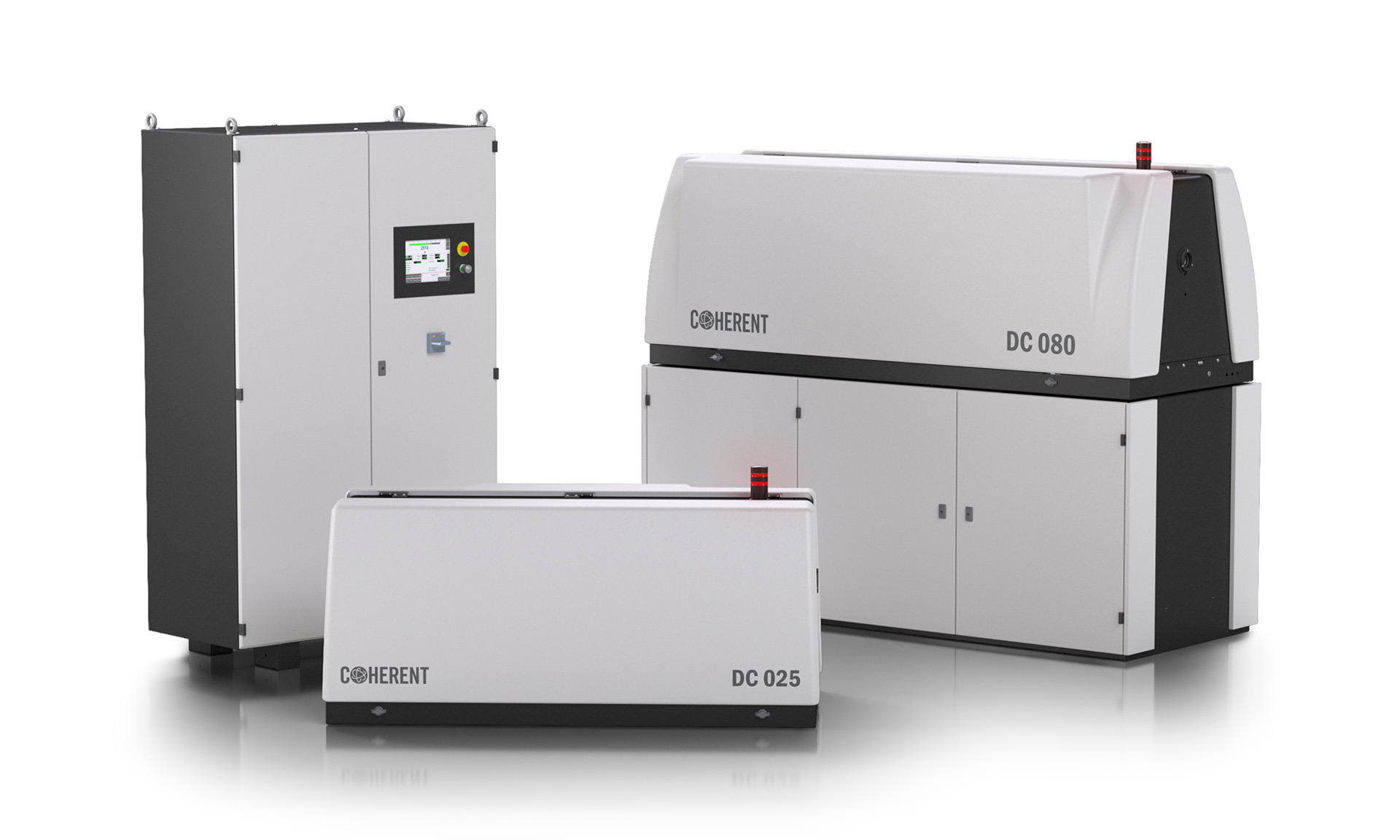
Figure 3: DC Series are diffusion-cooled, highly stable, multi-kW CO₂ slab lasers with output powers from 1 kW to 8 kW.