Cool Solutions for EV Thermal Management
Advanced materials to improve powertrain thermal management are key to improving EV efficiency and reliability.
February 12, 2024 by Coherent
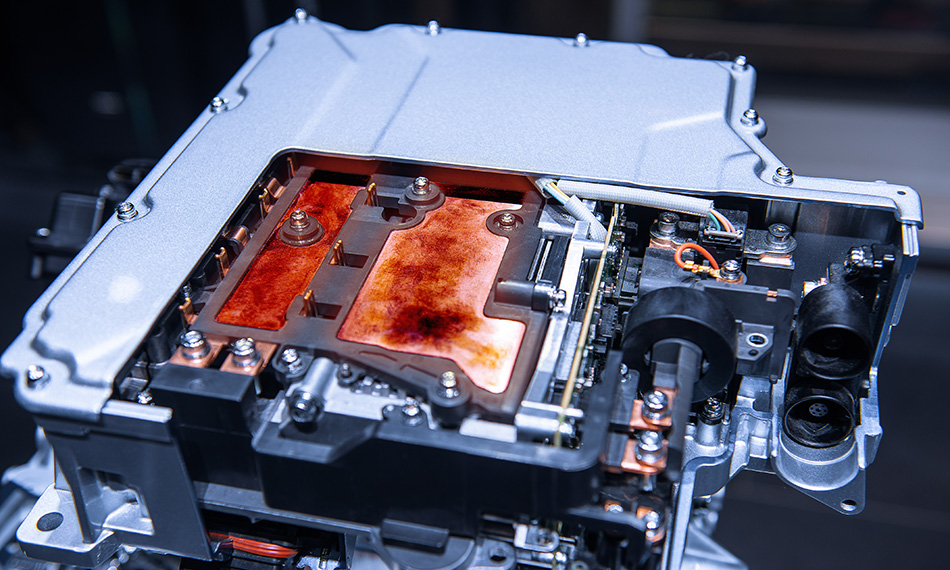
Electric vehicles (EVs) may not be as cool as some people think. In particular, quite a bit of heat is generated in the EV traction inverter. This is the circuity that converts the DC current from the batteries to the AC form required by the traction motor (which powers the wheels).
If the electronic components in the traction inverter run too hot it can lower their operating efficiency. Plus, operating at elevated temperatures can reduce the lifetime and reliability of these electronics. This makes cooling this circuitry an important factor in EV design. And the challenge is to do this with a cooling system that is as lightweight, reliable, and compact as possible since adding weight lowers vehicle efficiency and range.
Traditional Powertrain Cooling
Typically, cooling is accomplished by mounting the power electronics and other heat-generating components on a water-cooled baseplate. This cools the electronics by transferring the heat away. Currently, most baseplates are made from copper or aluminum. Copper has good thermal conductivity, which means it efficiently moves the heat away from its source. Aluminum has a lower thermal conductivity than copper, but it is much lighter. So, there’s a weight savings.
However, neither of these metals are ideally suited for baseplates. A primary reason for this is because, as these materials heat up, they don’t expand at the same rate as the packaged silicon or silicon carbide electronics in the traction inverter. This differential expansion puts mechanical stress on the power electronics packaging. It can warp the electronic assemblies, eventually leading to breakage in the packaging.
Improving Thermal Management
The ideal baseplate material would have high thermal conductivity, and also closely match the thermal expansion characteristics of the electronics packaging. It is also advantageous if the material is mechanically strong and hard, corrosion resistant, lightweight, and also reduces or eliminates the need for water jackets. This in turn, would lower the weight and size of the inverter in some applications.
Coherent has developed a range of reaction-bonded Si/SiC (RBSiC) formulations to meet the requirements of a variety of thermal management applications. For example, some reaction-bonded Si/SiC formulations offer high thermal conductivity – similar to or higher than copper. Most importantly, their thermal expansion characteristics can be tailored to match those of electronics packaging substrate materials such as AlN or Si₃N₄. Testing has shown that baseplates made with this Coherent RBSiC significantly reduce packaging warpage.
Beyond that, this RBSiC also possesses desirable physical characteristics including high mechanical strength and hardness. This makes it durable and resistant to wear and damage, contributing to the long-term reliability of the heat sink. It’s also quite corrosion-resistant and chemically inert. Finally, our RBSiC has a lower density than copper, meaning a lighter-weight baseplate.
Because Coherent RBSiC combines high thermal conductivity with higher hardness (resistance to deformation) and a better thermal expansion match than metals, it also dramatically reduces the problem called ‘thermal grease pump out.’ This thermal grease or paste sometimes is applied between the high-power module packaging and heat sink to ensure good thermal contact. But with metal baseplates, it is gradually pushed out from between them due to mechanical pressure and thermal cycling. This reduces cooling effectiveness.
From a practical standpoint, Coherent can fabricate RBSiC baseplates as parts in their final shape. Plus, these can include complex features such as cooling fins or cooling channels. This lowers manufacturing costs. Additionally, we produce RBSiC in a form that is compatible with additive manufacturing techniques. This enables interior structures, like micro-cooling channels, to be included without the need for additional machining operations. Again, this reduces production costs.
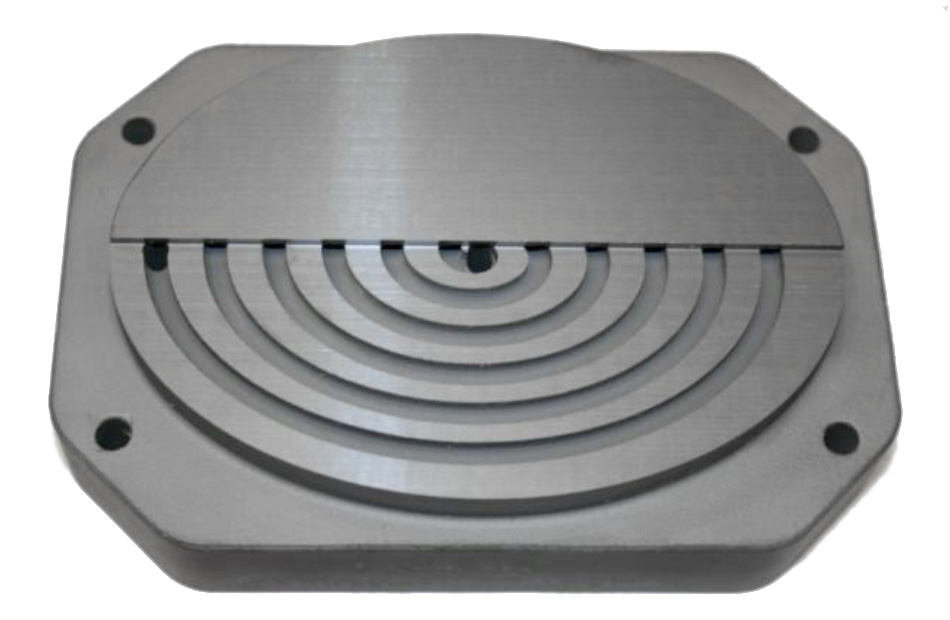
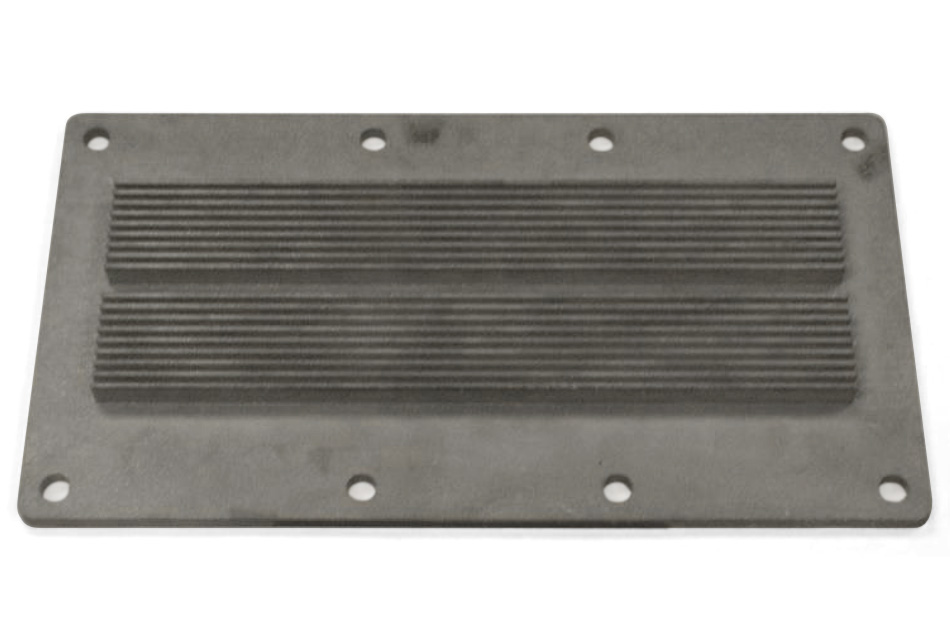
Coherent can readily fabricate RBSiC baseplates with features such as internal and external cooling fins, and internal water flow channels.
Coherent RBSiC provides a superior thermal management solution for EVs utilizing silicon power electronics. And it’s also a future-proof solution as EV makers embrace SiC power electronics. This is because SiC power electronics inherently operate at higher temperatures, and so demand even better CTE matching between the baseplate and electronics packaging. Thus, RBSiC stands as a reliable and adaptable asset, safeguarding system performance for years to come.
Learn more about Coherent RBSiC.