SiC CIRCUITRY MAKES EVs BETTER
Discover why SiC power electronics are in demand for improving EV performance.
January 30, 2023 by Coherent
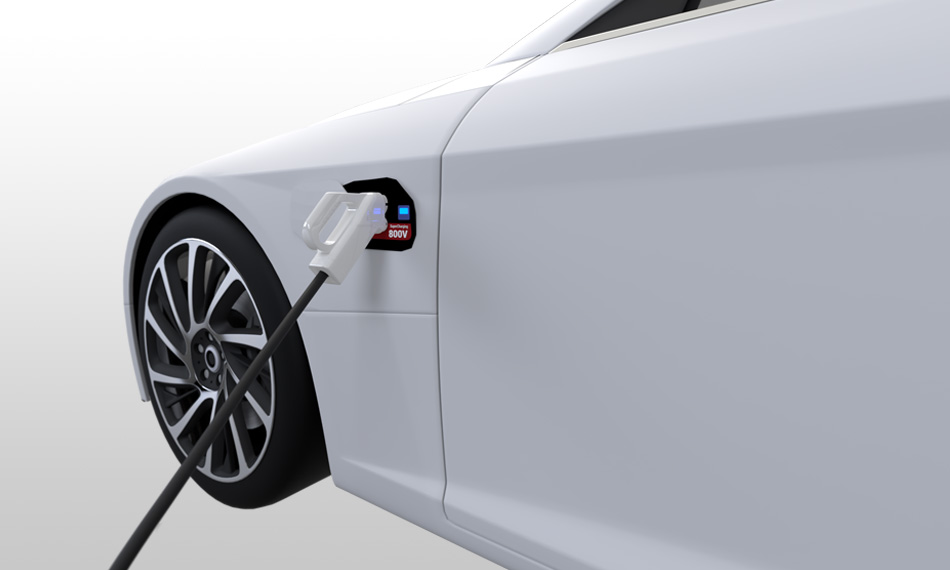
While many governments worldwide are actively promoting electric vehicle (EV) technology, consumers have not been universally enthusiastic about them. Two of the main factors limiting public acceptance of EVs are driving range and cost.
In terms of EV design, the most effective way to improve range is to increase battery voltage. Currently, most EV batteries output 400 V or less. Increasing this to 800 V delivers more vehicle horsepower at the same current. It also increases system efficiency at a given power level.
A key tool for lowering EV cost is to improve the efficiency – and most importantly the power density (the ratio of power efficiency to overall size) – of the power electronics. The function of the power electronics is to convert the high-voltage DC supplied by the battery into the various other forms required in the vehicle. This includes the three-phase alternating current (AC) needed for the traction motor (which drives the wheels), and the various DC/DC conversions required for the onboard charger and other systems.
Designers SiC silicon carbide on the problem
What limits the use of higher battery voltages and prevents further improvements in system power density? A big part of the problem is that most power electronics utilize silicon semiconductor power switches. Silicon – which is used for integrated circuits in nearly every single piece of electronics gear we now have – simply doesn’t work well at high voltages and high temperatures. And these are exactly the conditions present in EV power electronics.
Fortunately, there’s alternative semiconductor material to silicon for these kinds of applications called silicon carbide (SiC). It has a set of electronic characteristics that make it ideally suited for use at the high voltages, temperatures and powers found in EV power electronics. The main properties and benefits of SiC for EV power electronics are summarized in the table.
Property |
Description |
Benefit |
High-temperature operation |
SiC power devices have much higher operating temperatures and greater allowable junction temperatures than conventional silicon-based switches. SiC also has substantially better thermal conductivity than silicon. |
This eliminates the need for cooling components and bulky heat-sink materials. This reduces vehicle size, weight, and cost. |
High current carrying capacity |
SiC power devices can carry current densities of up to five times higher than silicon power components. |
This permits higher power density within a chip and also decreases the total number of components required in the system. This reduces traction inverter size, cost, and complexity. |
High switching frequencies |
SiC-based power components can switch much faster under high temperature, voltage, and power operating conditions than silicon circuitry. |
Faster switching cuts the size and cost of the passive components used in traction inverters, such as capacitors and inductors. |
High voltage capacity |
SiC switches can sustain up to ten times higher voltages than their silicon counterparts.
|
This minimizes the number of switches in series required in high-voltage systems, which, in turn, lowers system cost and size. It also supports EV industry migration towards 800 V systems for increased vehicle driving range and faster charging times. |
Meeting the global demand for SiC
Automakers are already well-aware of the advantages of SiC power switches. Of course, microelectronics manufacturers are working to scale up production capabilities to meet this developing demand.
But, producing high-quality SiC devices that match the volume and cost targets of the EV industry moving forward isn’t easy. In fact, after decades of research and development, there are still only a handful of suppliers worldwide who have mastered the art of producing high-quality, large, defect-free SiC wafers.
Furthermore, automotive manufacturers ideally want to source SiC-based power components from a vendor who is vertically integrated. That is, a company who does everything from growing the wafer material all the way through fabricating finished, packaged devices. A component manufacturer who has ownership and control over the material substrate and epitaxy gives the automaker or tier supplier confidence that the product will be delivered reliably and will maintain a consistent quality. It also eliminates finger-pointing amongst vendors within the supply chain if a problem occurs.
Coherent is one of the few companies worldwide with a complete, vertically integrated SiC manufacturing capability. We produce SiC wafers and epitaxy, all the way through power devices and modules. Furthermore, the unmatched quality with which we can produce SiC material makes Coherent virtually the only supplier positioned to successfully transition from the current standard wafer diameter of 150 mm up to 200 mm. The benefit of larger wafers is that it can significantly reduce the cost of devices.
Consumer acceptance of EVs requires that they deliver the same level of convenience and economy as traditional, gas-powered cars. This will require lowering initial purchase price and operating costs, plus increasing driving range and decreasing charging time. Vehicle power electronics based on the unique properties of SiC will play an important role in achieving every one of these goals. And efforts at Coherent to bring down the cost of SiC devices have us well on the road to success with this technology.