An In-Depth Study of Fiber Laser Welding
Coherent Labs engineers got the first-ever, high-resolution, cross-sectional views of ARM laser welding in progress using incredibly powerful X-rays at the European Synchrotron Radiation Facility.
May 30, 2023 by Coherent
What do you do with x-rays that are 10 trillion times brighter than the ones used for a typical chest x-ray? If you’re an engineer at Coherent Labs, you use them to learn more about the process of laser welding than anyone has ever known before.
Beneath the surface of fiber laser welding
Fiber laser welding has been studied extensively in the past using traditional high-speed video. The video makes it possible to study the dynamics of the pool of molten metal and vapor (called the “keyhole”) created during welding. Usually, the camera is placed above the part and looks down at it to record what’s happening on the surface. But, of course, there’s quite a bit more going on within the keyhole than just what’s seen from the top.
How can we actually see inside? X-ray videos have been used in the past for this purpose. But they’ve never provided sufficient detail because the X-ray sources weren’t powerful enough.
A research cooperation between the Production Technology Group of Technische Universität Ilmenau and the Coherent Applications Lab, Hamburg, envisioned using a much more powerful X-ray source than ever previously employed for this purpose. The idea was to use X-rays powerful enough to pass right through solid metal.
This would allow high-resolution movies of the welding process from the side view. Looking from the side would reveal much more useful information – namely the exact shape and evolution of the keyhole during welding.
Making ARM fiber laser welding even better
This group specifically wanted to use this approach to investigate the precise way in which the Coherent Adjustable Ring Mode fiber laser (FL-ARM) operates. We already know that the FL-ARM delivers amazing results – crack-free welding of high-strength steel, welding aluminum without filler wire, and successfully welding copper. And we know this comes from the ability of the ARM laser to carefully control part heating and cooling during the welding process. But we don’t always understand every nuance of exactly how this all happens.
The team especially wanted to target some of the most critical and challenging emerging applications for fiber lasers in various joining tasks in e-mobility. Specifically, welding copper, aluminum, and other traditionally “difficult” materials – and often doing it with very thin, heat-sensitive sheets. They were also interested in studying so-called “profile welding.” This is a method commonly used to make tubing.
This research was looking to gain greater insights into how all these processes work by visualizing the processes and keyhole dynamics and seeing the influence of different ARM laser power distributions on spatter formation during welding of copper materials. The goal, of course, being to improve results and develop more reliable production methods.
The European Synchrotron Radiation Facility
There are only a few facilities in the entire world that can generate X-rays powerful enough to perform the kind of imaging the team desired. One of the pre-eminent sites is the European Synchrotron Radiation Facility Extremely Brilliant Source (ESRF-EBS) in Grenoble, France. It’s been constructed specifically to service researchers in fields as diverse as health, clean energy, materials science, art, and anthropology. It’s even been used to study beehives and 119 million-year-old fish fossils.
The synchrotron itself is an 844 m circumference tube with a very high vacuum inside. Electrons circle around inside it and are accelerated nearly to the speed of light. Magnets around the ring are used to make the electrons quickly change their direction of travel. When this happens, the electrons emit extraordinarily high-energy x-rays.
These X-rays are then directed down into one or more of 44 different “beamlines.” The beamlines house the laboratories and associated instrumentation used to perform the actual research.
Experimenting outside the box
Our Coherent Labs team assembled a welding setup which included an 8 kW HighLight FL-ARM fiber laser. The research group from Technische Universität Ilmenau, Production Technology Group, built a mechanism to hold and move the parts automatically during welding as well as the focusing optics, and an assist gas delivery system.
All this equipment was taken to the ESRF and placed in an “experimental cabin” (a room entirely encased within 75 mm thick, solid lead shielding) on one of the beamlines. With our researchers sitting safely some distance away in another room, welding was performed under computer control while the setup was exposed to X-rays. A camera system that converts X-rays to visible light recorded the action at speeds of up to 50,000 frames per second. This team of 14 people worked in four shifts for seven days straight, performing several hundred individual welding tests on a variety of metals, including stainless steel, copper, and aluminum.
And what did we learn from all this? With 14 TB of data to analyze, it is going to take some time to answer that completely. But we have already seen that in copper busbar welding tests the video clearly shows that with a suitable power distribution (approximately equal power in the center and ring beams) the keyhole is stabilized, and there is no constriction at the base of the keyhole. In contrast, when the center spot power is too high, the capillary is constricted at the base. This results in spattering and the formation of pores. If the ring power is too high, the liquid melt spills into the keyhole, evaporates abruptly, and causes material ejection.
Furthermore, the influence of shield gases on the capillary formation was investigated. These findings provide greater insight into profile welding.
Further analysis of the data will help us better understand exactly how the power ratio between the center and ring beams affects results in various welding processes. This knowledge will enable Coherent Labs to develop more robust and consistent welding process recipes that deliver better outcomes for our customers – even faster.
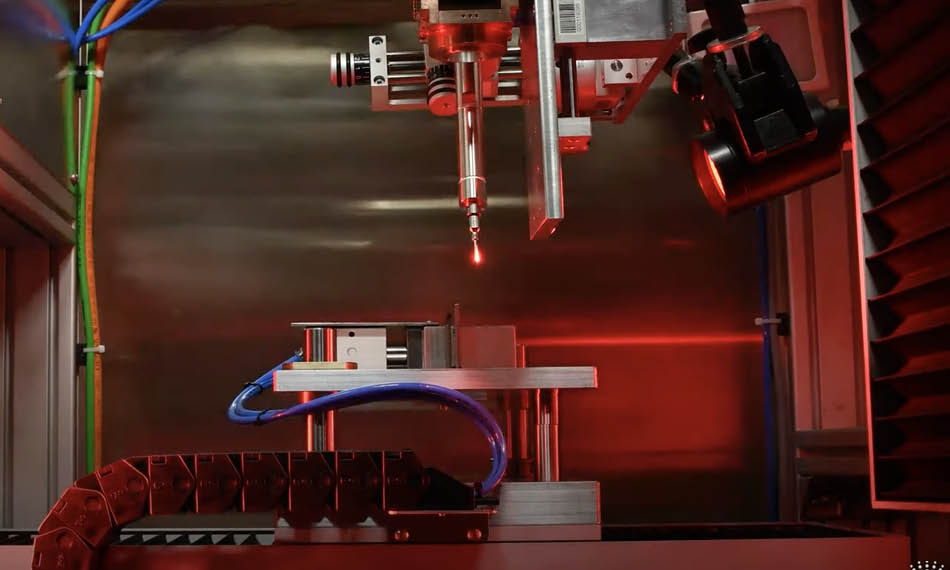