MDM WELDING FOR CONTRACTORS AND OEMS
Discover the advantages of a diverse family of machines for MDM welding, featuring a common welding process and a broad choice in automation.
May 11, 2023 by Coherent
For devices, instruments, and implants needing welding, the optimum MDM supply chain format depends on various factors, and varies from product to product, even for the same manufacturer.
But volume and batch sizes are virtually always dominant considerations. For example, the welding of smaller volumes of subassemblies featuring numerous batch-to-batch variations is often contracted out to a specialty job shop. Whereas larger volumes (e.g., >100,000) of identical devices usually require an investment in automated part handling and is often performed in-house using dedicated welding machines or welding subsystems integrated into a production line.

Laser welding is ideal for devices and instruments (e.g., endoscopes) with tubular or asymmetric shapes.
For manufacturers or sub-contractors alike, there is no point in buying features that you don’t need and no economy in sacrificing features that you do need.
That’s why Coherent has a flexible and modular welding product line. For larger manufacturers and custom line builders for example, we often supply a combination of just a laser, the welding head, and some laser beam monitoring.
But for those who need a standalone solution, we offer several turnkey machines such as our Coherent ExactWeld series. And as we will discuss here, even in these machines, you get to choose just the options that make sense for your particular MDM welding scenario. In addition, we also offer “manual welders” where the part loading/unloading and handling are performed by a human operator.
However, even in manual welding, each single laser spot weld is exactly the same as in one of the CNC-controlled automated machines, because we use the same laser source, similar beam guiding optics, and process heads. This makes it very easy to transfer processes from one level of automation to another with high consistent yields and product quality.
Automation options
Let’s take a look at how different machine options map onto the overall welding process. The process can be broken down into 5 important steps with details that can be optionally automated, logged, and archived for every batch and even every unit.
Material handling. This is a key time/cost factor that is important to get right in every MDM welding application. Coherent machines support a full spectrum of options here. The simplest is manual loading/unloading where every part is manually placed in the machine. A common automated option for smaller parts is tray loading where the parts are manually loaded into a tray before the machine takes over. And the most fully automated option is robotic “pick and place” where the machine picks up parts from a bin.
Pre-processing. This involves positioning and aligning the parts prior to applying the laser beam. Here the simplest option is to do this manually using crosshairs and joystick for spot welds and simple linear seams. Or this can be fully automated using 3D machine vision alignment.
Laser monitoring. The laser beam is a tool, albeit a precise non-contact tool. And it’s important to check that the tool is always sharp and correctly aligned. Automated beam monitoring – we call this BeamInspect – is an important feature when looking for ways to maximize yields in any welding application, particularly for challenging tasks like joining dissimilar metals or welding thin wires.
Welding. In addition to monitoring the laser beam, there are automated options for monitoring the welding process itself, as it is occurring. SmartSense+ from Coherent is a novel and economical system based on back-reflected laser light and light emitted by the process itself. It is often expanded to include acoustic and contact sensing that can identify any issues such as heat cracking in a joint - during or even after the welding process. Again, the goal is maximizing yields.
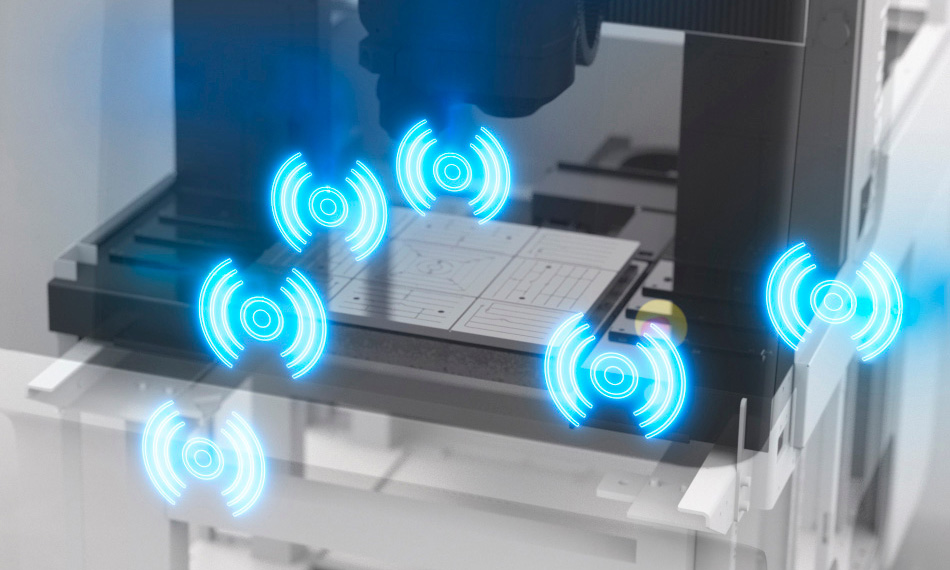
Automated welding machines like ExactWeld employ multiple sensors (highlighted schematically here) to monitor every important detail of the laser and the process.
Post-process verification and QC. These processes were historically handled separately from the welding process. But for high-volume production runs a better option is to integrate this functionality into the welding machine itself, based on machine vision.
Software configured for secure process control
Where all these aspects are fully automated, that’s a lot of different functions involving multiple technologies. The key to fully exploiting the speed and efficiency of all this automation is streamlined software control that integrates everything under a single interface.
At Coherent, we provide a unique software platform called Laser FrameWork that runs on all ExactWeld machines. It was created to enable faster job setup, increase operator productivity, decrease production errors, and reduce personnel training.
An intuitive, powerful, touchscreen interface where users can readily specify processing, inspection, and other automated steps and then combine these together into complete job recipes. All through simple drag-and-drop operations and all with complete logging and archiving capabilities. These recipes can then be called and executed by a semi-skilled operator. With different levels of secure access, this avoids the possibility of accidental operator modification of the process in any way.
Laser FrameWork works seamlessly in any “smart manufacturing” environment (i.e., IoT). It provides extensive connectivity capabilities, including numerous communications protocols and interface options, to integrate a Coherent machine or subsystem with other factory automation systems.
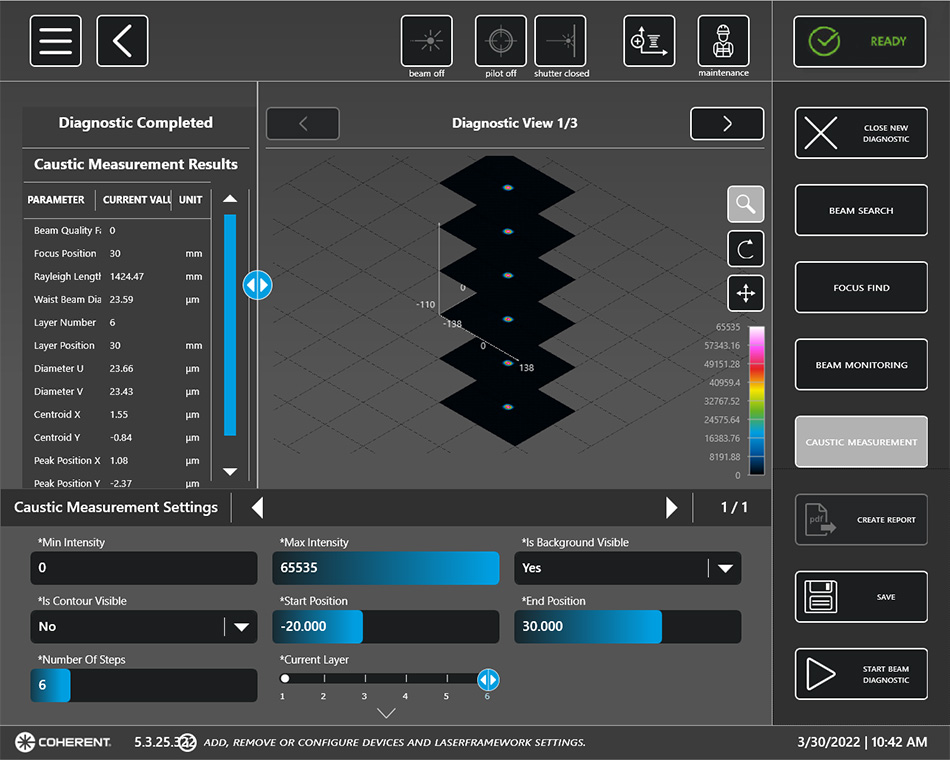
Laser FrameWork is an advanced software operating environment which integrates every aspect of machine programming, control, operation, and inspection through a single user-friendly GUI.
MDM combining welding with cutting and marking
The manufacture of devices such as orthopedic and cardiovascular implants not only requires fine welding, it also depends on precision cutting. Coherent is a leader in laser cutting machines including the popular StarCut Tube series optimized for stents and other tubular products. Many products also require another laser-based process, namely permanent marking. This meets the need for UDI on instruments and disposables. Standout examples are tip-to-tube welded components for robotic surgery. Coherent provides a host of marking machines and subsystems, including laser black marking systems for corrosion-resistant marks. Again, Laser FrameWork software simplifies the integration of marking for both contractors and in-house manufacturers.
Worldwide applications support and service
Both manufacturers and contract job shops can benefit from expert help with process development, particularly for difficult welding tasks like welding thin wires or joining dissimilar metals.
Coherent Labs is our worldwide network of applications labs with locations in the US, China, and the EU. They are staffed by personnel with extensive experience solving all kinds of welding challenges. Cut your development time and costs by drawing on this experience.
MDM is an industry that is increasingly based on global manufacturing. Coherent supports this trend with a worldwide service network bringing fast local help whenever you need it. Couple that with machines configured for predictive maintenance and remote diagnostics and you can virtually eliminate expensive unscheduled downtime no matter where your process is located or sub-contracted.
Coherent: An essential partner to the MDM industry
Laser welding is an essential step in the manufacture of many MDM industry products. Maximizing its potential in terms of performance, reliability, and economy can be challenging whether you’re a volume manufacturer or a specialty contractor. Partnering with Coherent eliminates your risk in all these areas thanks to our wide range of machines and options, together with our service and experienced support team.
Learn more about our MDM solutions.