熟練したスタッフは、雇用やトレーニングにコストがかかるだけでなく、現在の労働市場では見つけるのも定着するのもますます困難になっています。自動化されたレーザ溶接システムは、熟練スタッフの必要性を大幅に削減します。たとえば、エンジニアや技術者がマシンのソフトウェアを使用して、溶接アプリケーションのさまざまな側面をすべて指定し、保存すると、オペレーターはGUIを介した制限付きアクセスにより、加工方法を安全に開始することができます。
オペレーターの主観を排除し、原位置ビジョン、加工方法監視、レーザ監視、ポストプロセス検証などの使用と組み合わせることで、より高い歩留まりとスクラップの削減による信頼性の高い製造が実現します。加工方法の一部が、指定された限界に近づくと、マシンは必要な調整を行うか、加工を停止してオペレーターに警告を発します。これはどのような用途においても明らかに利点です。しかし、これは特に、上流加工方法によってすでに価値が投資されている部品や、高価値の材料を使用する部品の溶接に利点があります。
これらすべての「最終的な」利益は文字どおり最終的なものです。このような自動化の利点の一つひとつが、直接的または間接的に、部品あたりの総コストの低減に寄与します。
自動化された機能と利点
ここでは、自動化されたソリューション全体の重要な構成要素となり得る、いくつかの重要な側面を紹介します。
自動化された部品ローディング/アンローディング –これには、部品をシステムに出し入れするロボットとのインターフェースとして機能するホッパー、コンベア、トレイローダーなど、さまざまな送り込みオプションがあります。 自動化は人件費を大幅に削減し、人件費が品質に与える影響も軽減します。 場合によっては、ピックアンドプレースロボットも加工方法に利用することができ、通常は3Dビジョンシステムと共に使用されます。この自動化された溶接位置合わせは、さらにコスト効率をもたらします。
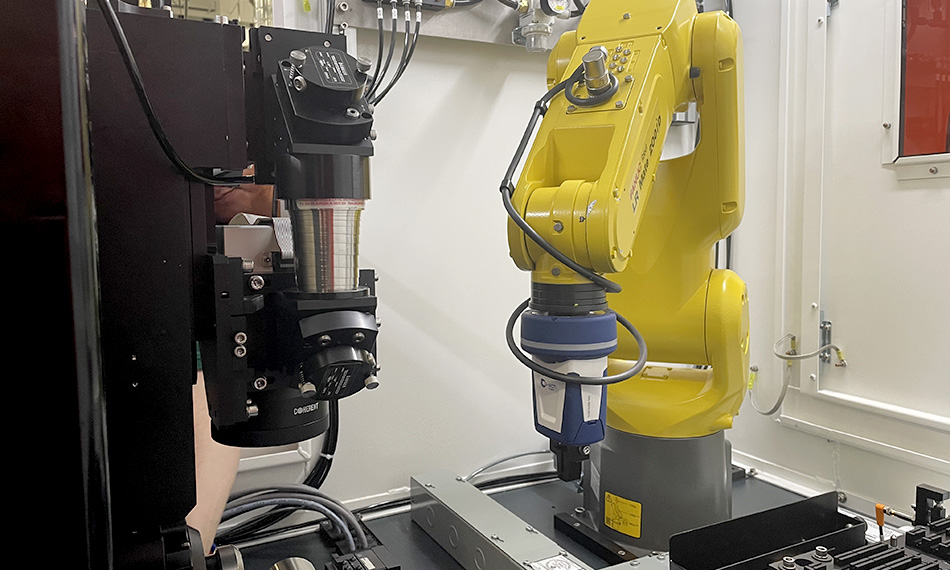
自動化ソリューションは、部品の出し入れや人件費の削減に役立ちます。
プリプロセスビジョン – すべての溶接で毎回正しい部品の確認と位置合わせができるようにします。この溶接前プロセスでは、部品の適合性に基づいて「go/no go」(継続か中止かの決定)をすることもできます。手作業による加工方法では、オペレーターは部品を固定具にセットし、溶接前にしっかりと締め付けます。回転テーブルを使用して溶接とローディング/アンローディングを同時に行うことで、この平凡な作業を高速化できる場合があります。一方で、自動化されたシステムでは、マシンビジョンシステムがホッパー内、ベルトコンベア上、トレイ内などで部品を個別に見ることができます。固有の物理的詳細、基準マーク、バーコード、その他のスワイプチェックなどを確認することができます。
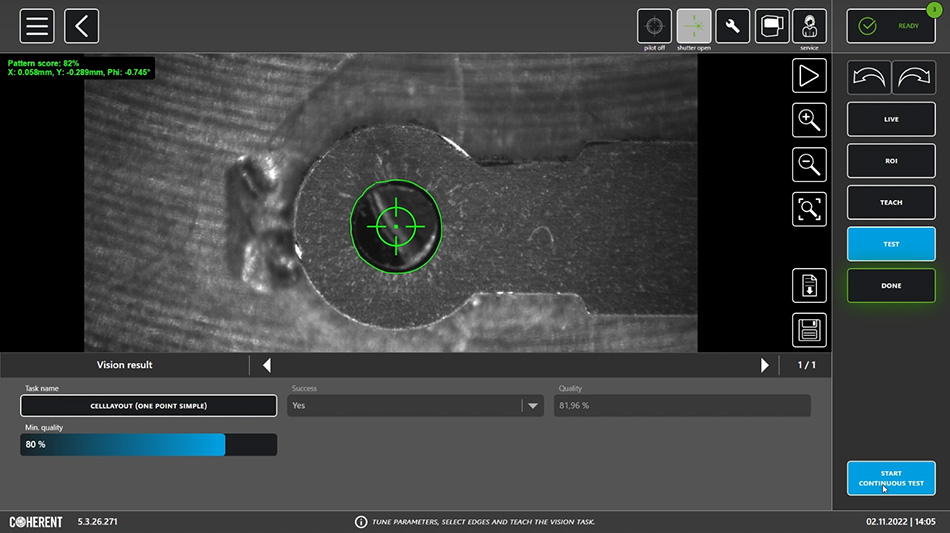
Coherent PartVisionは、すべての溶接で正しい部品の確認と位置合わせを実現します。
インプロセス監視 – 加工方法のばらつきを警告し、加工方法のドリフトに対する予防保守を計画したり、不良部品が組み立てられる前に製造を停止したりする機会を得ることができます。Coherentは、サードパーティのソリューションに依存することなく、経済的で包括的なインプロセス機能を提供するマイクロ溶接専用のシステム、Coherent SmartSense+を自社開発しました。SmartSense+の主なコンポーネントは、レーザの後方反射光と加工方法自体から発せられる光を捉えて分析する独自の光学系です。また、音響信号や他の信号も含めることができます。このデータは、溶接が実際に行われたかどうかを判断したり、水平および垂直方向の部品ギャップ幅を監視したり、ガスが使用されている場合は加工方法とシールドガス流量の変化を検出したりするために使用できます。また、溶接部に穴や空洞、微小亀裂がないかを評価することもできます。
当社のインプロセス監視のもう1つの利点は、信号を使用して、たとえば、プラズマが形成されるタイミング、溶接が不安定になるタイミング、これらをレーザや光学系パラメータに関連付けるなど、溶接スケジュールを最適化します。 当社のアプリケーションエンジニアは、数十年の溶接経験を持つユーザーであっても、この機能が非常に有用であることを何度も証明してきました!
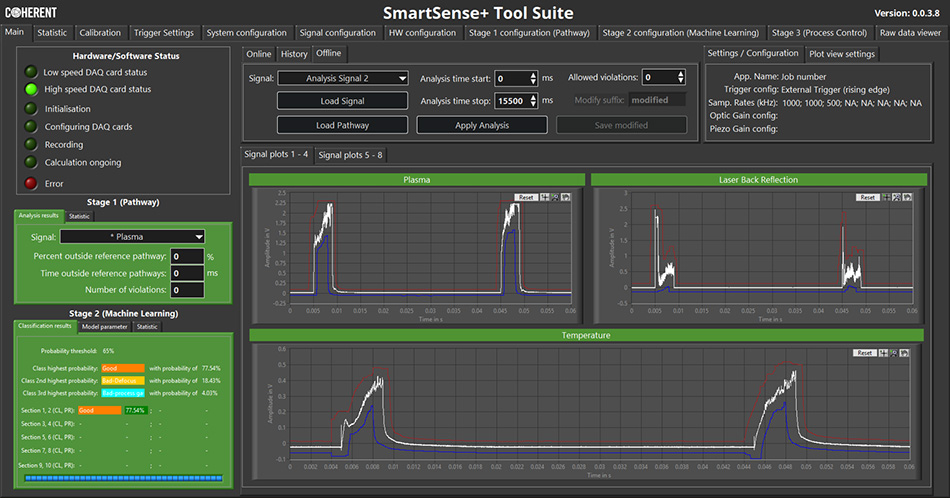
独自のアルゴリズムを使用してセンサー信号を分析し、OK/NOKフィードバックを提供するだけでなく、焦点のずれ、出力またはエネルギーの低下、ガスシールドの不足、汚染など、溶接不良の可能性に関するガイダンスも提供することができます。
プリプロセス、インプロセス、ポストプロセスのデータ取得 – データロギングは、機器の性能を理解し、加工方法を理解して加工歩留まりを最適化するために、今や製造の要となっています。 システムまたは加工方法からのアラートにより、加工方法が加工ウィンドウから脱落する前にアクションを起こすことができます。 たとえば、はめあい公差を超えた場合にアラートを発する溶接前プロセスビジョンシステム、G/NG通知のための加工ドリフトや条件の段階的変化を示すインプロセス監視、製造記録データに添付できる溶接のポストプロセス ビジョン キャプチャなどがあります。 当社のシステムは、主要な通信プロトコルすべてに対応しており、数十年にわたり、お客様のためにこれらのデータを結び付けて、配信してきた経験があります。
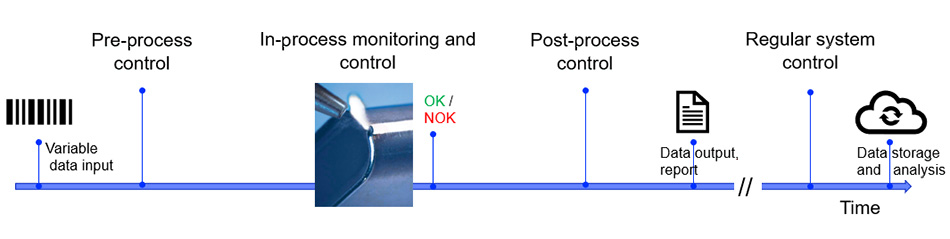
自動化された検査とデータ追跡/ロギングは、人による検査や手作業によるデータ入力に伴う時間とエラーのリスクを排除します。
シンプルで強力な制御ソフトウェア – このような自動化には、多くの異なる技術や方法が関わっており、これらを個別に組み込むことは困難です。Coherentの完全に自動化されたレーザ溶接システムでは、使いやすいGUIとオブジェクトベースの加工方法設定/実行を特徴とする次世代ソフトウェアプラットフォームである、Coherent Laser FrameWorkの下で、溶接のあらゆる側面が制御されます。このソフトウェアの制限付きアクセス機能により、オペレーターが自動化やデータロギング機能の起動や開始を忘れる可能性が完全に排除されます。
費用対効果の高いソリューション
自動化されたレーザ溶接システムは、多くのMDM用途でコストを削減できます。しかし、設備投資コストを過度に増加させるべきではありません。具体的には、アプリケーションが本当に必要としない機能を購入することに価値はありません。そのため、Coherentは送り込みオプションからRFIDタグリーダーの使用まで、複数のオプションを備えたフレキシブルなサービスを提供しています。当社は単に完成されたシステムを提供するだけでなく、お客様のニーズに合わせて最適化されたシステムを提供しています。
詳しくは、CoherentのMDM向けソリューションをご覧ください。
関連資料