Coherent in der Halbleiterherstellung: Wafer-Inspektion
UV-Laser von Coherent ermöglichen die Erkennung winziger Defekte auf Halbleiter-Wafern, um die Ausbeute zu maximieren und Kosten zu senken.
17. Oktober 2024 von Coherent
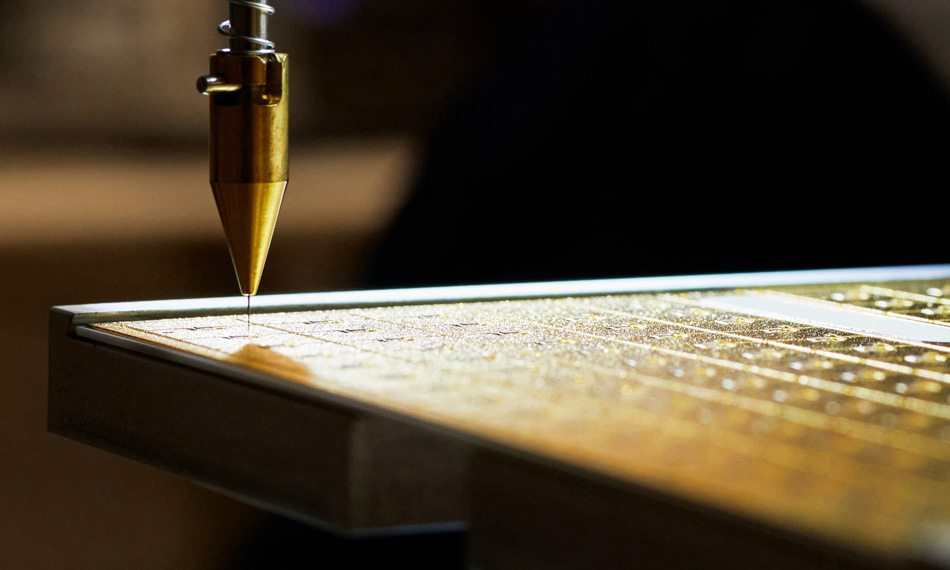
Der Bau des Apollo Guidance Computers (AGC) in den 1960er-Jahren, mit dem die NASA die Mondlandung vollbrachte, kostete rund 150 Millionen US-Dollar (1 Milliarde US-Dollar in heutigem Wert). Er war etwa so groß wie ein Mikrowellenofen und wog rund 32 kg.
Heute kostet das neueste iPhone 15 1.600 US-Dollar und passt in eine Handfläche. Und dieses iPhone ist, wenn man die mögliche Anzahl von Operationen pro Sekunde betrachtet, etwa 200 Millionen Mal leistungsfähiger als der AGC.
Dieser Leistungsanstieg bei Mikroprozessoren wurde vom Intel-Mitgründer Gordon Moore vorhergesagt, der prognostizierte, dass sich die Anzahl der Transistoren auf einem Mikrochip etwa alle zwei Jahre verdoppeln würde. Aber der eingangs erwähnte Vergleich demonstriert auch eine wichtige Begleiterscheinung des Mooresches Gesetzes, die manchmal als Zweites Mooresches Gesetz bezeichnet wird. Nämlich, dass die pro Dollar verfügbare Mikroprozessorleistung im Laufe der Zeit ebenfalls exponentiell ansteigt.
Sowohl das Erste als auch das Zweite Mooresche Gesetz haben sich in den vergangenen Jahrzehnten als zutreffend erwiesen, weil sich die Halbleiterindustrie gleichzeitig auf das Erreichen zweier verschiedener Ziele konzentriert hat. Das erste Ziel ist, Schaltkreiselemente und -baugruppen kleiner zu machen. Das zweite besteht darin, unermüdlich die Kosten zu senken.
Ein bedeutender Kostenfaktor in der Halbleiterherstellung ist die Ausbeute, und ein wichtiger Faktor für die Ausbeute sind Defekte und Verunreinigungen in der Produktionsumgebung. Um die Anzahl der Defekte zu reduzieren, investieren Hersteller viel Geld in ihre Ausrüstung wie Reinraumumgebungen, um eine Kontamination von vornherein zu verhindern. Außerdem versuchen sie, mithilfe moderner Inspektionstechniken auftretende Defekte zu erkennen und ihre Auswirkungen zu minimieren, um ihre Ausbeute und Kosteneffizienz zu optimieren.
Laser in der Wafer-Inspektion
Laser sind ein ideales Werkzeug für die Halbleiterinspektion, da es sich um eine berührungslose Methode handelt, die eine unübertroffene Kombination aus Empfindlichkeit und Geschwindigkeit bietet. Außerdem sind sie äußerst vielseitig und können für eine Vielzahl unterschiedlicher Prüfaufgaben optimiert werden.
Daher werden Laser bereits seit der Frühzeit der Mikroelektronik für Inspektionen eingesetzt. In den späten 1960ern – nicht lange, nachdem Laser erstmals auf den Markt kamen – fanden sie bereits bei messtechnischen Aufgaben Anwendung, etwa für die Messung der Ebenheit und Dicke von Wafern.
In den 1980ern, als Halbleitergeräte kleiner und komplexer wurden, begann die Branche mit der Einführung anderer laserbasierter Inspektionsmethoden. Diese Techniken umfassten die Ausrichtung eines Laserstrahls auf die Wafer-Oberfläche und die Analyse des zurückgeworfenen Lichts, um Defekte wie Partikel, Kratzer und Musterabweichungen zu erkennen. Damals wurden ausgeklügeltere laserbasierte Inspektionssysteme entwickelt, die in der Lage waren, zunehmend kleinere Defekte zu erkennen, was für die Fertigung von qualitativ hochwertigen Halbleitern entscheidend war.
In den folgenden Jahrzehnten kam es zu signifikanten Verbesserungen bei laserbasierten Methoden, unter anderem durch die Einführung der Scatterometrie und anderer fortschrittlicher Messtechnologien. Die Scatterometrie, bei der mithilfe von Lasern die Muster des von einer Wafer-Oberfläche zurückgeworfenen Lichts analysiert werden, ermöglichte die Erkennung kleinster Defekte, die zuvor nicht aufgespürt werden konnten.
Warum kleine Schaltkreise eine große Herausforderung für die Inspektion darstellen
Die Wafer-Inspektion wird mit jeder neuen Chip-Generation immer wichtiger und herausfordernder. Das liegt daran, dass die Chiparchitektur mit jeder Verkleinerung des Knotens komplexer wird und neue Materialien sowie kleinere, kompliziertere Merkmale verwendet werden. Durch diese Fortschritte werden nicht nur die Leistungsgrenzen verschoben, sondern es entstehen auch neue Möglichkeiten für das Auftreten von Fehlern. Und wenn man in einem so kleinen Maßstab arbeitet, kann selbst der kleinste Fehler auf dem Wafer zu einem nicht funktionierenden Chip führen.
Daher müssen die Hersteller nach wichtigen Prozessschritten eine strenge Inspektion durchführen, um Defekte frühzeitig zu erkennen. Die Durchführung dieser Inspektionen trägt zur Optimierung der Ausbeute (verwendbare Chips pro Wafer), des Durchsatzes (Produktionsgeschwindigkeit) und letztlich der Rentabilität bei.
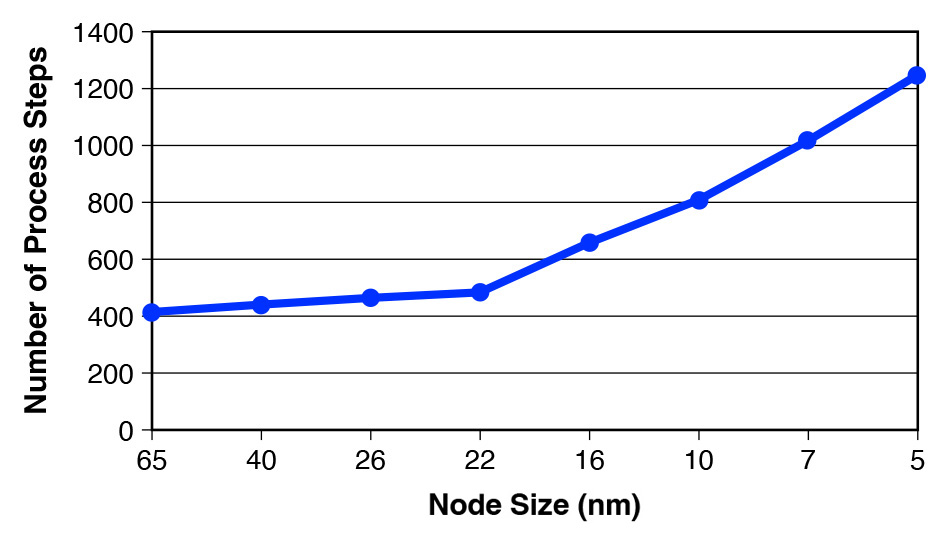
Durch die Verkleinerung der Schaltkreise hat sich der Bedarf an Inspektionen drastisch erhöht, die oft am besten mit Lasern durchgeführt werden können.
Aber ein wichtiges Konzept hierbei ist, dass Laser mit kürzeren Wellenlängen erforderlich sind, um die Grenzen der Defekterkennung weiter zu verschieben. Der Grund dafür ist, dass die Effizienz der Lichtstreuung von der Beziehung zwischen Lichtwellenlänge und der Größe der inspizierten Merkmale oder Defekte abhängt. Wenn die Merkmale deutlich kleiner sind als die Wellenlänge des Lichts, nimmt die Streuungseffizienz ab und das von diesen Merkmalen oder Defekten ausgesandte Signal wird schwächer. Das bedeutet, dass die Defekte nicht erkannt werden können – zumindest nicht in der Zeitspanne, die für die Massenproduktion von Halbleitern relevant ist.
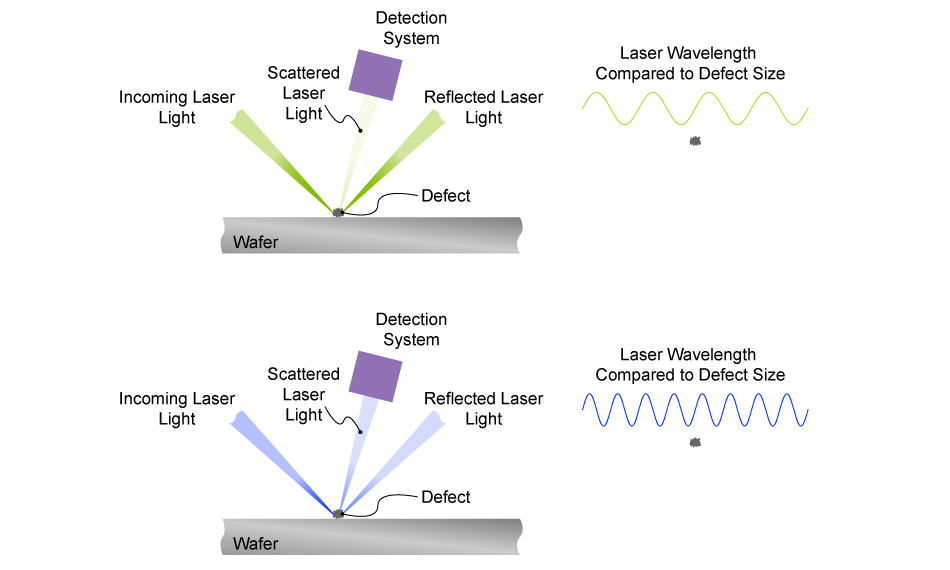
Aufgrund der Beziehung zwischen Lichtstreuung und Defektgröße sind kürzere Laserwellenlängen erforderlich, um kleinere Defekte zu erkennen. Derzeit werden für die herausforderndsten Wafer-Inspektionsaufgaben 266-nm-Laser eingesetzt.
Vor zwei Jahrzehnten, als Transistoren noch bequem 110 nm oder größer waren, reichten sichtbare grüne (532 nm) und ultraviolette (UV) Laser für die Fehlererkennung aus. Aber kleiner werdende Schaltkreisbestandteile haben in der Branche zu einer Bewegung hin zu tief-ultravioletten (DUV) Lasern geführt.
Coherent hat mit der Einführung unseres bahnbrechenden Azure-Lasers im Jahr 2002 dieser Herausforderung in Angriff genommen. Dieser Laser verwendet optisch gepumpte Halbleiter (OPS), um grünes Licht zu erzeugen, das dann per Frequenzverdoppelung in DUV (266 nm) überführt wird.
Der Azure liefert Dauerstrich (CW)-Leistung auf einer einzigen, frequenzstabilisierten Wellenlänge. Seine Kombination aus enger Wellenlänge, hoher Leistung und extremer Stabilität ermöglicht eine zuverlässige Erkennung kleiner Defekte in der Geschwindigkeit, die für eine Halbleiterherstellung mit hohem Durchsatz erforderlich ist.
Coherent hebt sich dadurch hervor, dass wir Hochleistungs-DUV-Laser mit außergewöhnlicher Lebensdauer und Zuverlässigkeit produzieren können. Diese Fähigkeit basiert auf mehreren Faktoren.
Erstens produzieren wir unsere eigenen nichtlinearen Kristalle. Für die Arbeit im tiefen UV-Bereich sind außergewöhnlich hochwertige Kristalle erforderlich, die mit enormer Präzision hergestellt werden müssen. Der einzige Weg, die Qualitätsstufe zu erreichen, die wir für unsere frequenzverdoppelnden Kristalle benötigen, ist, sie selbst herzustellen.
Dann wenden wir unsere patentierte PermAlign-Konstruktion für die optischen Halterungen innerhalb des Lasers an. Diese Halterungen bieten außergewöhnlich langanhaltende Stabilität, was bedeutet, dass niemals Anpassungen erforderlich werden. Mithilfe von PermAlign-Halterungen können wir den Laserresonator hermetisch abdichten. Und das ist entscheidend, um das Eindringen von Verunreinigungen aus der Umgebung zu verhindern, die die Laserleistung beeinträchtigen könnten. Zudem werden die Laser anfangs in Reinraumbedingungen mithilfe halbautomatisierter Methoden montiert, um von Anfang an jegliche Kontamination zu vermeiden. Dadurch erzielen wir ein hohes Maß an Konsistenz zwischen den einzelnen Einheiten.
Go/No-Go-Prüfung der Teilekonformität an einem Wafer Chuck im Prozess.
Eine weitere Anforderung der Wafer-Inspektion sind sehr schnell bewegliche Teile-Handhabungsmechaniken und eine extrem stabile Oberfläche (um Messrauschen zu minimieren). Wir bieten reaktionsgebundenes SiC (RB-SiC) für Tische und andere Werkezuge an, die dank ihrer einzigartigen Kombination aus geringer thermischer Expansion (CTE), hoher Festigkeit und hohem Stärke-Gewichtsverhältnis auch für die herausforderndsten Inspektionssysteme geeignet sind.
Zukünftige Entwicklungen
Mit immer kleineren Knoten in der Halbleiterindustrie werden die Anforderungen an Inspektionslaser noch strenger. Glücklicherweise deckt sich dies perfekt mit den Kernkompetenzen von Coherent. Wir arbeiten eng mit den führenden Herstellern von Wafer-Fabrikationsanlagen zusammen, um sicherzustellen, dass unsere Produkte die Anforderungen der Halbleiterfertigung nicht nur erfüllen, sondern vorwegnehmen. Auf diese Weise unterstützt Coherent die Hersteller bei der Bewältigung der heutigen und zukünftigen Herausforderungen bei der Inspektion.
Erfahren Sie mehr über Azure-Laser von Coherent.