Coherent 高意半导体制造:晶圆检测
Coherent 高意的紫外激光器能够检测半导体晶片上的微小缺陷,这是最大限度地提高良率和降低成本的关键。
2024 年 10 月 17 日,作者:Coherent 高意
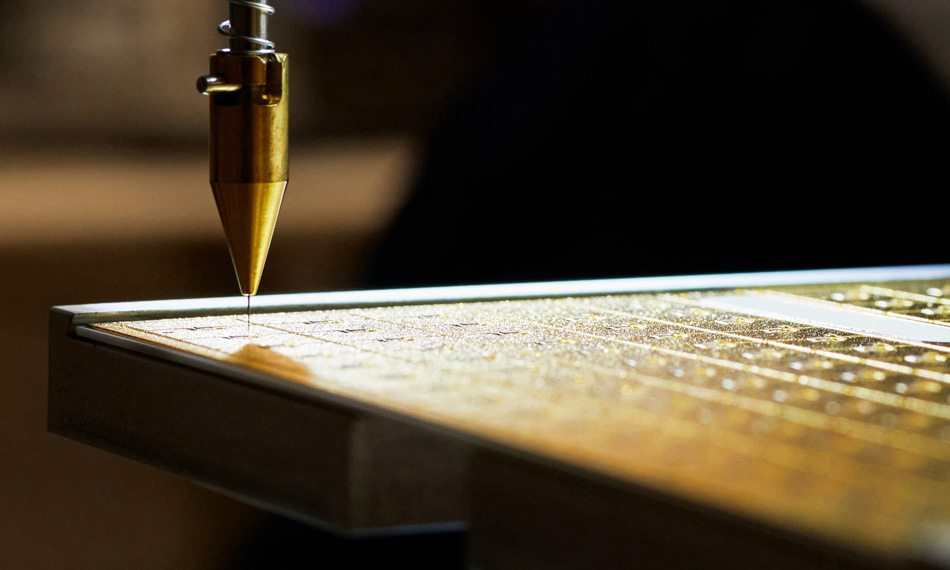
NASA 用于登月的阿波罗制导计算机 (AGC) 于20世纪60年代制造, 当时耗资约 1.5 亿美元(按今日币值计算约为 10 亿美元)。它的体积大约相当于一台微波炉,重量约为32公斤。
今天,一款顶配的 iPhone 15 售价 1600 美元,当然可以轻松握在手中。而且,就每秒可执行的操作数量而言,这款iPhone的性能比AGC强大约2亿倍。
英特尔联合创始人戈登·摩尔曾预测微处理器性能会提升。他提出,微芯片上的晶体管数量大约每两年会翻一番。但刚才提到的对比也凸显了摩尔定律的一个重要推论,有时被称为摩尔第二定律。即,每美元所能买到的微处理器性能也会随时间呈指数级增长。
摩尔第一定律和第二定律都经得起时间的考验,因为半导体行业一直在同时努力实现两个不同的目标。一是让电路元件和组件变得更小。第二是不断降低成本。
半导体制造的一个关键成本因素是良率,而影响良率的一个重要因素是生产环境中的缺陷和污染物。为了减少缺陷,制造商在设备方面投入了大量资金,例如,打造无尘室环境,从一开始就防止污染。此外,他们还部署了先进的检测技术来检测并最大限度地减少任何已发生缺陷的影响,从而确保最佳良率和成本效率。
晶圆检测中的激光
激光是半导体检测的理想工具,因为它是一种非接触式方法,兼具无与伦比的灵敏度和速度。此外,激光还具有高度通用性,经过优化后可执行各种不同的检测任务。
因此,从微电子工业早期开始,激光就被用于检测。20 世纪 60 年代末,激光刚进入市场后不久,就已用于测量晶圆平整度和厚度等计量任务。
20 世纪 80 年代,随着半导体器件变得更小、更复杂,业界开始采用其他基于激光的检测方法。这些方法包括将激光束对准晶圆表面,并分析返回的光以检测缺陷,例如颗粒、划痕和图案偏差。这一时期见证了更复杂的基于激光的检测系统的发展,这些系统能够检测对高质量半导体生产至关重要的越来越小的缺陷。
在接下来的几十年里,随着散射测量法和其他先进计量技术的引入,基于激光的方法取得了重大进步。散射测量法使用激光来分析从晶圆表面反射的光模式,从而能够检测到以前无法检测到的细微缺陷。
为何小型电路给检测带来巨大挑战
随着每一代芯片的更迭,晶圆检测变得越来越重要且更具挑战性。这是因为随着节点尺寸的减小,芯片架构都会变得更加复杂,采用了新材料和更小、更精细的特性。这些进步在突破性能界限的同时,也带来了新的缺陷发生机会。在如此小的尺寸下工作时,晶圆上即使最小、最轻微的缺陷也可能导致芯片无法功能。
因此,制造商必须在关键工艺后进行严格检查,以便尽早发现缺陷。执行这些检测有助于优化良率(每片晶圆上的可用芯片数量)、吞吐量(生产速度)以及最终盈利能力。
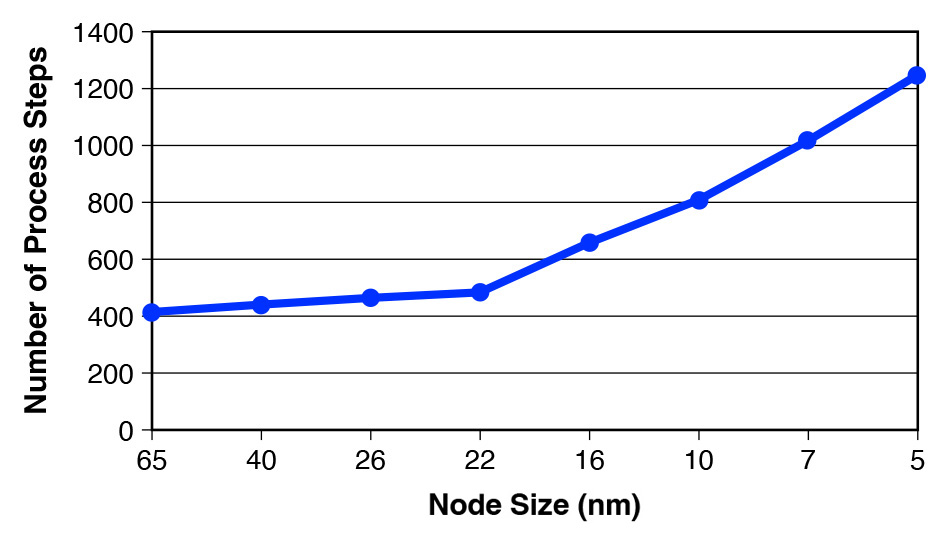
小型电路特性极大地增加了对检测的需求,而激光通常是执行检测的最佳工具。
但这里需要理解的一个关键概念是,要突破缺陷检测的界限,需要使用波长更短的激光。这是因为光散射的效率取决于光波长与被检测特性或缺陷尺寸之间的关系。当特性尺寸远小于光波长时,散射效率会降低,这些特性或缺陷发出的信号会减弱。这意味着无法检测到缺陷,至少在与大批量半导体制造相关的时间范围内无法检测到。
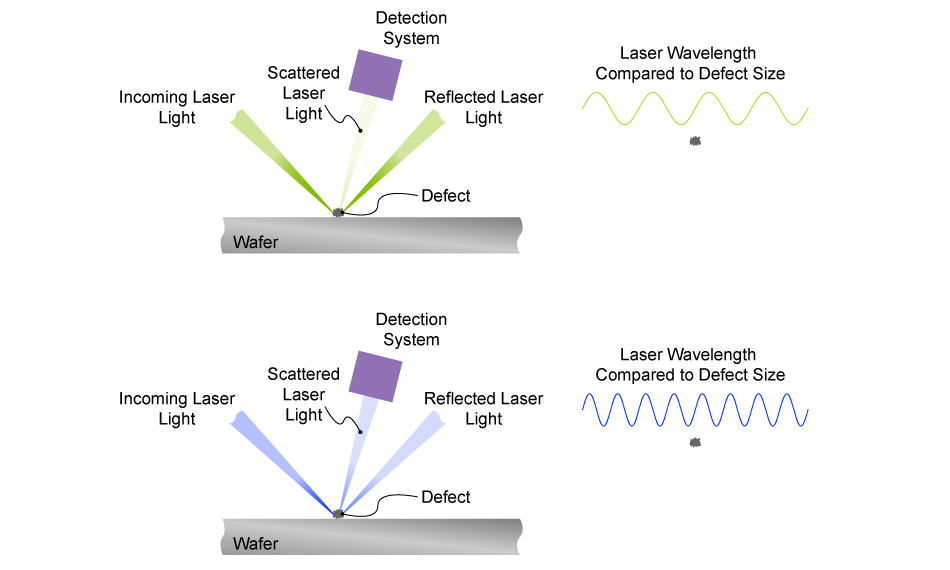
由于光散射和缺陷尺寸之间的关系,需要波长更短的激光来检测更小的缺陷。目前,用于最严苛晶圆检测任务的是266纳米激光。
二十年前,当晶体管的尺寸达到 110 nm 或以上时,可见绿色激光(532 nm)和紫外 (UV) 激光器就足以满足缺陷检测的需求。但随着电路特征尺寸的不断缩小,业界开始转向使用深紫外(DUV)激光器。
Coherent 高意于 2002 年推出了开创性的 Azure 激光器,直面这一挑战。该激光器利用光泵浦半导体 (OPS) 技术产生绿光输出,然后通过倍频技术将其转换为深紫外光(266纳米)
Azure 能够在单个、频率稳定的波长下提供连续波(CW)输出。其波长窄、功率高、噪声低、稳定性强的特点,能够在高吞吐量半导体制造所需的速度下,可靠地检测出微小的缺陷。
Coherent 高意凭借制造高性能、高寿命、高可靠性的深紫外激光器而脱颖而出。我们之所以能做到这一点,原因有以下几点:
首先,我们自行生产非线性晶体。在深紫外领域工作,需要制造精度极高的高质量晶体。为了满足倍频晶体所需的品质水平,我们唯一的选择是自己生产。
其次,我们在激光器内部的光学支架上采用了专利PermAlign结构。这些支架提供卓越的长期稳定性,这意味着无需调整。PermAlign 支架使我们能够密封激光谐振器。这是防止任何可能影响激光器性能的环境污染物进入的关键。此外,激光器最初是在洁净室条件下使用半自动方法组装的,以避免在一开始就造成任何污染。这也确保了各台激光器之间的高度一致性。
在晶圆卡盘上进行部件合格性(通过/不通过)检查。
晶圆检测的另一个要求是高速运动和部件处理机制,以及极其稳定的表面(以最大限度地减少测量噪音)。我们为工作台和其他工具提供反应烧结碳化硅(RBSiC),这些工具结合了低热膨胀系数(CTE)、高强度和高强度重量比等独特优势,能够满足最严苛的检测系统的需求。
未来展望
随着半导体行业向更小的节点发展,对检测激光器的要求变得更加严格。幸运的是,这与 Coherent 高意的核心优势完全契合。我们与领先的晶圆设备制造商保持密切合作,确保我们的产品不仅满足,而且能够预测半导体制造工艺的需求。因此,Coherent 高意帮助制造商应对当前和未来的检查挑战。
详细了解 Coherent Azure 激光器。