LASER SICHERN MICROLED-DISPLAY PRODUKTION
Durch laserunterstütztes Bonden wird eines der letzten Hindernisse bei der Massenproduktion von microLED-Displays umgangen.
28. März 2024 von Coherent
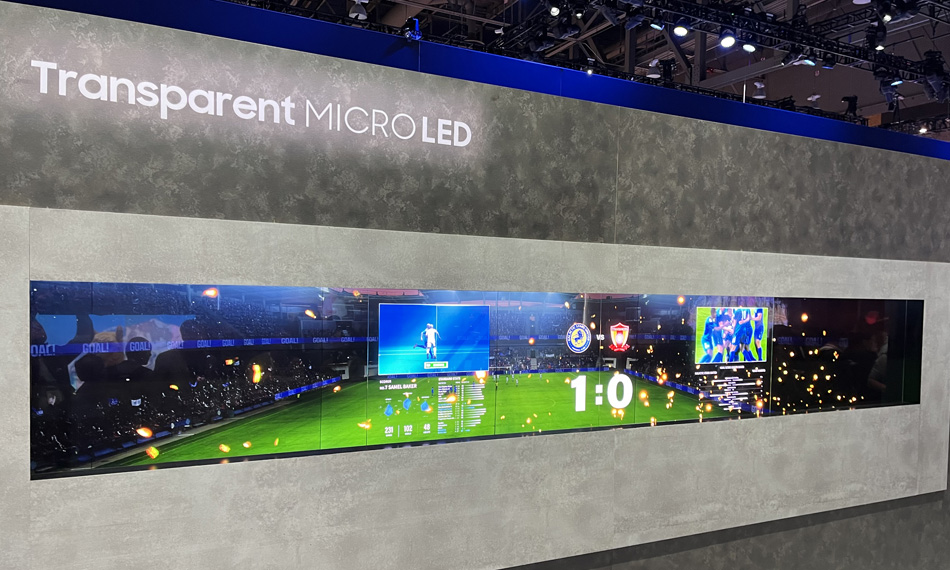
Samsung begeisterte die Besucher der Consumer Electronics Show (CES) im Januar 2024 mit seinem riesigen, transparenten microLED-Display. Aber microLED-Displays bieten mehr als nur gutes Aussehen. Sie bieten mehrere Vorteile gegenüber anderen Displaytechnologien wie LEDs und OLEDs. Dazu gehören eine verbesserte Energieeffizienz, längere Lebensdauer, höhere Helligkeit und bessere Farbgenauigkeit. Darüber hinaus können Hersteller durch die Verwendung von microLEDs Größe, Form und Auflösung problemlos ändern und so neue Displaydesigns erstellen, ohne dass umfangreiche Umrüstungen erforderlich sind.
Trotz dieser Vorteile haben sich microLEDs noch nicht durchgesetzt. Dies liegt daran, dass ihre Herstellung im Allgemeinen komplizierter ist als die anderer Displays. Für eine erfolgreiche Kommerzialisierung dieser Technologie müssen noch einige erhebliche Herausforderungen bewältigt werden.
Excimerlaser verleihen microLEDs einen LIFT
Um zu verstehen, wo diese Herausforderungen auftreten, veranschaulicht die Zeichnung einige der wichtigsten Schritte bei der Herstellung von microLED-Displays. Nach Abschluss dieser Schritte folgen noch verschiedene weitere Prüfschritte und ein „Alterungsprozess“. Große Displays werden durch die Kombination mehrerer kleinerer Panels hergestellt, sodass in diesem Fall zusätzliche Montage- und Verpackungsschritte erforderlich sind.

1) Rote, grüne und blaue LEDs werden getrennt auf transparenten Substraten hergestellt. 2) LLO: Die LEDs werden mit einem temporären Träger verbunden, der mit einem Kleber versehen ist, um sie zu halten. Ein Excimerlaser wird durch das transparente Substrat fokussiert und trennt die LEDs davon ab. 3) LIFT: Ein Excimerlaser wird durch den temporären Träger fokussiert, um die einzelnen LEDs zu trennen und sie zu den Lötpads auf dem endgültigen Substrat zu befördern. 4) LAB: Ein Diodenlaser erhitzt zahlreiche LEDs und Löthöcker gleichzeitig, um sie schnell zu schmelzen und eine endgültige Verbindung herzustellen.
Wie die meisten Halbleiterbauelemente werden LEDs ursprünglich epitaktisch auf einem Wafer gezüchtet. Typischerweise handelt es sich hierbei um ein Saphirsubstrat. Für die Herstellung jedes Pixels eines microLED-Displays sind separate LEDs erforderlich, die in jeder der Primärfarben – Rot, Grün und Blau – emittieren. Aber jeder Wafer enthält nur LEDs einer einzigen Farbe. Daher müssen die LEDs in einzelne integrierte Schaltkreise aufgeteilt und dann im erforderlichen Muster angeordnet werden, um das endgültige Display zu erhalten.
Für die ersten beiden großen Schritte dieses Prozesses haben sich Excimerlaser bereits als kostengünstige Werkzeuge bewährt. Konkret werden zunächst die einzelnen LED-Chips mittels Laser-Lift-Off (LLO) vom Saphir-Wafer getrennt und auf einen temporären Träger übertragen.
Als nächstes wird die laserinduzierte Vorwärtsübertragung (LIFT) verwendet, um einen „Massentransfer“ durchzuführen. Dies ist der Prozess, bei dem die Chips vom temporären Träger auf das endgültige Display-Substrat übertragen werden. Am wichtigsten ist, dass beim Massentransfer die LEDs im gewünschten Pixelmuster angeordnet werden.
Die Herausforderung bei der microLED-Montage
Nachdem die LEDs auf dem Substrat angebracht sind, müssen sie mit diesem verklebt und elektrisch verbunden werden. Sonst würde das Display nicht leuchten und alle LEDs würden bei Bewegung einfach abfallen!
Um diesen Vorgang zu erleichtern, werden zunächst an allen vorgesehenen Stellen der elektrischen Verbindung Lotkügelchen auf dem Substrat platziert. Anschließend wird das Lot nach der Chipplatzierung mittels LIFT erhitzt, bis es schmilzt. In diesem Zustand umströmt es die elektrischen Kontakte sowohl auf dem Substrat als auch auf dem Chip. Anschließend kühlt es ab und verfestigt sich wieder, wodurch sowohl eine elektrische als auch eine mechanische Verbindung zwischen ihnen entsteht. Dies ist eine Standardmontagetechnik in der gesamten Elektronikindustrie.
Die gebräuchlichste Methode zum Schmelzen des Lots wird „Mass Reflow“ (MR) genannt. Dabei wird im Wesentlichen die gesamte Anordnung aus Substrat, Lotkugeln und Chips in einen Ofen gegeben. Die Temperatur wird zyklisch verändert, um das Lot zu schmelzen und dann wieder abzukühlen.
Doch das Massen-Reflow-Verfahren hilft den Herstellern von microLEDs nicht dabei, den Sprung zu kleineren LEDs zu schaffen, die mit höherer Positionsgenauigkeit enger beieinander platziert werden müssen. Das Problem besteht darin, dass der Aufheizzyklus mehrere Minuten dauert. Dies führt zu einer erheblichen Wärmebelastung aller Komponenten und kann zu Verformungen der Komponenten, thermomechanischen Spannungen und einer physikalischen Verschiebung der Position der Chips auf dem Substrat führen. Durch die lange Prozesszeit im Massen-Reflow-Ofen steigt auch das Risiko schlechter elektrischer Verbindungen. Auch der Prozess selbst ist energieintensiv.
Thermisches Kompressionsbonden (TCB) ist eine Alternative, die das durch die Magnetresonanz (MR) verursachte Verformungsrisiko verringert. TCB fügt Kraft hinzu, während Hitze angewendet wird, wodurch die Höhe und Form der Verbindungen besser kontrolliert werden kann. Es ist jedoch eine komplexe Düse erforderlich, die an die jeweilige Chip- und Gehäusegröße angepasst ist und im Wesentlichen jeweils nur einen einzelnen Chip verklebt. Dies macht es weniger geeignet für microLED-Anwendungen, bei denen buchstäblich Millionen von LED-Chips verbunden werden müssen, um ein einziges Display herzustellen.
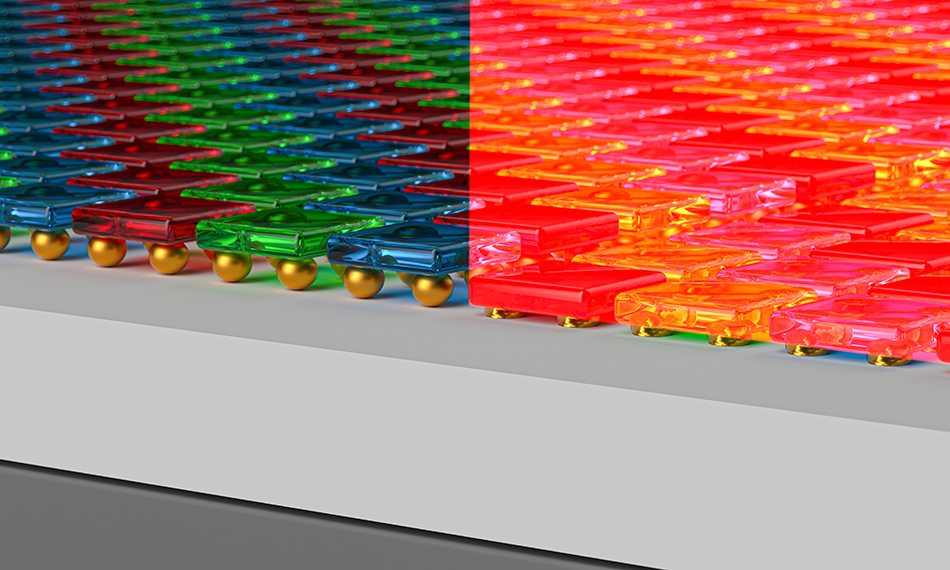
Laserunterstütztes Bonden
Laserunterstütztes Bonden (LAB) löst all diese Probleme. Beim LAB wird die Ausgangsleistung eines leistungsstarken Infrarot-Diodenlaserstrahls in ein Rechteck geformt. Die Intensitätsverteilung wird homogenisiert, sodass sie über die gesamte Strahlfläche hinweg äußerst gleichmäßig ist. Die Abmessungen des rechteckigen Strahls variieren je nach Anwendung, aber es ist durchaus möglich, es groß genug zu machen, um Tausende oder sogar Millionen von LEDs auf dem Substrat gleichzeitig zu beleuchten.
Während des LAB wird der Laser sehr kurz eingeschaltet – für weniger als eine Sekunde. Dies ist jedoch ausreichend Zeit, um genügend Wärme in die Baugruppe zu übertragen und das Lot zu schmelzen. Sie ist jedoch zu kurz, um eine nennenswerte Masseerwärmung hervorzurufen, die zu einem Verzug oder einer Positionsverschiebung der Chips führen würde. Der Laser ermöglicht eine präzise Steuerung des Heizzyklus, bei Bedarf auch mit Abkühlphasen. Dadurch erfolgt der Lötvorgang schnell und ohne nennenswerte negative Folgen. Die kurze Zykluszeit von LAB macht es außerdem wesentlich energieeffizienter als MR oder TCB.
Bessere Laser für ein verbessertes laserunterstütztes Bonden
Bezogen auf den Laser besteht eine entscheidende Anforderung für LAB darin, dass die Strahlintensität über die gesamte Fläche gleichmäßig ist. Dies ist notwendig, um eine gleichmäßige Erwärmung des Lots und damit gleichbleibende Ergebnisse zu erzielen. Ziel ist es, selektiv nur den gewünschten Bereich zu erwärmen, der eine bestimmte Anzahl von microLEDs enthält, und nicht umliegende Bereiche überhaupt zu erwärmen. Daher ist es besonders wichtig, ein rechteckiges Strahlmuster zu erzeugen, bei dem die Intensität in Randnähe nicht stark abnimmt. Andernfalls besteht die Möglichkeit, dass die LEDs in diesem Bereich überhaupt nicht verklebt werden. Allerdings muss die Strahlintensität außerhalb des beleuchteten Bereichs sehr schnell abfallen.
Die Coherent HighLight DL-Serie fasergekoppelter Diodenlaser kann mit unserer PH50 DL Zoom Optik kombiniert werden, um genau diese Art von sehr gleichmäßigem rechteckigem Strahl zu erzeugen. Typischerweise wird für das LAB von microLEDs ein 4 kW HighLight DL-Laser (zwischen 1 und 4 kW) verwendet.
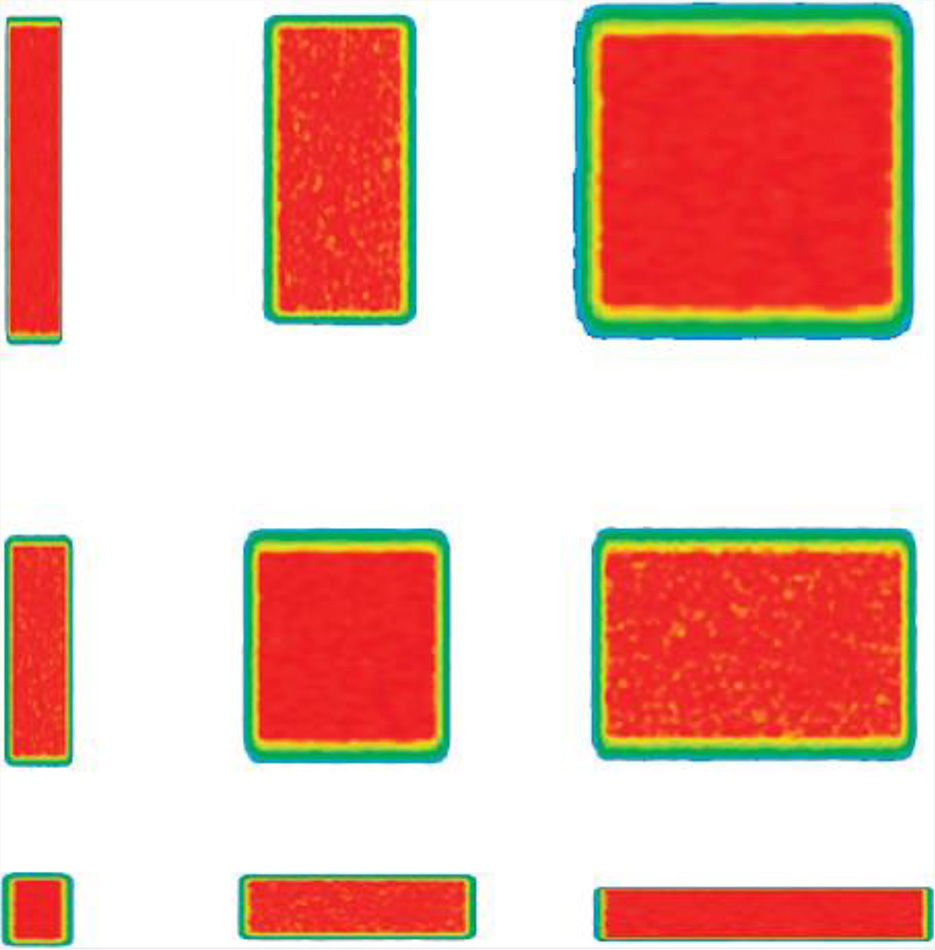
Die Coherent PH50 DL Zoom Optik wandelt den fasergekoppelten Multi-Mode-Ausgang eines Diodenlasers der HighLight DD-Serie in einen äußerst gleichmäßigen rechteckigen Strahl um. Länge und Breite dieses Rechteck können unabhängig voneinander dynamisch angepasst werden. Die hier gezeigten Spotgrößen reichen von 12 x 12 mm bis 110 x 110 mm, es sind jedoch auch andere Zoomkonfigurationen verfügbar.
Diese Kombination bietet durch die Verwendung unseres proprietären optischen Designs eine bessere Intensitätsgleichmäßigkeit als jedes Konkurrenzprodukt. Die Strahlhomogenisierung wird durch den Einsatz einer Reihe von Mikrolinsen erreicht, die den eingehenden Laserstrahl in zahlreiche „Teilstrahlen“ aufteilen. Diese werden dann erweitert und überlappt, um eine äußerst gleichmäßige Intensitätsverteilung zu erzielen.
Ein weiterer großer Vorteil der Coherent PH50 DL Zoom Optik ist, dass sie „on-the-fly“, also sogar während des Prozesses, einstellbar ist. Das heißt, sowohl die Länge als auch die Breite des rechteckigen Strahls können je nach Bedarf über einen weiten Bereich unabhängig voneinander eingestellt werden. Diese Zoomfunktion ist für Hersteller bei der Entwicklung und Qualifizierung ihres Prozesses nützlich. Es ermöglicht ihnen, verschiedene Konfigurationen auszuprobieren, um herauszufinden, was am besten und effizientesten funktioniert. Natürlich kann Coherent den gleichen Ansatz nutzen, um feste (nicht Zoom-)Optiken herzustellen, die spezifische Kundenanforderungen erfüllen. Solche Linienstrahlen können von wenigen Millimetern bis zu 1000 mm betragen.
LLO und LIFT haben sich bereits als zwei Schlüsseltechnologien in der microLED-Produktion etabliert. Nun scheint es, als würde ein weiteres Verfahren auf Basis eines Coherent Laser – LAB – die Massenproduktion hochauflösender microLED-Displays erleichtern.
Erfahren Sie mehr über Coherent Laser für LAB.