Was sind MicroLED-Displays?
In einigen Jahren wird der Markt für µLED-Displays ein Volumen im Wert von mehr als 10 Milliarden US-Dollar aufweisen. Erfahren Sie, warum Laser dabei eine entscheidende Rolle spielen.
24. Juni 2021 von Coherent

MicroLEDs (µLEDs) sind eine relativ neue Technologie für brillante, hochauflösende Displays, die wirtschaftlich auf riesige Abmessungen vergrößert werden – problemlos auf mehr als 6 Meter (20 Fuß). Derzeit werden sie für große Displays in Konferenzräumen, Arenen, Konzerthallen und im Außenbereich eingesetzt. Zukünftig werden sie wahrscheinlich eine gängige Technologie für große Fernsehgeräte darstellen. In den nächsten fünf Jahren wird der Markt für µLED-Displays auf einen Wert von mehr als 10 Milliarden US-Dollar wachsen – und Laser spielen bei ihrer Herstellung eine entscheidende Rolle.
Der Unterschied zwischen AMOLEDs und MicroLEDs
Bei AMOLED und anderen derzeit für Mobilgeräte und Fernsehgeräte verwendeten Displaytechnologien werden die lichtemittierenden (oder lichtfilternden) Pixel direkt auf der Displayglasscheibe erzeugt. Um größere Displays herzustellen, müssen mehrere Schritte mit teuren OLED-Materialien auf einem entsprechend großen Panel ausgeführt werden, das alle erforderlichen Schaltkreise enthält. Dieses wird mit zunehmender Größe teurer und immer weniger praktikabel. Aus diesem Grund können Fernsehgeräte mit einem Displaymaß von mehr als 80 Zoll Zehntausende US-Dollar kosten.
MicroLED-Displays sind anders. Die einzelnen LED-Emitter werden in Massenproduktion auf relativ kleinen Saphir-Wafern hergestellt. Sie sind dicht aneinander gepackt, was zu geringen Stückkosten führt. Diese µLEDs werden dann vom Wafer entfernt und auf eine Glasscheibe mit bereits aufstrukturiertem Schaltkreis übertragen. Durch Vergrößern der Abstände zwischen den µLEDs lassen sich immens große Displays herstellen. Der Hauptkostenfaktor ist dann die Pixelanzahl und nicht die Glasgröße. Das Aneinanderreihen vieler einzelner Panels hält auch die Kosten für größere Displays in Grenzen.
Millionen und Abermillionen von Pixeln
Doch die Sache hat einen großen Haken. Jedes Pixel eines µLED-Displays besteht aus drei separaten LED-Emittern (rot, grün und blau), die in der Tat sehr klein sind. Der Stand der Technik liegt derzeit bei etwa 50 × 50 Mikrometern und wird voraussichtlich 10 × 10 Mikrometer erreichen. Und es gibt buchstäblich Millionen von ihnen. Zum Beispiel enthält selbst ein hochauflösendes Standard-Display (1920 × 1080) über 2 Millionen Pixel. Und wir sollten nicht vergessen, dass jedes dieser Pixel drei separate µLEDs benötigt. Ein wirklich großes Display kann also Hunderte von Millionen µLEDs umfassen.
Die Herausforderung bei der Herstellung besteht darin, all diese winzigen LED-Lichtquellen vom Saphir-Wafer, auf dem sie gezüchtet wurden, auf das endgültige Displayglas zu übertragen. Und sie dabei sehr genau zu platzieren und nicht zu beschädigen. Alle mechanischen Verfahren, seien es Vakuumaufnehmer oder sehr präzise Stellglieder, wären beim Handhaben der µLEDs zu langsam und wahrscheinlich zu grob. Es überrascht daher nicht, dass Laser genau den sanften Touch ermöglichen, der für solch filigrane und anspruchsvolle Abläufe erforderlich ist.
Was ist Laser-Induced Forward Transfer (LIFT)? Danke für die Frage.
Als praktikabel erweist sich ein Verfahren namens Laser-Induced Forward Transfer (LIFT). Wie funktioniert es? Dieses Video erklärt es. Kurz gesagt, ist es ein zweistufiges Verfahren. Zuerst werden die µLEDs vom Saphir-Wafer, auf dem sie gezüchtet wurden, getrennt und mit einer anderen laserbasierten Technik namens Laser Lift-Off (LLO) auf einen temporären Träger übertragen. Dadurch bleibt der Abstand der µLEDs auf dem temporären Träger gegenüber dem auf dem Wafer unverändert.
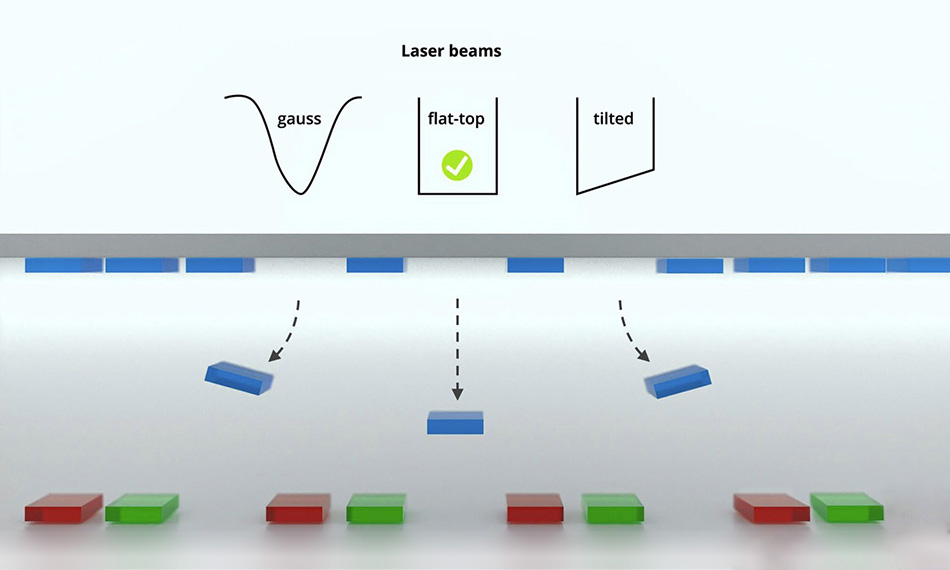
Abbildung Bei LIFT durchdringt ein großflächiger Laserstrahl eine Fotomaske, sodass nur bestimmte Pixelelemente freigegeben und auf das Displaysubstrat geschoben werden. Für das perfekte Platzieren entscheidend ist ein einheitlicher sogenannter Top-Hat-Beam (nicht maßstabsgetreu).
Als nächstes wird LIFT angewendet. Dabei treten Pulse eines Ultraviolettlasers (Excimer-Lasers) durch die Rückseite des transparenten Trägers ein. Das Laserlicht wird von der dünnen Klebstoffschicht, mit der die µLEDs auf dem temporären Träger gehalten werden, absorbiert und verdampft so diese Schicht. Dadurch werden die µLEDs abgeblasen und auf das endgültige, extrem nahe platzierte Displaypanel geschoben. Der Klebstoff auf dem Displaypanel fixiert die µLEDs.
Der Strahl und die Maske
Das Geheimnis dabei: Der rechteckige Laserstrahl passiert eine Maske mit Löchern, die den gleichen Abstand wie die Pixel auf dem endgültigen Displaypanel aufweisen. Somit wird nur jede fünfte oder sogar nur jede zehnte µLED von einem bestimmten Laserpuls auf das Displaypanel geschoben. Die Maske gibt den Optikpfad vor und der temporäre Träger wird dann um eine kurze Strecke zum benachbarten µLED-Satz versetzt. Das Displaypanel jedoch wird um eine große Strecke versetzt. Der Vorgang wird an einem neuen Teil des Displaypanels wiederholt. Damit kann also eine große Anzahl von µLEDs auf relativ kleinen Saphir-Wafern wirtschaftlich hergestellt und dann in viel größeren Abständen auf einem einzigen großen Panel platziert werden. Der andere große Vorteil von LIFT ist seine Geschwindigkeit. Mit jedem Puls werden Tausende von µLEDs bewegt. Bei einer Laserpulsrate von 500 Pulsen pro Sekunde (500 Hz) kann in nur einer Sekunde eine Fläche von bis zu 32 mm × 1 Meter mit µLEDs bestückt werden!
Wir arbeiten daran
Coherent produziert bereits ein Tool namens UVtransfer für das Verarbeiten von µLEDs für Displays. Es führt tatsächlich drei separate Prozesse durch: Laser Lift-Off (LLO), Laser-Induced Forward Transfer (LIFT) und Repair/Trimming für defekte Pixel. Dieses 3-in-1-Tool wird Verarbeitungsstandards setzen und das praktische und wirtschaftliche Potenzial für die Herstellung großer µLED-Displays belegen.
Verwandte Ressourcen