레이저가 MicroLED 디스플레이를 다시 살립니다.
레이저 보조 본딩은 마이크로LED 디스플레이 대량 생산에 남아 있는 장애물 중 하나를 우회합니다.
2024년 3월 28일, Coherent
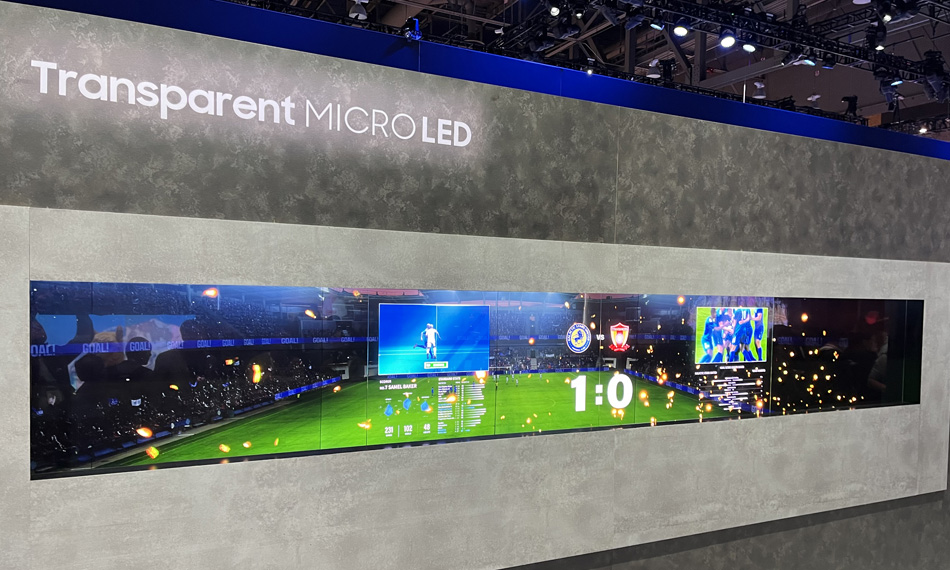
삼성은 2024년 1월 CES(Consumer Electronics Show)에서 거대하고 투명한 마이크로LED 디스플레이로 참석자들을 놀라게 했습니다. 그러나 MicroLED 디스플레이에는 단지 멋진 외관 이상의 것이 있습니다. 이는 LED 및 OLED와 같은 다른 디스플레이 기술에 비해 몇 가지 장점을 제공합니다. 여기에는 에너지 효율성 향상, 수명 연장, 밝기 향상, 색상 정확도 향상 등이 포함됩니다. 또한, 마이크로LED를 활용하면 제조업체는 크기, 모양, 해상도를 쉽게 수정하여 광범위한 재조정 없이도 새로운 디스플레이 디자인을 만들 수 있습니다.
이러한 장점에도 불구하고 마이크로LED는 아직 일반화되지 않았습니다. 이는 일반적으로 다른 디스플레이보다 만들기가 더 복잡하기 때문입니다. 이 기술의 성공적인 상용화를 위해서는 여전히 극복해야 할 몇 가지 중요한 과제가 있습니다.
엑시머 레이저로 MicroLED 생산 프로세스 개선
이러한 문제가 발생하는 위치를 이해하는 데 도움이 되도록 그림에서는 microLED 디스플레이 생산의 주요 단계 중 일부를 보여줍니다. 이 작업이 완료된 후에는 다양한 다른 테스트 단계와 “에이징” 프로세스가 있습니다. 대형 디스플레이는 여러 개의 작은 패널을 결합하여 만들어지므로 이 경우 추가 조립 및 포장 단계가 필요합니다.

1) 빨간색, 녹색, 파란색 LED가 투명 기판에 개별적으로 제작됩니다. 2) LLO: LED를 접착제가 있는 임시 캐리어에 접촉하여 고정합니다. 엑시머 레이저가 투명 기판을 통해 초점을 맞춰 LED를 분리합니다. 3) 리프트: 엑시머 레이저가 임시 캐리어를 통해 초점을 맞추어 개별 LED를 분리하고 최종 기판의 납땜 패드 쪽으로 추진합니다. 4) LAB: 다이오드 레이저는 수많은 LED와 납땜 범프를 한 번에 가열하여 빠르게 녹이고 최종 접합을 형성합니다.
대부분의 반도체 소자와 마찬가지로 LED는 원래 웨이퍼에서 에피택셜 방식으로 성장합니다. 일반적으로 이는 사파이어 기판입니다. microLED 디스플레이의 각 픽셀을 만들려면 빨간색, 녹색, 파란색 등 각 기본 색상에서 방출되는 별도의 LED가 필요합니다. 그러나 각 웨이퍼에는 단일 색상의 장치만 포함되어 있습니다. 따라서 LED를 개별 다이로 분리한 다음 필요한 패턴으로 함께 배열하여 최종 디스플레이를 만들어야 합니다.
엑시머 레이저 레이저는 이미 이 프로세스의 처음 두 가지 주요 단계에서 비용 효율적인 도구임이 입증되었습니다. 구체적으로 레이저 리프트 오프(LLO)를 사용하여 먼저 사파이어 웨이퍼에서 개별 LED 다이를 분리하여 임시 캐리어로 옮깁니다.
다음에 레이저 유도 순방향 전사(LIFT)가 '대량 전송'을 수행하는 데 사용됩니다. 금형을 임시 캐리어에서 최종 디스플레이 기판으로 이동하는 공정입니다. 가장 중요한 것은 대량 전달시 LED가 원하는 픽셀 패턴으로 배열된다는 것입니다.
MicroLED 조립 문제
LED를 기판의 제자리에 배치한 후에는 접착하고 전기적으로 연결해야 합니다. 그렇지 않으면 디스플레이가 켜지지 않고 이동 시 모든 LED가 떨어지게 됩니다!
이 프로세스를 용이하게 하기 위해 먼저 기판의 모든 전기 연결 지점에 납땜 '범프'(작은 납땜 공)를 배치합니다. 그런 다음 LIFT를 사용하여 다이를 배치한 후 땜납이 녹을 때까지 가열합니다. 이 상태에서 양쪽 기판과 다이의 전기 접점 주위를 흐르게 됩니다. 이후 냉각되고 재응고되어 둘 사이에 전기적, 기계적 연결이 형성됩니다. 이는 전자공학 업계 전반의 표준 조립 기술입니다.
솔더를 녹이는 가장 일반적인 방법은 '매스 리플로우'(MR)입니다. 기본적으로 땜납 볼과 다이가 포함된 전체 기판 어셈블리를 오븐에 넣는 작업이 포함됩니다. 온도는 땜납을 녹인 다음 다시 식힐 때까지 순환됩니다.
그러나 매스 리플로우를 사용하면 MicroLED 제조업체가 더 높은 위치 정확도로 더 가깝게 배치해야 하는 더 작은 LED로 전환하는 데 도움이 되지 않습니다. 문제는 가열주기가 몇 분 정도 걸린다는 것입니다. 이로 인해 모든 구성 요소에 상당한 열 부하가 발생하고 구성 요소가 휘어지고 열-기계적 변형이 발생하며 기판의 다이 위치가 물리적으로 이동할 수 있습니다. 대량 리플로우 오븐의 긴 처리 시간은 전기 연결 불량의 위험도 증가시킵니다. 프로세스 자체도 에너지 집약적입니다.
열 압축 접합(TCB)은 MR로 인한 뒤틀림 위험을 줄이는 대안입니다. TCB는 열이 가해지는 동안 힘을 더해 상호 연결부의 높이와 형태를 더 잘 제어합니다. 그러나 특정 다이 및 패키지 본체 크기에 맞게 맞춤화되고 기본적으로 한 번에 하나의 다이만 접착하는 복잡한 노즐이 필요합니다. 이로 인해 단일 디스플레이를 만들기 위해 말 그대로 수백만 개의 LED 다이를 접착해야 하는 마이크로LED 애플리케이션에는 적합하지 않습니다.
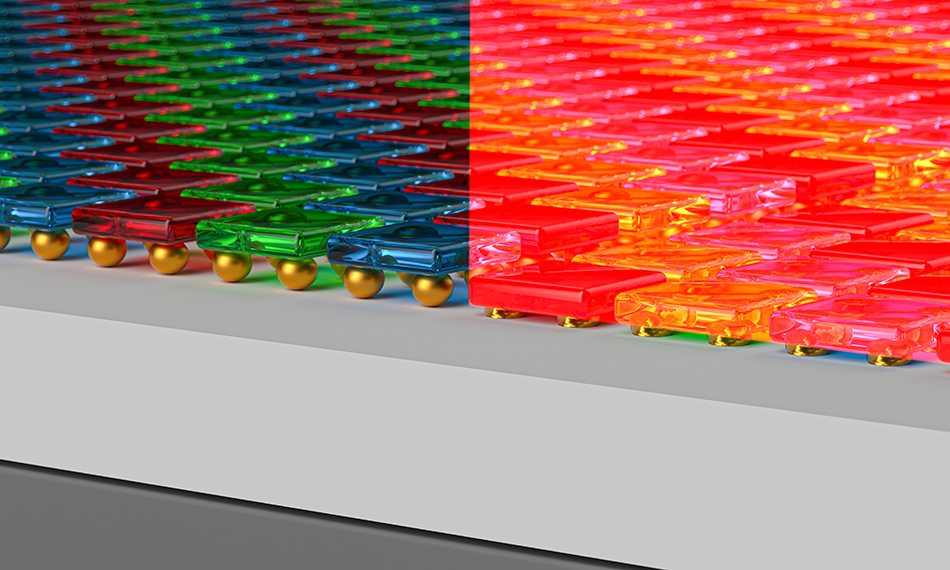
레이저 보조 접합
LAB(레이저 보조 접합)는 이러한 모든 문제를 해결합니다. LAB에서는 고출력 적외선 다이오드 레이저 빔의 출력이 직사각형 모양으로 만들어집니다. 강도 분포는 빔의 전체 영역에 걸쳐 매우 균일하도록 균질화됩니다. 직사각형 빔의 치수는 용도에 따라 다릅니다. 그러나 기판에 있는 수천 또는 수백만 개의 LED를 동시에 조명할 수 있을 만큼 충분히 크게 만드는 것은 가능합니다.
LAB 동안 레이저는 1초 미만의 매우 짧은 시간 동안 켜집니다. 그러나 이것은 솔더를 녹일 만큼 충분한 열을 어셈블리에 전달하기에 충분한 시간입니다. 그러나 다이의 뒤틀림이나 위치 이동을 초래할 수 있는 상당한 벌크 가열을 유발하기에는 너무 짧습니다. 레이저를 사용하면 필요에 따라 냉각 단계를 포함하여 가열 주기를 정밀하게 제어할 수 있습니다. 결과적으로 납땜 공정은 심각한 부정적인 결과 없이 신속하게 수행됩니다. LAB의 짧은 사이클 시간은 MR이나 TCB보다 훨씬 더 에너지 효율적입니다.
향상된 LAB을 위한 더 나은 레이저
레이저 측면에서 LAB의 중요한 요구 사항은 빔 강도가 전체 영역에 걸쳐 균일해야 한다는 것입니다. 이는 솔더를 일관되고 균일하게 가열하여 일관된 결과를 얻기 위해 필요합니다. 목표는 특정 수의 microLED가 포함된 원하는 영역만 선택적으로 가열하고 주변 영역을 전혀 가열하지 않는 것입니다. 따라서 가장자리 근처에서 강도가 많이 떨어지지 않는 직사각형 빔 패턴을 생성하는 것이 특히 중요합니다. 그렇지 않으면 이 영역의 LED가 전혀 접착되지 않을 수 있습니다. 그러나 빔 강도는 조명되는 영역 외부에서 매우 빠르게 감소해야 합니다.
파이버 전달 다이오드 레이저인 Coherent HighLight DL 시리즈는 당사의 PH50 DL Zoom Optic과 페어링할 수 있으며, 이러한 종류의 매우 균일한 직사각형 빔을 정확하게 생성합니다. 일반적으로 4kW HighLight DL 레이저(1~4kW 사이)가 microLED의 LAB에 사용됩니다.
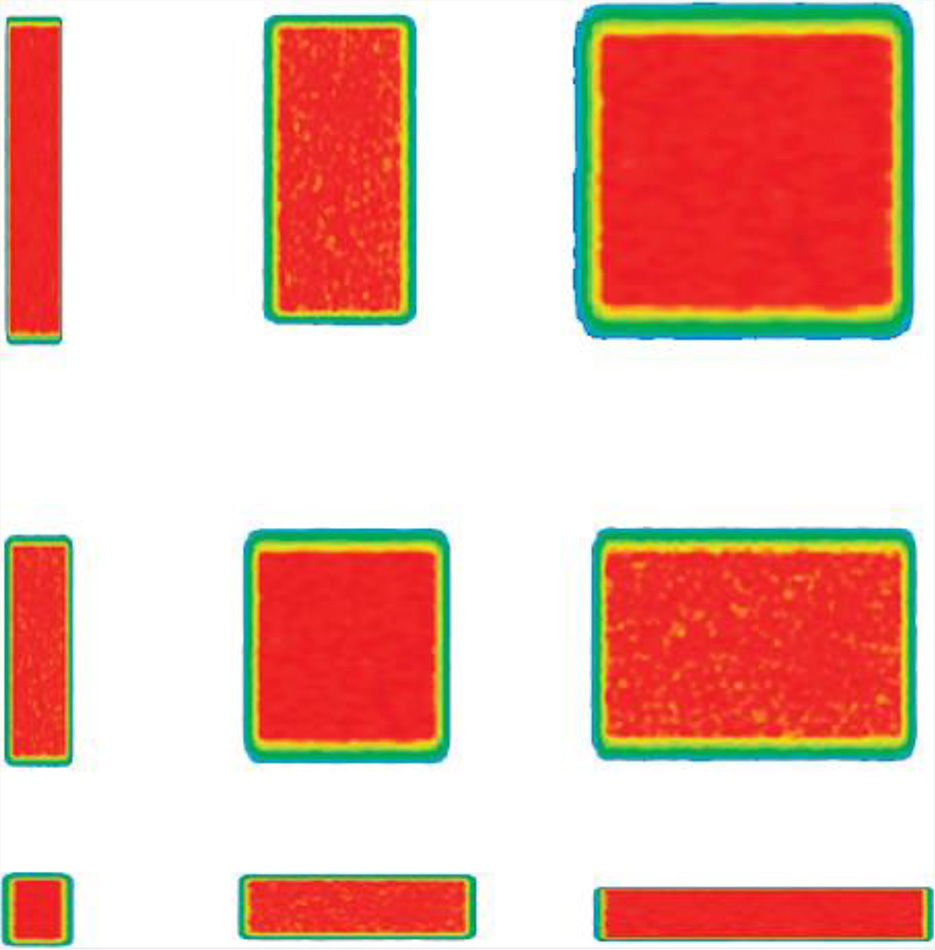
Coherent PH50 DL Zoom Optic은 HighLight DD 시리즈 다이오드 레이저의 광섬유 전달 다중 모드 출력을 매우 균일한 직사각형 빔으로 변환합니다. 이 직사각형의 길이와 너비는 동적으로 독립적으로 조정될 수 있습니다. 여기에 표시된 스팟 크기는 12x12mm에서 110x110mm까지 다양하지만 다른 줌 구성도 사용할 수 있습니다.
이 조합은 당사 고유의 광학 설계를 사용하여 다른 경쟁 제품보다 더 나은 강도 균일성을 제공합니다. 특히, 빔 균질화는 들어오는 레이저 빔을 수많은 '빔렛'으로 분리하기 위해 마이크로 렌즈 배열을 사용하여 수행됩니다. 그런 다음 이들은 매우 균일한 강도 분포를 얻기 위해 확장되고 중첩됩니다.
Coherent PH50 DL Zoom Optic의 또 다른 큰 장점은 공정 중에도 '즉시' 조정이 가능하다는 것입니다. 즉, 직사각형 빔의 길이와 너비를 필요에 따라 광범위하게 독립적으로 조정할 수 있습니다. 이 확대/축소 기능은 제조업체가 프로세스를 개발하고 검증할 때 유용합니다. 이를 통해 다양한 구성을 시도하여 무엇이 가장 효과적이고 가장 효율적인지 확인할 수 있습니다. 물론 Coherent는 동일한 접근 방식을 활용하여 특정 고객 요구 사항을 충족하는 고정(줌 아님) 광학 장치를 생산할 수 있습니다. 이러한 라인 빔의 범위는 수 밀리미터에서 최대 1000mm까지입니다.
LLO와 LIFT는 이미 마이크로LED 생산의 두 가지 핵심 구현 기술로 확립되었습니다. 이제 Coherent 레이저(LAB)를 기반으로 하는 또 다른 공정이 고해상도 MicroLED 디스플레이의 대량 제조를 촉진할 것으로 보입니다.