The Promise – and Challenge – of Hydrogen Fuel Cells
Coherent FL-ARM lasers enable cost-effective welding of bipolar plates, a key component of PEM fuel cells.
September 16, 2022 by Coherent
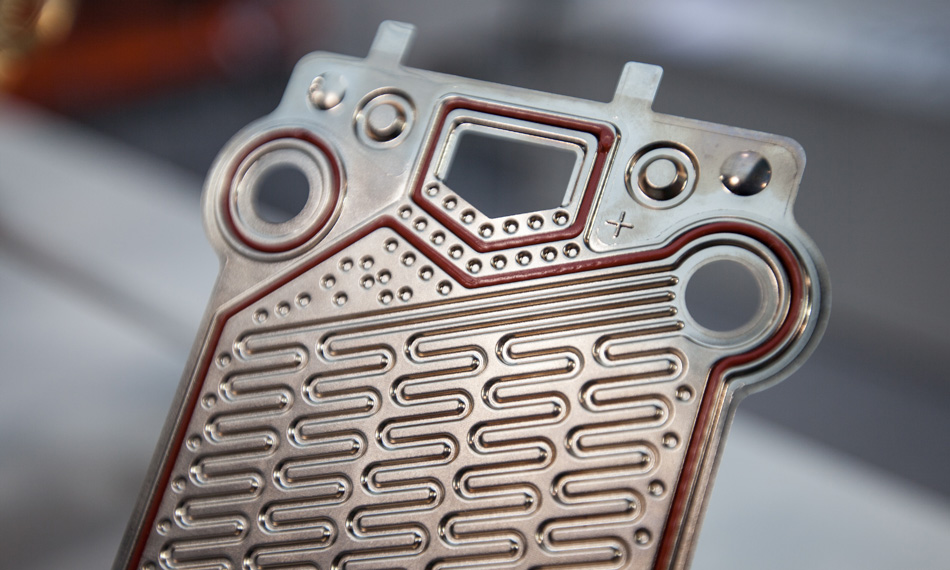
Imagine a highly fuel-efficient car engine that only produces pure water as an exhaust. That’s a hydrogen fuel cell. And it already exists. However, we’re not ready yet to use hydrogen fuel cells to power automobiles on a large scale. That will require developing quite a bit of technology and infrastructure to make them practical and cost-competitive with other technologies. Coherent is already developing fiber laser processes to contribute to that effort.
Celling the technology
Technically, the hydrogen fuel cell is referred to as the proton-exchange membrane fuel cell (PEMFC), or the polymer electrolyte membrane fuel cell. It contains positive and negative electrodes separated by an electrolyte (a fluid that conducts electricity). Hydrogen fuel comes in at the negative electrode, and air (containing oxygen) comes in at positive electrode.
A single fuel cell (called a membrane electrode assembly or MEA) produces less than one volt. This is way too little for most purposes. To reach useful power levels, hundreds of MEAs are electrically connected together within a single fuel cell. The MEAs are physically stacked together inside the cell housing.
But first, each MEA is sealed between two “bipolar plates.” This is a stamped foil part, usually somewhere between 50 µm to 100 µm thick. It’s usually made from stainless steel or titanium. The bipolar plates allow the individual MEAs to be electrically connected, give the assembly some mechanical strength and rigidity, and also contain a set of channels that allows gases and cooling liquids to flow over it.
The bipolar plates are sealed together by welding. This needs to be a very high-quality weld – it has to pass a hydrogen leakage test. And, the complex shape of the bipolar plate, which includes several cutouts, makes the weld paths long, and with numerous curves.
Traditional fiber lasers can’t seal the deal
Because of the very large number of bipolar plates used in each fuel cell, the sealing process needs to be fast. Otherwise, it can create a production bottleneck. It is currently estimated that economically viable and practical PEMFC production for automotive applications requires a welding speed of over 1 m/sec for the MEA sealing process.
Fiber lasers delivered through a scanning system can weld at those speeds, and more. Plus, they can produce the complex shaped welds required. But the weld quality they offer at those feed rates isn’t good.
In particular, traditional fiber lasers tend to produce “humping” when welding bipolar plates at high speeds. These are small bumps in the weld seam produced when turbulent areas in the melt pool resolidify. This turbulence is caused directly by the very rapid beam movement.
Humps are a problem because they stick up. This prevents the MEAs from being stacked close enough together during assembly.
HighLight FL-ARM gets over the hump
Testing at Coherent Labs has demonstrated that a properly configured Adjustable Ring Mode (ARM) fiber laser solves the problem of humping. Specifically, a Coherent HighLight FL4000CSM-ARM (4 kW laser with a single mode center beam) can weld stainless steel bipolar plates at speeds of at least 1.2 m/s without any humping. This is 50% faster than previously possible with fiber lasers. For these tests, the laser was delivered through a Coherent HIGHmotion 2D Remote Laser Welding Head.
The ARM fiber laser avoids the problem of humping by eliminating turbulence around the rapidly moving weld melt pool. This is accomplished by taking advantage of the Adjustable Ring Mode architecture.
Specifically, the center beam power is set high enough to produce full penetration keyhole welding at the target speed. But the ring beam only carries enough power to melt the material – so that it can flow – but not enough to create a weld keyhole.
This provides a zone around the center beam where the melted material can slow down and flow in a laminar (non-chaotic) fashion. Furthermore, the symmetric, round ARM laser beam always welds the same way no matter which direction it’s heading in. So, there’s no change in weld characteristics when going through curves or changing direction. This provides an advantage over other multi-beam fiber lasers which don’t have a symmetric spot.
Of course, there are many other challenges in deploying fuel cells. These include other cell manufacturing issues, sourcing hydrogen and platinum (which is used as a catalyst to separate the hydrogen atom into protons and electrons). We would also need to develop a network of hydrogen “gas stations” to make getting fuel convenient for the consumer. But, with the HighLight FL-ARM laser – and the extensive process knowledge Coherent Labs possess about using it effectively for bipolar plate welding – we’ve bypassed one important roadblock in that journey.