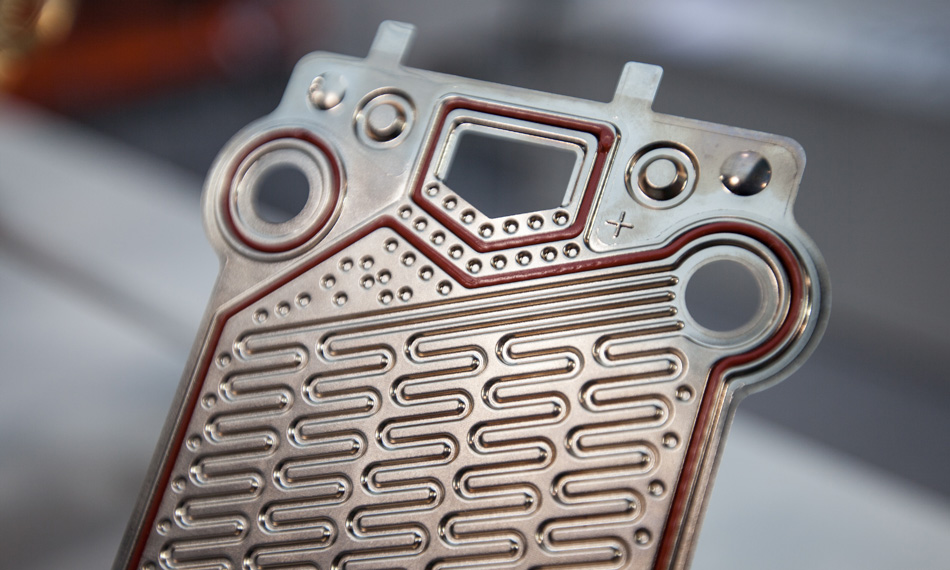
想象一下,如果一款高燃油效率汽车发动机只产生纯水排放物,将会是怎样。 氢燃料电池即可助力实现这种想象。 这种电池已经问世。 不过,我们还没有准备好大规模使用氢燃料电池为汽车提供动力。 要实现这个目标,将需要开发相当多的技术和基础设施,使它们与其他技术相比具有实用性和成本竞争力。 Coherent 已经在开发光纤激光工艺来为实现这个目标做出努力。
卓越电池技术
从技术上讲,氢燃料电池被称为质子交换膜燃料电池 (PEMFC) 或聚合物电解质膜燃料电池。它包含由电解质(一种导电流体)隔开的正极和负极。 氢燃料从负极进入,空气(含氧)从正极进入。
单个燃料电池(称为膜电极组件或 MEA)产生的电压不到 1V。 这对于大多数用途来说都太少了。 为了达到有用的功率水平,数百个 MEA 在单个燃料电池中用电连接在一起。MEA 在电池外壳内以物理方式堆叠在一起。
但首先,每个 MEA 都密封在两个“双极板”之间。这是一个冲压箔部件,厚度一般在 50 µm 到 100 µm 之间, 通常由不锈钢或钛制成。 双极板允许单独的 MEA 进行电气连接,赋予组件一定的机械强度和刚度,并且还包含一组允许气体和冷却液流过的通道。
双极板通过焊接密封在一起。 这需要非常高质量的焊接,必须要通过氢泄漏测试。 而且,双极板的形状较为复杂,具有多个切口,这使得焊接路径较长,并且有许多曲线。
传统光纤激光器无法达到理想的焊接密封效果
由于每个燃料电池中使用大量双极板,因此密封过程需要十分快速。 否则,可能会造成生产瓶颈。 目前估计,用于汽车应用的经济实用的 PEMFC 生产需要 MEA 密封过程的焊接速度超过 1 米/秒。
通过扫描振镜传送能量的光纤激光器能够以这种速度进行焊接,甚至更快。 此外,这些激光器还可以形成所需的复杂形状的焊缝。 但是,它们在这些进给速度下提供的焊接质量并不好。
尤其是传统的光纤激光器在高速焊接双极板时往往会产生“驼峰”。 这些“驼峰”是当熔池中的湍流区域重新凝固时在焊缝中形成的小凸起。 这种湍流是由非常快速的光束运动直接引起的。
“驼峰”之所以会成为问题,是因为它们会造成突起。 这会妨碍 MEA 在组装过程中实现紧密堆叠。
HighLight FL-ARM 解决了“驼峰”问题
Coherent 实验室的测试表明,正确配置的可调环模 (ARM) 光纤激光器可以解决“驼峰”问题。 具体来说,Coherent HighLight FL4000CSM-ARM(具有单模中心光束的 4 kW 激光器)能够以至少 1.2 米/秒的速度焊接不锈钢双极板,而不会产生任何“驼峰”。 这比以前使用光纤激光器的速度快 50%。 在这些测试中,激光是通过 Coherent HIGHmotion 2D 远程激光焊接头提供的。
ARM 光纤激光器通过消除快速移动的焊接熔池周围的湍流来避免“驼峰”问题。 这是通过利用可调环模架构来实现的。
具体来说,将中心光束功率设置得足够高,以在目标速度下产生全熔透小孔焊接。 但是环形光束只承载足够的能量来熔化材料以使其能够流动,而不足以形成焊接锁孔。
这在中心光束周围提供了一个区域,熔化的材料可以在该区域中减速并以层流(非混沌)方式流动。 此外,对称的圆形 ARM 激光束无论朝向哪个方向,总是以相同的方式焊接。因此,在通过曲线或改变方向时,焊接特性没有变化。 与其他不具有对称光斑的多光束光纤激光器相比,这种激光器具有更多优势。
当然,部署燃料电池还有许多其他挑战。 这些挑战包括其他电池制造问题,以及氢和铂(铂用作催化剂,将氢原子分离成质子和电子)的来源。 我们还需要打造一个氢“加气站”网络,以方便消费者获取燃料。 但是,凭借 HighLight FL-ARM 激光器,以及 Coherent 实验室拥有的关于将其有效用于双极板焊接的广泛工艺知识,我们已经避开了这一过程中的一个重要障碍。