WHITE PAPER
Polymer Welding: A Recipe for Success
Laser welding offers several advantages over other methods for joining polymers. But implementing it right requires an understanding of the technology, and often benefits from discussions with a knowledgeable equipment supplier early in the product development cycle.
Why use laser welding?
Laser welding offers numerous advantages over other polymer joining technologies. The most important of these are summarized in the following table:
Precision |
Highly localized application of laser energy produces little or no part distortion, delivers tight dimensional tolerances, and can be used with complex shaped parts. |
Repeatability |
The laser process is inherently highly consistent and can be closely regulated with process monitoring equipment |
Weld quality |
Weld seams are narrow and cosmetically excellent (no flash), and post processing is rarely required. |
Weld strength |
Laser welding delivers a strong weld, which is free of gaps, and can provide hermetic sealing. |
Low contamination |
Laser welding doesn’t use filler materials and produces virtually no debris. |
Speed |
The process is fast and well and lends itself to automation. |
But, actually getting all these benefits in practice requires that the polymer welding process is carefully and correctly implemented. Plus, cost is always a factor. Therefore, the laser polymer welding process must be configured in a way that is cost-effective without compromising in other areas. There are really three key things to consider before starting production – possibly even as early as the product design cycle.
Material selection
A primary consideration is material selection. This is particularly true for “through transmission laser welding” (TTLW), which is one of the most commonly used techniques. TTLW involves joining one part that is transparent at the laser wavelength to another plastic which is opaque. The two parts are placed in contact with the clear part on top. The laser is focused in through the clear part, and down towards the opaque one. It heats and melts the opaque part causing them to be joined.
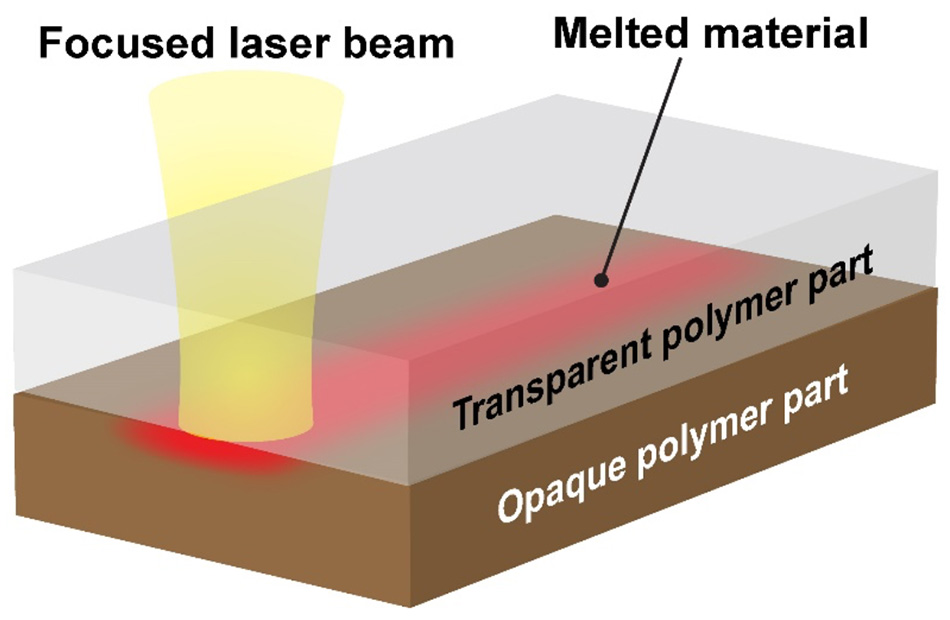
Figure 1. In TTLW, laser light passes through the transparent top part and melts the bottom one to form a bond.
For TTLW to work right, there must be some temperature range over which both polymers (clear and opaque) will remain molten (but not decompose). The greater this overlap, the wider the process window. The wider process window makes production easier and more robust. The chart summarizes which common polymer combinations are compatible with laser welding.
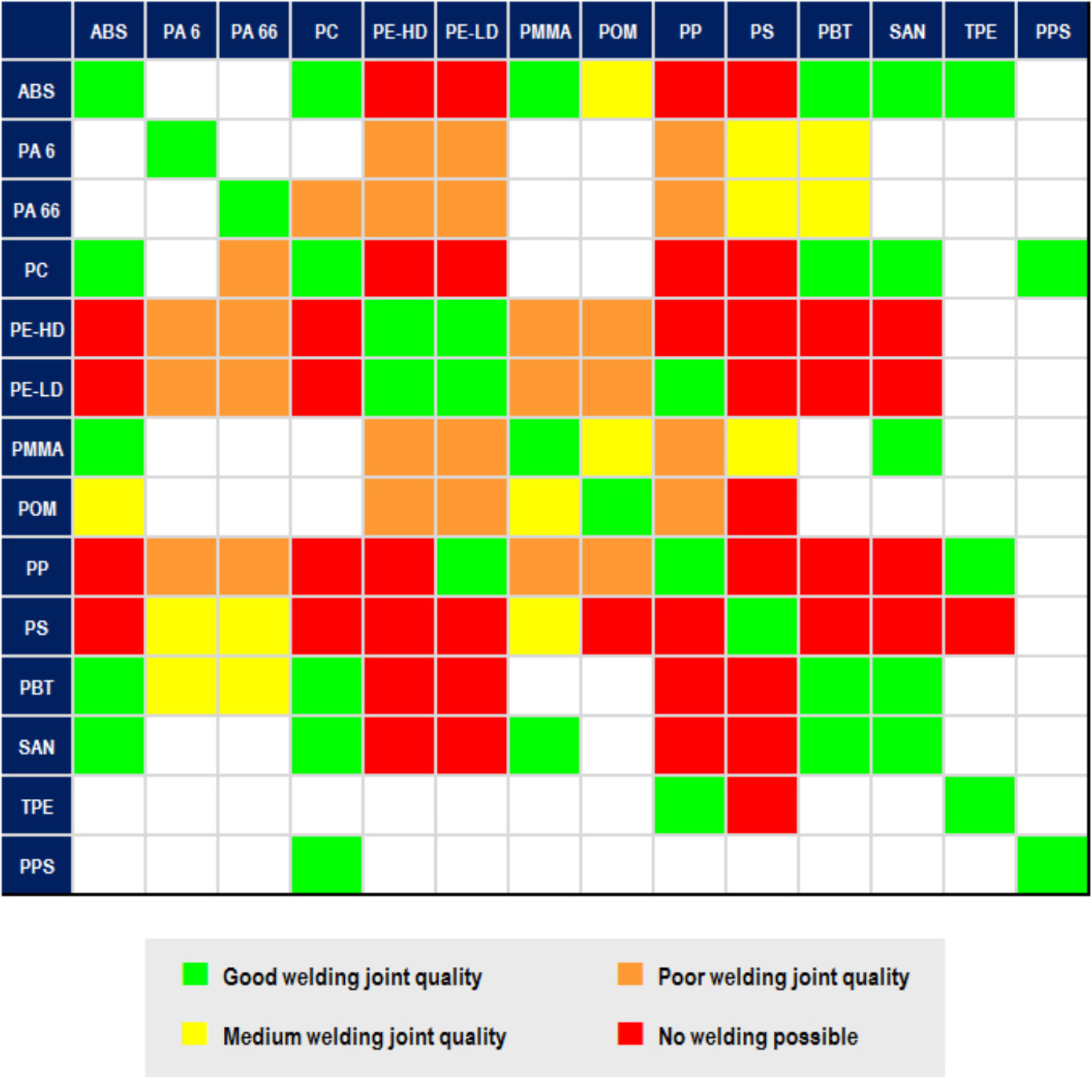
Figure 2. Material compatibility chart for TTLW.
Design for manufacturing
The next consideration is “design for manufacturing.” For example, one widely employed TTLW technique is quasi-simultaneous welding using the “collapse rib” method. In this process, the bottom part has a thin protruding rib which mates into a corresponding groove in the top part. The groove is a bit wider than the rib.
Successfully implementing the collapse rib method requires a part design with sufficient space – in exactly the right location – for the clamps to engage and deliver the necessary downward force during welding. But the clamp location must also permit unobstructed access to the entire weld path for the laser beam.
The dimensions and shapes of the rib and groove must also provide enough molten material for the welding process and accommodate the melt flash that is produced. Plus, it’s necessary to design the parts to allow for a sufficient collapse height. For high precision applications, alignment features, such as locating pins, may have to be incorporated into the part design. The goal is to achieve a strong weld with good cosmetics, while eliminating the need for post-processing to trim or remove flash.
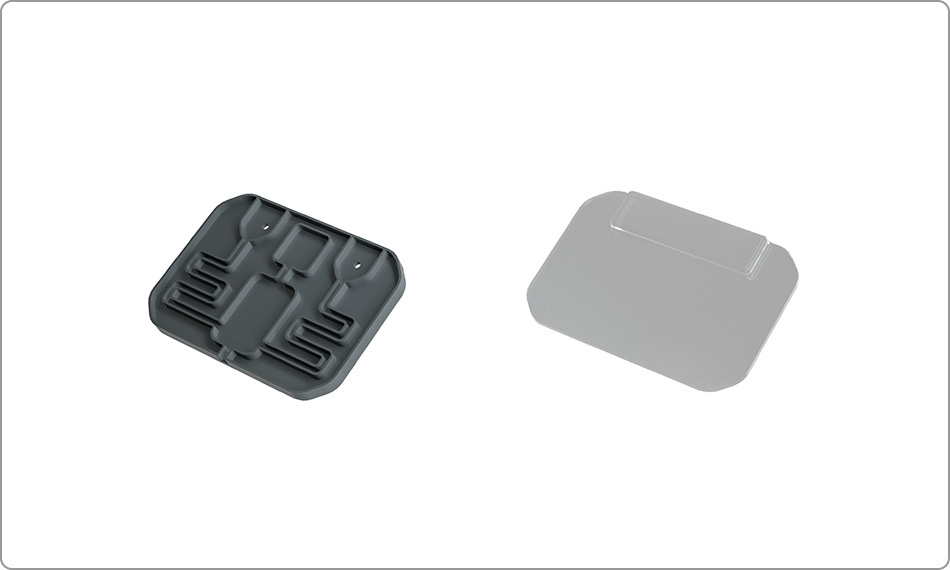
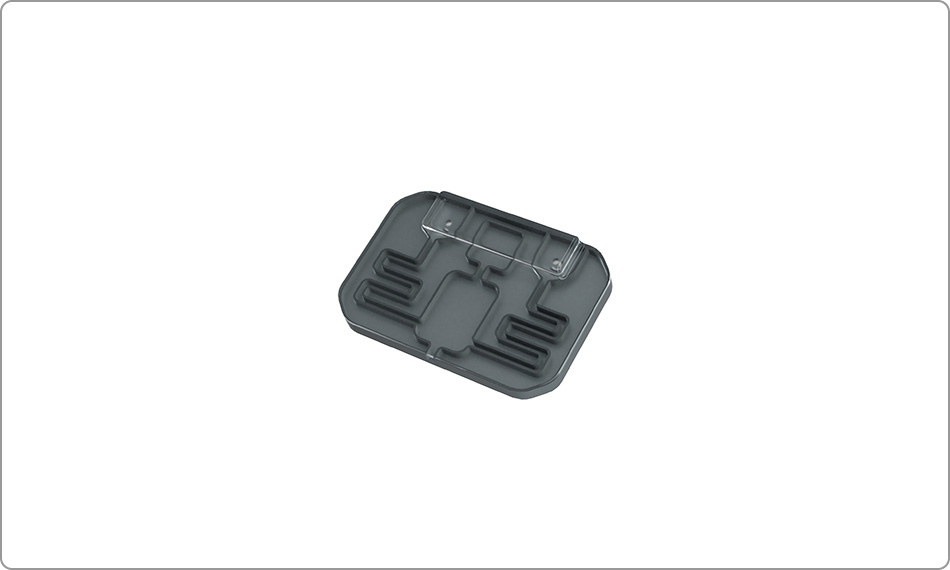
Figure 3. An example of two polymer parts before and after welding.
Selecting the right partner
A final consideration is choosing an appropriate system supplier. This is particularly important for polymer welding systems for two reasons. The first is to provide access to specialized laser expertise, and the second is to aid in process development.
A high degree of laser system knowledge is required to ensure that the right laser source and beam delivery system is chosen for the materials and part configuration being used. A laser system must be designed to deliver energy in a way that welds the part fast enough to achieve the desired throughput. But simply throwing more power at the problem increases system cost. The optimum balance must be achieved.
An experienced supplier can also address various practical issues in terms of clamping tooling, part handling, and the mechanical and software interface of the polymer welding system with other production equipment.
Process development assistance is valuable because there is often a fairly large “parameter space” which must be explored for laser welding. It’s very helpful to have prior experience to quickly determine the optimum laser operating conditions and identify what process variables must be monitored or controlled to achieve the desired yields.
It’s also very helpful if the welding system supplier has access to a variety of different lasers to actually test the process on real part samples. Ideally, the vendor’s application lab can even develop and refine the “process recipe.” Obviously, this kind of effort has a higher upfront cost. But it saves money because it gets the system into production faster and then produces better and more reliable results.
In conclusion, laser welding enables precision joining of polymer parts, and is a cost-effective method over a wide range of production volumes. It can help deliver on the promise of polymers to lower cost, save weight, and provide advanced functionality in a wide range of products. Unless an organization already possesses expertise in polymer welding, effective implementation is aided by working with a knowledgeable equipment supplier from the very outset.