What is Laser Scanning?
Laser scanning is just moving a laser beam across a surface – whether it’s to read a product barcode, project a laser light show, or weld an autobody. While conceptually simple, the actual technologies used for laser scanning can be quite sophisticated.
We all encounter laser scanning frequently. It’s the technique used to pass a laser beam across a product barcode when making a purchase at a store. But laser scanning is used in many more ways than just that. In fact, the diversity of scanning applications is so great that it is useful to break them down into three main categories:
Purpose |
Process |
Common Applications |
Data acquisition and imaging |
The laser is used to determine something about the physical characteristics of an object — size, shape, spatial position, spatial orientation, color, color variations, surface texture, chemical composition, and more. To accomplish this, the laser beam is scanned over a surface or within a volume. The projected laser pattern is then imaged – or the light returned (through reflection, scatter, or fluorescence) is detected – and analyzed to derive the desired information. |
Reading barcodes, QR codes, Datamatrix codes, and the like. Measuring the physical dimensions of products going by on a conveyor belt to identify units that are out of specification. Scanning a laser beam over a landscape to perform LIDAR in a moving vehicle. Imaging food items (like shrimp or nuts) going by on a conveyor belt to grade them by size or to identify nonconforming product. Scanning an actual object, like teeth or a building interior, to create an accurate computer model Confocal microscopy where the laser beam is projected through a microscope onto a sample and scanned across it to build up an image Optical coherence tomography (OCT) for medical imaging Semiconductor wafer inspection |
Data writing and display |
The laser light is used to display information, or to produce patterns or images. To achieve this, the laser beam travels over a surface or within a volume while being modulated in intensity. |
Scanning across a rotating photoconductive drum in a laser printer Laser light shows and signage Laser alignment gauges for construction and surveying |
Materials processing |
A laser is used to physically transform (cut, weld, ablate, melt, etc.) or affect (anneal, color change, heat, etc.) a material in a spatially varying manner. This is done by moving the laser beam over a surface or within a volume while it is modulated in intensity. |
Marking Welding Cutting Engraving Heat treating Cladding |
The uses just listed – which are only a small sampling of laser scanning applications – have widely varying technical requirements. This includes parameters like scanning speed, the size of the area or volume that must be covered, the laser power involved, the cost, size, reliability, and lifetime of the scanner, and much more. Different scanning technologies have been developed to meet the diverse needs of these applications.
Most applications employ one of three scanning technologies – galvanometer mirrors, polygon mirrors, or acousto-optic deflectors. It’s worth looking at how each of these works, and their operational and practical characteristics.
Galvanometer scanners
A galvanometer scanner consists of a mirror mounted on a shaft which can rotate freely. The shaft also has as a magnet mounted on it. The shaft is suspended within a coil; applying electricity to the coil causes the shaft (and mirror) to rotate.
Depending on the nature of the task, galvanometer scanners are often used in pairs. Specifically, in this case they are mounted with their scan directions at right angles to each other. This enables the laser beam to reach any point in a plane. For many applications, specialized scan optics, like an F-theta lens, are used to focus the beam on the final surface.
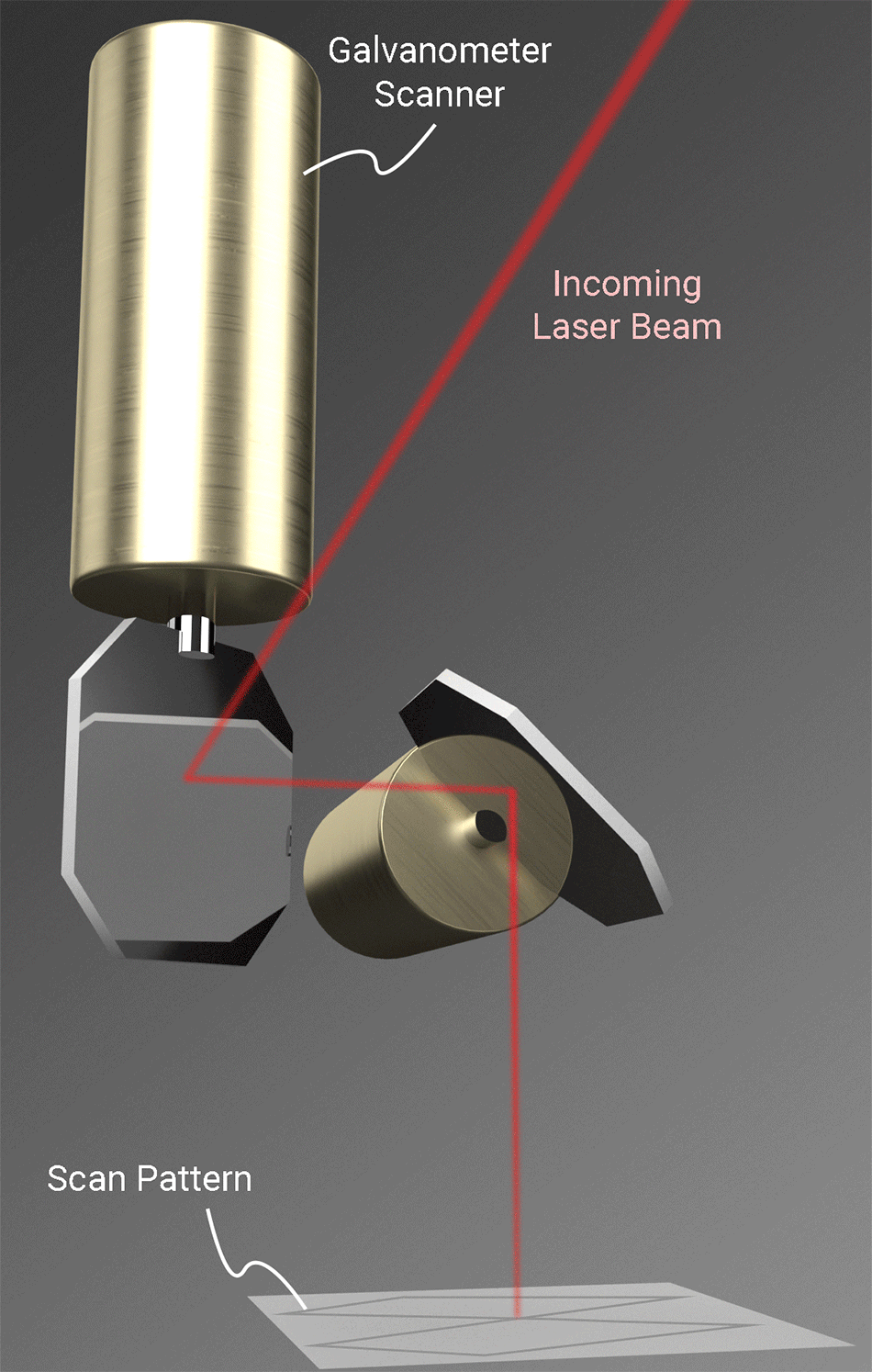
Figure 1. Galvanometer scanners are often used in pairs to produce a 2D scan pattern.
Galvanometer scanners offer operational flexibility, since their movement can be computer controlled on-the-fly. They can be used in pairs to produce 2D vector patterns over relatively large scan angles (typically up to ±20°). They can he used with big mirrors to accommodate large beam sizes. Together, these characteristics make them ideal or applications like light shows, material marking and welding, biomedical and ophthalmic imaging, confocal microscopy, and laser-assisted medical treatments.
Polygon scanners
The key element of a polygon scanner is a polygon shaped component – the edges of which have been polished and coated to be mirrors. This polygon mirror is mounted on a motor shaft and spun rapidly. This allows a laser beam to be scanned quickly in one direction.
As with galvanometer scanners, polygon scanning systems often utilize specialized scan optics. It is not uncommon for these optics to be fabricated as a long thin stripe, because the laser beam will only traverse them along a narrow straight path. This dramatically reduces scanning system size and weight.
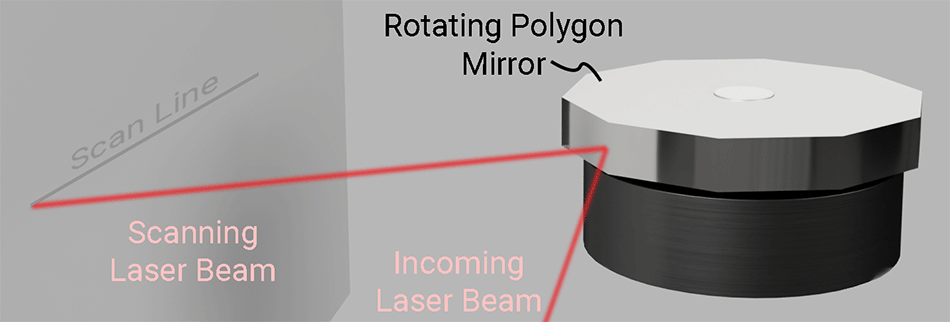
Figure 2. A polygon scanner can rapidly move a laser beam in a single direction.
Polygonal scanners excel in applications requiring unidirectional scans at high speeds. They can operate over very large scan angles (over 50°). When two-dimensional coverage is required, they are typically combined with some form of part motion in the direction perpendicular to the scan to produce a raster pattern. These properties make them ideal for applications like laser printers, LIDAR, and certain high-speed materials processing uses like large area surface treatment and thin film patterning.
Acousto–optic deflectors
The acousto-optic (AO) deflector consists of a block of transparent material with a piezoelectric transducer bonded to its side. When driven at radio frequencies, the piezoelectric transducer produces a sound (pressure/density) wave within the crystal. This creates a variable, periodic, spatial change in the material’s refractive index which acts like a Bragg diffraction grating. This grating deflects an input laser beam by an amount that depends upon its period. So, varying the frequency of the input signal changes the beam deflection angle.
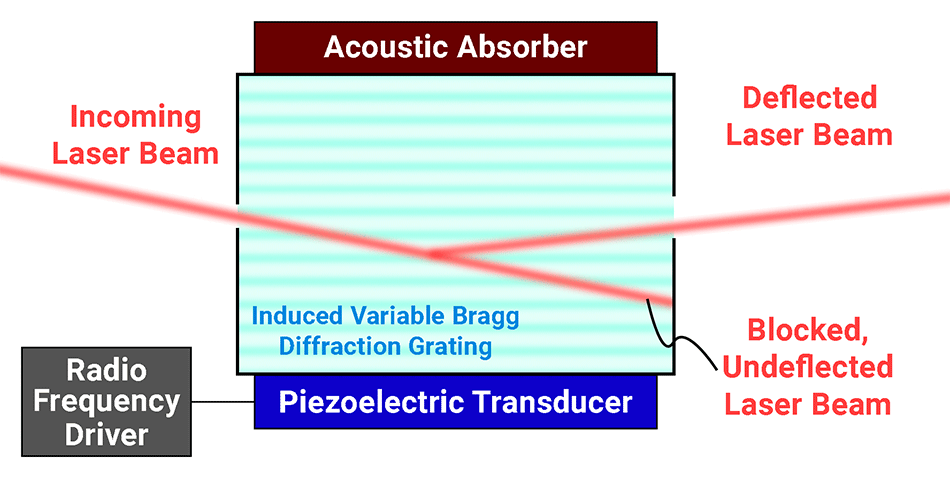
Figure 3. An acousto-optic deflector scans a laser beam using diffraction and has no moving parts.
The absence of any moving mechanical parts (and hence inertia) allows acousto-optic deflectors to achieve much higher scan speeds than the other technologies – well into the MHz range. Plus, they are capable of “random access” scanning – this is the ability to quickly jump from one point in the scan field to another. However, they can only deflect the beam over a very limited angular range – a few degrees at most. And they only offer small aperture (<2.5 mm) sizes. This makes them most useful for specialized uses in laser cooling, laser tweezers, microscopy and medical imaging, and some graphic arts applications.
In addition to these three common types of scanners, there are many other technologies that service specialized uses. All this supports the tremendous diversity of laser scanning applications.