This Time, Less Really Is More for Laser Process Monitoring
SmartQD Fiber – sensors exactly where they should be.
February 20, 2025 by Coherent
In high-power laser material processing, reliable process monitoring is paramount, the adage ’If you’re not measuring, you’re not managing’ could not be more apt. Deviations in laser parameters, parts or optic contamination can lead to costly defects, particularly in quality-critical industries. So, process monitoring is essential for data-driven, intelligent manufacturing, but conventional solutions often involve bulky, expensive, and complex process head-mounted devices for light extraction and analysis. SmartQD from Coherent is a novel approach that integrates process monitoring directly within a standard fiber connector, offering a streamlined, cost-effective, and highly reliable solution.
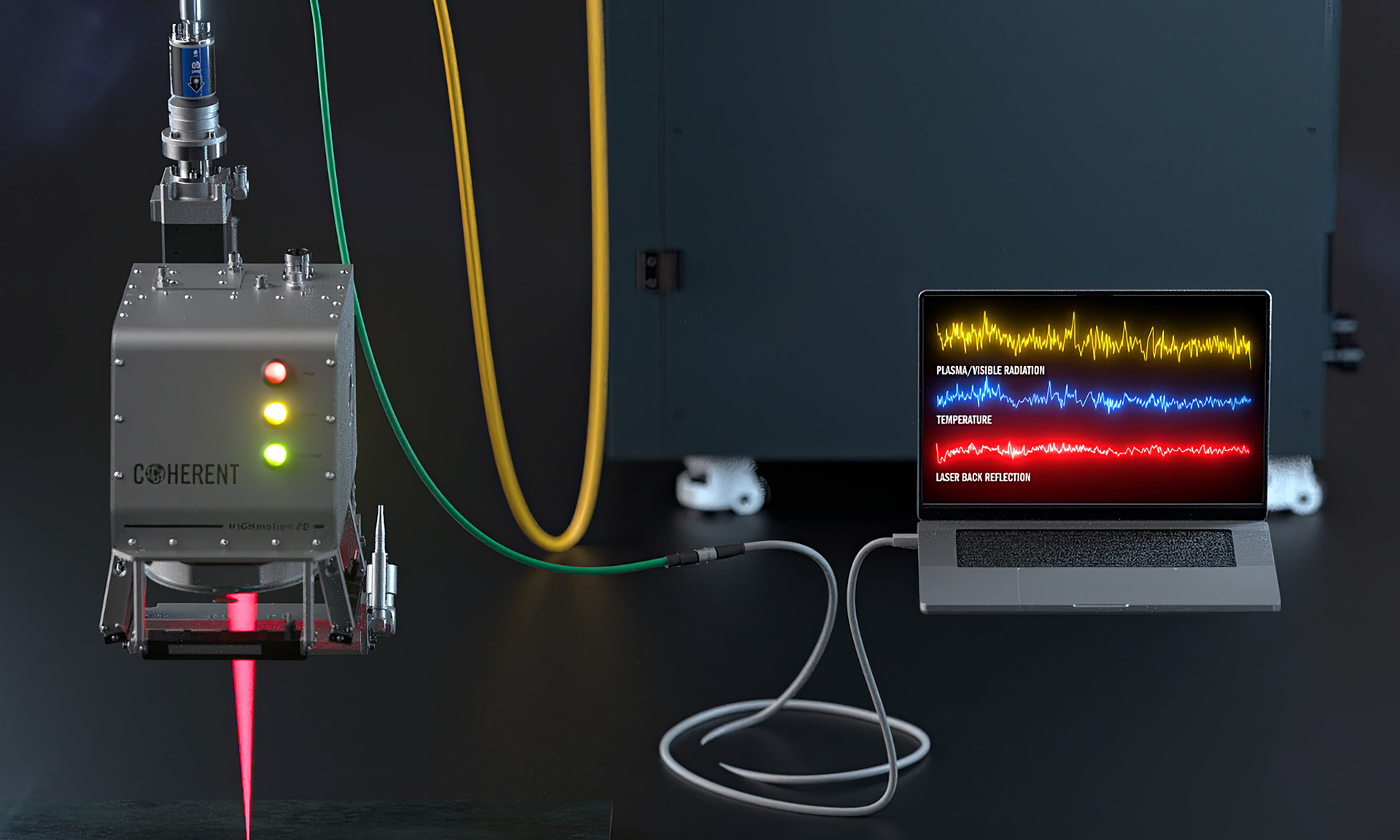
Limitations of Conventional Process Monitoring Setups
Traditional process monitoring systems rely on external optical components mounted on the processing head. These include beam splitters, lenses, and photodiodes, adding significant bulk, cost, and complexity. Furthermore, these systems require careful alignment and calibration, increasing susceptibility to environmental factors and introducing potential points of failure. In today's lean manufacturing environment, such inefficiencies are unacceptable. The need for robust, integrated process monitoring that minimizes waste and maximizes productivity is clear.
SmartQD: The next level of integration for Process Monitoring
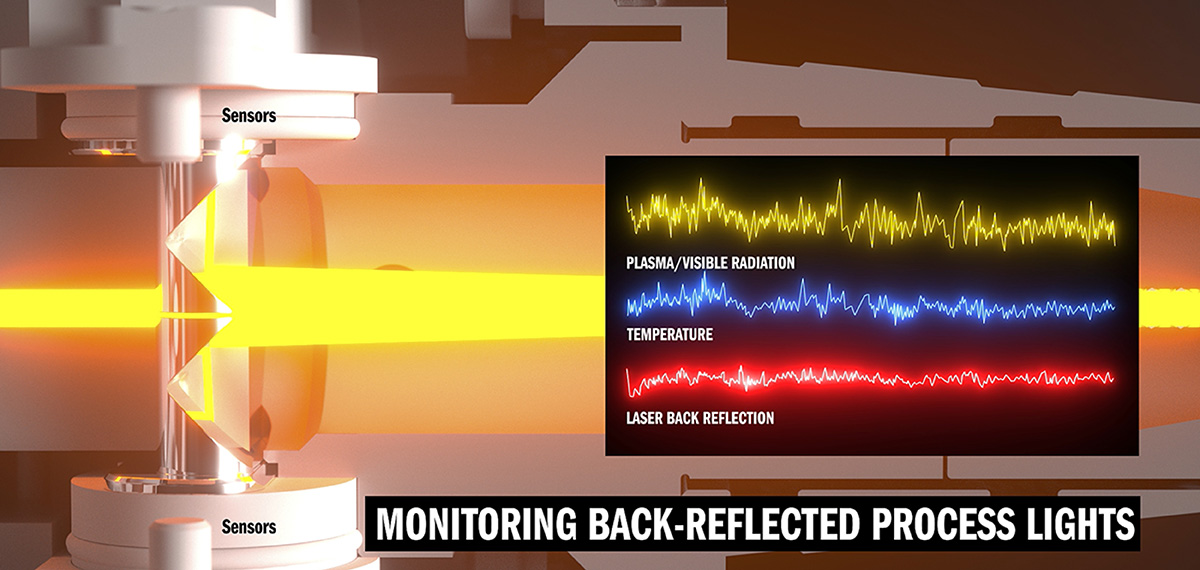
The SmartQD fiber optic cable represents a significant advancement in high-power laser beam delivery and process monitoring. This patented technology integrates sensing capabilities directly into the industry proven QD fiber connector, eliminating the need for external optical components, adapters, and sensor boxes. This innovative design simplifies setup, reduces system footprint, and enhances reliability.
The SmartQD advantage: A dive into the technology
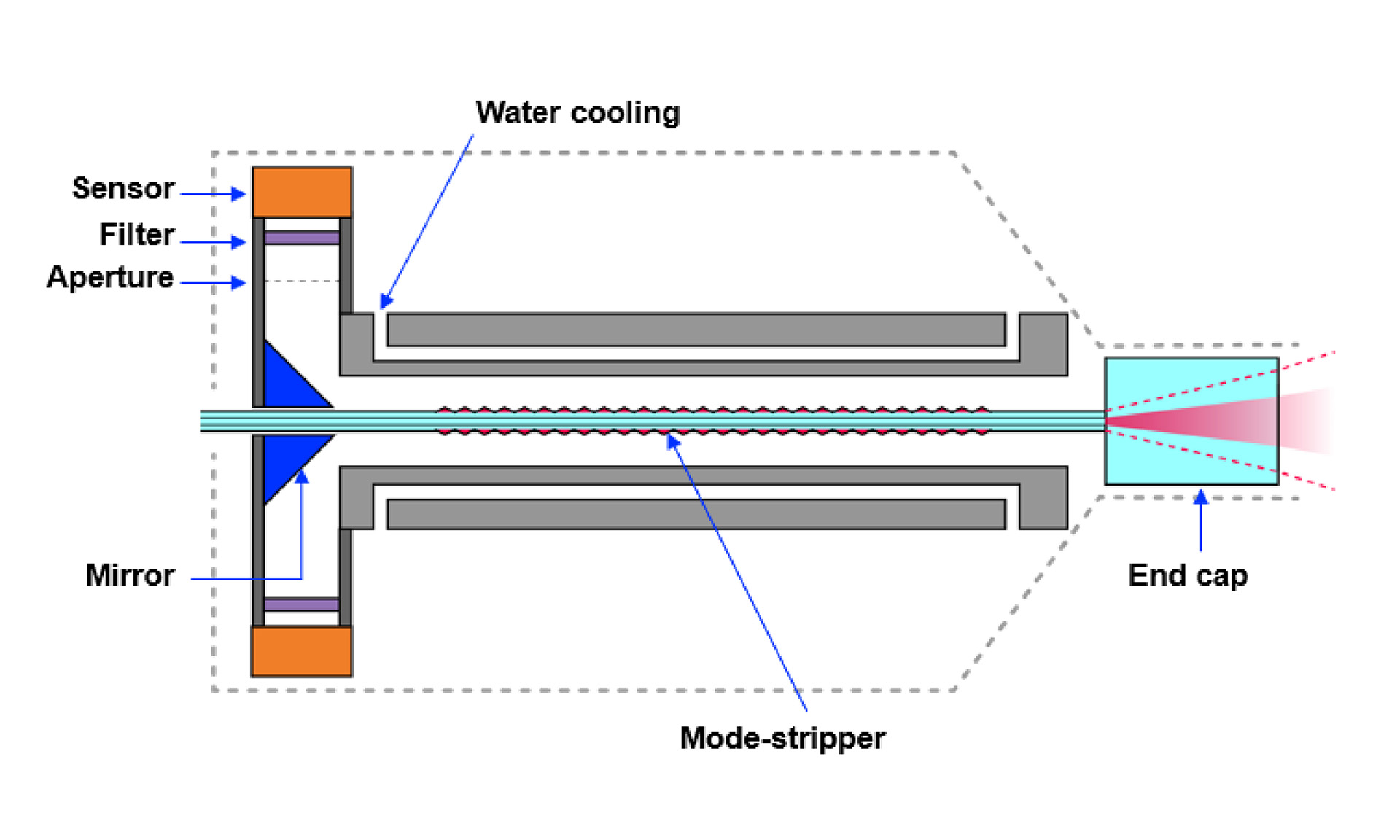
SmartQD leverages the light rejected by the mode stripper, which ensures a well-defined laser beam by eliminating cladding light. This light, originating from the process side, is directed via a mirror within the connector through apertures and optical filters onto photodiode sensors. The design facilitates the measurement of back-reflected laser light, temperature radiation, and visible radiation during the process. Indirect water cooling maintains stable sensor temperatures and prevents water contamination. An AR-coated quartz end cap with a larger surface area reduces power density and simplifies fiber alignment. The robust cable design and precise fiber coupling ensure reliable performance, even in demanding robotic applications. While the output connector is QD, the input connector can be flexibly chosen as QD, QBH, or pigtail.
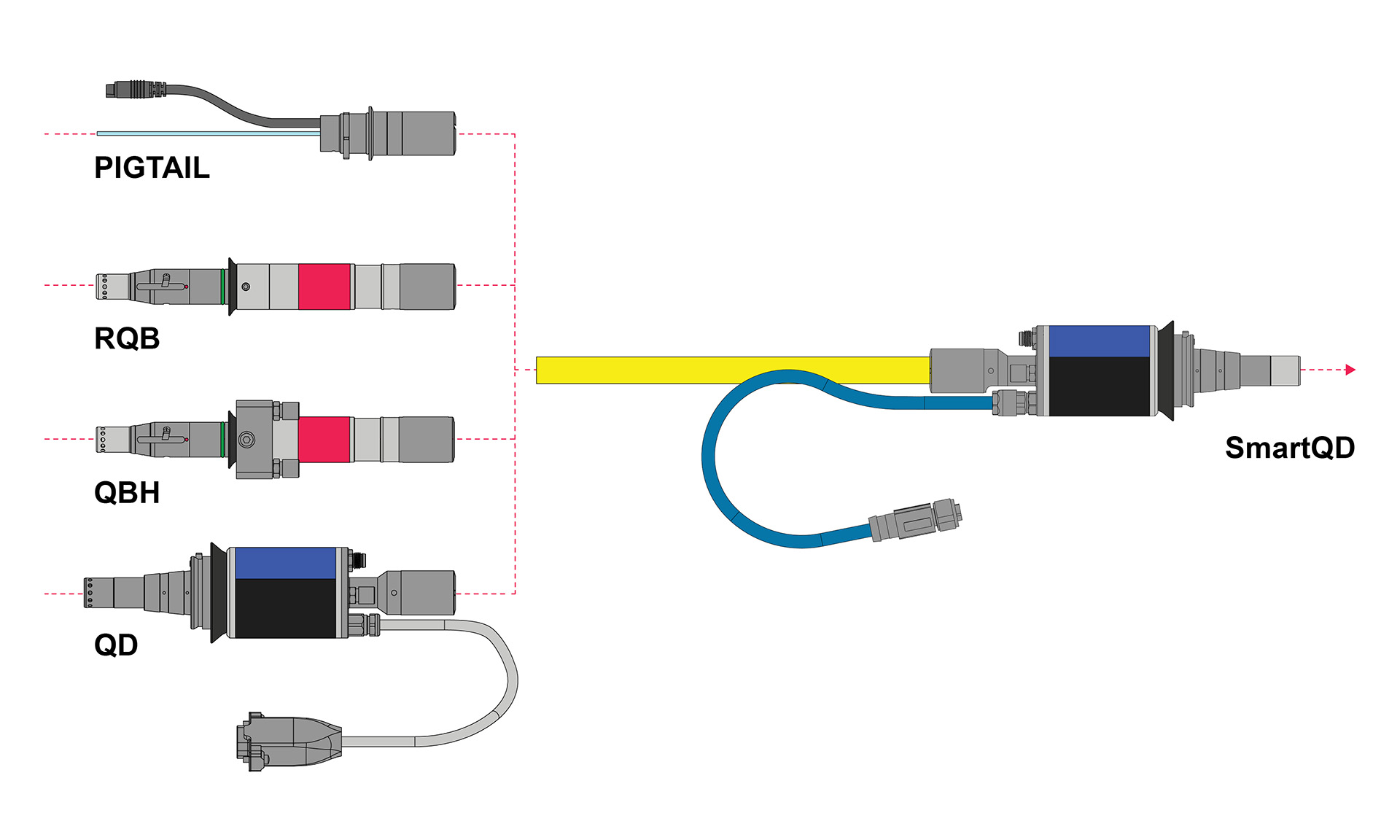
- Integrated Design: Eliminates bulky external optics and simplifies system integration.
- Simplified Setup: No alignment of mirrors or sensor focus adjustment is required.
- Real-time Monitoring: Captures process data for analysis via standard Ethernet protocol.
- Comprehensive Data Acquisition: Measures back-reflected laser light, temperature radiation, and visible radiation.
- Enhanced Reliability: Fewer components and connections improve system robustness.
- Cost-Effectiveness: Reduces component costs, assembly time, and maintenance.
- Plug-and-Play Compatibility: Seamless integration with existing process optics and adherence to automotive industry standards.
- High-Power Capability: Supports laser powers up to 20 kW (CW) within the 1030-1090 nm wavelength range.
Quality over quantity
SmartQD provides low-loss transmission of high laser power for extended periods. Its plug-and-play design minimizes setup time and effort, making it ideal for integration into existing process heads, including scanners. The integrated monitoring capabilities enable real-time process analysis, facilitating the detection of anomalies and deviations that indicate potential quality issues. This data-driven approach empowers manufacturers to optimize processes, improve product quality, and reduce downtime.
The SmartQD fiber optic cable represents a significant advance in high-power laser processing. By integrating process monitoring directly into the fiber connector, SmartQD offers the most compact, independent, cost-effective, and highly reliable solution for real-time process analysis. This innovative technology enables manufacturers to achieve higher levels of quality, efficiency, and productivity in demanding applications across all industries utilizing high power lasers for welding & cutting in production.