PulseEQ: Process The Most Delicate Materials Without Thermal Damage
Discover how Coherent PulseEQ technology prevents thermal damage when processing delicate materials.
July 13, 2021 by Coherent
Many products today, particularly in microelectronics and display manufacturing, incorporate materials which are thin, mechanically delicate, or heat sensitive. Lasers have become widely used for processing (cutting, marking, welding, etc.) these kinds of materials for three main reasons. First, they can produce smaller and more precise features than any other technology. Second, they impart no mechanical force to a workpiece, so they don’t introduce any stress or chance of breakage. Finally, when used right, it’s possible to limit how much the laser heats the part during processing. That’s important, because heat can damage a part or somehow change its physical properties.
A hot topic
As manufacturers continue to push the envelope of what’s possible – producing more complex parts at ever-increasing throughputs – the issue of heat damage becomes even more critical. A typical example of this occurs in the production of cellphone displays. These are often based on flexible OLED modules. To produce these, multiple displays are fabricated on a large panel, and then the individual phone displays are cut out at the final stage.
The shape of these cutouts can be quite complex, with rounded corners, indents for buttons, and holes for cameras and other sensors. And, it is absolutely critical that the cutting process doesn’t heat the part too much, otherwise it might affect display cosmetics (like discoloration) or even reduce functionality.
Because this same problem affects so many applications, laser manufacturers have been developing technology to deal with it for some time. One important breakthrough was the development several years ago of industrial ultra-short pulse (USP) lasers. These deliver a burst of light so brief that material is vaporized off the part before most of the heat has time to be conducted into it.
Trouble with the curve
But, for some of the most demanding and sensitive applications, even USP technology needs a little help to completely avoid heat damage to a part. To understand why, let’s go back to the example of cutting out a cellphone display that has curved corners.
To do that, the laser beam has to trace out the desired cut pattern on the part surface – in other words, the beam has to move relative to the part to cut out the shape you want. That can be done by moving the part on a motorized platform, or by moving the laser beam using a scanner mirror (or a combination of both).
Either way, the mechanical system that’s producing the beam motion has mass. And, that means it can’t be stopped or started instantaneously. In order to change direction, it has to accelerate or decelerate. So, when the beam reaches the curved part in the cutting pattern, it’s going to slow down to go into the curve, and then accelerate back up coming out of it. Just like a car might do on a curved road.
So what? Well, the laser is producing a series of pulses of light. And, it doesn’t matter if they’re the ultra-short pulses mentioned earlier or longer pulses. Either way, they’re typically evenly spaced in time – for example, one pulse every millionth of a second (yes, these things are that fast and more so!).
But, look what happens when the motion system goes through a curve while a laser is producing pulses at a fixed repetition rate. Because the beam motion slows down and then speeds back up through the curve, the pulses get placed closer to each other on the part than they were when cutting the straight sections. And that means that the laser is pumping a bit more heat into the part at that point. That’s not a good thing.
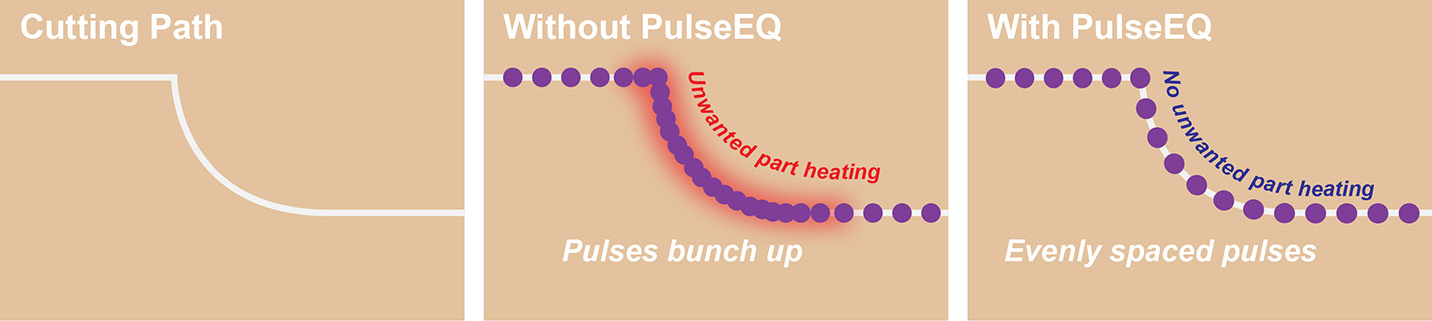
How cool is PulseEQ?
Conceptually, the solution is really simple. Just adjust the laser pulse rate during the cutting process so that the physical spacing between where each pulse hits the work piece is always the same, regardless of how fast the beam is moving relative to the surface.
Of course, doing that in real life isn’t exactly straightforward. For one reason, when you reduce the pulse repetition rate on USP lasers, the pulse energy increases exponentially. Also, you need a control system that tells the laser exactly how fast the beam is moving on the part surface at any moment. Then the laser pulse rate has to be adjusted to match that.
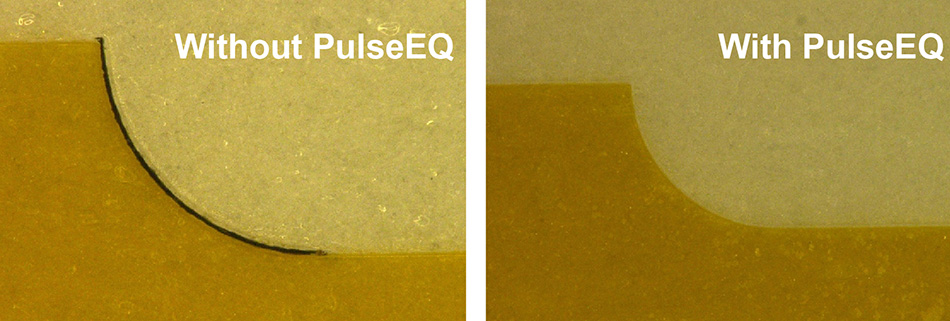
And, those are exactly the things that PulseEQ accomplishes. There’s a lot of technology that goes into making it work, and making it work precisely and reliably. But, the bottom line is that PulseEQ keeps the pulse energy constant at the desired level no matter what repetition rate the laser is operated at. And, it allows the laser repetition rate to match the part motion. So, no matter what the scan pattern and scan speed looks like, the laser cutting power at the work surface always remains the same. This enables the laser to perform the most precise and demanding processing tasks without producing any heat damage to the part.
Because PulseEQ helps Coherent lasers deliver the best possible results in so many different applications, we’ve made it available on all of our industrial USP and nanosecond lasers.
Related Resources