Large Format Windows from Material to Mission
Coherent overcomes the challenges of making large windows for aerospace and defense through advanced manufacturing technology and vertical integration.
August 12, 2024 by Coherent
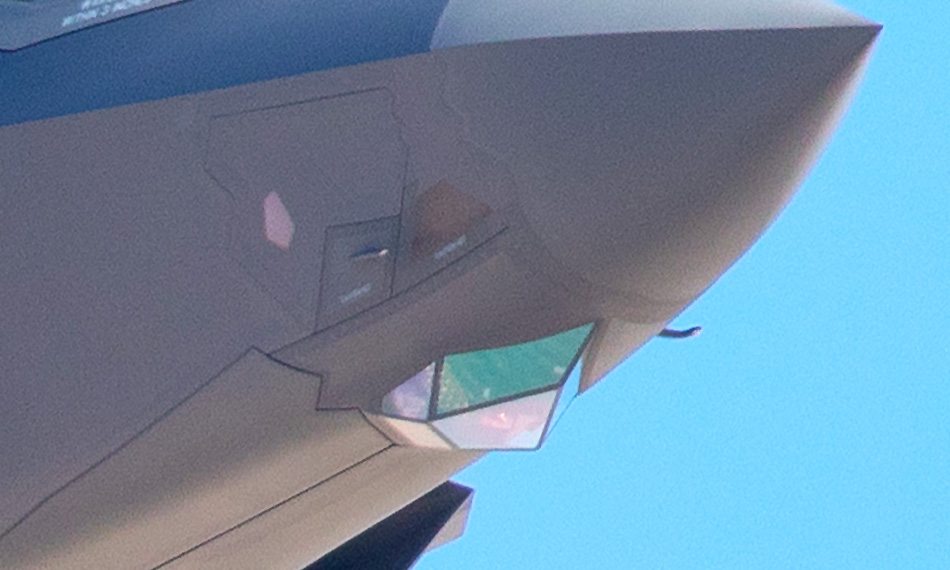
Windows are used on aircraft skins to allow sensors to view the outside scene.
Windows are a big deal in aerospace and defense applications. Quite literally.
In fact, “large format” windows – which usually means those that have at least one dimension greater than 300 mm (12 inches) – are used extensively in airborne, spaceborne, marine, and ground vehicle applications - and many times these windows protect multiple instruments.
However, when optimizing multiple instrument integration, a single large window is usually the preferred solution. Specifically, it is often desirable to share a single window between multiple imaging and sensing systems – like reconnaissance, targeting, and navigation – each of which may operate over different wavelength bands. Reducing window count is important on aircrafts as well -- and even in ground vehicles like tanks --because it simplifies the design and maximizes structural integrity.
Defense applications, in particular, are always tasked with the balancing act that optimizes size, weight, power, and cost (SWaP-c) efficiencies when specifying new equipment. The challenge is how to balance beneficial trade-offs for optimal performance.
The Challenge of Large Format Window Manufacturing
The truth is that making large format windows presents many challenges, starting with the material itself. It takes highly specialized equipment and expertise to grow the most popular window materials – like sapphire or zinc sulfide multispectral (ZnS MS) – in large sizes. Then comes fabrication -- which often involves very high levels of optical and mechanical precision -- followed by anti-reflective coatings. The coatings can range from simple films to sophisticated antireflection thin films to protect patterned, metallized coatings for electromagnetic interference (EMI) protection.
Coherent has supplied large format windows for defense and aerospace applications for more than 30 years and is a vertically integrated manufacturer – from growth through final coating and assembly – for many of the materials that we offer. Our experience and capabilities position us to uniquely understand the challenges involved in making large format windows and to develop innovative solutions to meet the challenging performance, delivery time and cost targets required to support these mission-critical applications.
Material Matters
When it comes to performance and reliability, Coherent carefully considers a number of factors to ensure requirements are met, while taking risk mitigation into account.
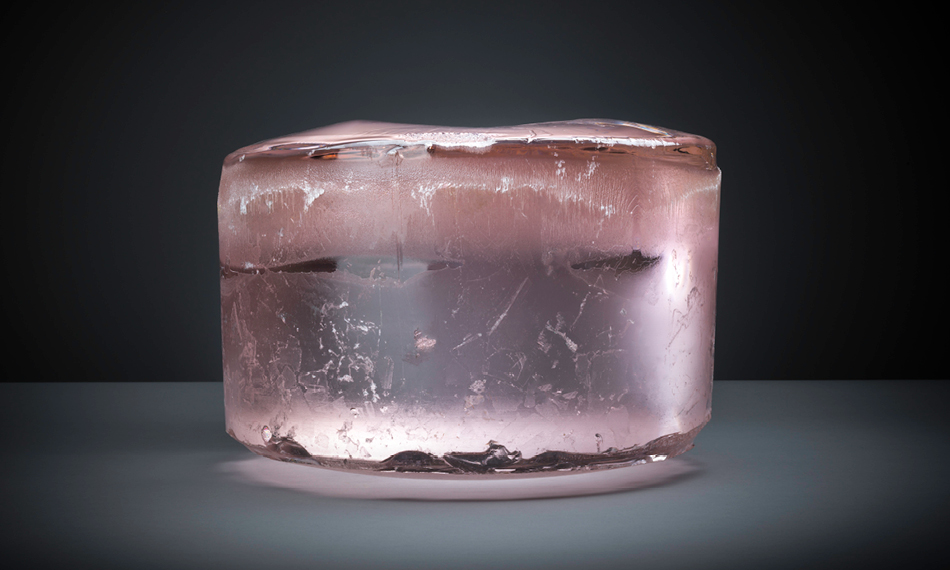
Coherent is an established US-based source for a wide range of materials grown and fabricated into large windows.
To start, selecting the right material is the cornerstone of the large format window production process. At Coherent, we begin by engaging in a detailed conversation with our customers to understand their specific requirements. This is key to ensuring that the finished product will meet their performance and cost targets.
Some of the parameters we typically discuss include:
- Transmission range: The window’s properties must precisely match the equipment it is protecting; that is, it must transmit all the wavelengths needed by any and all instrumentation behind the window.
- Mechanical characteristics: Resistance to pressure, mechanical stress, and shock are frequently important considerations in aerospace and defense applications. Material hardness – which affects how easily it can be scratched or abraded – can also be a factor, although coatings can minimize this challenge.
- Thermal characteristics: The temperature extremes often experienced in aerospace and defense applications can make thermal stability and thermal conductivity key considerations.
- Environmental: For terrestrial uses, it’s common to require that windows resist degradation from exposure to chemicals, weather conditions and, especially, saltwater.
- Radiation hardness: This can come into play for spaceborne and high-altitude use.
- Weight: The density and weight of the material are important whenever weight reduction is critical, such as in aircraft and spacecraft.
- Size availability: The maximum available size varies by material and can present limitations in some instances.
Striking the right balance between these various factors and cost often requires trade-offs. This is why discussing material selection with a vendor who thoroughly understands these materials and their properties is such a critical starting point.
The table below provides a broad comparative overview of the materials and primary characteristics Coherent routinely considers when fabricating windows.
Material |
Transmission range |
Mechanical characteristics |
Thermal characteristics |
Chemical resistance |
Density/ Weight |
Cost |
UV to MWIR |
↑ |
↑ |
↑ |
– |
– |
|
UV to LWIR |
↑ |
↑ |
↑ |
– |
↓ |
|
Visible to LWIR |
– |
– |
– |
– |
↑ |
|
MWIR to LWIR |
– |
– |
– |
– |
– |
|
Visible (red) to LWIR |
↓ |
– |
– |
↓ |
↑ |
|
SWIR to LWIR |
– |
↓ |
– |
↓ |
– |
|
Fused silica |
UV to SWIR |
– |
↑ |
↑ |
↑ |
– |
Spinel |
Visible to MWIR |
↑ |
– |
↑ |
– |
↑ |
ALON |
UV to MWIR |
↑ |
– |
↑ |
– |
– |
Coherent employs several different materials for large format windows, most of which we grow ourselves. No single material is best for all applications, so having this range of choices is essential for meeting specific customer performance and cost targets.
One of the advantages Coherent brings to this discussion is that we grow most window materials in-house and have close partnerships with suppliers for the few materials we source externally. This affords us a deep understanding of each material’s characteristics. Producing our own materials enables us to control every aspect of the process and ensure consistent quality. In some cases, it even allows us to customize a material. For example, we have specific ways we can dope germanium to optimize its performance.
Precision Fabrication
Aerospace and defense applications almost invariably require windows fabricated to exceptional levels of precision. Dimensional tolerances, flatness, parallelism, and wavefront distortion on transmission are all crucial. The difficulty meeting these tight specifications increases substantially with window size.
This is where Coherent excels. We possess an array of advanced production equipment and proprietary processes that enable manufacturing of large optics in diverse configurations, all while adhering to the highest standards of precision.
But our commitment goes beyond just fabrication. We have invested heavily in state-of-the-art metrology and quality control systems. And it is our ability to rigorously measure and validate specifications that enable us to consistently meet customer needs -- because you can’t make it if you can’t measure it. Plus, this instrumentation allows us to fully comply with the strict certification and documentation requirements of the military and aerospace sectors.
One specific fabrication capability at Coherent worth pointing out is our unique ability to “bond on edge.” This means directly joining two or more separate windows together – edge-to-edge -- to yield a single, larger optic. This capability is invaluable for creating large windows from materials that cannot be grown to sufficiently large sizes. It typically provides better functionality in use than mounting multiple windows together in a mechanical frame.
Thin Film Coatings
Precision transmissive optics often utilize thin film coatings to enhance performance, especially antireflection (AR) coatings. But in many aerospace and defense applications, the window coating also serves to enhance component durability. Coatings can improve abrasion resistance to particulates, like sand, or help prevent surface degradation from exposure to corrosive substances, such as saltwater or exhaust fumes.
Just as with fabrication, coating large format windows presents a unique set of challenges as compared to smaller-sized parts. A key characteristic is uniformity – namely, achieving consistent coating thickness, which directly affects coating spectral response across the entire part. Large-sized parts are also more prone to stress and deformation during the coating process. This can lead to warping or cracking, particularly with more brittle materials.
Larger, heavier windows are also more challenging to handle and fixture during the coating process. This increases the risk of damage during handling and requires more mechanically robust support systems.
Addressing these challenges requires both specialized equipment and expertise. Coherent has both. For example, we possess a wide array of deposition chambers representing several different technologies. These include traditional evaporative methods, ion beam sputtering, and plasma-assisted reactive magnetron sputtering. The latter utilizes a high-frequency electrical field to ionize the reactive gas.
Each of these technologies is selected by our experienced engineering team to meet specific performance goals or to strike the optimal balance between performance and cost.
For example, ion beam sputtering yields fully densified coatings which are durable and extremely spectrally stable. It often delivers the ultimate in layer thickness precision and uniformity. But it’s relatively slow. Plasma-assisted reactive magnetron sputtering produces very good uniformity and is fast. It can be readily scaled to larger substrates and higher throughput.
A Pattern of Success
EMI patterning is another type of window surface treatment frequently utilized in windows for aerospace and defense applications. These can heat a window or shield electronic devices and systems from electromagnetic interference that might disrupt their normal operation.
EMI coatings typically consist of a pattern of conductive material – usually a metal – which reflects or absorbs electromagnetic waves over the desired frequency range. The patterns themselves are usually in the form of hub and spoke, overlapping circles, rectangular grid or hexagonal (honeycomb) array, consisting of lines that are in the range of microns wide with spacings generally in the hundreds of microns. Grid parameters (type, size, spacing) are dependent on shielding, transmission, and diffraction requirements.
Coherent excels at creating a pattern that delivers the necessary level of shielding while also maintaining optimal transparency and durability of the window and coatings. We design our products with manufacturability in mind so we can meet mission-critical requirements.
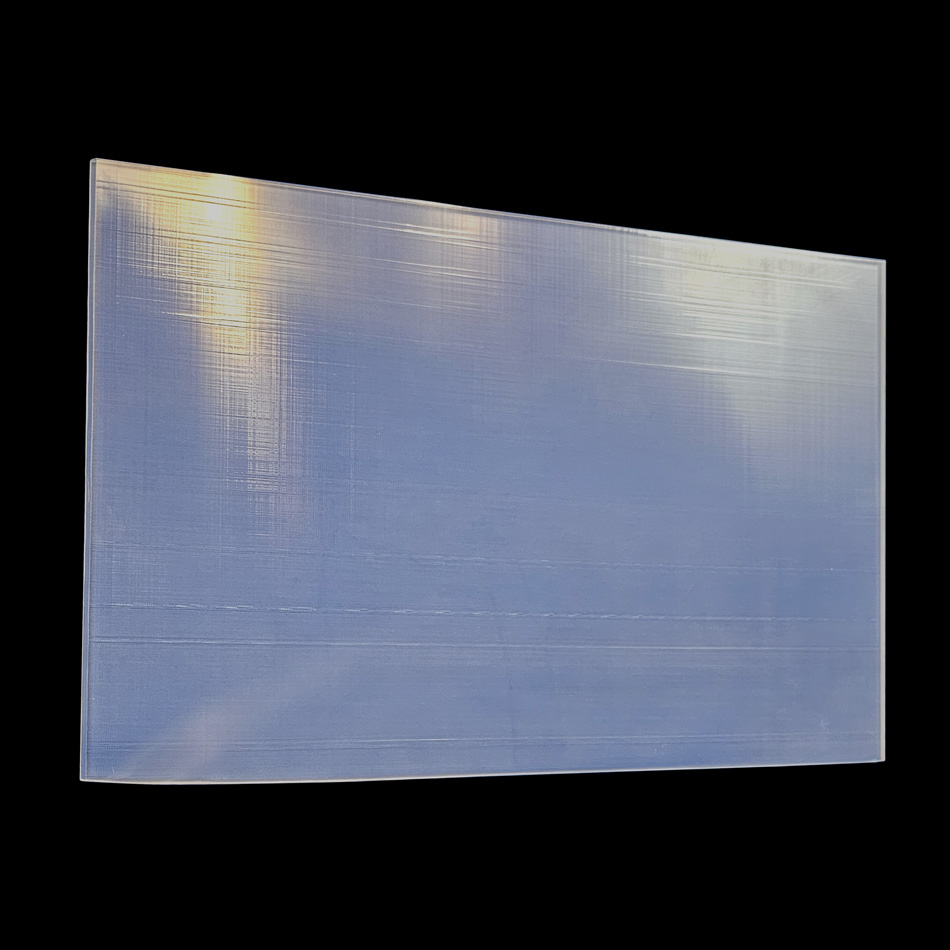
Large windows can be coated with custom or standard patterns and coatings.
Coherent Large Format Windows: Delivering Quality, Performance and Cost
Large format windows are crucial for modern aerospace and defense applications. But there are only a few suppliers capable of fabricating them with the necessary combination of quality, performance, and cost.
Coherent stands out thanks to our comprehensive and vertically integrated approach to manufacturing large format windows. This vertical integration enables us to control every step of the production process, from raw material growth to final assembly. It’s a capability that ensures consistent quality and reliability. And it also gives us the ability to drive rapid innovation and customization to meet specific application requirements.
Learn more about Coherent materials and our optical manufacturing capabilities.