Fiber Lasers: Why We Approach E-Mobility Welding with Finesse, Not Brute Force
Success with the most difficult automotive and e-mobility welding tasks requires precise control over how laser power is delivered to the work piece.
October 26, 2021 by Coherent
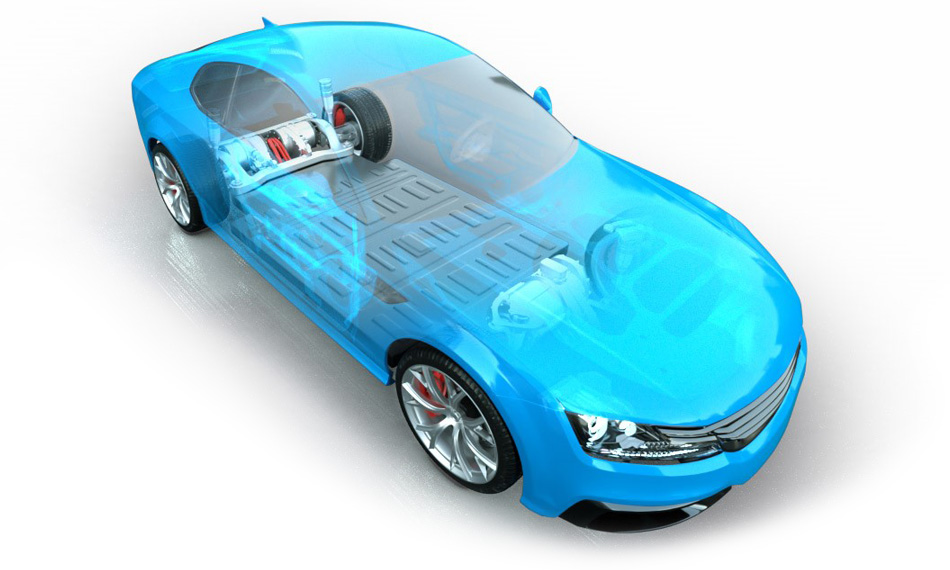
The use of fiber lasers in automotive production has been a huge success story — and they have been adopted for numerous welding and cutting applications including body-in-white, hang-on parts, powertrain components, and more. It’s no surprise. Fiber lasers offer several advantages over most previously employed technologies, both laser, and non-laser.
However, the automotive industry continues to be a great source of innovation. While high-power fiber lasers have been successfully used in automotive production for some time, the trickiest welding processes now coming online to support e-mobility and lightweight require more than just raw power and brute force. Even though there are actually quite a variety of different individual applications, most of them usually involve:
- Very thin or heat-sensitive material
- "Difficult”-to-weld materials like aluminum, copper, and high strength steel
- Joining of dissimilar materials
To complete these more challenging types of tasks, a laser must offer two primary capabilities. The first is sufficient power to support the necessary production throughput rates. High power is also needed to achieve adequate material penetration when working with thicker parts. The second is the ability to precisely control the way that laser power is distributed at the work surface – both spatially and over time.
Power with precision
Coherent developed the Adjustable Ring Mode (ARM) fiber laser specifically to deliver both power and precision. To accomplish this, the ARM uses dual beam output – it produces a central spot, surrounded by another concentric ring of laser light. The power in both the center and ring spots can be independently controlled, and even modulated.
Coherent HighLight FL-ARM Series fiber lasers are available with up to 10 kW of total power. This is more than enough for performing virtually all of the more critical joining tasks at useful throughput rates. In fact, the majority of the most delicate and demanding ones typically use less than half that amount. So, Coherent ARM lasers provide the ability to direct sufficient laser power to exactly where it’s needed, when it’s needed.
One example of how this works is seen in copper welding. Some manufacturers have turned to green lasers for welding copper because that color light is better absorbed by copper than the infrared output of a fiber laser. But, that’s only true at room temperature. Once copper gets heated up, it absorbs IR light well, and once a keyhole is established it gets even better. And then the lower absorption actually becomes an advantage because it allows deeper penetration of the laser light, making it easier to weld thicker substrates.
So, the scenario for welding copper with an ARM laser starts by having power only in the ring beam to heat the material until it melts. Next, a high-power center beam comes on to create the keyhole. However, some power is maintained in the ring during welding because this stabilizes the keyhole, making it less turbulent and chaotic. This reduces spatter and provides more consistent results. When the beam reaches the end of the weld seam, the ring power is turned off completely and the core power is ramped down smoothly to create a clean, even end.
This same ability – to tailor the heating profile to the material so as to maximize keyhole stability and consistency, and to ramp power up and down at the end of the weld – delivers similar benefits when welding other difficult materials, such as aluminum and galvanized steel. And, it enables highly precise welding of thin, delicate, or heat-sensitive materials.

Overpowering logic
Some manufacturers of fiber lasers similar to the Coherent ARM have made a point that their products allow 100% of the total power to be shifted into the core or ring beams as if this were an advantage. But, it isn’t – because the whole magic of the ARM laser is dividing the power between core and ring spreads the heat input into the part in a way that produces better results than a single beam – just like in the copper welding example previously described. Otherwise, why not just use a standard single beam (and less expensive) fiber laser to begin with?
They’ve also created a concern that the Coherent ARM architecture isn’t “flexible.” To understand this claim, you need to know that ARM lasers are actually constructed using two or more fiber laser modules, each of these are coupled into either the core or ring to give various maximum power ratios. (In operation, the power in each can then be smoothly varied from 0% to 100% of this maximum.)
The number of modules that feed into the core and ring fibers are set when the system is manufactured. So an 8 kW ARM laser, which is constructed using four 2 kW modules, can be configured with three different maximum center/ring power ratios. These are 6 kW/2 kW, 4 W/4 kW, or 2 kW/6 kW. And, these totals can’t be subsequently changed, hence the supposed “inflexibility.”
But, the configuration used for any specific customer’s laser is based on process trials conducted long before the laser is purchased. These establish the power levels and power ratios necessary to successfully perform the target operation in production. And, they provide a sufficiently large process window to support any changes needed to accommodate process variations (batch-to-batch changes in raw materials, for example). In addition, a given laser will usually allow very wide latitude for subsequent changes in the process itself. The bottom line is determining the right power and power ratio at the beginning eliminates the need to make large changes to laser output later on.
The competition may claim that the Coherent product isn’t a “real” 8 kW fiber laser. And they’re right – it’s an 8 kW ARM fiber laser. That means it does a better job than anything else in applying laser power in exactly the way that produces the best results for a specific task. And, this same 8 kW fiber laser will continue to yield better results even as your needs change or evolve.
Explore the Coherent Highlight FL ARM Series
Related Resources