WHITEPAPER
MicroLEDs – Laserprozesse für die Bildschirm-Produktion
Überblick
Hochenergetische, ultraviolette Laserstrahlen ermöglichen den UV-Transferprozess für die Herstellung von Bildschirmen, insbesondere für die Laser-Schichtseparation (LLO) und den laserinduzierten Vorwärtstransfer (LIFT) sowie die Pixelreparatur. In diesem Dokument erfahren Sie, wie UVtransfer sicherstellt, dass diese Produktionsschritte für den Massentransfer und die Bestückung auch bei immer kleiner werdenden Formen zukunftssicher bleiben. Außerdem bietet das Verfahren den Vorteil, dass es mit verschiedenen Reparaturschemata kompatibel ist, um die zu erwartende realistische Ausbeute an Stümpfen zu erreichen.
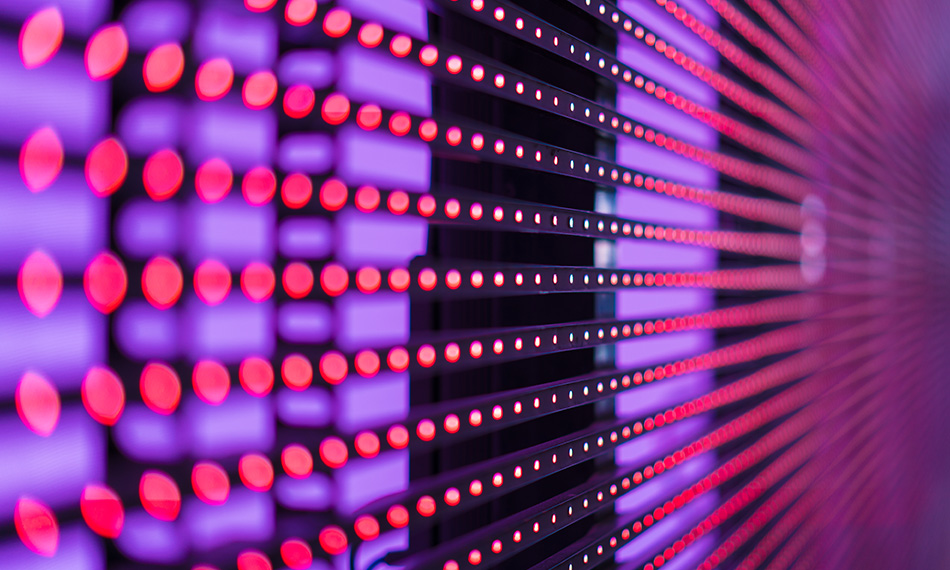
MicroLEDs - Das Potenzial und die Herausforderungen
MicroLEDs (μLEDs) sind ein aufregender neuer Gerätetyp mit enormem Potenzial für zukünftige Bildschirme. Diese typischerweise auf Galliumnitrid (GaN) basierenden Bauelemente haben derzeit Abmessungen im Bereich von 20–50 μm, wobei erwartet wird, dass sie auf 10 μm und kleiner schrumpfen werden. Mit der bestehenden GaN-Fertigungstechnologie auf Saphir-Wafer-Wachstumssubstraten können μLEDs in sehr hohen Dichten mit Straßenbreiten von wenigen Mikrometern hergestellt werden.
Die Kombination aus Mikrometerabmessungen, hoher Helligkeit und hoher Fertigungsdichte kann den Bildschirmmarkt über das hinaus erweitern, was derzeit durch OLED- und LCD-Technologien möglich ist. Zum Beispiel können μLEDs verwendet werden, um miniaturisierte (z. B. <1“), hochauflösende Bildschirme für AR/VR-Anwendungen zu erstellen. Und am anderen Ende des Größenspektrums unterstützen sie sehr große Bildschirme für den Innen- und Außeneinsatz.
Solch große Bildschirme können kostengünstig aus μLEDs hergestellt werden, da bei schrumpfender Chipgröße die Anzahl der Chips, die auf einem gegebenen Wafer gezüchtet werden können, deutlich zunimmt. Folglich wird bei großen Bildschirmen, bei denen der Pixelabstand viel größer ist als die Chipgröße, die Gesamtzahl der Pixel zum wichtigsten Kostentreiber. Dies steht im Gegensatz zu OLEDs und anderen Technologien, bei denen die Kosten mit der Gesamtfläche des Bildschirms steigen.
Vor einem breiten Einsatz von μLEDs gibt es jedoch noch einige technische Herausforderungen zu bewältigen. Eine wichtige Hürde ist die Entwicklung eines Verfahrens, mit dem die Chips aus dem Saphir-Wafer gelöst werden können. Ein anderes ist ein Verfahren, um diese mit mikrometergenauer Präzision und Zuverlässigkeit auf das Bildschirmsubstrat zu übertragen. Und diese Prozesse müssen mit Reparatur-/Ersatzsystemen kompatibel sein, um das unvermeidliche Problem defekter Formen zu lösen. Gleichzeitig müssen sie mit der Automatisierung kompatibel sein und einen hohen Durchsatz liefern, da die LED-Industrie eine bis zu 20-fache Reduzierung der derzeitigen Gesamtkosten anstrebt. Darüber hinaus wird die Erwartung einer kontinuierlichen Entwicklung immer kleinerer Formen Prozesse begünstigen, die diesem Miniaturisierungstrend Rechnung tragen, ohne dass für jede weitere Verkleinerung ein kapitalintensives Umrüsten erforderlich ist.
„...ein kontinuierlicher Trend zu immer kleineren Chips wird Prozesse begünstigen, die diesem Miniaturisierungstrend Rechnung tragen."
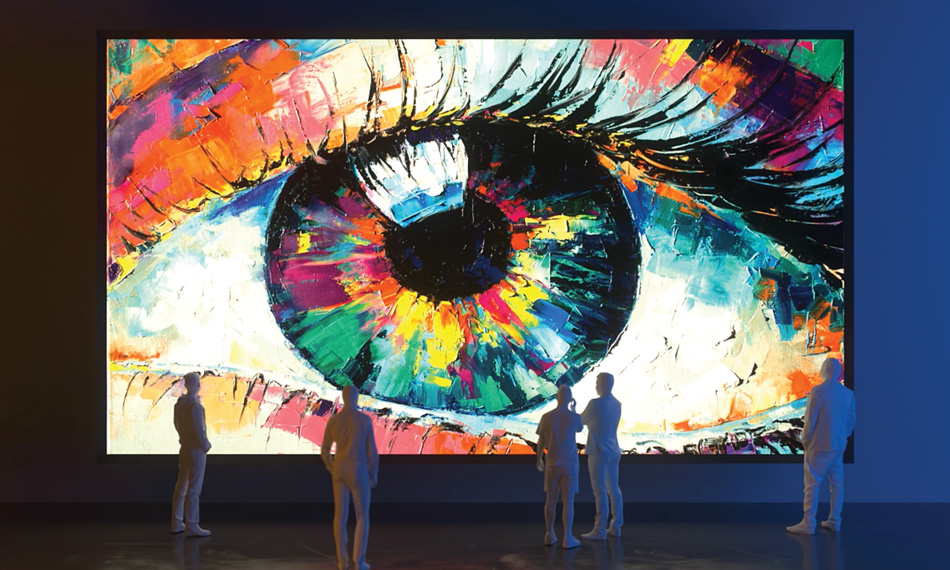
Abbildung 1: Illustration eines großen Direct View MicroLED-Bildschirms.
Laserbearbeitung Kontext
Die Laserbearbeitung mit hochenergetischen ultravioletten Laserpulsen mit Nanosekunden-Pulsdauer bietet eine einzigartige Kombination von Vorteilen, um diese Herausforderungen zu meistern. Kurzwelliges UV-Licht kann dünne Schichten von Materialien an Grenzflächen und Oberflächen direkt abtragen, ohne tief in das Material einzudringen. In Kombination mit der kurzen Pulsbreite vermeidet dieser kalte Photoabtragsvorgang die Entstehung eines thermischen Schocks und die Beschädigung des darunter liegenden Materials. Und die große Pulsenergie bietet einen einmaligen Multiplex-Prozessvorteil, denn der Strahl kann zur Projektion einer Fotomaske verwendet werden, so dass Hunderte oder sogar Tausende von Chips mit jedem Puls bearbeitet werden können. Deshalb sind diese Arten von Lasern in der Bildschirmindustrie als Massenproduktionswerkzeug für die Erzeugung der TFT-Silizium-Backplane sowohl für OLED- als auch für Hochleistungs-LCD-Bildschirms fest etabliert – eine Funktion, die sie zweifellos auch bei den μLED-Bildschirms der nächsten Generation übernehmen werden.
Derzeit bietet die Laserbearbeitung mehrere Möglichkeiten für die Produktion von μLED-Bildschirms:
- Laser-Schichtseparation (LLO) zur Trennung der fertigen μLED vom Saphir-Wafer
- Laserinduzierter Vorwärtstransfer (LIFT), um die μLED von einem Donor auf das Substrat zu übertragen
- Laserreparatur von μLEDs zur Behebung von Ertragsproblemen und Fehlerraten
- Excimerlaser Annealing (ELA) zur Herstellung einer LTPS-TFT Backplane
- Laserschneiden auf verschiedenen Aggregationsniveaus
Im Folgenden finden Sie die wichtigsten Entwicklungen in einigen dieser Bereiche.
Laser-Schichtseparation (LLO)-Update
Die Laser-Schichtseparation (LLO) zur Trennung der fertigen μLEDs vom Saphir-Wafer wurde bereits in Laser Processing of Micro-LEDs beschrieben. Daher werden wir hier nur kurz die wichtigsten Vorteile von LLO für blaue und grüne Stanzformen beschreiben, einschließlich der neuesten automatischen Ausrichtungsfunktion, die jetzt Teil der Entwicklungswerkzeuge ist.
Bulk-GaN-μLEDs werden normalerweise auf Saphir als optimalem Wachstumssubstrat hergestellt. Die dünnen LEDs müssen dann aber vom Saphir getrennt werden, um einen zweiten Kontakt für den vertikalen LED-Betrieb zu schaffen. Außerdem ist der Saphir für die Weiterverarbeitung unpraktisch sperrig, da er 50–100 Mal so dick ist wie die μLED-Matrizen. Daher müssen die μLEDs mit hoher Dichte vom Saphir-Substrat entfernt und auf einen temporären Träger übertragen werden.
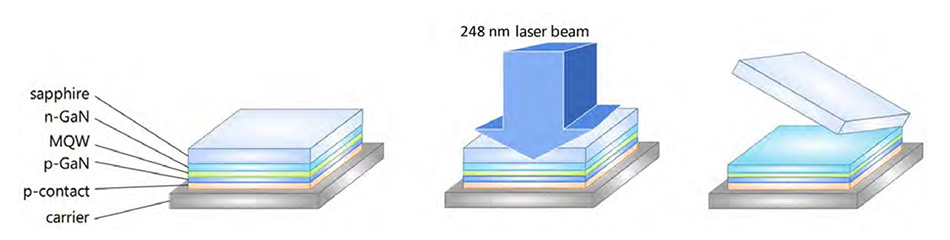
Abbildung 2: Schema eines LLO-Prozesses für die Delaminierung einer GaN-Schicht von einem Saphir-Wafer.
Für die LLO von μLED hat Coherent den UV-Transferprozess entwickelt. Das LLO-Verfahren funktioniert, indem die Stümpfe von der Rückseite (durch den transparenten Saphir) bestrahlt werden. Dadurch wird eine mikroskopisch kleine GaN-Schicht abgetragen, wodurch eine kleine Menge an expandierendem Stickstoffgas entsteht, das den Die freigibt. Die Wellenlänge (248 nm) unseres UV-Transferverfahrens ermöglicht auch die Verwendung mit μLEDs, die mit einigen anderen Materialvarianten einschließlich AlN gezüchtet wurden.
Beim UV-Transferverfahren wird der UV-Laserstrahl zu einem rechteckigen Strahl mit einem „Zylinderhut“-Intensitätsprofil umgeformt, bevor er durch eine Fotomaske auf den Saphirwafer projiziert wird. Diese gleichmäßige Intensität gewährleistet, dass an jedem Punkt des Prozessfeldes die gleiche Kraft angewendet wird. Die Optik ist so konfiguriert, dass mit jedem Hochenergiepuls ein großer Bereich der Matrizen angehoben wird. Dieser Multiplex-Vorteil ist einzigartig für unser LLO-Verfahren, das auf hochenergetischen UV-Excimer-Laserpulsen basiert, und wird ein entscheidender Faktor für die Kostenreduzierung in der Großserienproduktion sein. (Ein ähnliches System von Coherent mit dem Namen UVblade wird heute in der LLO für flexible OLEDs verwendet).
Excimer-basierte LLO-Systeme sind bereits in mehreren μLED-Pilotproduktlinien in Betrieb. Anfangs wurde die Bewegung des Wafers relativ zum projizierten (maskierten) Strahl nur von den Encodern in Translationsphasen gesteuert. „On-Die-Bearbeitung“ ist ein neuerer Fortschritt und das Herzstück des UVtransfer-Prozesses, der nun die Ausrichtungspräzision weiter verbessert und damit kleinere Stanzformen und schmalere Straßen ermöglicht.
Die „On-Die-Bearbeitung“ schließt auch die Möglichkeit aus, dass ein Stempel am Rand der Laserlinie teilweise beleuchtet wird. In diesem Fall wird die Grobausrichtung immer noch von den Encodern in der Translationsphase überwacht. Die Feinausrichtung wird jedoch durch ein intelligentes Bildverarbeitungssystem mit geschlossenem Regelkreis realisiert, das den Wafer anhand des Schachbrettmusters der Matrizen relativ zum Strahl ausrichtet. Dadurch wird sichergestellt, dass die Ränder des Laserfeldes immer mit der Mitte einer Straße übereinstimmen und niemals quer zu einem Würfel liegen.
Abbildung 3: Beim UV-Transferverfahren sorgt die On-Die-Bearbeitung dafür, dass die Ränder des Laserfeldes immer mit der Mitte einer Straße übereinstimmen.
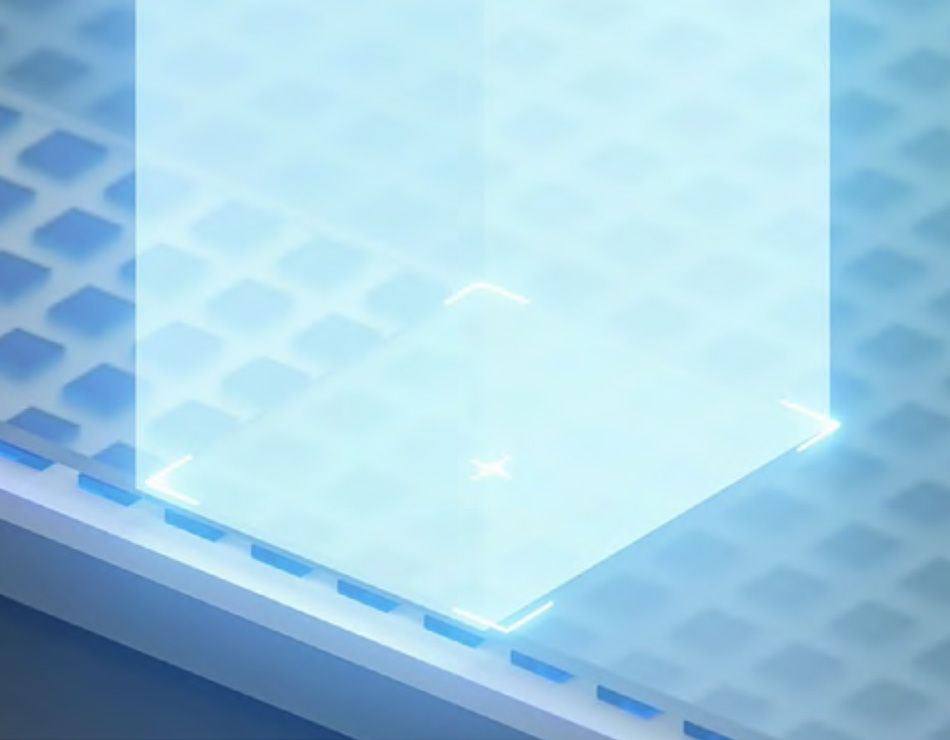
Laserinduzierte Vorwärtsübertragung (LIFT)
Das UVtransfer-Verfahren eignet sich auch perfekt für den Massentransfer und die Platzierung ausgewählter Stanzformen nach dem Prinzip des Laser Induced Forward Transfer (LIFT). Eine große Herausforderung ist dabei der dramatische Unterschied in der Tonhöhe. Auf dem Wafer und dem Transfercarrier sind die Stempel dicht gepackt, derzeit mit einem Abstand von etwa 1000 dpi. Je nach Größe und Auflösung kann der Abstand jedoch nur 50–100 dpi auf dem Bildschirm betragen. Außerdem müssen die Würfel verschachtelt werden, d. h. ein roter, ein blauer und ein grüner Würfel müssen an jeder Pixelposition platziert werden.
Bestehende Nicht-Laser-Übertragungsmethoden können nicht den erforderlichen Durchsatz bei der erforderlichen Auflösung liefern. Mechanische Bestückungsmethoden sind zum Beispiel in Bezug auf Geschwindigkeit und Platzierungsgenauigkeit begrenzt und können daher die aktuelle Technologieentwicklung nicht unterstützen. Flip-Chip-Bonder hingegen sind in der Lage, hochpräzise zu platzieren (z. B. ±1,5 μm), können aber nur einen Chip auf einmal bearbeiten. Im Gegensatz dazu kann UVtransfer sowohl eine hohe (±1,5 μm) Genauigkeit als auch einen enormen Multiplex-Durchsatz liefern, indem Tausende von Stanzformen in einem einzigen Laserschuss bewegt und platziert werden.
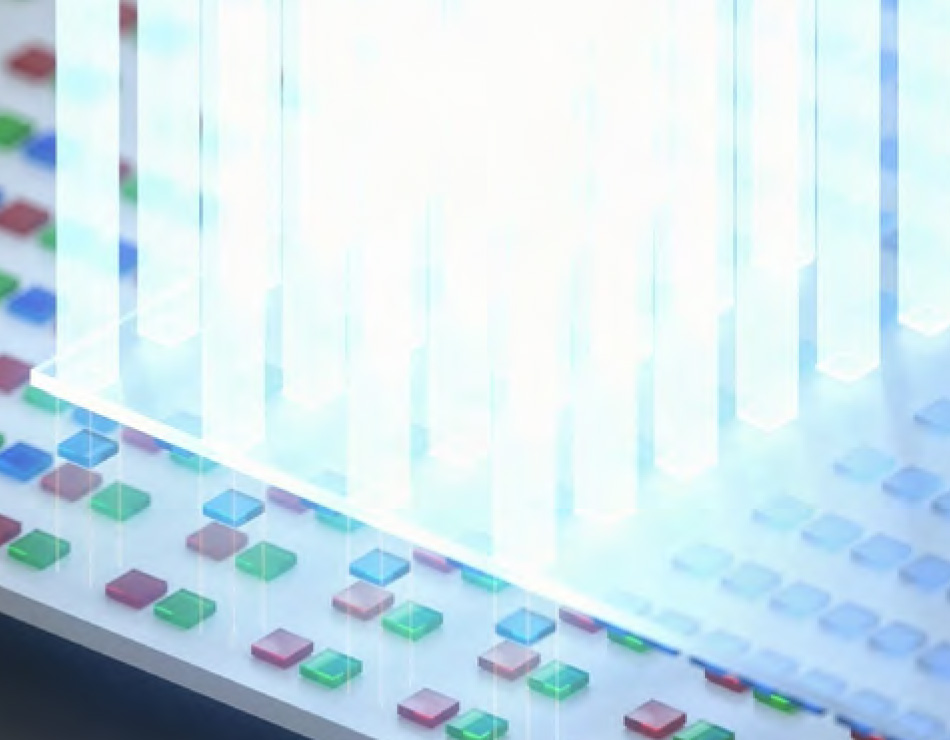
Abbildung 4 zeigt schematisch, wie diese Methode funktioniert. Bei LLO bleiben die Stümpfe mit Hilfe einer dynamischen Trennschicht an einem temporären Träger befestigt. Dies ist ein gutartiger Klebstoff, der UV-Licht stark absorbiert. Der temporäre Träger und die Matrizen werden in engen Kontakt mit dem endgültigen Träger gebracht, bei dem es sich in der Regel um eine Glas- oder Flexplatte handelt, die bereits mit einer TFT-Backplane gemustert und mit einer Bonding-Schicht oder Pads versehen ist. Das UV-Licht wird auf die Rückseite des Trägers gerichtet. Praktisch die gesamte Laserenergie wird von der dynamischen Trennschicht absorbiert, die dadurch verdampft wird. Die Impulskraft, die durch den expandierenden Dampfdruck entsteht, treibt den Stumpf vom Träger auf das endgültige Substrat, idealerweise ohne Rückstände auf den Stümpfen.
Abbildung 4: UVtransfer verwendet ein Step-and-Scan-Verfahren mit einer Maske, um den richtigen Abstand auf dem Bildschirm zu erzeugen.
Im Gegensatz zum LLO-Prozess, bei dem ganze Bereiche benachbarter Chips gleichzeitig bearbeitet werden, ist der Transferprozess der Schritt, bei dem der Abstand der Chips vom engen Abstand des ursprünglichen Wafers auf den Pixelabstand des endgültigen Bildschirms geändert wird. Dazu wird eine Fotomaske mit einem Muster verwendet, das z. B. nur jeden 5. oder jeden 10. Wenn dann der nächste Bereich des Bildschirms in die Position für die Befüllung mit Stanzformen gebracht wird, wird die Maske so indexiert, dass sie sich um eine Einheit des Waferabstandes relativ zum temporären Träger bewegt, so dass eine ganz neue Reihe von Stanzformen übertragen werden kann.
Ein weiterer Unterschied zwischen LLO und Transfer besteht darin, dass bei Letzterem ein Klebstoff abgetragen wird, was eine 5–20-fach geringere Laserfluenz erfordert als bei einem III-V-Halbleiter. Diese hohe Effizienz bedeutet, dass ein hoher Durchsatz mit nur bescheidenen Laserleistungen erreicht werden kann.
Mehrere andere Merkmale unseres UVtransfer-Verfahrens sind entscheidend für seine Umsetzung. Obwohl der Abstand zwischen den auf dem Träger montierten Chips und dem TFT-Substrat nahezu Null ist, muss die Impulskraft gesteuert und kontrolliert werden, um eine erfolgreiche Übertragung jedes Chips mit genauer Platzierung und ohne Beschädigung zu erreichen. Insbesondere müssen sowohl die Größe der Kraft als auch die Richtung der Kraft über den gesamten Bildschirm optimiert und konsistent sein, um das Prozessfenster für die Übertragung nicht zu gefährden.
Ein sehr gleichmäßiger und konsistenter Transfer der Matrizen im Prozessbereich erfordert eine sehr gleichmäßige Laserbestrahlung, die eine Kernkompetenz von Coherent ist und in vielen verschiedenen Anwendungen eingesetzt wird. Auf diese Weise entsteht ein sehr gleichmäßiges 2D-Feld, das dann optisch zu einem Quadrat oder Rechteck mit hohem Seitenverhältnis umgeformt wird, um der Anwendung zu entsprechen. Für zum Beispiel die Übertragung von 6-Zoll-Wafern beträgt das nutzbare Feld auf dem Wafer etwa 100 mm x 100 mm. Wie in Abbildung 4 schematisch dargestellt, bedeutet eine Intensitätsgleichmäßigkeit im lokalen (Einzelchip-)Maßstab, dass der Chip gleichmäßig über seinen gesamten Bereich geschoben wird. Die Kraft wirkt also immer senkrecht, ohne die seitlichen Verschiebungen, die ein Strahl mit gaußförmigem oder schrägem Intensitätsprofil hervorrufen würde. Eine homogene Strahlintensität auf der größeren Skala (Waferbreite) ist ebenso wichtig, da dies sicherstellt, dass jeder Chip mit der gleichen Kraft angestoßen wird.
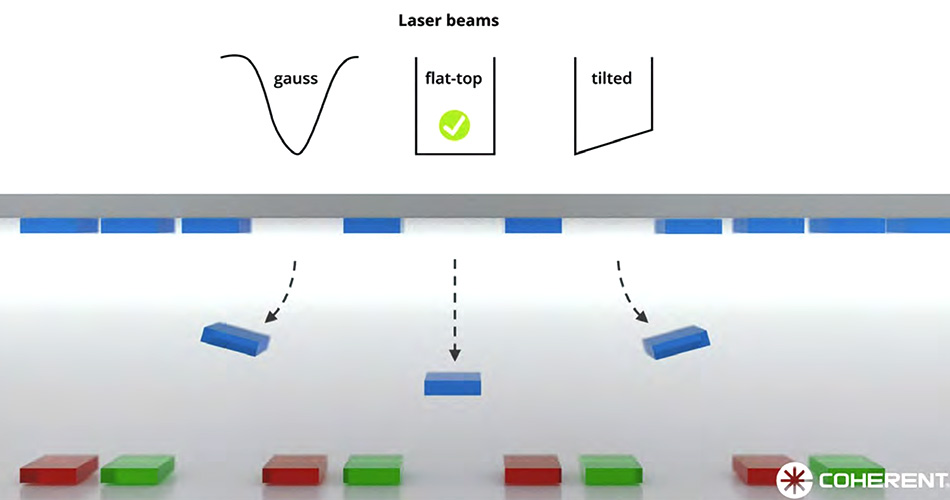
Abbildung 5: Ein sehr gleichmäßiges „Flat-Top“-Balkenprofil ist für eine genaue Platzierung unerlässlich – nicht maßstabsgetreu.
Wichtig ist, dass das UVtransfer-Verfahren sehr viel kleinere Stanzformen (<5 Mikrometer) und schmalere Straßen unterstützen kann als die derzeitige Pilotproduktion. Aufgrund der kurzen UV-Wellenlänge ist in Zukunft sogar eine Auflösung im Mikrometerbereich möglich. Für kleinere Formen ist lediglich eine andere Projektionsmaske erforderlich.
Reparatur/Ersatz von Schurkenstempeln
Der Markterfolg von Bildschirmen, die auf μLEDs basieren, erfordert sowohl eine erhebliche Senkung der Produktionskosten als auch einen unerbittlichen Vorstoß in Richtung 100%ige Ausbeute. Andernfalls sind Bildschirms mit potenziell Hunderten von Millionen Pixeln nicht praktikabel. Aber problematische Stümpfe sind unvermeidlich, so dass die Hersteller nur Produktionstechnologie-Plattformen einsetzen können, die mit Reparatur-/Ersatzplänen kompatibel sind. Der UVtransfer von Coherent, der sowohl für LLO als auch für den Transfer eingesetzt wird, ist mit den Ersatzkonzepten kompatibel, die bereits untersucht werden.
Der erste Schritt in diesem Prozess ist das Auffinden und Entfernen fehlerhafter Dies vom Wafer. Allerdings fehlen dann auf dem vorläufigen Träger die Stellen, die von den entfernten Würfeln belegt worden wären. Diese leeren Stellen müssen dann also auf dem endgültigen Substrat wieder aufgefüllt werden.
Die ausgefallenen Chips können vor dem LLO-Verfahren vom Wafer entfernt werden, indem der Prozess nur auf einen ausgewählten Bereich angewendet wird, bis hin zu einem einzelnen Chip. Die Karte der entfernten Dies von jedem Wafer wird dann nach vorne übertragen und in eine Karte der fehlenden Dies auf dem Substrat umgewandelt. Diese können nach dem Massentransfer durch ein ähnliches Vorwärts-UV-Transferverfahren, diesmal jedoch mit einem definierten einzelnen UV-Strahl, einzeln eingefügt werden. Die Laserleistung ist darauf abgestimmt, ob der Laser ein III-V-Material oder einen Opferkleber abträgt.
Zusammenfassung
MicroLEDs sind eine aufregende neue Technologie, die die Leistung und die Anwendungsmöglichkeiten von Bildschirmen an beiden Enden des Größenspektrums erweitern kann. Niemand bezweifelt, dass es zahlreiche Hürden zu überwinden gibt, bevor ein hoher Durchsatz in der Produktion Realität wird. Aber zwei hochgradig gemultiplexte Prozesse, die UV-Laserstrahlen verwenden, demonstrieren ihre Fähigkeiten auf der Ebene der Pilotanlage. Und was noch wichtiger ist: UVtransfer ist vollständig skalierbar und ermöglicht so eine reibungslose Weiterführung der Miniaturisierung, ohne dass an irgendeiner Stelle kostspielige Neuinvestitionen oder ein Prozesswechsel erforderlich sind. Sobald der Prozess des Kunden entwickelt ist, können die demonstrierten Lösungen aufgrund der Skalierbarkeit des Hochenergie-UV-Lasers leicht auf Produktionslinien übertragen werden, wobei die Präzision der heutigen und zukünftigen Anforderungen erhalten bleibt.