WHITEPAPER
WARUM DAS QUASI-SIMULTANE LASER-POLYMERSCHWEISSEN?
Die Quasi-Simultantechnik für das Laserdurchstrahlschweißen liefert bei vielen Anwendungen bessere Ergebnisse als andere Methoden. Dies gilt vor allem dann, wenn ein Verzug der Teile vollständig vermieden werden muss, oder bei Teilen mit komplexen Schweißnahtgeometrien. Um jedoch eine optimale Qualität in einem quasi-simultanen Schweißprozess zu erreichen, ist ein hohes Maß an Prozesskontrolle erforderlich. Dies ist insbesondere für die Aufrechterhaltung eines stabilen, konsistenten Prozesses notwendig, der skalierbar ist und in mehreren Produktionslinien repliziert werden kann. Um dies zu erreichen, ist in der Regel eine Spannkraftkontrolle mit anschließender Wärmebildgebung erforderlich.
Polymere bieten eine Reihe einzigartiger Eigenschaften, darunter mechanische Eigenschaften, Korrosionsbeständigkeit, Biokompatibilität sowie elektrische und thermische Isolationseigenschaften. Außerdem kosten Polymere im Allgemeinen weniger als andere Materialien. All dies hat dazu geführt, dass sie zunehmend in einer Vielzahl von Produkten verwendet werden.
In vielen Fällen müssen Polymerteile während der Produktion zusammengefügt werden. Bei höherwertigen Produkten – insbesondere bei medizinischen Instrumenten und Sensoren, die in der Automobilindustrie oder in industriellen Anwendungen eingesetzt werden – muss diese Verbindung mit hoher mechanischer Präzision, ohne Verformung der Teile, mit minimaler Partikelproduktion und mit ausgezeichneter Haftfestigkeit erfolgen.
Polymere in Verbindung gebracht
Bei der Serienproduktion wird die Verbindung häufig durch eine Form des Schweißens erreicht. Vor allem für die anspruchsvollsten Anwendungen hat sich das Laserschweißen als die bevorzugte Technologie herauskristallisiert.
Im Vergleich zu anderen Verfahren bietet das Laserschweißen oft eine höhere Schweißqualität, Festigkeit und Präzision sowie eine bessere Wiederholbarkeit bei geringeren thermischen und mechanischen Auswirkungen. Und das alles ohne Partikelbildung. Aber es gibt tatsächlich mehrere verschiedene Techniken für das Laser-Polymerschweißen, und jede dieser Techniken hat eine Vielzahl von spezifischen Implementierungen.
Die meisten von ihnen sind Formen des „Laserdurchstrahlschweißens”. Bei dieser Methode wird ein Teil, das bei der Laserwellenlänge transparent ist, mit einem anderen Kunststoff verbunden, der undurchsichtig ist. Die beiden Teile werden in Kontakt gebracht, wobei das durchsichtige Teil oben liegt. Der Laser wird durch das durchsichtige Teil hindurch nach unten auf das undurchsichtige Teil gerichtet. Das transparente Teil wird erhitzt und geschmolzen, so dass sich die beiden Teile verbinden.
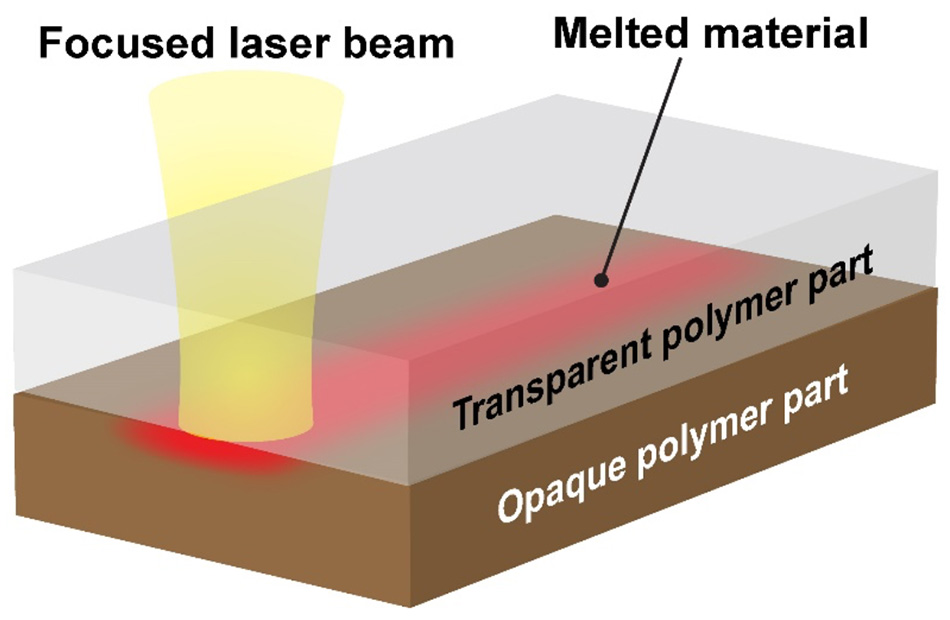
Abbildung 1. Beim Laserdurchstrahlschweißen durchdringt das Laserlicht das transparente Oberteil und schmilzt das Unterteil, um eine Verbindung herzustellen.
Die gängigsten Techniken des Laserdurchstrahlschweißens sind hier zusammengefasst:
Kontur: Wie beim traditionellen Laserschweißen von Metall zeichnet der Laserstrahl den Schweißweg ein einziges Mal nach. Aus diesem Grund ist immer nur ein kleiner Teil der Schweißnaht geschmolzen.
Quasi-Simultan: In diesem Fall fährt der Laserstrahl mehrmals schnell über die gesamte Schweißbahn. Dies geschieht so schnell, dass die gesamte Schweißnaht auf einmal geschmolzen wird.
Linie: Dabei wird der Laserstrahl zu einer dünnen Linie geformt, deren Länge der Breite des Teils entspricht. Diese Linie wird einmal über die gesamte Oberfläche des Teils gestrichen. Zu jedem Zeitpunkt ist nur ein Teil der Schweißbahn geschmolzen.
Simultan: Der Laser wird in einem statischen Muster projiziert, das der Form der Schweißnaht entspricht. Dadurch wird die gesamte Schweißnaht auf einmal geschmolzen.
Die Tabelle fasst die verschiedenen Möglichkeiten, Vor- und Nachteile jeder dieser Methoden zusammen.
Methode |
Vorteile |
Nachteile |
Typische Anwendungen |
Kontur |
Keine Begrenzung der Teilegröße. Kann beliebig geformte Teile schweißen und 3D-Schweißnähte erzeugen. Sehr flexibel und leicht zu ändern. |
Starke örtliche Erwärmung der Teile kann zu Verformungen führen. |
Auto-Rücklichter. |
Quasi-Simultan |
Minimale thermische Belastung vermeidet Verformung der Teile. Sehr flexibel und leicht zu ändern. |
Maximale Teilegröße typischerweise 400 mm x 400 mm. Beschränkt auf 2D-Schweißnähte. |
Medizinische Präzisionsgeräte und elektronische Sensoren. |
Linie |
Einfach zu implementieren. Kompatibel mit relativ großen Teilen. |
Es ist nicht möglich, die Laserleistung oder die Strahlgeschwindigkeit lokal zu ändern. Nicht flexibel. Starke örtliche Erwärmung der Teile kann zu Verformungen führen. |
Produktion von medizinischen Komponenten in großen Mengen. |
Simultan |
Kurze Zykluszeit. Minimale thermische Belastung vermeidet Verformung der Teile. |
Äußerst begrenzt in Bezug auf die Teileformen, die verarbeitet werden können. Begrenzt auf einige einfache Nahtgeometrien, wie Linien oder Kreise. Überhaupt nicht flexibel. Inhomogene und instabile Energieverteilung bei Verwendung einer Multi-Faser-Konfiguration. |
Produktion von Verbrauchsgütern in hohen Stückzahlen. |
Quasi-Simultanes Schweißen
Das Quasi-Simultanschweißen (QS) ist die am weitesten verbreitete Technik für das Fügen von hochwertigen Präzisionsteilen, die nicht die einfachsten Nahtgeometrien aufweisen (z.B. eine Radialnaht oder ein kreisförmiges Muster). Da die gesamte Schweißnaht gleichmäßig auf einmal erhitzt wird, liefert das QS-Schweißen qualitativ hochwertige Verbindungen und vermeidet den Verzug der Teile. Praktisch gesehen handelt es sich um einen flexiblen Prozess, der durch Softwarekontrolle leicht verändert werden kann. QS-Schweißen ist auch eine kosteneffiziente Methode, die mit einer Produktionsumgebung kompatibel ist, die kurze Zykluszeiten erfordert und in der die Losgrößen von klein bis groß variieren können.
Eine wichtige Form des QS-Schweißens ist die „Collapse Rib”-Methode. Die Illustration zeigt die wichtigsten Elemente davon. Bei dieser Technik hat das Unterteil eine dünne Stegstruktur, die in eine entsprechende Nutenstruktur im Oberteil passt. Allerdings ist die Nut etwas breiter als der Steg.
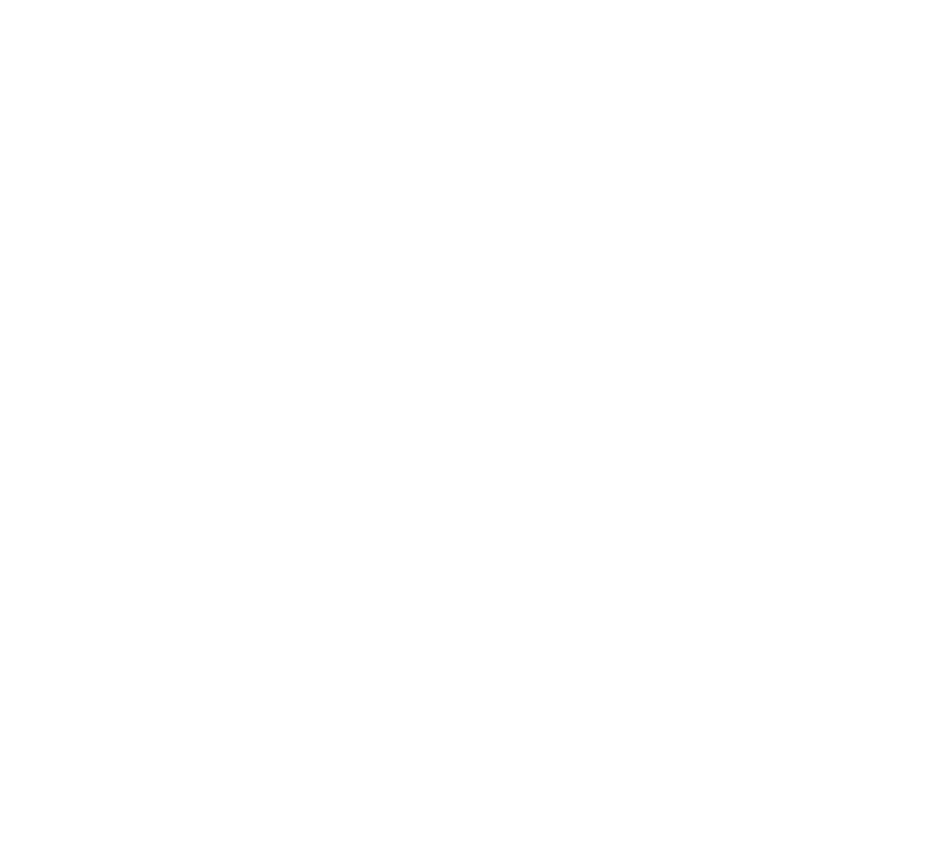
Abbildung 2. Schematische Darstellung der wichtigsten Schritte bei der „Collapse Rib”-Methode dem Quasi-Simultanen Laserdurchstrahlschweißen.
Der untere Steg wird während des Schweißens vom Laser teilweise aufgeschmolzen, während Klemmen die beiden Teile aktiv zusammenpressen. Das geschmolzene Material fließt und füllt einen Teil der Lücke zwischen dem oberen und dem unteren Teil. Dieses Material erstarrt dann wieder und bildet die Schweißnaht. Diese spezielle Art von Laserdurchstrahlschweißen ist besonders nützlich, weil sie eine gute Schweißnaht liefert, selbst wenn die Teile nicht perfekt flach oder eng toleriert sind.
QS-Schweißprozess-Überwachung
Um die Vorteile des QS-Schweißens in Bezug auf Nahtqualität und Ausbeute zu maximieren, ist eine genaue Prozessüberwachung erforderlich. Insbesondere bei der „Collapse Rib”-Methode ist die Setzwegkontrolle ein Schlüsselelement.
Die Setzwegkontrolle besteht in der Regel in der aktiven Überwachung und Steuerung des Setzwegs, d.h. des Ausmaßes, in dem sich das Oberteil während des Schweißens nach unten bewegt. Insbesondere wird die automatische Messung des Setzwegs des Werkstücks für die Steuerung der Spannkraft (und damit der Geschwindigkeit) sowie für die Regelung der Laserleistung verwendet.
Coherent setzt bei seinen Polymer-Schweißsystemen eine ausgefeiltere Version der Setzwegkontrolle ein. Dieses System verwendet integrierte Kraftsensoren für den geschlossenen Regelkreis der servomotorischen Spannvorrichtung und nicht nur für die Höhenmessung. Kein anderer Hersteller wendet diese Methode an. Einige verwenden den Strom des Servomotors als Rückkopplungssignal, aber das liefert nicht die gleiche Messgenauigkeit und den gleichen Grad an dynamischer Kontrolle. Andere Hersteller verwenden überhaupt keine Servomotoren. Stattdessen verwenden sie pneumatische Aktuatoren, die in der Regel nicht die für optimale Ergebnisse erforderliche Präzision oder Reaktionsgeschwindigkeit bieten.
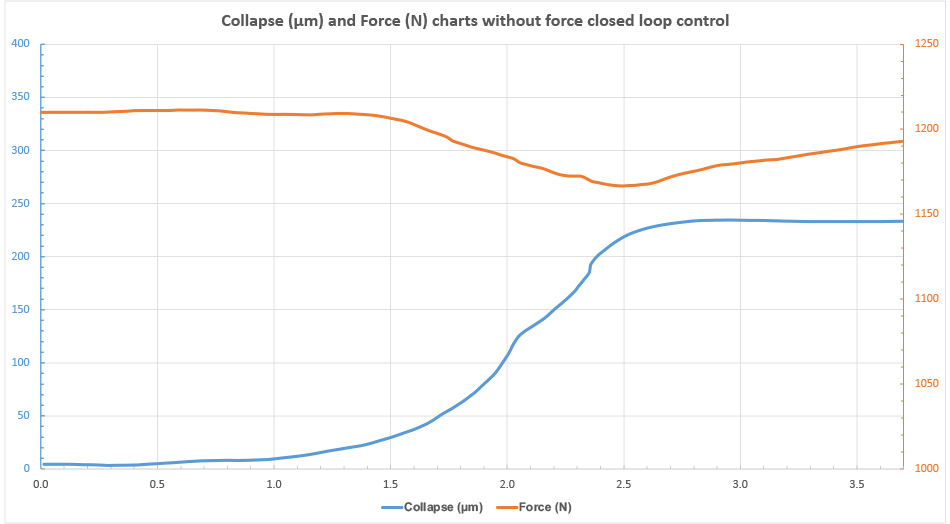
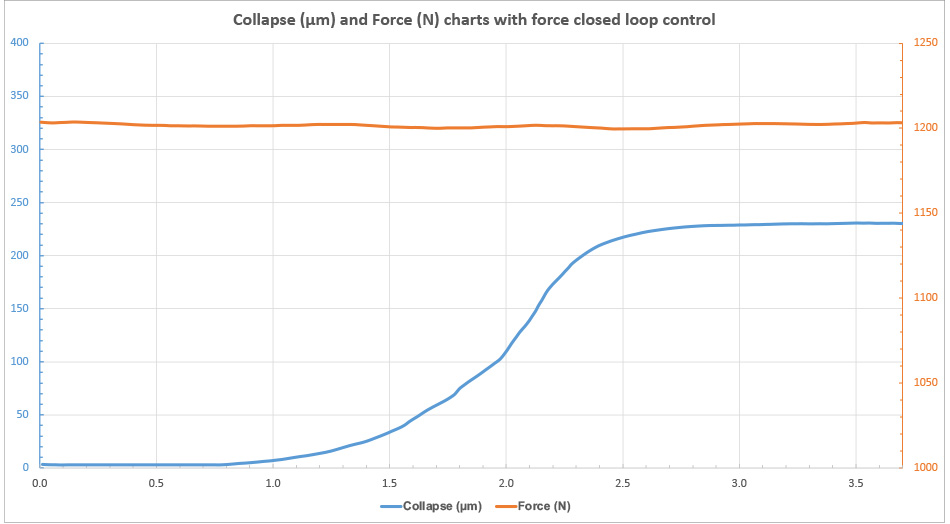
Abbildung 3. QS-Polymerschweißen ohne (links) und mit (rechts) hochpräziser, geschlossener Kraftregelung in Echtzeit. Dieser Ansatz ermöglicht es, sowohl den Setzweg als auch die angewandte Kraft in der Mitte des Prozessfensters zu halten. Dies führt zu konsistenten Schweißnähten, selbst bei Material-, Maß- oder anderen Abweichungen von Teil zu Teil.
Diese Rückmeldung ermöglicht es dem System, Maßabweichungen von Teil zu Teil oder Unstimmigkeiten bei den Materialabsorptionseigenschaften zu korrigieren. Es verbessert die Prozesskonsistenz, auch wenn sich die Umgebung oder die Teile selbst ändern – und erweitert damit das Prozessfenster. Es ermöglicht auch einen einfachen Ausgleich von Unterschieden zwischen den Maschinen. So kann ein an einem Ort entwickelter Prozess an einen anderen Ort verlagert werden und dennoch zuverlässig die gleichen Ergebnisse liefern.
Wärmebildtechnik
Nach der Fertigstellung einer Schweißnaht kann ein Wärmebildkamerasystem (Infrarot) verwendet werden, um die Qualität der Schweißnaht zu beurteilen. Die Wärmebildtechnik misst die Temperatur an der Oberfläche des oberen transparenten Teils und nicht im Inneren der Schweißnaht selbst. Diese Daten über die Oberflächentemperatur liefern jedoch viel nützlichere Informationen über die Schweißqualität als eine direkte Messung der Schweißnahttemperatur.
Um zu verstehen, warum das so ist, sollten Sie bedenken, dass der Laser nur den unteren undurchsichtigen Teil direkt erhitzt. Das obere transparente Teil wird durch Wärmeleitung geschmolzen, da es in Kontakt mit dem unteren Teil gehalten wird.
Die Messung der Oberflächentemperatur des oberen Teils nach dem Schweißen verrät also zwei Dinge. Erstens, wie gut der untere Teil die Laserenergie absorbierte und wie gründlich er geschmolzen wurde. Zweitens, wie gleichmäßig die Klemmkraft auf das Teil ausgeübt wurde, um diese Hitze in das obere Teil zu leiten und es ebenfalls zu schmelzen.
Die Wärmebildkontrolle liefert ein Bild der gesamten Schweißnaht. Unterbrechungen entlang des Pfades weisen auf Lücken in der Schweißnaht hin, und Abweichungen in der Liniendicke zeigen Schwachstellen in der Schweißnaht an.
In der Regel wird die Wärmebildtechnik zur Qualitätsanalyse nach dem Schweißen eingesetzt. Es kann fehlerhafte Teile sofort identifizieren und sie so aussortieren. Dadurch spart der Hersteller Geld, weil er keinen Aufwand mehr in ein schlechtes Teil steckt. Und natürlich wird so auch verhindert, dass ein schlechtes Teil an einen Kunden ausgeliefert wird.
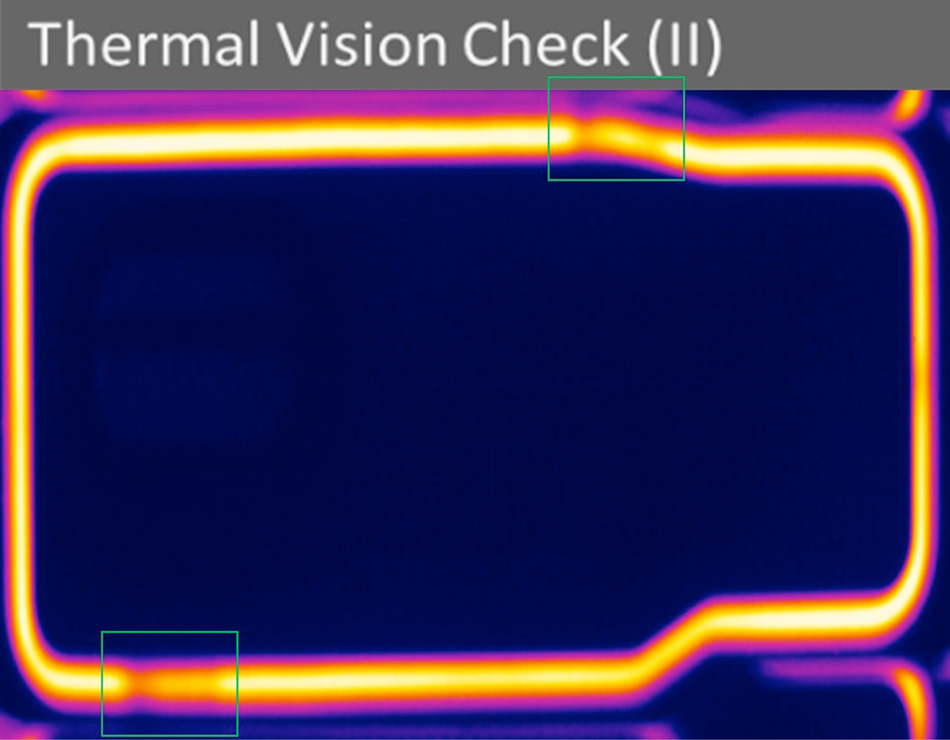
Abbildung 4. Die thermische Überwachung in Echtzeit ermöglicht es, Schweißfehler (grün markiert) sofort zu erkennen und oft sofort zu korrigieren.
Schlussfolgerung
Das Quasi-Simultane Laserdurchstrahlschweißen ist eine besonders nützliche Methode für anspruchsvolle Polymerverbindungsanwendungen. Es kann selbst komplex geformte Schweißnähte mit hoher Schweißpräzision, hervorragender Optik und guten mechanischen Eigenschaften liefern. Bei richtiger Konstruktion entstehen keine Verformungen der Teile und keine Partikel, so dass eine Nachbearbeitung nicht erforderlich ist. Vor allem, wenn es mit geschlossenem Regelkreis für die Spannkraft und mit thermischer Überwachung implementiert wird, bietet es einen robusten und zuverlässigen Prozess, der zudem modular und skalierbar ist.