WHITEPAPER
Polymerschweißen: Ein Erfolgsrezept
Das Laserschweißen bietet gegenüber anderen Verfahren zum Verbinden von Polymeren zahlreiche Vorteile. Die richtige Umsetzung erfordert jedoch ein Verständnis der Technologie sowie Gespräche mit einem erfahrenen Lieferanten in einer frühen Phase des Produktentwicklungszyklus.
Warum Laserschweißen?
Das Laserschweißen bietet zahlreiche Vorteile gegenüber anderen Technologien zum Verbinden von Polymeren. Die wichtigsten davon sind in der folgenden Tabelle zusammengefasst:
Präzision |
Die punktuelle Anwendung von Laserenergie führt zu geringer oder gar keiner Verformung der Teile, liefert enge Maßtoleranzen und kann bei komplex geformten Teilen eingesetzt werden. |
Reproduzierbarkeit |
Der Laserprozess ist von Natur aus sehr stabil und kann mit Equipment zur Prozessüberwachung genau reguliert werden |
Schweißnahtqualität |
Die Schweißnähte sind schmal und kosmetisch hervorragend (kein Grat), und eine Nachbearbeitung ist nur selten erforderlich. |
Schweißnahtfestigkeit |
Das Laserschweißen liefert eine starke, spaltfreie Schweißnaht und kann eine hermetische Abdichtung gewährleisten. |
Geringe Kontamination |
Beim Laserschweißen werden keine Zusatzwerkstoffe (Füllstoffe) verwendet, es fallen praktisch keine Rückstände an. |
Geschwindigkeit |
Der Prozess ist schnell und lässt sich gut automatisieren. |
Aber um all diese Vorteile in der Praxis tatsächlich nutzen zu können, muss der Polymerschweißprozess sorgfältig und korrekt umgesetzt werden. Außerdem spielen die Kosten immer eine Rolle. Daher muss der Polymerschweißprozess mit Laser wirtschaftlich gestaltet werden, ohne Kompromisse in anderen Bereichen einzugehen. Drei Schlüsselaspekte sind vor der Aufnahme der Produktion – und falls möglich, bereits schon im Produktentwicklungszyklus – zu beachten.
Materialauswahl
Eine primäre Überlegung ist die Materialauswahl. Dies gilt insbesondere für das „Through Transmission Laser Welding" (TTLW), eine der am häufigsten verwendeten Techniken. Beim TTLW-Verfahren wird ein für die Laserwellenlänge transparentes Teil mit einem anderen undurchsichtigen Kunststoff verbunden. Die beiden Teile werden so angeordnet, dass sie sich berühren und das durchsichtige Teil oben ist. Der Laser wird durch das durchsichtige Teil hindurch nach unten auf das undurchsichtige Teil gerichtet. Er erwärmt und schmilzt das undurchsichtige Teil, wodurch sie verbunden werden.
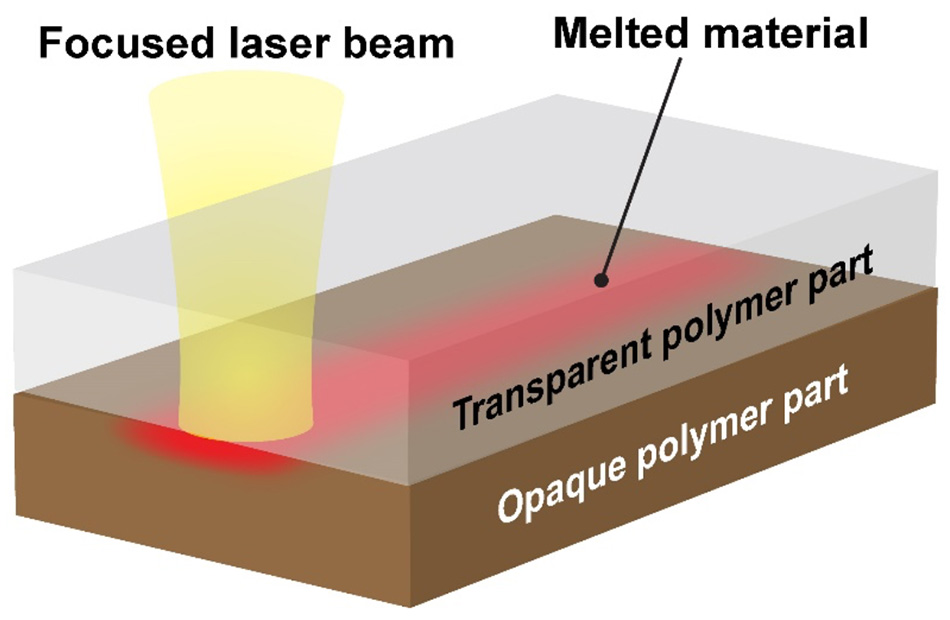
Abbildung 1. Beim TTLW-Verfahren durchdringt Laserlicht das transparente obere Teil und schmilzt das untere auf, um eine Verbindung herzustellen.
Damit das TTLW-Verfahren korrekt funktioniert, muss ein gewisser Temperaturbereich vorhanden sein, in dem beide Polymere (durchsichtig und undurchsichtig) geschmolzen bleiben, ohne sich zu zersetzen. Je größer diese Überlappung ist, desto größer ist das Prozessfenster. Das breitere Prozessfenster macht die Produktion einfacher und robuster. Die Tabelle fasst zusammen, welche gängigen Polymer-Kombinationen mit dem Laserschweißen kompatibel sind.
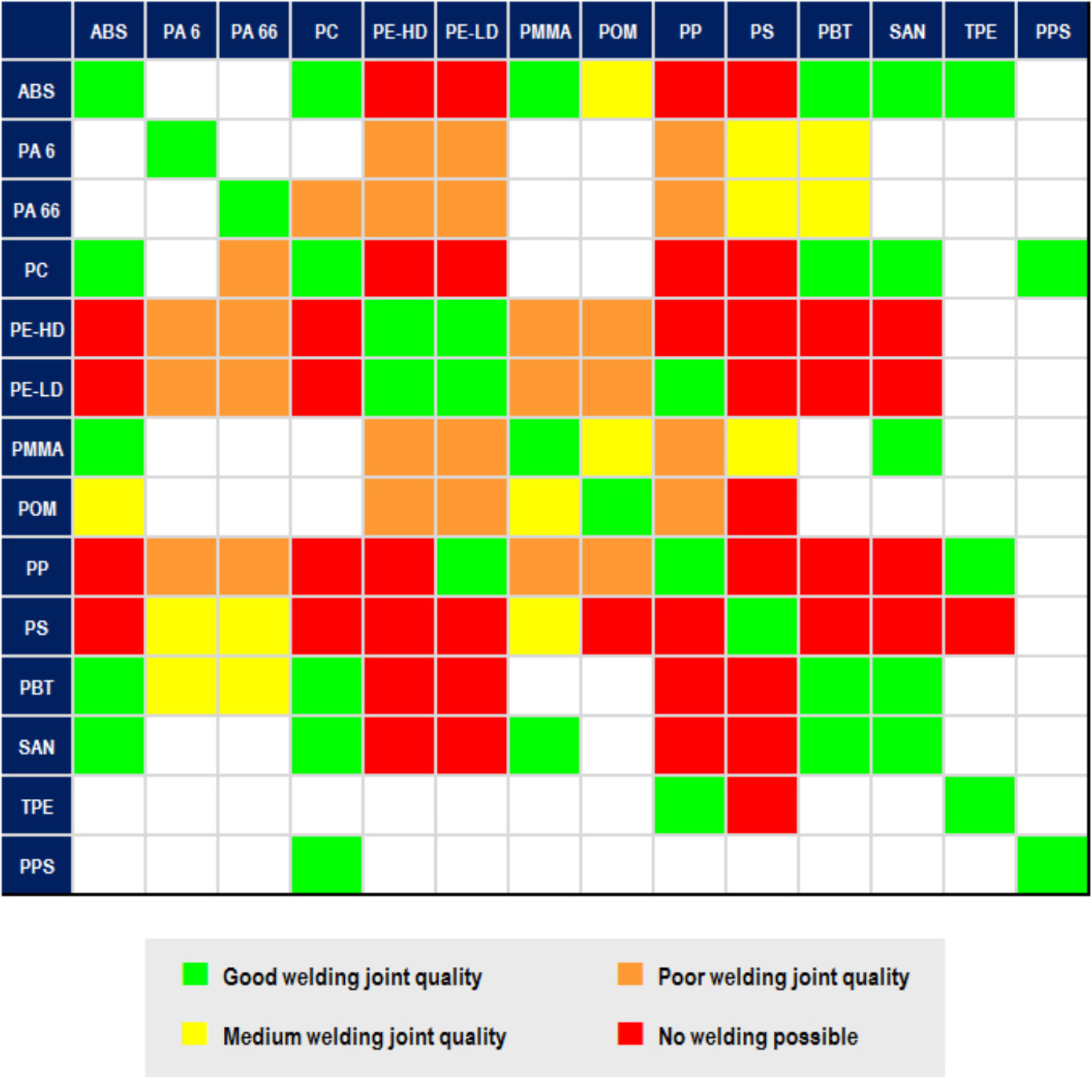
Figur 2. Tabelle der für TTLW kompatiblen Materialien.
Fertigungsgerechte Konstruktion
Die nächste Überlegung betrifft die „fertigungsgerechte Konstruktion”. Eine weit verbreitete TTLW-Technik ist beispielsweise das quasi-simultane Schweißen unter Verwendung der sog. „Collapse Rib"-Methode. In diesem Verfahren besitzt das Unterteil eine Stegstruktur, die in eine entsprechende Nutenstruktur im Oberteil passt. Die Nut ist jeweils etwas breiter als der Steg („Rib“) auf dem unteren Werkstück.
Die erfolgreiche Umsetzung des „Collapse Rib”-Verfahrens erfordert eine Teilekonstruktion mit ausreichend Platz – an genau der richtigen Stelle – damit die Klemmen einrasten und während des Schweißens die erforderliche Abwärtskraft liefern können. Allerdings muss die Klemmstelle dem Laserstrahl einen ungehinderten Zugang für den gesamten Schweißpfad ermöglichen.
Auch die Abmessungen und Formen der Stege und Nuten müssen so gewählt werden, dass genügend geschmolzenes Material für den Fügeprozess zur Verfügung steht und der entstehende Schmelzgrat aufgenommen werden kann. Außerdem müssen die Teile so konstruiert werden, dass ein ausreichender Hub beim „Collapse Rib“ Verfahren gewährleistet ist. Bei hochpräzisen Anwendungen müssen unter Umständen Ausrichtungsmerkmale, wie z. B. Passstifte, in die Konstruktion der Teile integriert werden. Ziel ist es, eine starke Schweißnaht mit gutem Aussehen zu erreichen und gleichzeitig die Notwendigkeit einer Nachbearbeitung (Trimmen oder Entfernen von Graten) zu vermeiden.
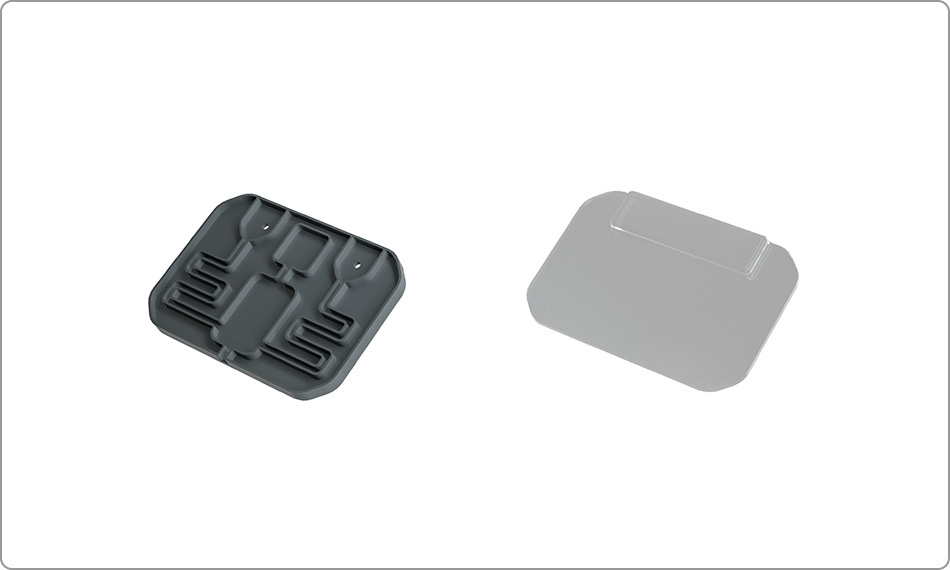
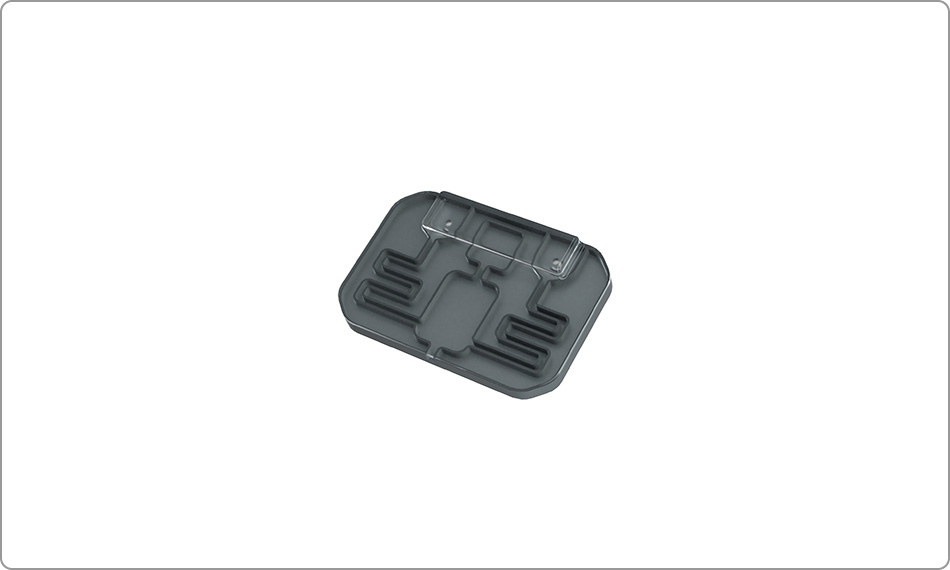
Figur 3. Ein Beispiel von zwei Polymerteilen vor und nach dem Schweißen.
Auswahl des richtigen Partners
Eine letzte Überlegung ist die Auswahl eines geeigneten Systemlieferanten. Dies ist aus zwei Gründen für Polymerschweißsysteme besonders wichtig. Der erste Grund ist der Zugang zu spezialisiertem Laser-Know-how, der zweite die Unterstützung bei der Prozessentwicklung.
Nur mit einem hohen Maß an Lasersystemkenntnissen kann sichergestellt werden, dass die richtige Laserquelle und das richtige Strahlführungssystem für die verwendeten Materialien und Teilekonfigurationen ausgewählt werden. Ein Lasersystem muss so ausgelegt sein, dass es die Energie in einer Weise liefert, durch die das Teil schnell genug geschweißt wird, um den gewünschten Durchsatz zu erreichen. Doch das Problem einfach mit einer Erhöhung der Leistung anzugehen, erhöht die Systemkosten. Hier muss das optimale Gleichgewicht erreicht werden.
Ein erfahrener Lieferant kann darüber hinaus verschiedene praktische Themen in Bezug auf die Einspannwerkzeuge, die Handhabung der Teile, die mechanische und softwaretechnische Schnittstelle des Polymerschweißsystems mit anderen Produktionsanlagen und natürlich bezüglich der Betriebskosten ansprechen.
Die Prozessentwicklungsunterstützung ist wertvoll, weil es oft einen ziemlich großen „Parameterraum" gibt, der für das Laserschweißen erforscht werden muss. Vorkenntnisse sind sehr hilfreich, um schnell die optimalen Laserbetriebsbedingungen zu bestimmen und zu ermitteln, welche Prozessvariablen für das Erreichen der gewünschten Erträge überwacht oder gesteuert werden müssen.
Es ist ferner sehr hilfreich, wenn der Schweißanlagenlieferant auf eine Vielzahl unterschiedlicher Laser zurückgreifen kann, um den Prozess tatsächlich an realen Teilemustern zu testen. Im Idealfall kann das Anwendungslabor des Herstellers sogar das „Prozessrezept“ entwickeln und verfeinern. Diese Art von Aufwand hat allerdings offensichtlich höhere Vorlaufkosten. Doch dies spart Geld, weil das System dadurch schneller in Produktion gebracht wird und dann bessere und zuverlässigere Ergebnisse liefert.
Zusammenfassend lässt sich sagen, dass das Laserstrahlschweißen ein präzises Fügen von Polymerteilen ermöglicht und eine kostengünstige Methode für sehr unterschiedliche Produktionsvolumina ist. Das Laserstrahlschweißen kann dazu beitragen, die Vorteile von Polymeren als vielfältiges Material einzulösen: Kosten zu senken, Gewicht zu sparen und eine erweiterte Funktionalität bei vielen Produkten zu bieten. Wenn ein Unternehmen nicht bereits über Fachwissen im Bereich des Polymerschweißens verfügt, ist es für eine effektive Implementierung hilfreich, von Anfang an mit einem sachkundigen Anlagenlieferanten zusammenzuarbeiten.