WHITEPAPER
SHARP™ TECHNOLOGIE FÜR LiB-ABFÄLLE
SHARP (Streamlined Hydrometallurgical Advanced Recycling Process)
Dr. Ghazaleh Nazari
Senior Direktor für Technologie
Zusammenfassung
Coherent hat ein optimiertes hydrometallurgisches fortschrittliches Recyclingverfahren (SHARP) entwickelt und validiert, um kritische Metalle effizient aus der schwarzen Masse von Lithium-Ionen-Batterien (LiBs) zurückzugewinnen und hochwertige Batteriematerialien herzustellen. Diese Technologie wurde erfolgreich hochskaliert. Die Auswirkungen sind wie folgt:
#1. Qualität: Rohstoffflexibilität; >95 % Rückgewinnung kritischer Metalle und Herstellung von Kathodenvorläufern und Kathodenmaterialien, die für die LiB-Produktion geeignet sind.
#2. Umweltverträglichkeit: 60 %, 70 % bzw. 60 % geringerer Energieverbrauch, Wasserverbrauch und Gesamtemissionen im Vergleich zu herkömmlichen hydrometallurgischen Verfahren. Keine Ableitung von Flüssigkeiten, keine Erzeugung von giftigen festen, gasförmigen oder flüssigen Abfällen und Erzeugung von wertvollen Nebenprodukten.
#3. Kosten: Dieses optimierte Verfahren ermöglicht im Vergleich zu herkömmlichen hydrometallurgischen Verfahren mindestens 50 % geringere Kapitalkosten und 50 % geringere Reagenzien- und Betriebskosten.
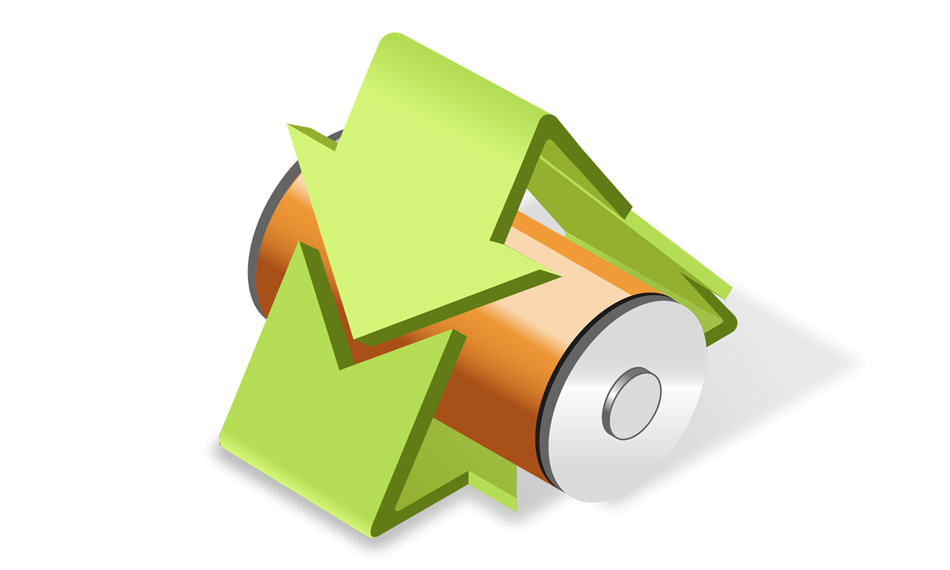
In den meisten hydrometallurgischen Prozessen erfordert die Trennung kritischer Metalle komplexe und empfindliche Prozessschritte zur Lösungsmittelextraktion. Es sind viele Ausrüstungsteile und eine große Stellfläche erforderlich, was zu hohen Kapitalkosten führt. Bei der SHARP-Technologie werden mehrere Metalltrennschritte umgangen. Kathodenvorläufer und Kathodenmaterialien werden direkt aus Batterieabfällen hergestellt, ohne dass eine Trennung und Reinigung kritischer Metalle erforderlich ist. Diese Technologie wurde in einer größeren und kontinuierlichen Konfiguration hochskaliert und validiert, um das Produkt zu qualifizieren und prozessökonomische Vorteile aufzuzeigen. Der Betrieb der Pilotanlage war erfolgreich und bestätigte das geringe Risiko bei der Weiterentwicklung. Dies liegt daran, dass die für den Prozess erforderliche Ausrüstung nachweislich häufig und erfolgreich in der Hydrometallurgie-Industrie eingesetzt wird. Um das Risiko zu reduzieren und eine genaue kommerzielle Anlagendimensionierung, einen schnellen Hochlauf und die Produktion hochwertiger Produkte sicherzustellen, wurde eine stufenweise Hochskalierung implementiert.
Eine sich entwickelnde Chance
Um das Wachstum des Marktes für Elektrofahrzeuge (EV) aufrechtzuerhalten, ist es entscheidend, die Rohstoffquellen zu sichern. Angesichts all der neuen und geplanten Entwicklungen bei Batterieanwendungen wird das Recycling von LiBs am Ende ihrer Lebensdauer (EOL) immer wichtiger. Zwar besteht die Möglichkeit der Aufarbeitung und Wiederverwendung von LiBs für Second-Life-Anwendungen, letztlich müssen LiBs jedoch entsorgt werden. Mit dem bevorstehenden Anstieg der Nachfrage nach LiBs auf dem Elektrofahrzeugmarkt wird das Recycling einfacher, da LiBs größer und daher einfacher zu beschaffen sind. Die früheste Generation dieser Batterien wird immer noch verwendet, da Elektrofahrzeugbatterien ihr EOL typischerweise nach 10 – 12 Jahren erreichen. Die Entsorgung von EOL-Batterien wird in den nächsten Jahren zunehmen.
Produktionsabfälle sind eine weitere wichtige Materialquelle für das Recycling, wie in Abbildung 1 dargestellt. Die Ausschussquoten für die LiB-Produktion liegen bei etwa 5 % bei den besten Herstellern, 10 % bei typischen Herstellern und bis zu 30 % oder mehr in der Anlaufphase. Angesichts der schnellen Einführung von Elektrofahrzeugen wird mit einer erheblichen Menge an ausrangierten Batteriematerialien gerechnet, die den Großteil des LiB-Abfalls in diesem Jahrzehnt ausmachen. Dadurch entsteht ein erheblicher Recyclingbedarf. Schätzungen zufolge werden zwischen 2020 und 2030 mehr als 15 Millionen Tonnen Abfall aus der LiB-Produktion anfallen.
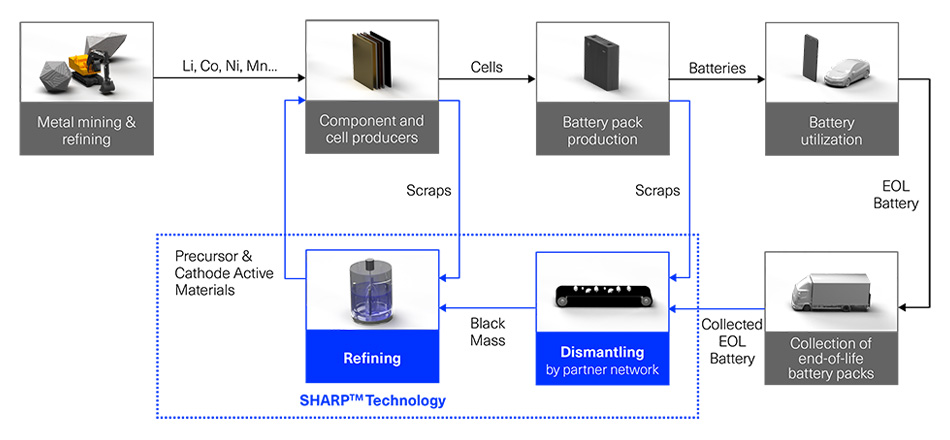
Abbildung 1. Lebenszyklus eines Li-Ionen-Akkus.
Kritische wertvolle Metalle und der Umgang mit ihnen
Aktuelle Bewertungen der Lieferkette dieser wertvollen Metalle aus Primärquellen offenbaren eine Reihe von Risiken, darunter politische, sicherheitsrelevante und geschäftliche Risiken, die mit ihrer geografischen Konzentration verbunden sind. Im Falle von Lithium stammt etwa die Hälfte des weltweiten Erzangebots aus Australien und wird nach China exportiert, wo es raffiniert und im Inland verwendet wird. Lateinamerika ist ein weiterer wichtiger Lithiumlieferant, und die Region steht zunehmend unter dem Druck, in der Wertschöpfungskette nach oben zu gelangen und in einem schwierigen politischen Klima zu agieren.
Kobalt, das wertvollste Metall in aktuellen Batteriedesigns für Elektrofahrzeuge, wird aufgrund seines Potenzials, die Lieferkette zu stören, als Hochrisikomineral eingestuft. Dies liegt vor allem daran, dass mehr als die Hälfte des weltweiten Kobaltvorkommens in der Demokratischen Republik Kongo abgebaut wird, wo die Besorgnis über Arbeits- und Menschenrechtsverletzungen zunimmt.
Forschung und Experimente zu kobaltarmen oder kobaltfreien Batteriedesigns zielen darauf ab, die Abhängigkeit von Kobalt zu verringern, ohne die Leistung zu beeinträchtigen. Die meisten Lösungen basieren entweder auf NMC-Chemikalien mit hohem Nickelgehalt, was die Nachfrage und damit den Preis für Nickel weiter erhöhen wird, oder auf der Verwendung von LFP mit geringerer spezifischer Kapazität, die immer noch stark auf Li angewiesen sind.
Die Umstellung auf Elektrofahrzeuge ist ein Hauptbestandteil der Umweltpolitik vieler Länder, um den Einsatz fossiler Brennstoffe einzudämmen und den Klimawandel zu bekämpfen. Die Lebenszyklusanalyse von Elektrofahrzeugen zeigt jedoch, dass der Rohstoffabbau, seine Verarbeitung und Lagerung sowie die Entsorgung verbrauchter LiBs erhebliche Auswirkungen auf die Umwelt haben. Der Schlüssel zur deutlichen Reduzierung der gesamten Umweltauswirkungen von Elektrofahrzeugen liegt im Recycling der verbrauchten LiBs. Die Konzentrationen der Metalle in LiB übersteigen oft die im Erz, was ihre Gewinnung relativ einfacher macht. Dadurch werden natürliche Ressourcen erheblich geschont, der Energieverbrauch bei der Verarbeitung gesenkt und die Entsorgung giftiger Abfälle entfällt.
LiB-Recyclingprozesse
Am Ende ihrer Nutzungsdauer werden LiBs gesammelt und einer Recyclinganlage zugeführt. Um die gespeicherte Restenergie vollständig abzubauen, werden die Batterien zunächst entladen. Anschließend werden die Batterien zerlegt, entweder manuell oder durch Zerkleinern der Batteriemodule in einem Schredder oder einer Mühle. Dadurch entsteht Granulat, das gesiebt wird, um Materialien wie Stahl, Kunststoff, Aluminium und Kupfer von der sogenannten „schwarzen Masse“ zu trennen. Abbildung 2 zeigt die Bestandteile von LiBs in Gewichtsprozent.
Der bestehende kommerzielle Weg zur Verarbeitung des LiB-Abfalls sind pyrometallurgische Prozesse, bei denen das Schmelzen der Kernprozessschritt ist. Dieser Weg birgt erhebliche Hürden wie einen hohen Energieverbrauch, eine kostspielige Behandlung giftiger Gase und den Verlust von Lithium in der Schlacke. Darüber hinaus liegen die zurückgewonnenen Metalle in einer Form vor, die für die Batterieproduktion ungeeignet ist und eine zusätzliche Verarbeitung zur Trennung in einzelne Metallverbindungen erfordert.
Hydrometallurgische Prozesse umgehen die Einschränkungen pyrometallurgischer Prozesse, stellen jedoch ihre eigenen Herausforderungen dar. Die meisten hydrometallurgischen Prozesse beinhalten die Lösungsmittelextraktion – ein Prozess, der viele Extraktions-, Wäsche- und Stripping-Schritte sowie komplexe Ausrüstung und einen großen Platzbedarf und damit hohe Kapitalaufwendungen erfordert. Darüber hinaus verbrauchen diese Prozesse große Mengen an Reagenzien, Brennstoff und Strom und erzeugen eine erhebliche Menge an Prozessabwässern. Bisher wurde kein hydrometallurgisches Verfahren zur Rückgewinnung von LiB-Abfällen kommerziell umgesetzt.
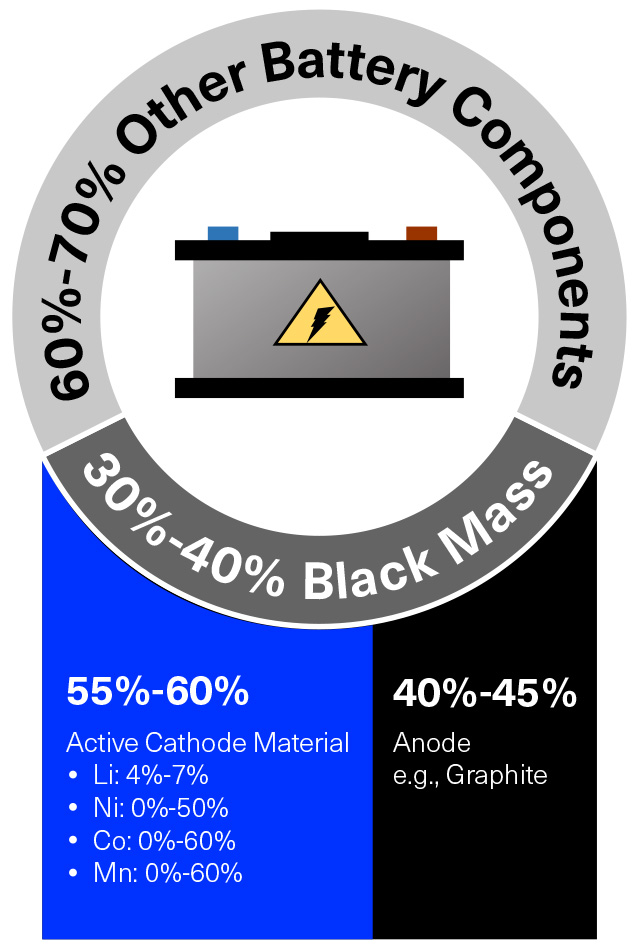
Abbildung 2. Bestandteile von LiBs in Gewichtsprozent.
Durch die Anwendung eines effizienten hydrometallurgischen Verfahrens kann die Rückgewinnung wertvoller Metalle in der schwarzen Masse mehr als 95 % betragen. In Kombination mit den mechanischen Trennverfahren können mehr als 80 % der Bestandteile der Batterie zurückgewonnen werden.
Coherent ist im Rahmen seiner Mission, die Welt sicherer, besser, gesünder und effizienter zu machen, ein weltweit führender Anbieter von seltenen Metallraffinerien und verfügt über eine herausragende Erfolgsbilanz in den Bereichen Umwelt, Gesundheit und Sicherheit (EHS) sowie hervorragende Qualität. Coherent verfügt über mehr als 30 Jahre umfangreiches Fachwissen in der extraktiven Metallurgie, wobei kompetente und erfahrene Ingenieure und Chemiker das Herzstück verschiedener neuer Produkt- und Prozessentwicklungen bilden. Eine dieser Innovationen ist die Entwicklung der SHARP-Technologie zur effizienten Rückgewinnung kritischer Metalle aus der schwarzen Masse von LiBs.
Unsere Technologie wurde erfolgreich hochskaliert und hat sich als technisch machbar erwiesen, um kritische Metalle effizient zurückzugewinnen und Materialien in Batteriequalität herzustellen. Der Pilotanlagenbetrieb hat sich in einer größeren und kontinuierlichen Konfiguration bewährt und seine wirtschaftlichen Vorteile wurden nachgewiesen. Um das Risiko zu reduzieren und eine genaue kommerzielle Anlagendimensionierung, einen schnellen Hochlauf und die Produktion hochwertiger Produkte sicherzustellen, wurde eine stufenweise Aufskalierung implementiert.
Abbildung 3 verdeutlicht die Vorteile der vorgeschlagenen Technologie im Vergleich zum aktuellen Stand der Technik, wie oben erläutert. Im Gegensatz zu pyrometallurgischen Verfahren wird Lithium zurückgewonnen und es entsteht kein giftiges Gas. Im Gegensatz zu herkömmlichen hydrometallurgischen Verfahren wird der Großteil des Einsatzmaterials dem kostengünstigeren und vereinfachten Recyclingprozess zugeführt, wobei die Trenn- und Reinigungsschritte umgangen werden.
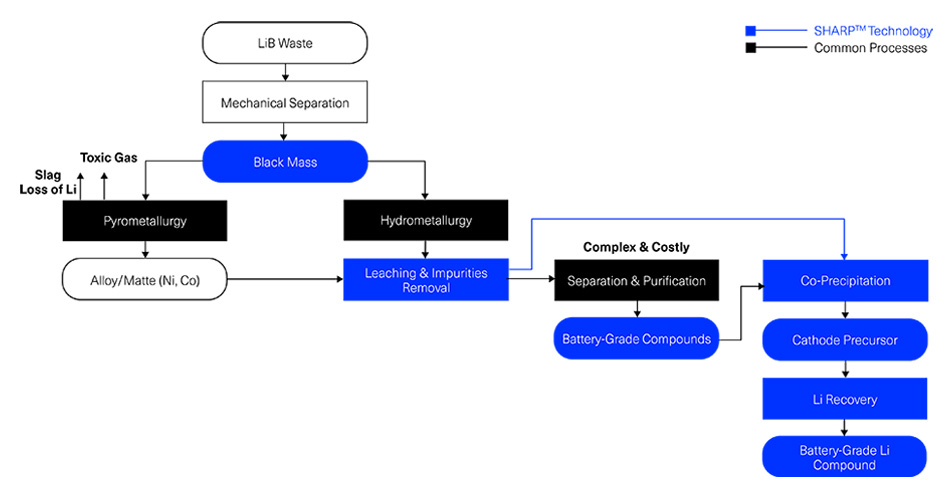
Abbildung 3. Vergleich der SHARP-Technologie von Coherent mit pyrometallurgischen und gängigen hydrometallurgischen Verfahren.
Ergebnisse der Pilotanlage von SHARP Technology
Die SHARP-Technologie von Coherent wurde erfolgreich hochskaliert (Abbildung 4). Die Ergebnisse der Pilotanlage bestätigten, dass die Produktion von Materialien in Batteriequalität zu wesentlich niedrigeren Kosten möglich ist. Dies ist ein überzeugendes Angebot sowohl für umweltbewusste Verbraucher als auch für den Markt als Ganzes. Um die Robustheit des Prozesses zu bestätigen, wurde die für die Pilotanlage ausgewählte schwarze Masse mit verschiedenen Verunreinigungen wie Aluminium, Eisen, Kupfer, Cadmium, Kalzium, Magnesium, Fluor und Zink kontaminiert. Einige dieser Verunreinigungen sind in NMC-LiB-Abfällen nicht zu erwarten und waren in dieser schwarzen Masse aufgrund einer Kreuzkontamination mit anderen Batterietypen vorhanden. Die effiziente Entfernung aller Verunreinigungen aus der schwarzen Masse und die Herstellung von Materialien in Batteriequalität bestätigten die Robustheit der SHARP-Technologie, selbst bei einem hohen Anteil an Verunreinigungen.
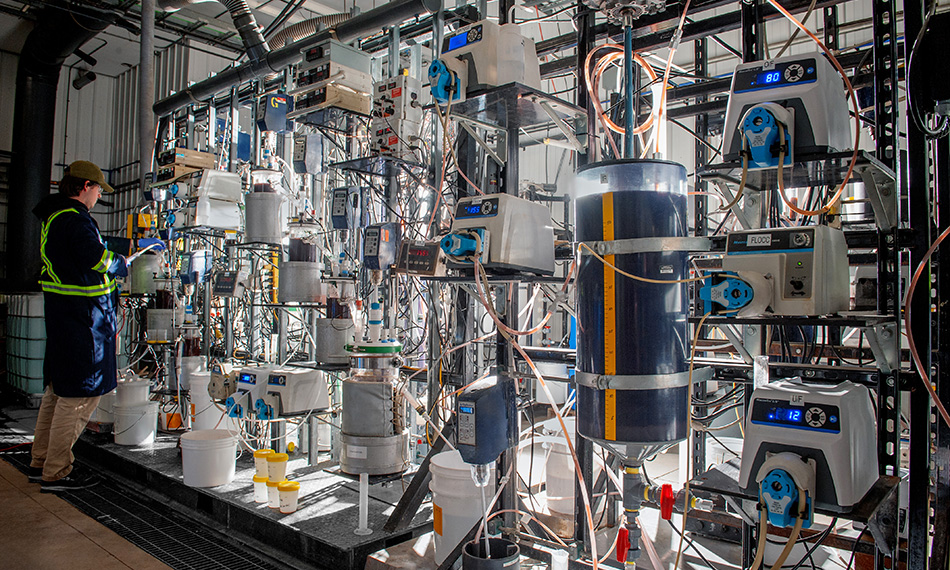
Abbildung 4: Eine Reihe von Reaktoren für den Schritt zur Entfernung von Verunreinigungen in der SHARP-Technologie.
Kommerzialisierungspfad der SHARP-Technologie
Nach dem erfolgreichen Betrieb der Pilotanlage treibt Coherent diese Technologie im Jahr 2024 voran, indem es in seiner bestehenden Anlage unter Nutzung ungenutzter Anlagen eine Demonstrationsanlage mit einer Kapazität von 1.500 Tonnen/Jahr (MT/Jahr) betreibt.
Coherent plant den Bau einer LiB-Recyclinganlage mit einer Kapazität von 20.000 Tonnen schwarzer Masse pro Jahr. Diese hochmoderne Anlage wird voraussichtlich eine wichtige Rolle bei der nachhaltigen Bewirtschaftung von LiBs spielen. Ziel des Projekts ist es, einen erheblichen Teil dieser Batterien zu recyceln und so zur ökologischen Nachhaltigkeit und Ressourcenschonung beizutragen. Durch die effektive Verarbeitung dieser Batterien wird Coherent schätzungsweise 11.000 Tonnen/Jahr recyceltes Produkt als pCAM und 5.500 Tonnen/Jahr LiOH.H2O, entsprechend 10 GWh, produzieren und so den Bedarf an Rohstoffen reduzieren und den Abfall minimieren. Diese Initiative steht im Einklang mit der breiteren weltweiten Forderung nach umweltfreundlichen Praktiken in der Batterieindustrie und trägt dazu bei, Bedenken hinsichtlich der Umweltauswirkungen der Batterieentsorgung und der Erschöpfung kritischer Materialien auszuräumen.
Der Vorteil von Coherent
- Hydrometallurgische Erfahrung:
Mit über 30 Jahren Erfahrung kann Coherent auf eine reiche Geschichte im erfolgreichen Betrieb von Raffinerieanlagen für seltene Metalle zurückblicken. Coherent zeichnet sich durch die Produktion von hochreinem Tellur und Selen aus und deckt damit einen großen Teil des weltweiten Bedarfs. - Robustheit der SHARP-Technologie:
Die Fähigkeiten von SHARP erstrecken sich auf den Umgang mit verschiedenen Verunreinigungen, einschließlich Aluminium, Eisen, Kupfer und Fluor, die häufig in NMC-LiBs vorkommen, unabhängig von ihrer Konzentration. - Geringes Risiko bei der Hochskalierung:
Die erforderliche Ausrüstung wird nachweislich erfolgreich in der Hydrometallurgie-Industrie eingesetzt und minimiert das Hochskalierungs-Risiko. - Vielseitigkeit und Flexibilität:
Die SHARP-Technologie ist nicht nur für die Verarbeitung von Ausschuss geeignet, sondern beweist auch ihre Vielseitigkeit, indem sie aus schwarzer EOL-Masse Produkte in Batteriequalität herstellt, die Verunreinigungen wie Cadmium, Kalzium, Magnesium, Zink, Wolfram und Zirkonium enthalten. Die aus EOL-Batterien gewonnene schwarze Masse, die einen hohen Anteil an Verunreinigungen enthält, wurde in unserer Pilotanlage effektiv verarbeitet, was den Erfolg unserer Technologie unterstreicht.
Unser Engagement für Spitzenleistungen, gepaart mit fortschrittlicher Technologie und Anpassungsfähigkeit, positioniert uns bei Coherent als führendes Unternehmen im LiB-Recycling und in der Herstellung von Batteriematerialien, an der Spitze der nachhaltigen Innovationen für die Zukunft