EINE NEUE GENERATION VON WELTRAUMTELESKOPEN ERMÖGLICHEN
Coherent hat Fertigungstechniken entwickelt, die den Einsatz von Metallen und Kompositwerkstoffen für Spiegel in weltraumgestützten Teleskopen erweitern.
8. Februar 2024 von Coherent
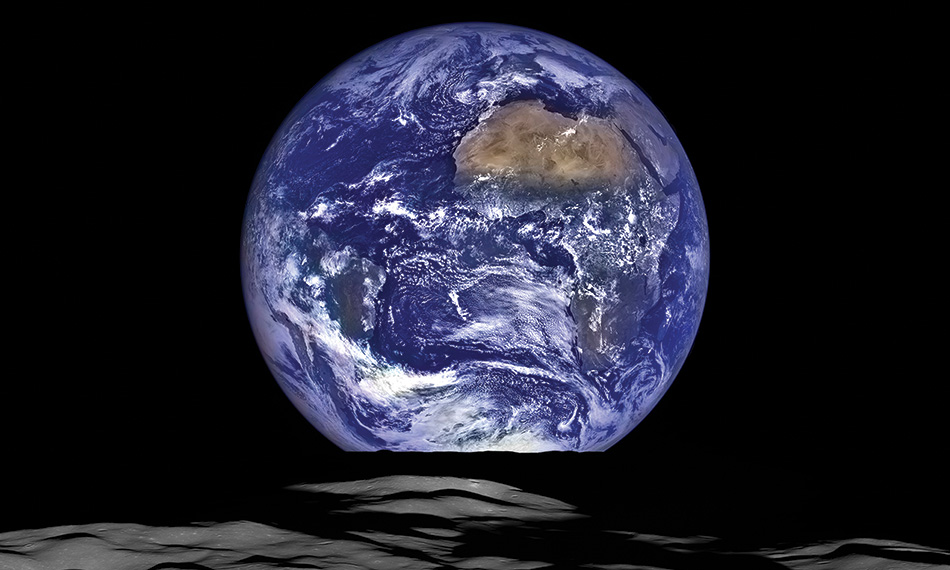
Die Konstrukteure moderner weltraumgestützter Teleskope nehmen sich ein Beispiel an den Pionieren der Astronomie und kehren zur Verwendung von Metallspiegeln zurück. Im Jahr 1668 verwendete Sir Isaac Newton "Spekulum-Metall", um den Spiegel für das allererste Spiegelteleskop herzustellen. Spekulum-Metall ist eine Kupfer-Zinn-Legierung, die bis Mitte des 18. Jahrhunderts das bevorzugte Material für Teleskopspiegel war. Der technologische Fortschritt führte dann zu einem Wechsel zu Glasspiegeln, die bessere Ergebnisse lieferten.
Zurück in die Zukunft mit Metallspiegeln
Warum also jetzt die Uhr zurückdrehen auf Metallspiegel? Erstens, weil wir keine Spiegel aus Spekulum-Metall verwenden, die schwer herzustellen waren und schnell anliefen. Die modernen weltraumgestützten Teleskopspiegel von heute werden aus modernen Aluminium- und Berylliumlegierungen sowie aus Kompositwerkstoffen wie Siliziumkarbid (SiC) hergestellt.
Ein Hauptvorteil der Verwendung dieser Materialien besteht darin, dass sowohl der Spiegel als auch seine Halterung (die mechanische Struktur, die den Spiegel hält) als eine einzige, monolithische Struktur hergestellt werden können. Bei Glas ist das nicht möglich. Der monolithische Aufbau kann die Anzahl der Teile und das Gesamtgewicht des Teleskops drastisch reduzieren, den Montageprozess vereinfachen und beschleunigen und damit die Kosten senken.
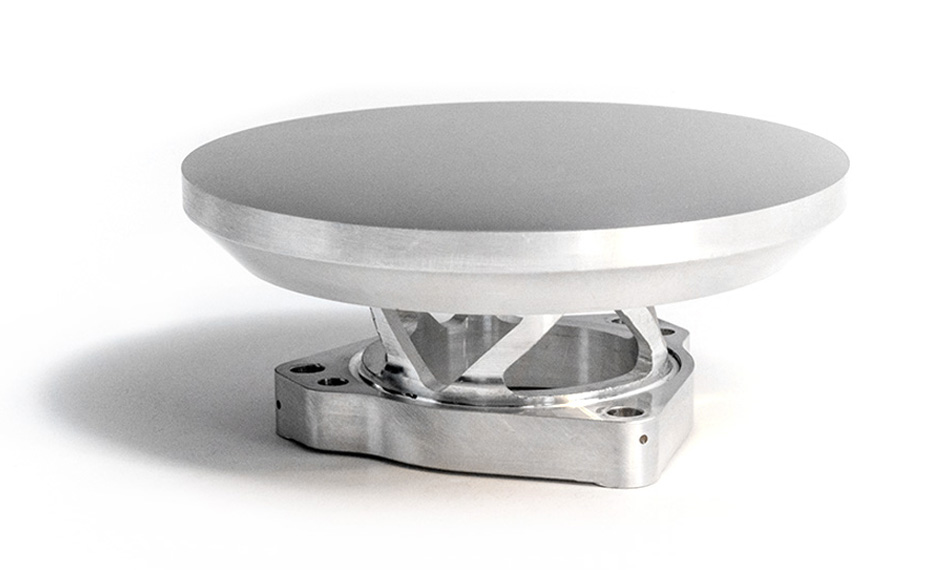
Ein monolithischer Metallspiegel integriert die optische Komponente mit den Befestigungsteilen.
Materialunterschiede
Metallspiegel haben zwar erhebliche praktische Vorteile, sind aber nicht für jede Anwendung das "beste" Material. Dies gilt insbesondere, wenn man die thermischen Eigenschaften des Teleskops berücksichtigt. Dies ist ein wichtiger Aspekt bei der Entwicklung von Systemen im Weltraum, da Raumfahrzeuge dort extremen Temperaturen und schnellen Temperaturschwankungen ausgesetzt sind. Um dies näher zu untersuchen, ist es sinnvoll, einige der wichtigsten Eigenschaften der Materialien zu betrachten, die am häufigsten für Hauptspiegel von Weltraumteleskopen verwendet werden.
Material |
Dichte (g/cm³) |
Steifigkeit (GPa) |
WAK (10⁶/°C) |
Wärme- leitfähigkeit (W/m·K) |
|
Glassorten |
Quarzglas |
2,2 |
73 |
0,55 |
1,4 |
ZERODUR® |
2,53 |
90 |
0,1 |
1,7 |
|
Kompositwerkstoffe |
SiC | 2,95 |
410 |
4 |
120 |
Metalle |
Beryllium |
1,85 |
287 |
11,4 |
190 |
Aluminium |
2,7 |
69 |
23,6 |
205 |
ZERODUR® ist ein eingetragenes Warenzeichen der Schott AG
Quarzglas und Zerodur sind nur zwei von mehreren Glassorten, die für Spiegelträger verwendet werden, aber sie repräsentieren diese Klasse von Materialien gut. Ihr charakteristisches Merkmal ist ein extrem niedriger Wärmeausdehnungskoeffizient (WAK). Das bedeutet einfach, dass sich diese Materialien bei Temperaturschwankungen nicht stark ausdehnen oder zusammenziehen.
Außerdem hat Glas eine geringe Wärmeleitfähigkeit. Daher dauert es sehr lange, bis es sich bei Änderungen der Umgebungstemperatur entweder aufheizt oder abkühlt. Dadurch bleiben sie bei Temperaturschwankungen stabil.
Im Gegensatz dazu ändert Aluminium je nach Temperatur schnell seine Form und leitet auch Wärme gut. Es hat den praktischen Vorteil, dass es preiswert und leicht verfügbar ist und aus ihm schnell fertig bearbeitete Teile hergestellt werden können.
Beryllium ist ein geradezu "magisches" Material. Es hat eine geringere Dichte als Glas, ist aber viel steifer. Deshalb lassen sich daraus dünne und leichte Bauteile herstellen, die dennoch mechanisch stabil sind. Außerdem ändert Beryllium bei Temperaturen unter -130 °C seine kristalline Form, und sein Wärmeausdehnungskoeffizient wird recht klein. Diese Kombination von Eigenschaften macht es zum leichtesten, strukturell stärksten und thermisch stabilsten Material auf dem Markt. Aus diesem Grund wird es für die anspruchsvollsten Anwendungen eingesetzt, wie z. B. für die Hauptspiegelsegmente des James-Webb-Weltraumteleskops.
Der Nachteil von Beryllium ist, dass es selten und extrem teuer ist. Außerdem ist es ziemlich giftig, so dass Personen bei der Verarbeitung extreme Vorsichtsmaßnahmen treffen müssen.
SiC hat eine höhere Dichte als jedes dieser anderen Materialien. Das bedeutet jedoch nicht, dass das Gewicht von SiC-Spiegeln nicht niedrig gehalten werden kann. Das liegt daran, dass SiC sehr steif ist. Infolgedessen können SiC-Spiegel und -Bauteile sehr viel dünner als bei anderen Materialien hergestellt werden, wobei sie dennoch sehr stabil und widerstandsfähig sind.
Diese Eigenschaften machen Glas zum bevorzugten Material, wenn das Teleskop voraussichtlich großen Temperaturschwankungen ausgesetzt ist. Dies geschieht, wenn sich ein Teil des Teleskops im Sonnenlicht befindet, das es aufheizt, während ein anderer Teil im Schatten ist. Der abgeschattete Teil kühlt ab, weil seine Wärme in den Weltraum abstrahlt. Der niedrige WAK und die geringe Wärmeleitfähigkeit von Glas bedeuten, dass sich der Spiegel bei einem Temperaturwechsel nicht so schnell verformt.
Wenn dagegen gleichmäßige Temperaturen in der gesamten Konstruktion zu erwarten sind, ist es vorteilhaft, sowohl den Spiegel als auch die Halterung aus einem Metall oder einem Kompositwerkstoff herzustellen. Durch die effiziente Wärmeableitung erreicht ein solches System schneller ein Gleichgewicht, wodurch die Auswirkungen vorübergehender Temperaturschwankungen verringert werden.
Außerdem gibt es, wenn sich die Temperatur ändert, durch die Verwendung desselben Materials für Spiegel und Halterung keine Unterschiede hinsichtlich der Reaktion dieser Teile (selbst wenn es sich um separate Teile handelt). Dies ist wichtig, weil durch die unterschiedliche Ausdehnung zwischen Spiegel und Halterung die Optik eines Teleskops unscharf werden kann. Außerdem kann die unterschiedliche Ausdehnung den Spiegel belasten und seine Oberflächenform verzerren, was die Bildqualität beeinträchtigt. Entwickler von Glasspiegelteleskopen entwerfen oft Konstruktionen, die diesen Effekt minimieren, was jedoch zusätzliche Kosten und manchmal auch mehr Gewicht bedeutet.
Glas hat einen klaren Vorteil
In Bezug auf die Herstellung von Optiken hat Glas seit langem einen weiteren wichtigen Vorteil gegenüber anderen Materialien. Es kann mit einem außerordentlich hohen Präzisionsgrad geformt und poliert werden. Und es ist schon seit über einem Jahrhundert möglich, Optiken mit dieser hohen Präzision herzustellen - lange bevor Computer und Laser verfügbar waren.
Um genau zu verstehen, was „Präzision“ bei Teleskopspiegeln bedeutet, muss man ein wenig darüber wissen, wie optische Oberflächen spezifiziert werden. Es gibt im Wesentlichen zwei getrennte Bereiche, die wichtig sind.
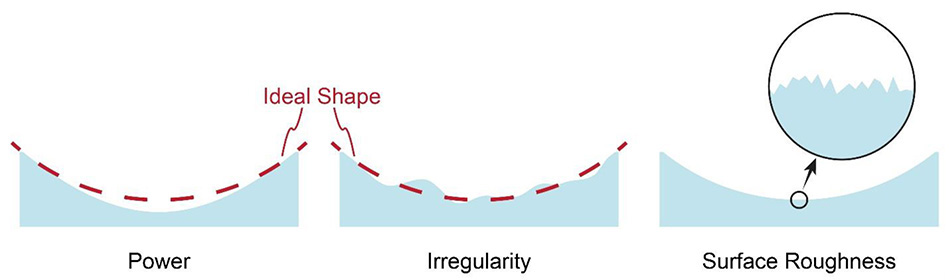
Eine Möglichkeit, die Form eines Teleskopspiegels zu quantifizieren, besteht darin, seine „Güte“ (der Betrag, um den seine Gesamtform von der gewünschten Kurve abweicht), seine „Unregelmäßigkeit“ (die kleineren Unebenheiten und Wellen auf der Oberfläche) und seine „Oberflächenrauhigkeit“ (die Höhenunterschiede auf mikroskopischer Ebene) zu messen. ).
Der erste ist die Gesamtform, die gewöhnlich als „Figur“ oder „Oberflächengenauigkeit“ bezeichnet wird. Konkret geht es darum, wie gut die Oberflächenform (Krümmung) der Spiegeloberfläche mit der vorgesehenen Form übereinstimmt.
Um eine optimale Bildqualität zu erzielen, sollte die Oberflächenform mit einer Genauigkeit von mindestens 150 nm mit dem Sollwert übereinstimmen (ein Nanometer ist ein Milliardstel eines Meters). Es ist durchaus nicht ungewöhnlich, dass die Oberflächengenauigkeit eines Teleskopspiegels bei 60 nm liegt.
Der zweite wichtige Bereich ist die Oberflächenrauheit auf mikroskopischer Ebene. Ein Teleskopspiegel muss außerordentlich glatt sein, um die Streuung des Lichts zu minimieren. Streulicht verringert die Bildhelligkeit und den Kontrast.
Um qualitativ hochwertige Bilder im sichtbaren Wellenlängenbereich zu erzeugen, sollte ein Teleskopspiegel eine maximale Oberflächenrauhigkeit von wenigen Zehntel Angström aufweisen. Ein Angström ist ein Zehnmilliardstel eines Meters. Dies ist etwa der Durchmesser eines Wasserstoffatoms.
In der Vergangenheit war es nicht möglich, Metallspiegel mit der bei Glasspiegeln erreichbaren Formgenauigkeit und Glätte (geringe Oberflächenrauhigkeit) zu polieren. Um die Rauheit der Metallspiegeloberfläche zu verringern, wurde eine dicke Metallschicht (einige zehn Mikrometer) auf den Spiegel aufgetragen, um ihn zu glätten.
Bei Aluminiumspiegeln ist es üblich, Nickel als Beschichtungsmaterial zu verwenden. Aber der WAK von Nickel ist anders als der von Aluminium. Eine unterschiedliche Ausdehnung oder Schrumpfung zwischen der Beschichtung und dem Spiegelträger kann dazu führen, dass sich der Spiegel verformt und die Abbildungsqualität sinkt. Dies war ein einschränkender Faktor für den Einsatz von Aluminiumspiegeln.
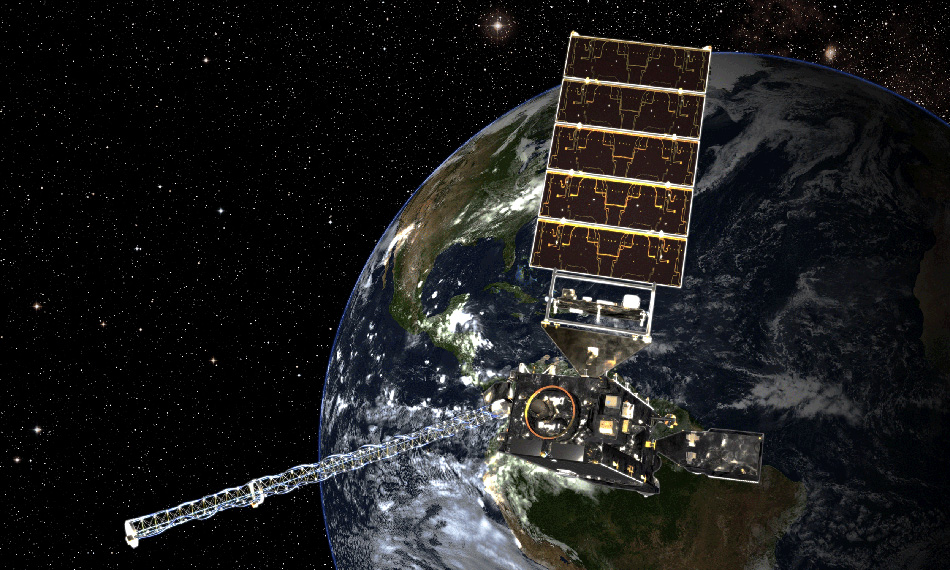
Verbesserung der Metallpoliertechnologie
Coherent arbeitet seit vielen Jahren an der Verbesserung der optischen Poliertechnologie. Wir haben unser eigenes, geschütztes Verfahren zur computergesteuerten optischen Oberflächenbearbeitung (CCOS) entwickelt und umfangreiche Investitionen in moderne Messgeräte getätigt.
Dadurch können wir Metallspiegel mit einer Formgenauigkeit polieren, die mit der von Glasoptiken konkurriert. Wir haben diesen Meilenstein schon vor einiger Zeit erreicht, aber unsere Fähigkeiten in diesem Bereich sind nach wie vor einzigartig in der Optikbranche.
In jüngster Zeit haben wir unser Verfahren weiter verfeinert, um die Oberflächenrauhigkeit bei Metallspiegeln drastisch zu verringern. Jetzt können wir eine Oberfläche herstellen, die so glatt ist, dass sie ohne Beschichtung als Spiegel verwendet werden kann. Meistens wird jedoch eine dünne Schicht (viel weniger als ein Mikrometer) aus Metall oder dielektrischem Material aufgetragen, um das Reflexionsvermögen zu erhöhen. Gold ist ein häufig verwendetes Beschichtungsmaterial. Vor allem aber sind diese Schichten dünn genug, um Probleme im Zusammenhang mit einem unterschiedlichen WAK zwischen der Beschichtung und dem Spiegelsubstrat zu vermeiden.
Die neue Generation von hochpräzisen Metall- und Kompositwerkstoffspiegeln, die mit unserer Technologie möglich ist, macht diese Materialien besser praktisch einsetzbar und erweitert das Instrumentarium der Teleskopkonstrukteure. Insbesondere Aluminium wird zu einer attraktiven Option. Es kann die Kosten und das Startgewicht der Optik reduzieren, ohne die Bildqualität zu beeinträchtigen. Außerdem können Aluminiumspiegel in der Regel viel schneller hergestellt werden als andere Materialien, was die Einhaltung von Produktionsplänen erleichtert.
Erfahren Sie mehr über kundenspezifische Teleskopoptiken von Coherent für Weltraum- und terrestrische Anwendungen.