Lasers in Display Fabrication: Cell and Polarizer Cutting
Only CO2 lasers can cut display “cells” and polarizers with the speed and edge quality needed for cost-effective, high-volume production.
October 4, 2022 by Coherent
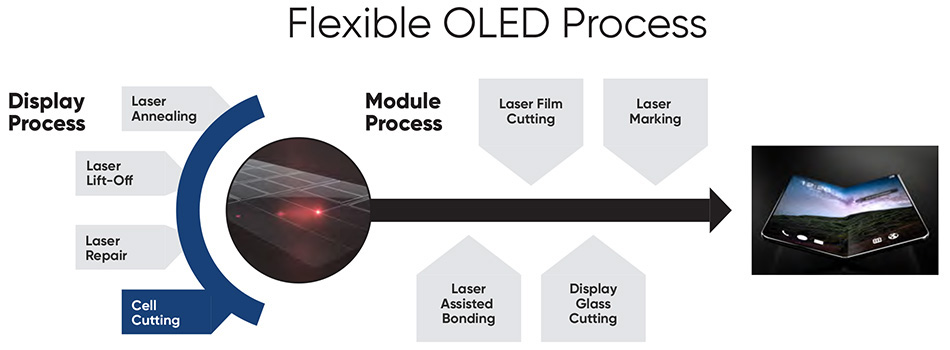
The world’s biggest display manufacturers make over one million displays every single day. Doing this requires extremely high-speed production processes.
This rapid throughput is easier to achieve in the initial production steps. That’s because the first part of the FPD production cycle is performed on mother glass panels containing well over a hundred displays. This allows steps like ELA and LLO to process all the displays on the mother glass simultaneously in a single operation.
But things change when that large panel is separated into “cells.” This means cutting it up into individual displays, or sometimes groups of just a few. By its very nature, this cell cutting operation can’t be done simultaneously over the entire panel. It’s a serial operation.
Of course, manufacturers don’t want cell cutting to be a production bottleneck. This process must still keep pace with the rest of the production flow.
Read the other blogs in this series on lasers in display fabrication |
|||
The kindest cut
Theoretically, at least, cutting through the thin, flexible OLED displays could be easily accomplished using a variety of different methods. However, this particular application presents a few unique problems.
First, each display is only separated from its neighbor on the panel by a few millimeters. Second, the display is a stack of heterogeneous materials, each of which may have different cutting characteristics. And, finally, the displays are relatively delicate electronic devices. They can be damaged by heat or anything else that causes the various layers to physically separate at all.
CO2 lasers offer the best way to optimize the cut, within all these constraints. These lasers produce high-power infrared light which is well absorbed by all the various materials in the OLED stack, meaning that every layer is efficiently cut. Plus, they cut without producing any debris which might affect display appearance or functionality or require extra production steps to remove.
For cell and polarizer cutting, the focused CO2 beam is usually delivered using a high-speed, precision scanning system. This provides the required throughput rate and yields straight cuts with narrow kerf width.
Cell cutting is a multi-layer problem
But the high laser power which enables rapid cutting can also be too much of a good thing. This is because the infrared light from the CO2 laser cuts by a thermal mechanism. That is, it heats the material up until it vaporizes. Putting too much heat into the part during cutting can create a large heat-affected zone which damages the display circuity.
Also, both the bottom and top layers of a flexible OLED display are polymers. When this plastic is heated during cutting, some of the material melts but doesn’t boil away. Then, it tends to flow and resolidify in a “bead.” That is a slightly thicker lip on the edge.
This lip creates an issue in subsequent production steps, in particular when a contrast enhancement polarizer is added on top of the OLED display. This polarizer is also CO2 laser cut and could experience the same problem with edge thickening.
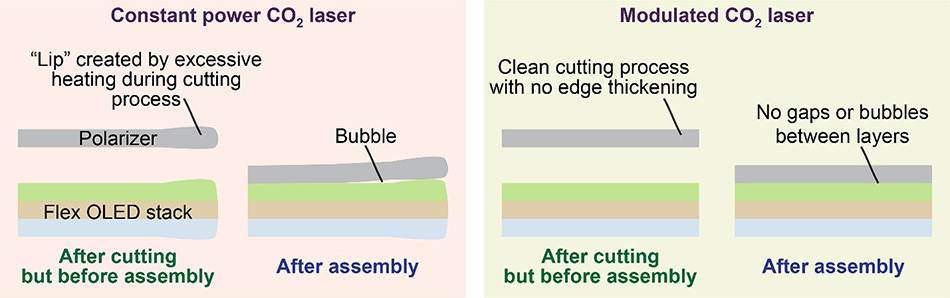
Schematic drawing illustrating the problem of display cell cutting using a CW CO2 laser.
When these two parts are laminated together, the edge lip can create bubbles or gaps between the layers. This is highly undesirable.
Modulated CO2 lasers are a cut above
The way to avoid creating a lip at the cut edge is to modulate the CO2 laser. That means rapidly turning the beam on and off. This still supplies enough heat to vaporize the material. But it doesn’t keep the laser on long enough for that heat to propagate very far into the substrate where it will melt material, rather than completely remove it.
There are two different ways to modulate a CO2 laser. The first is to take a laser that produces continuous output and then chop that up into pulses with an external acousto-optic modulator. That’s what’s done in the Coherent DIAMOND Cx10LDE+, which is currently the most popular laser for cell and polarizer cutting in the FPD industry.
One reason the CX10-LDE+ is so widely used is that the modulator is directly built into it. This approach allows us to fully integrate the laser and modulator control electronics and therefore optimize total system performance. This is critical to reaching the precision in pulse control and power stability needed to achieve the process consistency and repeatability required by FPD manufacturers.
The second way to modulate a CO2 laser is q-switching. Here a modulator is placed inside the laser resonator itself so that the laser operates in a pulsed (rather than continuous) mode. This makes a big difference in how the laser operates. Thus, while an external modulator provides microsecond range pulse widths, q-switching produces much shorter, nanosecond regime pulse widths and also increases the peak pulse power dramatically.
These shorter pulses reduce the heat-affected zone even more, and also allow greater precision and control over the cutting process. As a result, many FPD manufacturers are transitioning to this technology. The Coherent DIAMOND Cx-10LQS+ is the only q-switched CO2 laser commercially available.
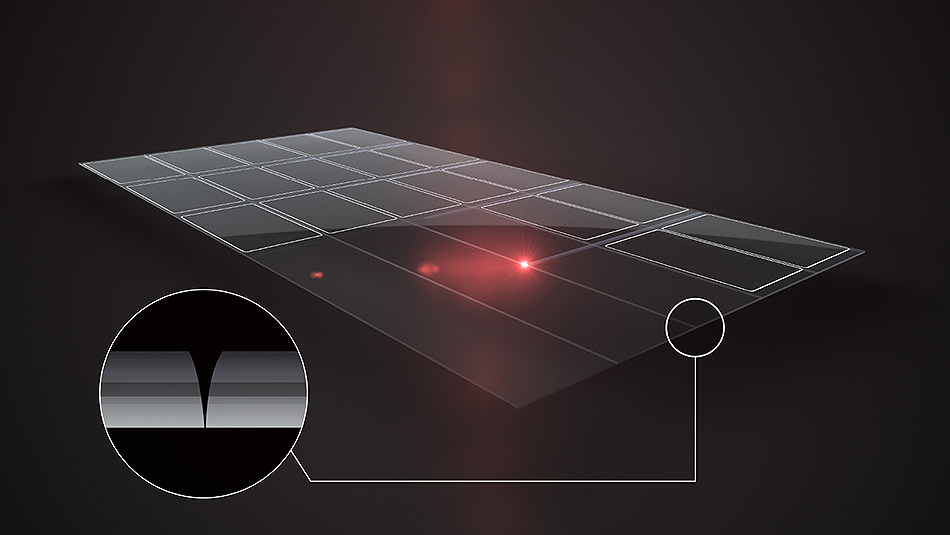
Reliability saves money
Another reason why Coherent lasers are so widely used in cell and polarizer cutting is their lifetime and reliability, plus our global service infrastructure. Once again, FPD makers are producing very large volumes of products continuously. Production downtime to service or replace a laser has a huge productivity and cost impact. The unmatched lifetime of these lasers – typically in the 10,000-to-20,000-hour range – ensures an uninterrupted flow of high-quality FPDs. And, when laser replacement is finally called for, Coherent’s worldwide inventory and quick-response service team ensure it’s swapped out without delay.
Learn more about our laser solutions for display manufacturing.