디스플레이 제작에서의 레이저: FlexOLED 형상 및 구멍 절단
고출력의 자외선 초단파 펄스 레이저만이 민감한 회로를 손상시키지 않으면서 거의 완성된 디스플레이를 절단하는 데 필요한 속도와 정밀도를 제공할 수 있습니다.
2022년 10월 4일, Coherent
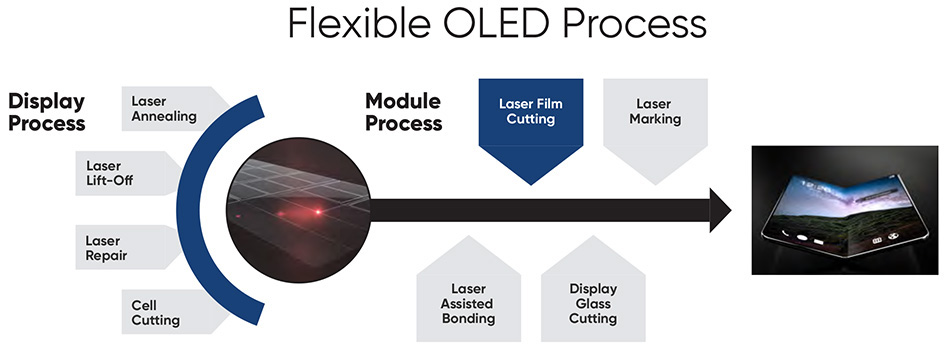
이 시리즈의 다른 게시물에서는 대형 “마더 글라스” 패널에서 수많은 모바일 기기 디스플레이를 모두 한 번에 제작하는 방법을 설명했습니다. 모든 회로가 만들어지고 기타 다양한 층이 회로에 추가된 후 CO2 레이저를 이용해 대형 기판을 “셀”로 절단합니다.
디스플레이를 몇 개만 포함하는 셀이 원래의 대형 기판보다 취급 및 운송이 훨씬 쉽기 때문에 이러한 작업이 수행됩니다. 모바일 기기 조립의 최종 단계는 일반적으로 디스플레이 회로가 원래 제작된 곳에서 떨어져 있는 별도의 생산 시설(대개 다른 국가에 소재!)에서 이루어집니다. 개별 디스플레이의 크기 및 기타 요소에 따라 셀은 보통 2~10개의 개별 디스플레이를 포함하고 있습니다.
디스플레이 제작용 레이저에 대한 이 시리즈의 다른 블로그 읽기 |
|||
수행하기 어려운 공정
휴대전화 또는 태블릿을 조립하기 전에 각 개별 디스플레이를 셀에서 잘라내야 합니다. 또한 디스플레이 내 어딘가에 구멍이 있어야 하는 디자인이 대부분입니다. 이러한 구멍은 일반적으로 카메라 또는 기타 센서가 볼 수 있도록 하기 위한 것입니다. 그리고 디스플레이 층 중 일부만 특정 영역에서 선별적으로 제거되는 경우도 있습니다. 이는 디스플레이 바로 밑에 위치하지만 관통 구멍이 필요하지 않은 지문 센서를 감안한 것입니다.
이러한 공정을 형상 및 구멍 절단이라고 합니다. 한편, 몇 가지 이유로 극도로 까다로운 작업입니다. 먼저, 거의 모든 비용이 들어간 사실상 완성된 디스플레이에서 수행됩니다. 그렇기 때문에 이 단계에서 부품을 폐기하는 일이 발생해서는 안 됩니다!
또한 높은 기계적 정밀도로 수행되어야 합니다. 즉, 매우 엄격한 공차 및 높은 반복성이 요구됩니다. 이는 조립 중 문제를 방지하기 위해 필수적입니다. 현재 대부분의 휴대전화는 기기의 상단 표면 전체를 거의 덮는 디스플레이를 갖추고 있으며 기기 둘레부는 매우 얇은 베젤로 이루어져 있습니다. 디스플레이가 너무 크게 절단되면 베젤에 맞지 않게 됩니다. 너무 작게 절단되면 가장자리 주위에 틈이 보이게 됩니다. 또한 모든 구멍은 후면에 있는 부품(예: 카메라)과 정확히 맞춰져야 합니다.
이러한 절단 공정의 또 다른 매우 중요한 측면은 발생되는 “열 영향부(HAZ)”입니다. HAZ는 가장자리 옆 영역으로 절단 공정에서의 열이 디스플레이 회로에 영향을 미치거나 기포, 균열 또는 기타 결함이 생길 수도 있는 부분입니다. 이러한 디스플레이의 불량 영역은 사용자의 눈에도 쉽게 띌 수 있습니다. 혹은, 폴더블 휴대전화의 경우 결국에는 균열이 형성되거나 퍼질 수 있는 원인이 될 수 있습니다.
일반적인 휴대전화 형상 절단을 위한 최대 HAZ 사양은 100µm일 수 있습니다. 폴더블 디스플레이의 경우는 50μm일 수 있습니다. 또한 구멍 절단의 경우 최대 허용 가능한 HAZ는 20µm 미만인 경우가 많습니다.
물론, 형상 절단 공정은 빠르게 수행되어야 합니다. 실제로 최대 몇 초 내에 완료해야 합니다. 그 이유는 절단 작업의 경우 다른 생산 단계와 보조를 맞춰야 하고 모바일 기기 제조업체가 직면하고 있는 엄청난 처리량 요구를 충족해야 하기 때문입니다.
초단파 펄스 레이저를 통해 FlexOLED의 성공적 수행
디스플레이를 절단하고 이러한 요구 사항을 모두 충족할 수 있는 레이저는 한 종류밖에 없습니다. 즉, 높은 반복률로 작동하고 자외선으로 출력하는 초단파 펄스(USP) 레이저 입니다. 이러한 각 특성이 왜 그렇게 중요한지 살펴보겠습니다.
USP 레이저는 기타 모든 레이저 유형보다 훨씬 더 작은 HAZ를 형성하며 최소한 몇 초 내에 0.5mm 두께의 디스플레이를 잘라낼 수 있습니다. 일반적으로 펄스가 짧아질수록 HAZ가 작아집니다. 따라서 펨토초 USP 레이저는 10µm 미만의 HAZ를 형성할 수 있는 반면 피코초 USP 레이저는 일반적으로 30µm 미만의 HAZ를 형성할 수 있습니다.
하지만 이와 같이 명확하지는 않습니다. 실제 HAZ 차이는 이론에서 나타내는 것처럼 항상 뚜렷한 것은 아닙니다. 그리고 특정 응용 분야에 “가장 적합한” 레이저 유형에 영향을 미칠 수 있는 기타 실제적인 고려 사항, 속도 및 비용 측면에서 차이가 있습니다.
그 결과, 피코초 레이저와 펨토초 레이저 모두가 생산 시 형상 및 구멍 절단에 현재 사용되고 있습니다. 여러 휴대전화 제조업체는 “자체적으로 뛰어난” 기술을 보유하고 있는 경향이 있습니다. 이러한 기술은 HAZ 요구 사항뿐만 아니라 특정 유형의 레이저와 관련한 경험 및 편의성 수준을 바탕으로 합니다.
형상 및 구멍 절단은 모두 스캐너를 사용하여 수행됩니다. 그리고 레이저는 디스플레이를 완전히 절단하기 위해 동일한 경로를 수차례 그대로 베껴야 합니다. 따라서 반복률이 중요한 요소로 작용합니다. 반복률은 절단 속도로 바로 이어집니다. 즉, 두 레이저가 동일한 펄스 에너지를 가지고 있는 경우 더 높은 반복으로 작동하는 레이저가 더 빠르게 절단을 수행합니다.
마지막으로 UV 출력은 몇 가지 이유로 유용합니다. 첫째, 디스플레이를 만드는 이질적인 스택에 있는 모든 다양한 물질에 의해 긴 파장보다 더 균일하게 흡수됩니다. 즉, 구성에 관계없이 각 층이 일관되게 절단됩니다.
자외선은 회절 덕분에 긴 파장보다 작은 스폿 크기에 집중될 수도 있습니다. 따라서 집중된 스폿의 에너지 밀도가 증가하며, 이는 각 펄스가 더 많은 물질을 제거한다는 것을 의미합니다. 이에 따라 절단 속도가 빨라집니다. 또한 자외선을 사용하면 광학 장치가 더 큰 초점 심도로 작동할 수 있습니다. 그러면 절단 공정 시 부품 높이 또는 두께가 약간 변경되어도 그에 맞게 조정하는 것이 더 수월해집니다.
Coherent는 FlexOLED 형상 및 구멍 절단을 위한 두 가지 기술을 모두 제공함으로써 어떠한 편견도 없이 제조업체가 생산에 적합한 옵션을 선택하도록 지원할 수 있습니다. Coherent의 Monaco 펨토초 및 HyperRapid NXT 피코초 레이저에 대해 자세히 알아보십시오.